Common Technologies of Waste Oil to Base Oil and How to Choose
Waste oil is a byproduct generated from various industrial processes, including motor oil, lubricants, and hydraulic oils, which are often contaminated with impurities such as metals, carbon particles, and organic compounds. The improper disposal of waste oil can cause severe environmental contamination, affecting water bodies, soil, and air quality, as well as posing health risks to humans and wildlife. Given the global need to reduce pollution and conserve resources, recycling waste oil into base oil has emerged as a significant avenue for waste minimization and resource recovery.
Base oil, which is a refined oil product used in the formulation of lubricants, hydraulic fluids, and other industrial oils, has a substantial demand in the market. The recycling of waste oil into high-quality base oil offers an economically and environmentally viable solution. This article delves into the technologies used for recycling waste oil into base oil and provides an in-depth economic analysis of the different recycling methods.
Part 1: Common Technologies for Recycling Waste Oil into Base Oil
1. Traditional Technologies
Acid-Base Refining
Acid-base refining is one of the most commonly used methods for recycling waste oil. The process involves treating waste oil with acidic or alkaline solutions to remove impurities, such as metals, sulfur, and organic contaminants. The oil is then neutralized and separated from the sludge or precipitate formed during treatment.
- Principle: Acid or base solutions react with the impurities in the oil, leading to the formation of soluble salts that can be easily removed.
- Advantages: It is a simple and widely used technique for removing acidic impurities and metals from waste oil.
- Disadvantages: This method is not very efficient in removing high molecular weight contaminants and may produce secondary waste, requiring additional disposal.
- Environmental Impact: The process generates waste acidic or alkaline solutions that require proper disposal to prevent secondary pollution.
Solvent Extraction
Solvent extraction involves mixing waste oil with a solvent that selectively dissolves contaminants, allowing the removal of impurities such as sulfur, nitrogen compounds, and high-molecular organic substances. After extraction, the solvent is evaporated, and the purified oil is separated.
- Principle: The oil is mixed with a solvent (such as aromatic hydrocarbons, alcohols, or ethers), which selectively dissolves impurities, while the oil remains relatively unaffected.
- Common Solvents: Aromatic hydrocarbons, alcohols, and ethers are commonly used for solvent extraction.
- Advantages: Solvent extraction can effectively remove organic impurities and produce a cleaner base oil.
- Disadvantages: The main issue with this method is the recovery and disposal of solvents. Some solvents may be toxic and require careful handling and recycling.
- Suitable Range: This method is ideal for waste oils with lower levels of contaminants and is particularly effective for lubricating oils.
Distillation
Distillation is a separation technique that uses differences in boiling points to separate the components of waste oil. The process involves heating the oil to evaporate its components and then condensing the vapors into separate fractions based on their boiling points.
- Types of Distillation:
- Atmospheric Distillation: Involves heating waste oil to its boiling point under normal atmospheric pressure to separate light fractions.
- Vacuum Distillation: Lowers the pressure to distill high-boiling components at a reduced temperature.
- Molecular Distillation: A specialized method that uses very low pressure to separate high-boiling contaminants from oil, making it suitable for high-viscosity waste oils.
- Advantages: Distillation effectively separates lighter hydrocarbons from heavier contaminants and is ideal for recovering base oils from waste oils.
- Disadvantages: It requires significant energy input and specialized equipment for high-efficiency separation, which can increase costs.
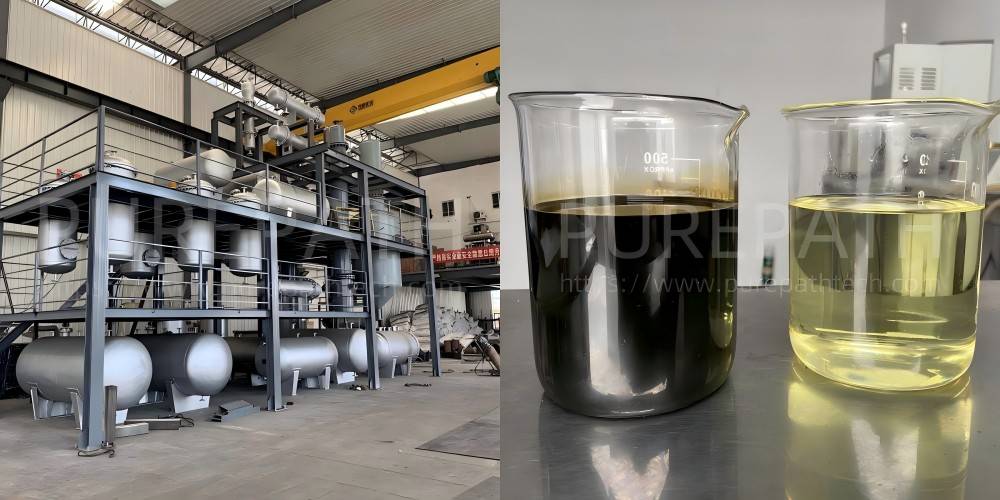
2. Modern Technologies
Hydrofining (Hydrotreating)
Hydrofining or hydrotreating is a process that uses hydrogen gas and a catalyst under high pressure and temperature to remove sulfur, nitrogen, and oxygen from waste oils. This method not only removes impurities but also improves the chemical stability and quality of the base oil.
- Principle: The hydrogen reacts with unsaturated hydrocarbons in the waste oil, converting them into saturated hydrocarbons and removing contaminants like sulfur and nitrogen.
- Advantages: Hydrofining results in a high-quality base oil with excellent stability, and it can process a wide range of waste oils.
- Application: This technology is particularly useful for refining used motor oils and other high-quality lubricants.
- Challenges: The high operational cost and the need for specialized equipment, including hydrogen gas, make this method more expensive than other traditional techniques.
Catalytic Cracking
Catalytic cracking involves breaking down heavy molecules in waste oil into lighter molecules using a catalyst, resulting in higher-quality base oils. This process is commonly used in petroleum refining but has also been adapted to waste oil recycling.
- Principle: A catalyst breaks down larger hydrocarbons into smaller, more valuable fractions, effectively producing lighter base oils.
- Catalysts Used: Acidic, zeolite-based catalysts are commonly employed to enhance cracking efficiency.
- Advantages: Catalytic cracking can produce high-value base oils with improved performance characteristics.
- Disadvantages: This process is energy-intensive and requires sophisticated catalytic systems, making it expensive.
- Product Characteristics: The base oils produced via catalytic cracking have low sulfur content and superior lubrication properties.
Membrane Separation
Membrane separation technologies, such as microfiltration, ultrafiltration, and reverse osmosis, are used to separate solid contaminants and water from waste oil. These methods are gaining attention for their lower energy consumption compared to traditional techniques.
- Principle: A membrane selectively allows smaller particles to pass through while retaining larger contaminants.
- Advantages: Membrane technologies have low energy consumption and are capable of removing fine particulate matter and water from waste oil.
- Challenges: Membranes are susceptible to fouling and may require periodic cleaning or replacement, which adds to maintenance costs.
- Applications: Membrane separation is particularly useful for wastewater and low-viscosity oils but is less effective for high-viscosity or highly contaminated waste oils.
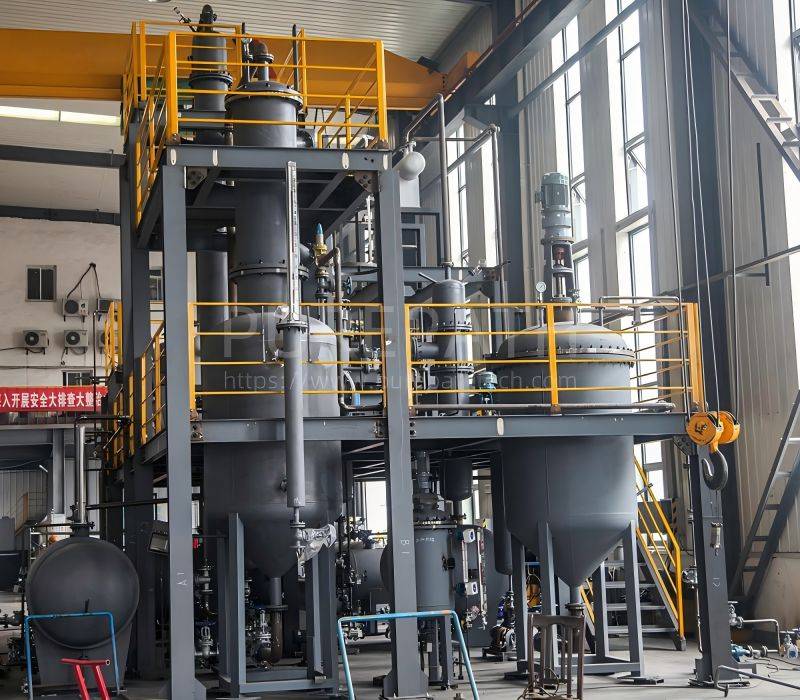
3. Emerging Technologies
Biotechnological Approaches
Biotechnology, including microbial degradation and enzymatic catalysis, is being explored for recycling waste oils. This approach leverages microorganisms or enzymes to break down contaminants in waste oil into harmless byproducts, offering a more environmentally friendly solution.
- Principle: Microorganisms or enzymes break down organic compounds in the waste oil, turning them into simpler, non-toxic substances.
- Advantages: This method is highly sustainable, requires minimal energy, and can be environmentally benign.
- Challenges: The technology is still under development, and the speed of bioremediation is slow, making it less commercially viable at present.
Nanotechnology
Nanotechnology uses nanoparticles as catalysts or adsorbents to enhance the recycling process. Nanomaterials with high surface areas can accelerate the removal of impurities from waste oil, improving the quality of the final product.
- Principle: Nanoparticles interact with contaminants in waste oil, enhancing separation and improving oil purification.
- Advantages: High efficiency in removing pollutants, low energy consumption, and minimal environmental impact.
- Challenges: The high cost of nanomaterials and the need for further research to optimize their effectiveness in oil recycling remain significant barriers.
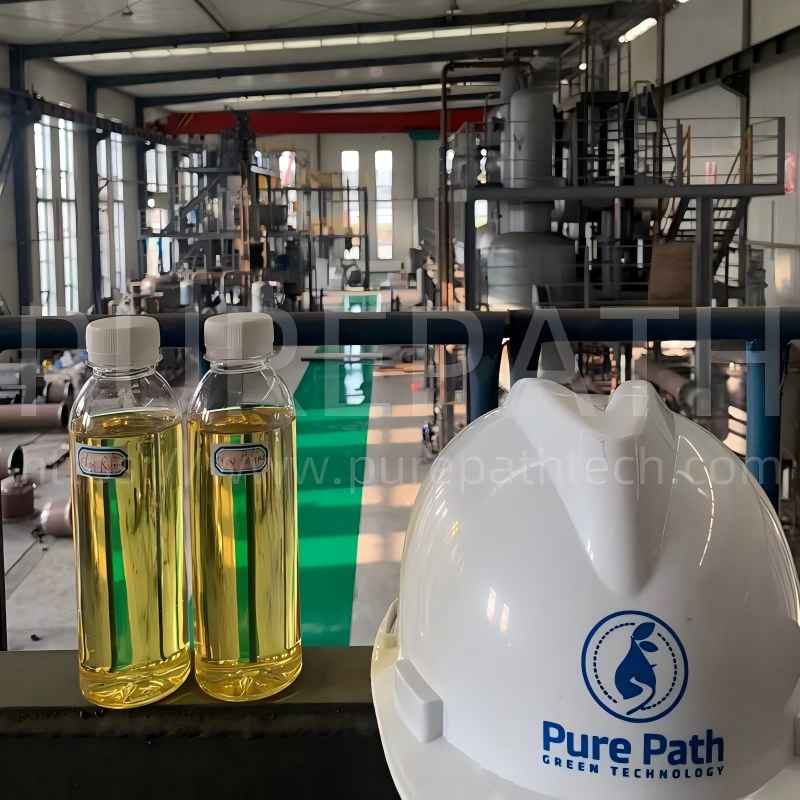
Part 2: How to Select the Most Economically Viable Technology
Factors to Consider in Technology Selection
- Type and Composition of Waste Oil: The specific type of waste oil (motor oil, hydraulic oil, etc.) and its contaminant levels dictate which technology is best suited. Some methods, like hydrofining, are better for oils with high levels of impurities, while others, like solvent extraction, may be more suitable for lower-contaminant oils.
- Product Quality Requirements: The quality standards for the recycled base oil, including viscosity, stability, and purity, will determine which technology is appropriate. High-end lubricants require advanced processes like hydrofining or catalytic cracking.
- Technology Maturity and Reliability: Established technologies like distillation and solvent extraction offer reliability and proven efficiency, while newer methods like bioremediation or nanotechnology are still in development stages and may not yet provide stable results.
- Investment and Operational Costs: Capital investment for equipment, operational costs (energy consumption, catalyst maintenance), and labor costs must all be considered. Modern technologies, while efficient, often come with high initial investments.
- Environmental and Sustainability Considerations: With increasing environmental regulations, the sustainability of the technology is a key factor. Technologies with lower emissions, energy use, and waste generation will be more attractive for long-term investment.
Economic Analysis
- Cost-Benefit Analysis: Cost factors include raw material costs, energy usage, catalyst maintenance, and labor. Efficient technologies like catalytic cracking and hydrofining typically have higher operational costs but may yield a higher value of recycled base oil.
- Market Demand and Price Volatility: The market demand for recycled base oil and price volatility can affect the profitability of recycling projects. An in-depth understanding of these market factors is crucial for determining the financial viability of a technology.
- Policy and Regulatory Factors: Government incentives, environmental regulations, and tax benefits can significantly affect the economic feasibility of waste oil recycling technologies. Policy support for eco-friendly practices can help offset the high capital costs associated with some advanced technologies.
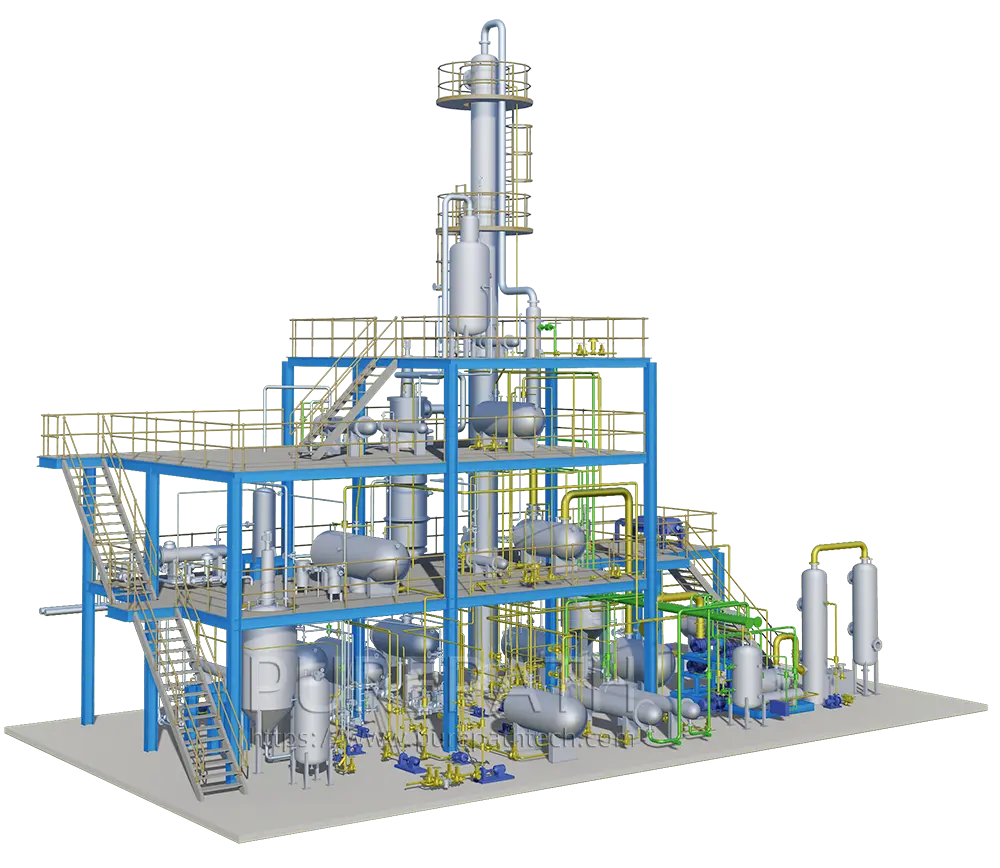
Conclusion
Recycling waste oil into base oil is a promising solution for both environmental protection and economic gain. Traditional methods such as distillation and solvent extraction are still widely used due to their simplicity and cost-effectiveness, while modern technologies like hydrofining and catalytic cracking offer high-quality products with improved performance characteristics. Emerging technologies like biotechnology and nanotechnology hold great promise for more sustainable and energy-efficient solutions.
The selection of the most economically viable technology depends on several factors, including waste oil type, product quality requirements, technology maturity, investment costs, and environmental considerations. As the global demand for base oil increases, investing in advanced and sustainable recycling technologies will help meet both economic and environmental goals, shaping the future of waste oil recycling.