Comprehensive Guide to Crude Oil Refining and Processing
Crude oil refining is a fundamental process in the petroleum industry that transforms raw crude oil into valuable products such as gasoline, diesel, fuel oil, lubricants, and chemical feedstocks. This intricate process involves a series of physical and chemical treatments designed to separate and refine the various components of crude oil. Understanding the basics of crude oil refining, the equipment used, and the factors affecting product quality is crucial for both industry professionals and those interested in the mechanics of petroleum processing.
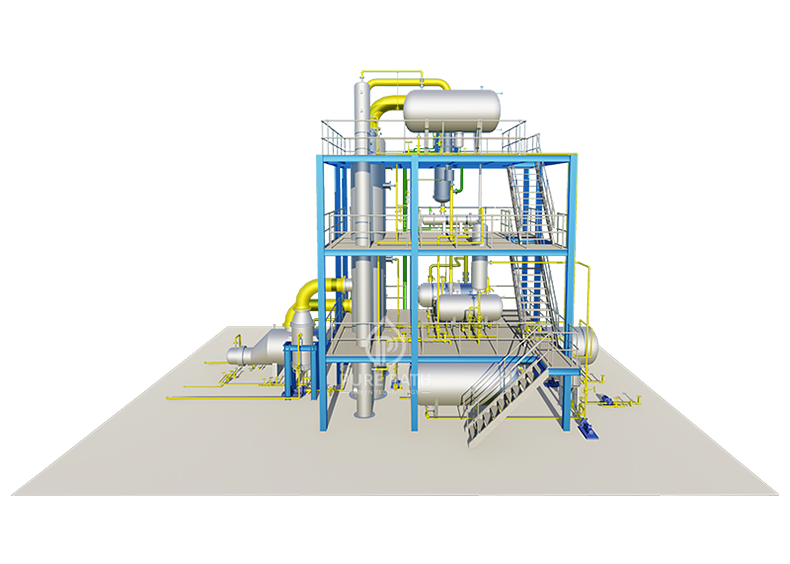
What is Crude Oil Refining?
Crude oil refining, also known as petroleum refining, is a process that separates crude oil into its constituent parts and converts these parts into usable products. This process is essential for producing a wide range of petroleum products that power vehicles, generate electricity, and serve as raw materials for chemical industries.
The primary goal of crude oil refining is to efficiently and economically produce high-quality petroleum products that meet market demands and regulatory standards. This involves several key steps:
Main Steps in Crude Oil Refining
- Pre-Treatment: The initial stage of crude oil refining involves pre-treatment processes that remove water and salts from the crude oil. This step is crucial as it prevents corrosion and fouling of the equipment used in subsequent refining stages.
- Atmospheric Distillation: This process uses the differences in boiling points of various components in crude oil to separate them. In atmospheric distillation, crude oil is heated in a furnace and then fed into a distillation column. As the oil rises through the column, different fractions are collected based on their boiling points.
- Vacuum Distillation: For heavier fractions that do not vaporize under atmospheric pressure, vacuum distillation is used. By reducing the pressure, the boiling points of these heavy fractions are lowered, allowing for their separation without cracking.
- Catalytic Cracking: This process breaks down larger, heavier molecules into lighter, more valuable products such as gasoline and diesel. Catalytic cracking involves the use of a catalyst and high temperatures to promote the cracking of heavy hydrocarbons.
- Hydrocracking: Similar to catalytic cracking, hydrocracking uses hydrogen and a catalyst to break down heavy molecules. This process also reduces sulfur and nitrogen content, improving the quality of the final products.
- Product Blending: The final step involves blending different fractions to meet market specifications and quality standards. This ensures that the final products have the desired properties, such as octane rating for gasoline or cetane number for diesel.
Key Products of Crude Oil Refining
The refining process yields a variety of products, each with distinct uses:
- Gasoline: The most widely used fuel for internal combustion engines in automobiles.
- Diesel: Primarily used in trucks, buses, and heavy machinery.
- Fuel Oil: Used for heating and as a fuel for large industrial boilers and ships.
- Lubricants: Essential for reducing friction and wear in engines and machinery.
- Chemical Feedstocks: Basic materials for the production of plastics, solvents, and other chemicals.
Key Equipment in a Petroleum Oil Refinery
The equipment used in petroleum oil refining is essential for transforming crude oil into various products. Some of the key pieces of equipment include:
- Distillation Columns: These are used for atmospheric and vacuum distillation. Atmospheric distillation columns separate lighter fractions, while vacuum distillation columns handle heavier residues.
- Reactors: Reactors are crucial for carrying out chemical reactions such as hydrodesulfurization (HDS) and hydrocracking. They ensure that the reactions occur efficiently and under controlled conditions.
- Fractionators: These units further separate and purify the products obtained from the distillation columns, improving their quality and usability.
- Furnaces: Furnaces provide the necessary heat for various refining processes. They are used to heat petroleum oil before it enters the distillation columns or reactors.
- Regenerators, Pumps, and Compressors: Regenerators clean and reactivate catalysts used in cracking processes. Pumps and compressors are used to move fluids and gases throughout the refinery.
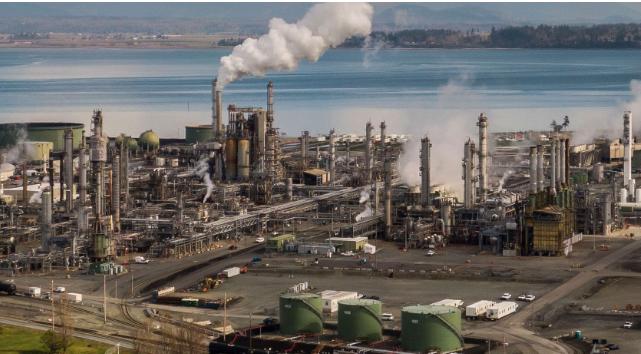
Technical Features of Crude Oil Processing Plant
1. Trends Towards Efficiency and Automation
Crude oil processing equipment has evolved significantly, with modern refineries incorporating advanced technologies to enhance efficiency and reduce environmental impact:
- Efficiency and Automation: Modern equipment is designed for high efficiency and includes automated systems that optimize operations and minimize human intervention.
- Intelligent Systems: Advanced control systems monitor and adjust parameters in real time, improving the reliability and performance of the equipment.
- Design Innovations: Innovations in equipment design focus on increasing capacity, reducing energy consumption, and minimizing environmental emissions.
2. Advantages of Modern Crude Oil Refining Technologies
Modern refining technologies offer several advantages over their predecessors:
- Enhanced Product Quality: New processes can produce cleaner fuels and petrochemicals with reduced sulfur and nitrogen content.
- Increased Yields: Advanced refining techniques can increase the yield of high-value products from each barrel of crude oil.
- Reduced Energy Consumption: Modern refineries are more energy-efficient, reducing the overall operational costs.
- Lower Emissions: Advanced technologies can significantly reduce greenhouse gas emissions and other pollutants.
3. Functions of Key Crude Oil Processing Plant
Understanding the specific functions of key equipment is crucial for appreciating the complexity of crude oil refining:
- Crude Oil Separators: These units initially separate crude oil into its various components, setting the stage for further processing.
- Atmospheric Distillation Columns: Separate lighter fractions such as gasoline and diesel based on boiling points.
- Vacuum Distillation Columns: Handle heavier residues that require lower pressures to distill.
- Hydrotreaters: Used to remove sulfur and nitrogen from crude oil, improving product quality and reducing environmental impact.
- Catalytic Crackers: Convert heavy hydrocarbons into lighter products such as gasoline and diesel. This process improves the yield of valuable products.
- Sulfur Removal Systems: Prevent the formation of harmful sulfur compounds in the final products.
- Reforming Units: Improve the quality of gasoline by increasing its octane rating and enhancing its performance.
Differences Between Atmospheric and Vacuum Distillation Columns
1. Operating Pressures
- Atmospheric Distillation Columns: Operate at atmospheric or slightly higher pressures, suitable for separating lighter fractions like gasoline and diesel.
- Vacuum Distillation Columns: Operate under reduced pressure, which lowers the boiling points of heavier fractions, making it possible to separate them without high temperatures.
2. Design Purposes
- Atmospheric Distillation Columns: Designed to separate lighter components that boil at lower temperatures.
- Vacuum Distillation Columns: Focus on handling heavier residues from atmospheric distillation by reducing the pressure to avoid thermal cracking.
3. Applicable Components
- Atmospheric Distillation Columns: Deal with lighter to medium boiling point fractions.
- Vacuum Distillation Columns: Handle heavy residues and high boiling point components that remain after atmospheric distillation.
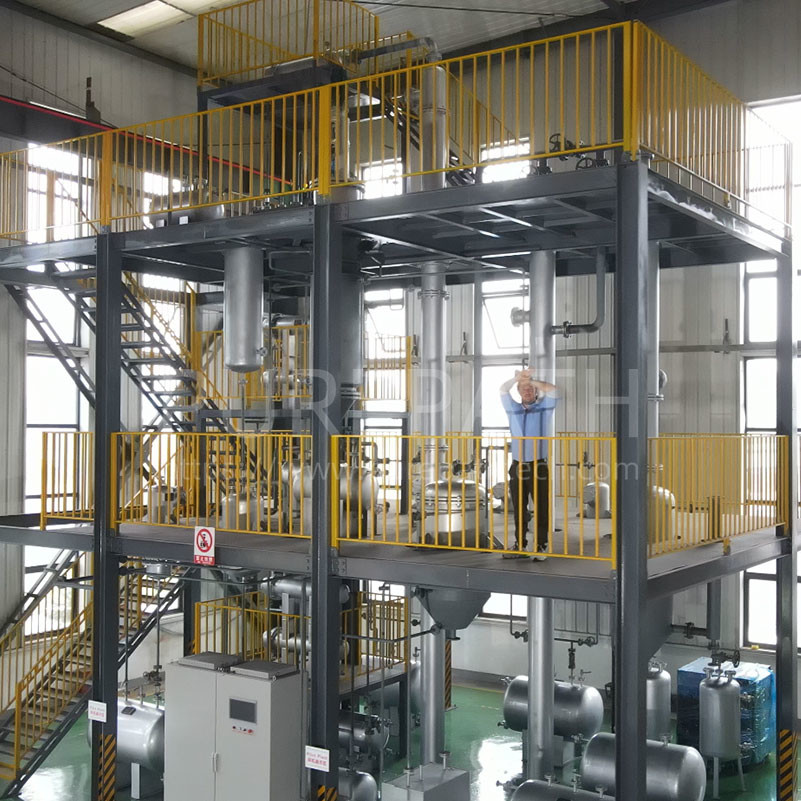
Role of Catalytic Cracking Units in Crude Oil Processing
Catalytic cracking is a pivotal process in crude oil refining, crucial for enhancing the production of lighter and more economically valuable products such as gasoline and diesel. This process involves breaking down larger, heavier hydrocarbon molecules into smaller, more useful molecules using a catalyst at high temperatures, typically between 450°C and 530°C. Not only does catalytic cracking increase the yield of these valuable products, but it also improves their quality, making them more suitable for various applications.
1. Cracking Reactions
Catalytic cracking primarily involves three key reactions—cracking, isomerization, and aromatization. During cracking, large hydrocarbon molecules are broken down into smaller ones. Isomerization transforms straight-chain hydrocarbons into branched forms, which are more effective in combustion. Aromatization converts alkanes into aromatic hydrocarbons, which enhance the octane rating of gasoline. The catalyst used in this process lowers the activation energy required for these reactions, enabling them to proceed efficiently and selectively.
2. Equipment Components
- Reactors: The reactor is the heart of the catalytic cracking unit, where the catalyst facilitates the cracking reactions. This equipment must handle high temperatures and pressures while ensuring efficient contact between the feedstock and the catalyst.
- Regenerators: After the cracking reactions, the catalyst becomes coated with coke—a byproduct that reduces its effectiveness. Regenerators burn off this accumulated coke, restoring the catalyst’s activity and maintaining its performance over time.
- Fractionators: These units separate the various products resulting from the cracking reactions. Fractionators use distillation to divide the product mixture into different fractions based on boiling points, ensuring the effective separation and recovery of valuable products.
3. Flexibility and Efficiency
Catalytic cracking units are designed for flexibility and efficiency, allowing refineries to adapt to fluctuating market demands. By adjusting operating conditions such as temperature and pressure, and by using different types of catalysts, these units can optimize the yield and quality of the products. This adaptability not only maximizes economic returns but also enhances the overall efficiency of the refining process, making catalytic cracking a key component in modern crude oil refining operations.
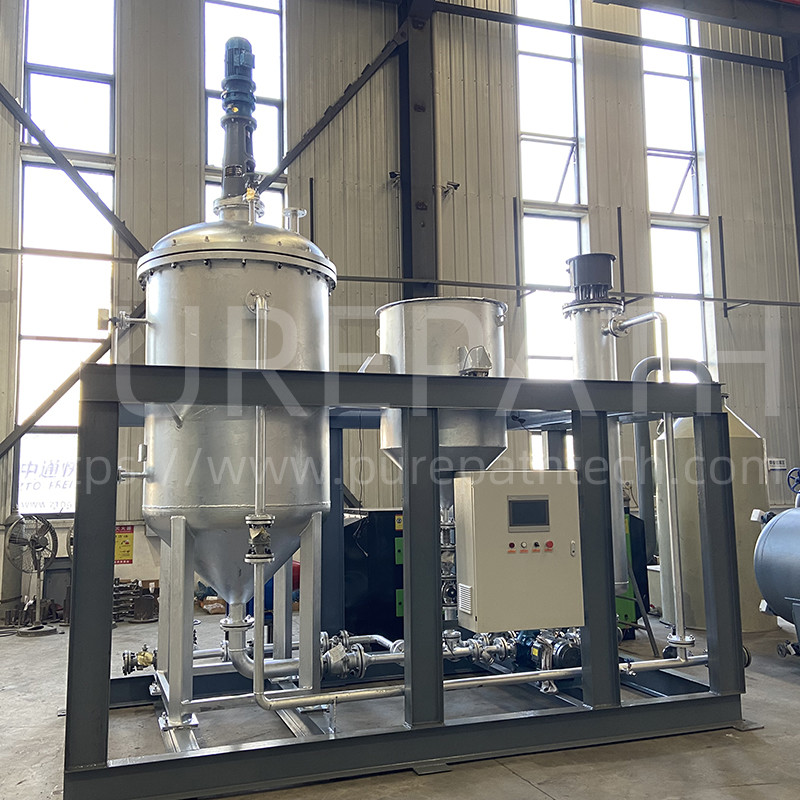
How Hydrocracking Reduces Sulfur and Nitrogen Content
Hydrocracking is a vital process in reducing sulfur and nitrogen content in crude oil. It uses hydrogen in the presence of a catalyst to convert heavy hydrocarbons into lighter products, simultaneously removing sulfur and nitrogen impurities.
1. Desulfurization (HDS): Involves breaking C-S bonds to produce hydrogen sulfide (H2S) and lighter hydrocarbons. Different sulfur compounds react at varying rates, with thiols reacting the fastest.
Denitrification (HDN): Converts nitrogen-containing compounds into ammonia (NH3) and lighter hydrocarbons. Amine compounds are more easily hydrocracked than heterocyclic nitrogen compounds.
3. Hydrogen Saturation: Involves saturating olefins to convert them into stable alkanes, improving the stability of the final products. Hydrogenation also reduces the presence of unsaturated components.
4. Optimization and Efficiency: Modern hydrocracking units utilize advanced catalysts and optimized reactor designs to enhance efficiency and lower energy consumption. Intelligent technologies improve control precision and operational flexibility, contributing to more sustainable and cost-effective refining.
Factors Affecting Product Quality in Crude Oil Refining
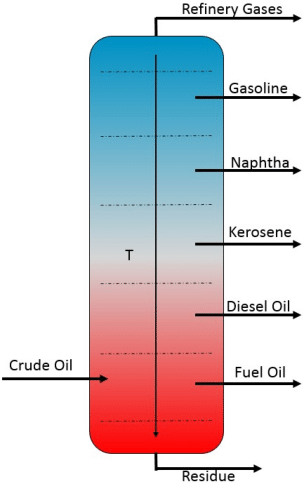
1. Process Factors
- Technology Level: Advanced refining technologies reduce impurities and improve product quality.
- Operating Conditions: Temperature, pressure, and reaction time significantly affect the final product’s quality.
- Equipment Quality: The performance of reactors, heat exchangers, and separation units impacts product quality.
2. Raw Material Factors
- Crude Oil Quality: The composition, sulfur, and nitrogen content of crude oil directly influence the quality of the refined products.
- Additives: Substances like anti-knock agents and detergents enhance product performance.
- Catalysts: The choice of cracking, hydrotreating, and reforming catalysts is crucial for achieving desired product specifications.
3. Environmental Factors
- Temperature and Humidity: Optimal conditions maintain product stability.
- Light Exposure: Protection from strong light prevents degradation and discoloration.
4. Storage and Transportation
- Conditions: Proper storage and transportation conditions, including temperature and humidity control, are essential for maintaining product quality.
Conclusion
Crude oil refining is a complex and multifaceted process that transforms raw crude oil into a range of valuable products. Understanding the basic concepts, equipment, and factors influencing product quality provides valuable insights into the petroleum refining industry. As technology advances, refinements in equipment and processes continue to enhance efficiency and environmental sustainability, shaping the