Base Oil Solvent Extraction Plants: Working Principle and Common Issues
Base oil is essential for creating lubricants and other specialized oil products. Achieving high-quality base oil involves removing impurities such as aromatics, sulfur compounds, and other undesired molecules that can affect performance and stability. Solvent extraction is a preferred technique due to its efficiency in selectively removing impurities while preserving the quality of the oil. The process is widely used in the petrochemical industry and has proven effective in producing pure base oils. This article delves into the working principles of base oil solvent extraction plants, common issues encountered during operation, and tips for maintenance and optimization.
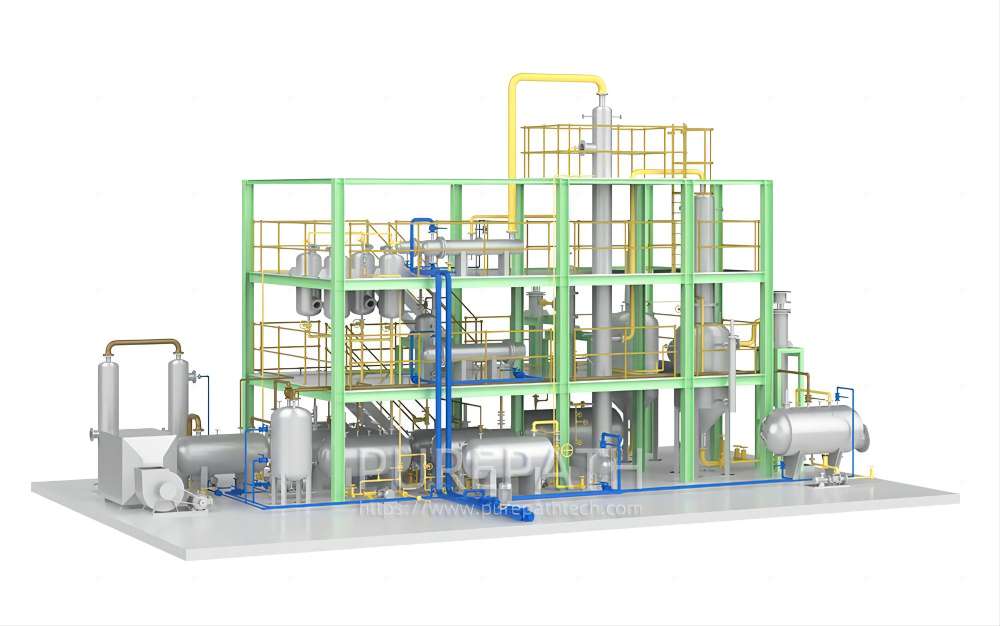
Working Principle of a Base Oil Solvent Extraction Plant
A base oil solvent extraction plant is a sophisticated system designed to refine crude base oil by removing impurities and enhancing its quality. This process involves several key steps:
1. Solvent Selection and Solubility:
- Solvent Choice: The first step is selecting a suitable solvent, such as methanol, ethanol, or other alcohol-based solutions. These solvents are chosen based on their ability to selectively dissolve impurities like aromatics and other undesirable compounds while leaving the desired base oil components intact.
- Solubility Differences: The effectiveness of the solvent relies on its solubility properties. The solvent must readily dissolve impurities but have minimal interaction with the base oil components. This difference in solubility is crucial for achieving efficient separation.
2. Heating and Mixing:
- Temperature Control: The base oil and solvent are heated to a specific temperature to increase the solubility of impurities in the solvent. Precise temperature control is essential, as excessive heat can degrade the base oil, while insufficient heat can hinder the extraction process.
- Thorough Mixing: The mixture is thoroughly mixed to ensure maximum contact between the solvent and the base oil. This mixing promotes the transfer of impurities from the base oil to the solvent.
3. Extraction and Separation:
- Extraction Tower: The mixture is introduced into an extraction tower or column, which is filled with trays or packing materials. These structures provide a large surface area for the solvent and base oil to interact, facilitating efficient separation.
- Phase Separation: As the mixture flows through the tower, the solvent dissolves impurities, forming a separate phase. The purified base oil, free from contaminants, remains in a different phase.
- Solvent-Rich Layer Removal: The solvent-rich layer containing the dissolved impurities is carefully removed from the tower, leaving behind the refined base oil.
4. Solvent Recovery:
- Evaporation and Condensation: To conserve solvent and minimize environmental impact, the solvent-rich layer undergoes a recovery process. This involves evaporating the solvent from the impurities, followed by condensation to recover the solvent in its pure form.
- Solvent Reuse: The recovered solvent is recycled back into the extraction process, making it a sustainable and cost-effective operation.
5. Desolvation of Base Oil:
- Solvent Removal: Any residual solvent remaining in the purified base oil is removed through a desolvation process. This is typically achieved through distillation or degassing techniques.
- Quality Assurance: Desolvation is crucial to ensure that the final base oil product meets stringent quality standards and is free from contaminants that could affect its performance.
6. Final Collection and Storage:
- Product Collection: The purified base oil, now free from impurities and solvent residues, is collected and prepared for storage, packaging, or further processing.
- Continuous Operation: While the purified base oil is collected, the solvent recovery system continues to operate, ensuring a continuous supply of solvent for the extraction process.
By following these steps, a base oil solvent extraction plant effectively refines crude base oil, producing a high-quality product suitable for various applications, such as lubricants and other refined oil products.
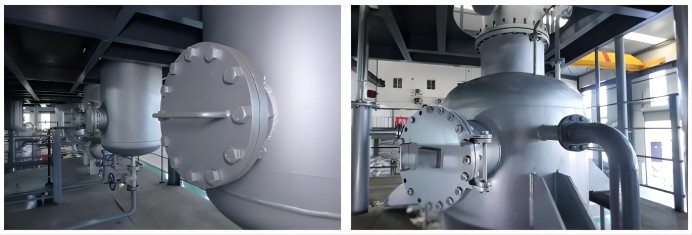
Common Issues and Troubleshooting in Solvent Extraction Plants
Operating a base oil solvent extraction plant can present a range of technical issues that may impact efficiency, safety, and product quality. Below are some common problems encountered and methods for addressing them.
1. Solvent Leakage
Solvent leakage can occur due to worn seals, aging components, or improper assembly. Leakage not only impacts efficiency but also poses safety and environmental risks. Regular inspection of seals and joints, along with timely replacement of worn parts, can prevent leaks. Ensuring equipment integrity through preventive maintenance can significantly reduce leakage risks.
2. Low Extraction Efficiency
Low efficiency often results from factors such as suboptimal solvent selection, incorrect solvent-to-oil ratios, or poor temperature control. Using an inadequate solvent can reduce the process’s ability to dissolve impurities effectively. Fine-tuning the solvent choice and concentration ratio, as well as closely monitoring temperatures, can improve extraction efficiency.
3. Equipment Blockage
Blockages within the plant’s systems, commonly caused by wax precipitation or solid impurities, disrupt flow and reduce efficiency. These blockages typically occur in cooler sections where waxy components crystallize. To prevent clogs, implementing regular cleaning schedules and using filtration systems to remove particulates can maintain smooth operation and extend the plant’s operational life.
4. Temperature and Pressure Fluctuations
Instability in temperature and pressure can lead to inconsistent solvent performance, reducing extraction quality. Temperature and pressure fluctuations may stem from malfunctioning sensors, faulty heating/cooling systems, or control system issues. Regular calibration of sensors and maintenance of heating and cooling units ensure stable operating conditions, enhancing solvent extraction efficiency.
5. Excessive Solvent Loss
High solvent consumption, often due to an inefficient recovery system, drives up costs and reduces overall process sustainability. Routine inspections and maintenance of the solvent recovery system, including condensers and evaporators, can minimize solvent loss. Improving recovery efficiency helps in managing costs and reducing environmental impact.
6. Mechanical and Control System Failures
Equipment failures, such as malfunctioning pumps, mixers, or control systems (e.g., PLC issues), can cause downtime and impact plant productivity. Regular preventive maintenance for mechanical components, coupled with troubleshooting of control systems, ensures continuous operation and minimizes unexpected shutdowns.
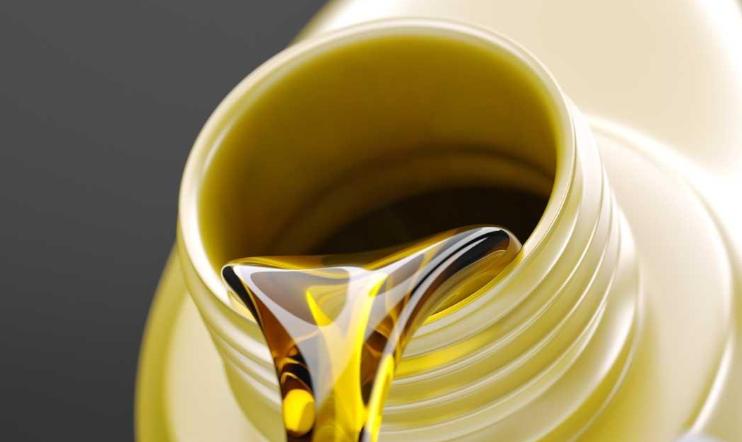
Maintenance and Optimization for Efficiency
Efficient operation of a solvent extraction plant relies on regular maintenance and optimization measures to minimize downtime and maximize output quality. Here are some best practices:
- Routine Inspections: Conduct regular checks on seals, pumps, and filters to ensure they are in good condition.
- Temperature and Pressure Monitoring: Maintain accurate and stable temperature and pressure settings to optimize solvent performance and prevent efficiency drops.
- Filter and Separator Cleaning: Regular cleaning of filters and separators to remove accumulated impurities and prevent blockages.
- Control System Upgrades: Upgrade control systems periodically to ensure reliability and improve monitoring accuracy.
- Solvent Recovery Optimization: Enhance solvent recovery through proper maintenance of condensers and evaporators, reducing solvent loss and operating costs.
Implementing these maintenance strategies can significantly improve operational stability, reduce the likelihood of mechanical issues, and ensure that the plant operates at peak efficiency.
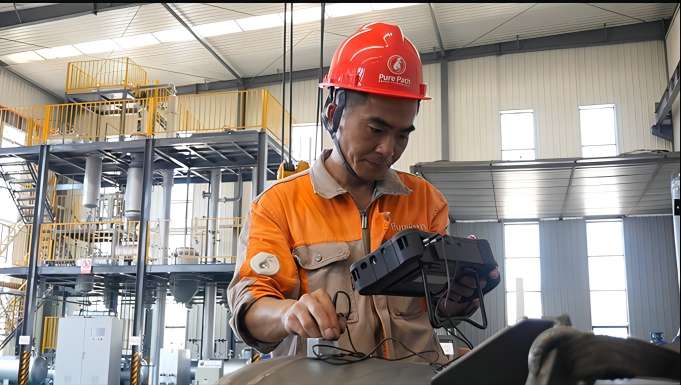
To sum up, base oil solvent extraction plants play a critical role in refining high-quality base oil for industrial and commercial applications. Understanding the extraction plant’s working principle and the technical intricacies behind each process step can help maximize production efficiency and product quality. By selecting the right solvent, maintaining optimal operating conditions, and regularly troubleshooting common issues, plant operators can achieve efficient and reliable extraction processes. Implementing robust maintenance and optimization practices further ensures the longevity and safety of equipment, making solvent extraction a cost-effective and sustainable choice for producing base oils.