Combining Base Oil Solvent Extraction with Other Refining Technologies
Base oils, the essential building blocks for lubricants, have to meet high standards in terms of purity, viscosity, and performance. As the demand for superior base oils increases, producers are constantly improving refining methods. Solvent extraction is a well-established technique for producing high-quality base oils. However, to meet today’s stringent requirements, combining this method with other refining technologies has proven to be a highly effective approach. This article will delve into how base oil solvent extraction works, its complementary refining technologies, and how these can be integrated for superior results.
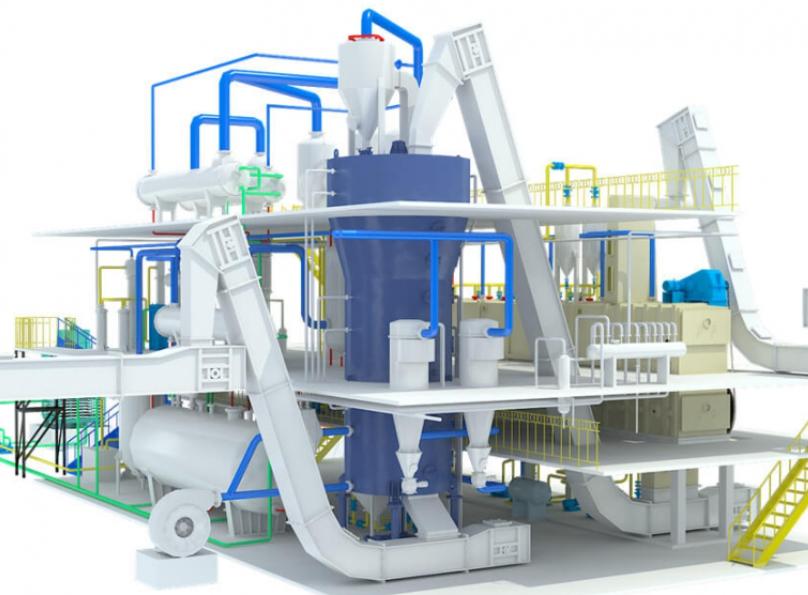
Base Oil Production and Solvent Extraction Overview
1. Base Oil Production Stages
- Distillation: The initial step involves heating crude oil to separate it into various fractions based on their boiling points. This process produces lighter fractions suitable for further refinement.
- Solvent Extraction: This critical refining process uses solvents to selectively remove undesirable components from the oil, such as aromatic hydrocarbons, sulfur, and nitrogen compounds. These impurities can negatively impact the oil’s stability and performance.
2. Role of Solvent Extraction
- Impurity Removal: Solvent extraction targets specific impurities that can reduce the base oil’s quality, improving characteristics such as viscosity and stability. By dissolving these contaminants, the process enhances the base oil’s overall performance.
- Solvent Recovery: After the extraction, the solvent is separated from the oil and recycled, making the process more efficient and cost-effective.
3. Integration with Other Technologies:
- Complementary Processes: Solvent extraction is often combined with other refining methods like hydrocracking and dewaxing to address additional impurities and enhance the oil’s properties further. This integrated approach ensures that the final base oil meets stringent industry standards for quality and performance.
Complementary Refining Technologies with Base Oil Solvent Extraction
To achieve the high-quality base oils required for advanced lubricants, solvent extraction is frequently complemented by additional refining technologies. Each of these processes addresses specific aspects of oil quality that solvent extraction alone cannot fully resolve.
Hydrocracking: Hydrocracking is a vital technology that uses hydrogen to break down larger, heavier hydrocarbon molecules into lighter, more desirable fractions. This process not only reduces the sulfur and nitrogen content but also saturates aromatic compounds, enhancing the oil’s stability and improving its viscosity index. By integrating hydrocracking with solvent extraction, refineries can produce base oils with better thermal stability, oxidation resistance, and a broader range of viscosities.
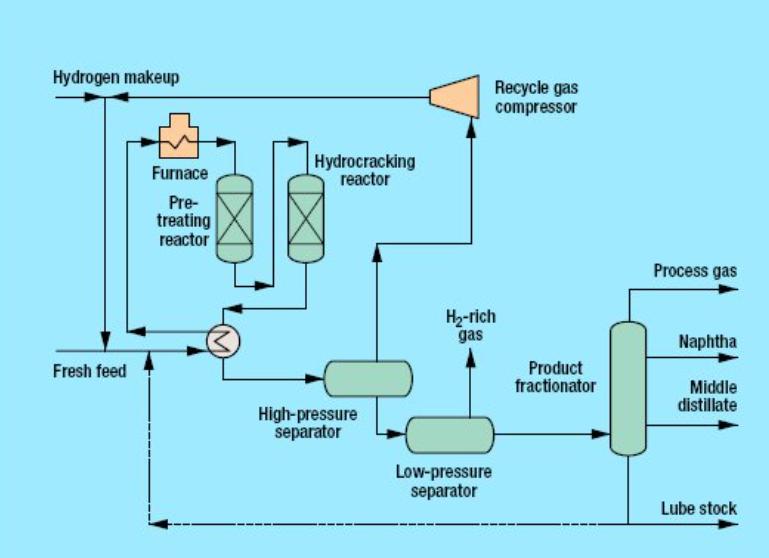
- Dewaxing: Dewaxing is essential for optimizing the low-temperature performance of base oils. This process removes waxy components that can cause the oil to solidify in colder temperatures. There are two primary methods: solvent dewaxing, which uses solvents to dissolve wax selectively, and catalytic dewaxing, which uses catalysts to modify the wax structure. When combined with solvent extraction, dewaxing ensures that the base oil remains fluid and effective in varying temperature conditions, making it suitable for diverse applications.
- Hydrotreating: Hydrotreating involves treating the oil with hydrogen to remove impurities such as sulfur and nitrogen, and to saturate any remaining aromatic compounds. This process enhances the oil’s color, stability, and overall purity. Hydrotreating complements solvent extraction by addressing impurities that may still be present after extraction, thus further improving the base oil’s quality and performance.
- Clay Treatment: Clay treatment, or adsorption, involves passing the base oil through a bed of clay or other adsorbents to remove residual color bodies, metals, and trace contaminants. This final polishing step is often used after solvent extraction to ensure that the base oil is clear and meets the highest purity standards. The use of clay treatment enhances the oil’s appearance and ensures it meets stringent specifications for marketability and performance.
By integrating these complementary technologies with solvent extraction, refineries can produce base oils that not only meet but exceed industry standards. This multi-faceted approach ensures that the final product has optimal properties, such as enhanced stability, improved performance across temperature ranges, and superior purity, making it suitable for a wide range of industrial and automotive applications.
Use of Oil Solvent Extraction Plant with Other Refining Equipment
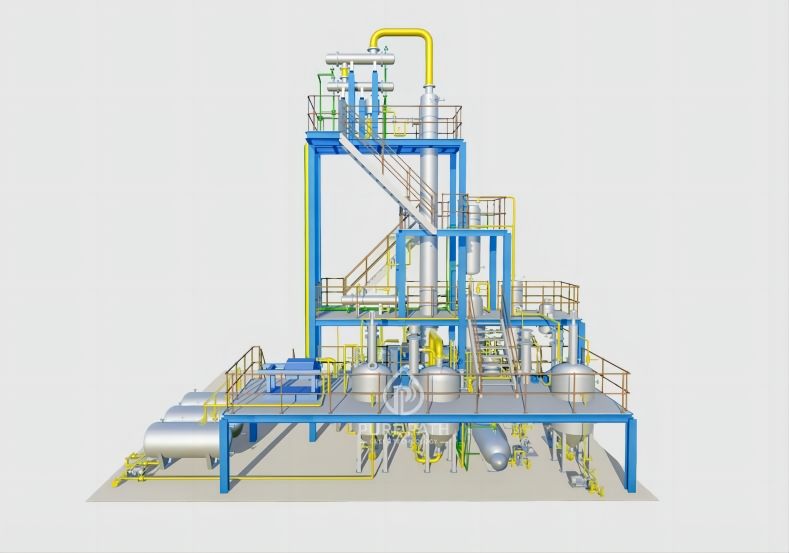
The effective integration of an oil solvent extraction plant with other refining equipment is crucial for optimizing the overall refining process and maximizing the production of high-quality base oils. By strategically combining solvent extraction with complementary technologies, refineries can enhance product quality, improve efficiency, and reduce environmental impact.
Key considerations for integrating solvent extraction with other refining equipment
- Process sequencing: The order in which solvent extraction is performed relative to other refining steps can significantly impact the overall efficiency and product quality. For example, solvent extraction may be conducted before or after hydrotreating, depending on the specific goals and characteristics of the base oil.
- Equipment compatibility: The solvent extraction plant must be compatible with the other refining units in terms of capacity, operating conditions, and safety requirements. Careful consideration must be given to factors such as flow rates, temperature, and pressure.
- Solvent recovery and recycling: Efficient solvent recovery and recycling are essential for minimizing costs and reducing environmental impact. The solvent extraction plant should be designed to capture and reuse the solvent, thereby reducing the need for fresh solvent.
- Waste management: The generation of waste products, such as spent solvent and extracted aromatics, must be carefully managed to comply with environmental regulations. Proper disposal or recycling of these materials is crucial.
- Automation and control: Modern solvent extraction plants are often highly automated, with sophisticated control systems that optimize the process and minimize human intervention. Automation can improve efficiency, reduce errors, and enhance safety.
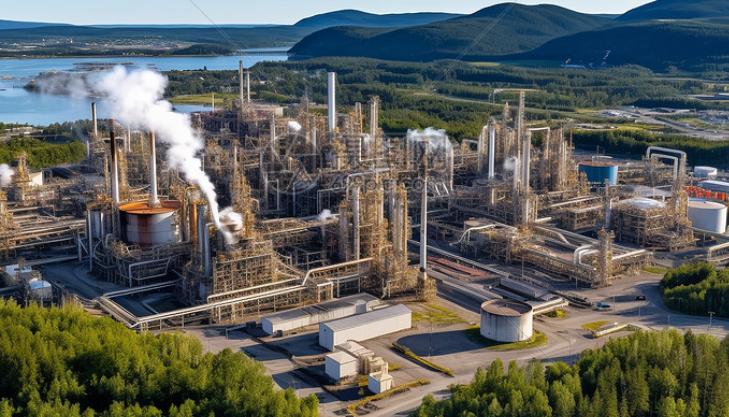
Examples of successful integration of solvent extraction with other refining equipment
- Solvent extraction followed by hydrotreating: This sequence can be used to remove aromatic compounds from the base oil before hydrotreating, which can improve the efficiency of the hydrotreating process and reduce the consumption of hydrogen gas.
- Solvent extraction combined with dewaxing: Solvent extraction can be integrated with dewaxing processes to selectively remove both aromatics and waxes from the base oil, resulting in a high-quality product with improved low-temperature performance.
- Solvent extraction followed by distillation: Solvent extraction can be used to produce a base oil with a reduced aromatic content, which can be further refined by distillation to isolate specific fractions with desired properties.
By carefully considering these factors and leveraging the latest technologies, refineries can effectively integrate solvent extraction plants with other refining equipment to optimize the production of high-quality base oils.
Solvent extraction is a fundamental process in base oil refining but needs to be complemented by other technologies to achieve high-quality oils. By integrating solvent extraction with hydrocracking, dewaxing, and hydrotreating, refineries enhance the performance, purity, and overall quality of base oils. Each technology targets specific refining needs, working together to produce base oils that meet modern lubricant standards. This combination ensures efficient production and compliance with regulatory and performance requirements.