Common Lube Oil Blending Plant Automation Systems and How to Choose
Lube oil blending plants are the backbone of the automotive and industrial sectors, providing essential lubricants that keep machinery running smoothly. As technology advances, automation has become an indispensable tool in modernizing these plants. This article delves into the common automation systems employed in lube oil blending plants, their benefits, and the crucial factors to consider when selecting the right system.
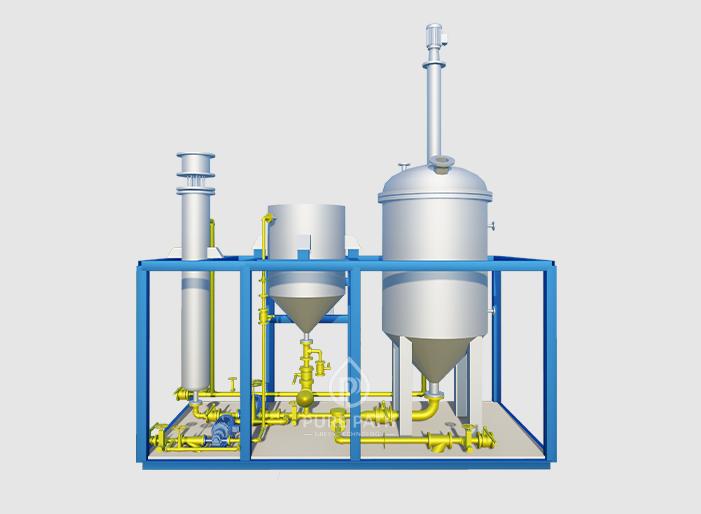
Understanding Automation Systems in Lube Oil Blending Plants
Automation in lube oil blending plants leverages a combination of hardware and software to optimize processes, maintain consistency, and improve overall productivity. The hardware components form the backbone of these systems and typically include Programmable Logic Controllers (PLCs), Human-Machine Interfaces (HMIs), sensors, and actuators.
On the software side, Supervisory Control and Data Acquisition (SCADA) systems, Distributed Control Systems (DCS), and Manufacturing Execution Systems (MES) work together to handle data processing, monitoring, and operational control. Together, these components streamline operations, allowing for the precise blending, temperature control, and packaging of various lubricant products. Understanding the types of automation systems used and their advantages is essential for choosing the right system for a lube oil blending plant.
Common Automation Systems in Lube Oil Blending Plants
Automation systems can be categorized into three primary types based on their functionality and the scale of operations they support: PLC-based systems, DCS-based systems, and SCADA-based systems.
1. PLC-Based Systems
PLC-based systems are often found in small to medium-sized lube oil blending plants. A PLC is a programmable device that can manage and control various processes within the plant, including valve operations, pump speeds, and temperature regulation. Paired with HMIs, PLC-based systems offer a user-friendly interface that allows operators to monitor and control the blending process easily.
Advantages of PLC-Based Systems
- Cost-effective: PLC systems generally require a lower initial investment than other options, making them a cost-effective solution for smaller plants.
- Reliable: PLC technology is well-established, with a proven record of reliable operation in industrial settings.
- Flexible: The system can be customized to meet the specific needs of a plant, allowing for modifications based on operational requirements.
Disadvantages of PLC-Based Systems
- Limited scalability: PLC-based systems may not be suitable for large-scale, complex operations. Scaling them up can be challenging and may require additional investment.
- Less sophisticated: Compared to other systems, PLC-based setups may lack advanced features such as predictive maintenance, real-time optimization, and comprehensive data analysis.
2. DCS-Based Systems
For larger, more complex lubricant blending plants, DCS-based systems are often preferred. DCS, or Distributed Control System, offers centralized control by integrating various subsystems within the plant, such as blending, filling, and packaging. This approach allows for greater operational visibility and control, as well as real-time monitoring and data collection.
Advantages of DCS-Based Systems
- Scalable: DCS-based systems can handle large-scale operations with multiple units, making them ideal for complex plants with extensive processes.
- Reliable: With high availability and redundancy features, DCS systems ensure continuous operation, minimizing the risk of downtime.
- Advanced features: DCS systems often include advanced capabilities such as predictive maintenance, process optimization, and energy management, making them suitable for plants seeking higher efficiency and reduced operational costs.
Disadvantages of DCS-Based Systems
- High initial investment: DCS-based systems come with significant upfront costs, making them a substantial investment.
- Complex implementation: Setting up and configuring a DCS requires specialized expertise, which can increase both time and cost.
3. SCADA-Based Systems
SCADA-based systems are designed for distributed systems, allowing operators to monitor and control different parts of the plant from a central location. SCADA collects data from PLCs, sensors, and other devices within the plant, providing real-time insights into operations. SCADA systems are ideal for blending plants where remote monitoring and control of equipment are essential.
Advantages of SCADA-Based Systems
- Flexible: SCADA can be customized to meet the unique requirements of the lubricant blending plant, providing a tailored approach to control.
- Scalable: SCADA systems are highly adaptable, allowing them to expand as the lube oil blending equipment grows.
- Remote monitoring and control: SCADA enables operators to manage distributed systems from a central location, reducing the need for on-site personnel.
Disadvantages of SCADA-Based Systems
- Additional hardware requirements: SCADA may require extra hardware for data acquisition and communication between devices.
- Complexity: SCADA systems can be challenging to configure and maintain, often requiring specialized skills.
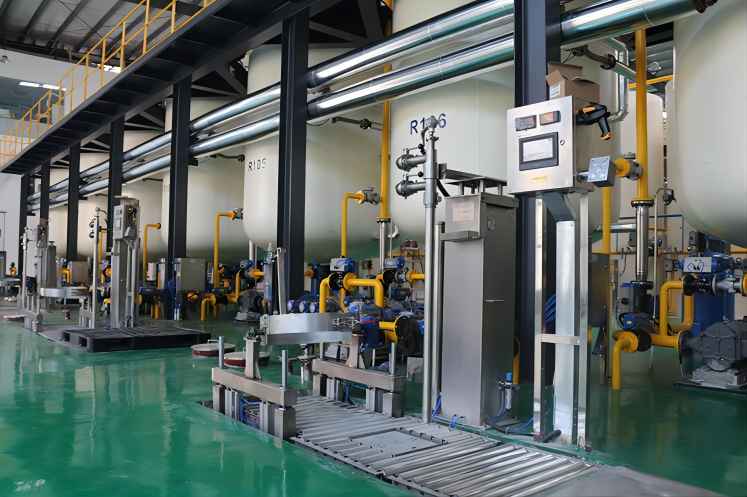
Key Considerations for Choosing an Automation System
Selecting an automation system for a lube oil blending plant requires careful assessment of several factors:
1. Plant Size and Complexity
- Small to medium-sized plants: A PLC-based system may be suitable, providing cost-effective and reliable control.
- Large, complex plants: A DCS-based system may be better, offering scalability and advanced features.
- Distributed systems: SCADA is a good choice, enabling efficient remote monitoring and control.
2. Process Requirements
- Control capabilities: The system must be able to precisely control blending ratios, temperatures, and pressures.
- Real-time monitoring: Real-time tracking of key parameters is critical for maintaining consistent product quality.
3. Future Expansion
- Modularity and scalability: Choose a system that can grow with the plant, allowing for integration with emerging technologies like IoT and AI.
- Long-term adaptability: Consider the longevity of the system and its ability to support future enhancements and upgrades.
4. Budget Constraints
- Initial vs. ongoing costs: Evaluate both the upfront investment and maintenance costs.
- Potential ROI: Consider how the automation system will impact productivity, quality, and maintenance, contributing to a positive return on investment.
Benefits of Automation in Lube Oil Blending Plants
Implementing automation in lube oil blending plants offers multiple benefits:
1. Improved Efficiency
- Optimization: Automation optimizes production, reducing downtime and minimizing waste.
- Resource utilization: Real-time monitoring enables better allocation and use of resources, boosting overall efficiency.
2. Enhanced Quality Control
- Consistency: Automated systems provide precise control over blending parameters, ensuring consistent product quality.
- Proactive quality management: Automated data analysis can detect potential issues early, preventing quality deviations.
3. Increased Safety
- Reduced human error: Automation minimizes manual intervention, reducing the risk of errors.
- Hazard reduction: Remote monitoring allows operators to manage equipment from safer locations, reducing exposure to hazardous environments.
4. Better Decision-Making
- Data-driven insights: Automation provides real-time data and analytics, supporting informed decisions.
- Predictive maintenance: With predictive insights, maintenance can be scheduled proactively, minimizing the likelihood of unplanned downtime.
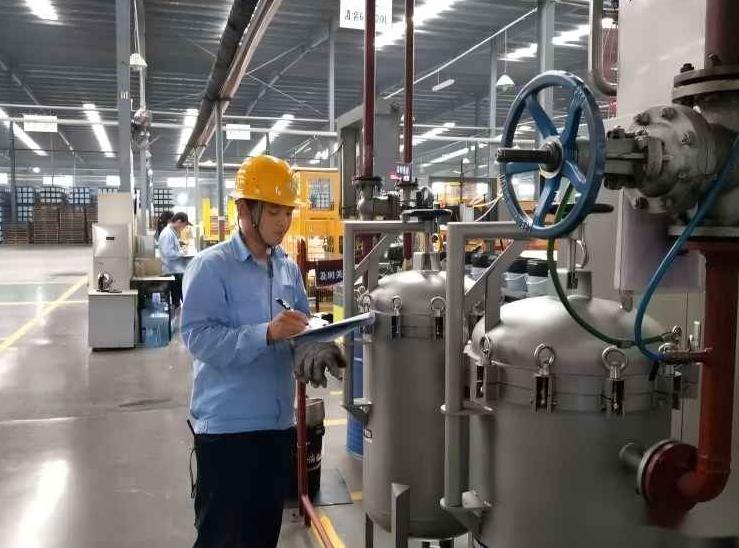
Overall, automation has revolutionized the lube oil blending industry, enabling plants to improve efficiency, product quality, and safety. By carefully evaluating factors such as plant size, process requirements, scalability, and budget, plants can select the right automation system to meet their needs. As technology continues to advance, the future of lube oil blending plants looks promising, with automation playing an increasingly vital role in enhancing productivity and maintaining quality.