6 Misconceptions in Selecting Lubricating Oil for Equipment
Selecting the right lubricating oil for machinery is crucial to maintaining equipment efficiency, longevity, and safety. Yet, many common misconceptions persist, causing people to make choices that reduce performance, increase wear, and even lead to serious malfunctions. This article addresses six common misconceptions about lubricating oil selection and offers guidance to avoid these pitfalls and achieve optimal results.
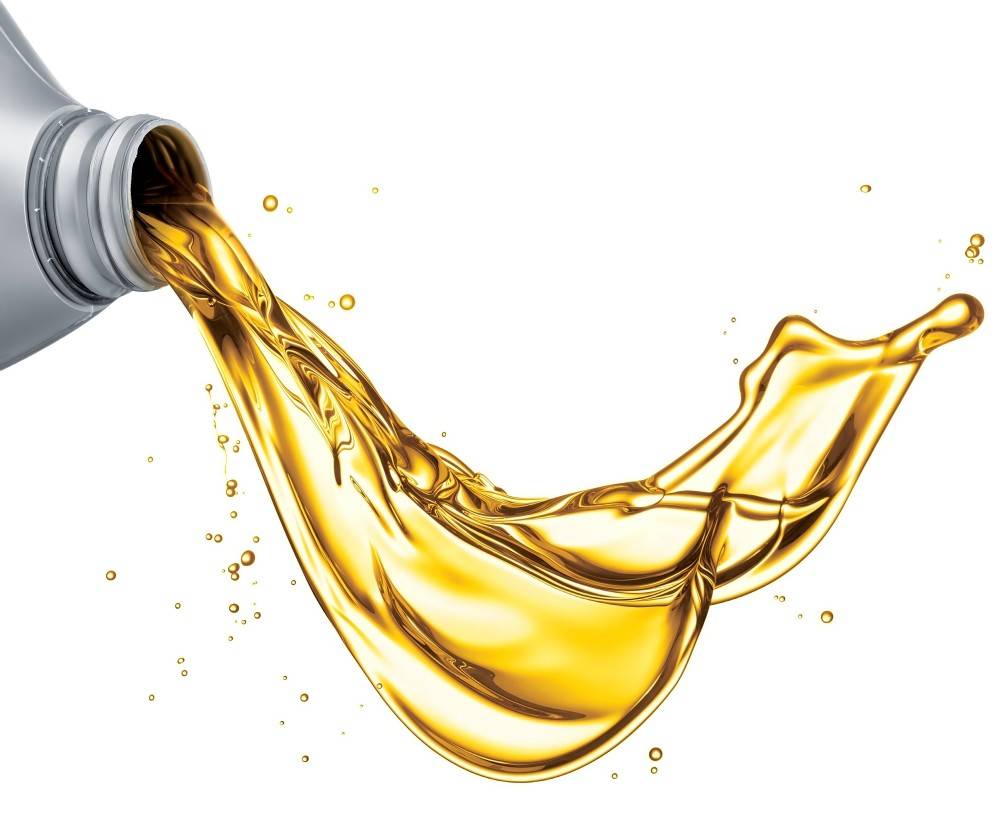
Misconception 1: “The More Engine Oil, the Better”
One prevalent myth is that adding more engine oil than recommended will ensure the engine doesn’t run low, and as a result, enhance protection. The logic here might seem sound at first—after all, oil is necessary for lubrication, so more should theoretically provide more protection. However, this is not the case.
Engine oil levels should be kept within a specific range, usually between the upper and lower marks on the dipstick. Adding too much oil can lead to various issues:
- Increased Resistance: With excess oil in the crankcase, the crankshaft has to work against greater resistance. This extra load results in higher power consumption, reducing the overall efficiency of the engine.
- Foaming and Leaks: Overfilled oil can create excessive pressure within the engine. As a result, the oil is more likely to bubble and form foam, which degrades lubrication quality. The foamy oil also loses its ability to form a stable film on engine components, leaving parts inadequately protected.
- Oil Spillage: Overfilled oil can cause leaks, potentially resulting in oil splashing into areas where it can harm other engine components.
Remember: Always check and add oil as needed but keep the level within the manufacturer’s recommended range. More oil does not mean more protection—sometimes, it’s just more trouble.
Misconception 2: “High-Viscosity Oil is Always Better for Engines”
Many assume that high-viscosity oil (thicker oil) provides better protection for engine parts. They believe that a thicker oil film will reduce wear and protect against heat and friction. While higher viscosity oils can indeed offer stronger lubrication under certain conditions, selecting an excessively high viscosity level has serious downsides.
Using an oil with a viscosity that’s too high for your engine can actually impair performance. Here’s how:
- Reduced Oil Flow: A high-viscosity oil is more resistant to flow, which means the oil pump has to work harder to circulate it throughout the engine. This can lead to reduced oil flow, starving critical parts of lubrication.
- Poor Lubrication and Cooling: Reduced flow means that parts don’t receive enough oil, leading to increased friction. High-viscosity oil also has a limited ability to dissipate heat effectively, meaning that the engine runs hotter, which can cause further degradation and wear.
- Risk of Dry Friction: Excessive thickness can lead to “semi-dry friction,” where oil does not fully separate the engine components. This can result in bearing wear, overheating, and even component failure.
Remember: Follow your engine’s recommended viscosity grade. Higher viscosity may be suitable in specific conditions, but going beyond recommended levels can cause more harm than good.
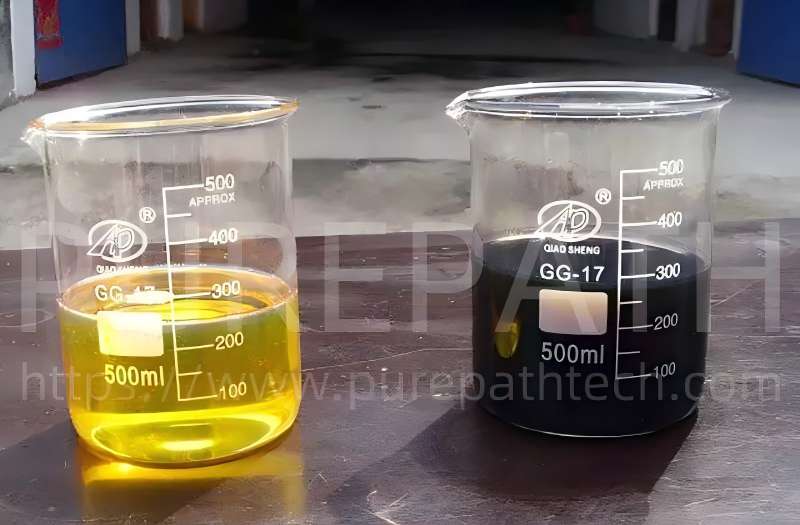
Misconception 3: “High-Viscosity Oil Can Solve Engine Power and Oil Leakage Problems”
Some people attempt to address engine performance problems like low power output or excessive oil leakage by switching to a higher-viscosity oil. They assume that thicker oil will prevent leaks and help the engine run more effectively. This is a risky assumption, as high-viscosity oil is rarely a solution for mechanical issues.
The belief that thicker oil will “fix” engine problems is a misconception:
- Increased Starting Resistance: Higher viscosity oil increases the force required to start the engine. This added resistance can make it harder for the engine to achieve the necessary power and can cause poor cold-start performance.
- Worsening Lubrication: If an engine already has wear-related issues, thicker oil won’t prevent further wear. Instead, it can worsen the situation by reducing lubrication, especially during startup.
- Leakage and Seal Problems: Higher-viscosity oil will not permanently solve leakage issues caused by worn or damaged seals. In some cases, using thick oil may worsen seal performance, as high viscosity can impede oil flow around critical seals.
Remember: Thicker oil is not a “quick fix” for mechanical problems. If your engine shows signs of wear or performance issues, it’s essential to inspect and repair the underlying problems instead of masking them with high-viscosity oil.
Misconception 4: “Always Use the Recommended Oil Grade without Adjustments”
It’s common practice to strictly adhere to the oil grade recommended in the machine’s manual. While these recommendations are generally reliable, they are often based on standard operating conditions and may not account for variations in actual usage or environmental conditions.
While it’s essential to follow manufacturer guidelines, some flexibility may be necessary in the face of demanding operating conditions:
- Adjusting for Harsh Environments: If the machine operates in extreme conditions (such as very high or low temperatures, heavy loads, or dust-prone environments), it might require an upgraded oil grade to cope with the added stress.
- Modifying the Oil Change Interval: Under particularly challenging conditions, shortening the oil change interval can help maintain proper lubrication. The extra cost of changing oil more frequently is often offset by longer equipment life and reduced breakdowns.
Remember: Assess your machine’s actual operating conditions, and don’t be afraid to adapt oil grades or intervals as needed. Manufacturer recommendations are a baseline; real-world conditions may necessitate adjustments for optimal performance.
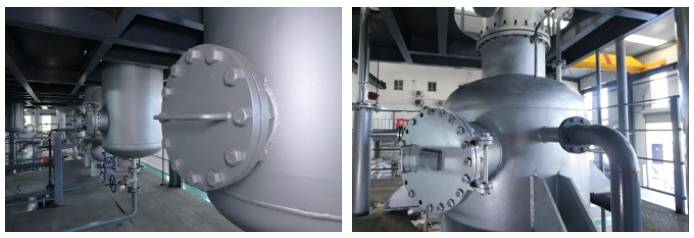
Misconception 5: “Black Oil Means Oil Degradation”
A common belief is that if oil turns black, it’s a sign that it has degraded and needs replacing. While darkened oil can sometimes indicate problems, modern lubricants contain additives that often cause them to darken during regular use without affecting their effectiveness.
The color of the oil is not a definitive indicator of its condition:
- Additive Effects: Modern lubricants include additives such as detergents and dispersants that help keep the engine clean by suspending impurities in the oil. These additives can cause the oil to darken as they trap and disperse contaminants.
- Not Always a Sign of Degradation: A dark color doesn’t necessarily mean the oil has lost its effectiveness. Instead of relying solely on appearance, consider conducting an oil analysis to determine the oil’s actual condition.
Remember: Don’t judge oil quality by color alone. If in doubt, have the oil tested, especially if your machinery requires high-performance lubrication.
Misconception 6: “Full-Hub Lubrication is Better than Empty-Hub Lubrication”
In some machinery, hub bearings are often packed completely with grease, a practice known as “full-hub lubrication.” The assumption here is that more grease equals better protection. In reality, a thin application in the hub cavity, known as “empty-hub lubrication,” is often more effective and safer.
Full-hub lubrication can cause several problems:
- Excessive Grease Increases Friction: When too much grease fills the hub cavity, it creates excessive internal friction, raising the operating temperature of the bearing. This excess heat can break down the grease and cause it to leak out.
- Potential for Brake Failure: Excess grease may leak into brake components, leading to reduced braking efficiency or even brake failure. This is especially dangerous in applications where reliable braking is critical.
Remember: Apply a moderate amount of grease to cover the bearings and a thin layer in the hub cavity to prevent rust. Full-hub lubrication is often unnecessary and may cause serious problems.
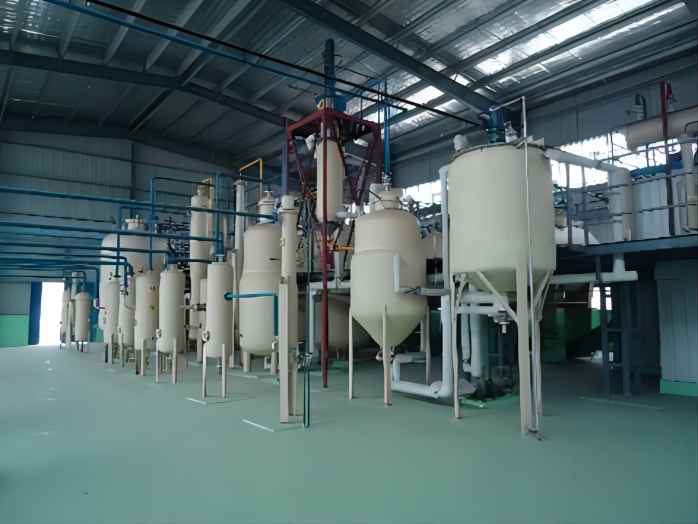
Final Thoughts
Proper lubricating oil selection is key to maintaining your equipment’s performance and longevity. Misconceptions about oil type, amount, viscosity, and usage can lead to costly repairs, safety hazards, and reduced efficiency. By understanding and avoiding these misconceptions, you can better protect your machinery and ensure it runs smoothly.
Remember, more isn’t always better, higher viscosity isn’t necessarily safer, and following manufacturer recommendations should be balanced with real-world conditions. For best results, stay informed, be flexible with oil choices, and rely on regular maintenance and analysis rather than assumptions about oil performance.