Converting Used Engine Oil to Diesel: A Technological Exploration
Used engine oil, a byproduct of internal combustion engines, poses significant environmental challenges if not disposed of properly. Its disposal in landfills can contaminate groundwater and soil, while improper burning releases harmful pollutants into the atmosphere. In recent years, there has been a growing interest in converting used engine oil to diesel fuel, a process that not only addresses environmental concerns but also provides a sustainable energy source. This article delves into the science and technology behind this process, exploring the reaction mechanisms, process flow, factors influencing yield and quality, and potential applications.
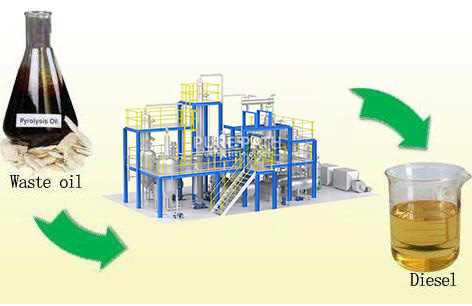
Reaction Mechanisms in Converting Used Engine Oil to Diesel
Used engine oil is a complex mixture of hydrocarbons, additives, and contaminants. The process of converting it into diesel involves breaking down the long hydrocarbon chains into shorter ones and then recombining them to form diesel molecules.
- Composition of Used Engine Oil: Understanding the composition of used engine oil is crucial. It primarily consists of base oil, additives, and contaminants like fuel, water, and wear metals. These components influence the efficiency of the conversion process.
- Cracking: This is the primary reaction where long hydrocarbon chains are broken into smaller fragments. Heat and pressure are applied to break the molecular bonds. Catalytic cracking is a common method that employs catalysts to lower the required temperature and improve selectivity.
- Recombination: The smaller hydrocarbon fragments then recombine to form molecules within the diesel range. Factors like temperature, pressure, and catalyst type influence the nature of the recombined molecules.
- Catalytic Role: Catalysts play a pivotal role in the conversion process. They accelerate the reaction rate, increase product yield, and improve product quality. Zeolites, for instance, are commonly used catalysts due to their acidic properties and high surface area.
Process Flow in Converting Used Engine Oil to Diesel
The conversion of diesel from waste engine oil process typically involves the following steps:
1. Pre-Treatment: Removing Impurities
Before conversion, used engine oil undergoes pre-treatment to eliminate water, dirt, and metal contaminants:
- Dehydration: Removes water through heating or separation techniques.
- Filtration: Extracts particulates and other solid impurities.
2. Cracking: Breaking Down Hydrocarbon Chains
This stage converts pre-treated oil into shorter-chain hydrocarbons:
- Thermal Cracking: Requires high temperatures (400–600°C), producing a range of hydrocarbons, some of which are further processed into diesel.
- Catalytic Cracking: Employs specific catalysts to streamline reactions, yielding higher proportions of diesel.
3. Refinement: Enhancing Diesel Quality
Refined processing improves the diesel product’s quality to meet market standards:
- Acid-Alkali Washing: Neutralizes acids and removes sulfur compounds.
- Bleaching Earth Treatment: Removes colors and odors, ensuring clear diesel output.
- Distillation: Separates diesel fractions from lighter and heavier hydrocarbons.
4. Post-Treatment: Final Adjustments
Final processing ensures compliance with diesel quality standards:
- Desulfurization: Reduces sulfur content to meet environmental regulations.
- Additive Blending: Enhances fuel properties like stability, lubricity, and combustion efficiency.

Diesel Yield from Used Engine Oil
1. Factors Influencing Yield
The amount of diesel obtained from waste oil to diesel plant is determined by several critical factors:
- Feedstock Quality: Cleaner and higher-grade used motor oil produces more diesel, as it contains fewer impurities and more usable hydrocarbons.
- Process Conditions: Variables such as temperature, pressure, and reaction duration play a vital role in determining the efficiency and yield of the process.
- Catalyst Type: Advanced catalysts tailored for diesel production enhance both the quantity and quality of the output by improving reaction efficiency and selectivity.
2. Yield Comparison Between Techniques
- Thermal Cracking: Achieves diesel yields of approximately 60–70%, but the process lacks precision in targeting diesel-range hydrocarbons, leading to more byproducts.
- Catalytic Cracking: Produces higher yields of 75–85%, with greater specificity for diesel molecules, resulting in a cleaner and more efficient process.
3. Strategies to Improve Diesel Yield
- Refining Catalyst Design: Using advanced catalysts increases conversion rates while minimizing unwanted byproducts.
- Adopting Innovative Reaction Technologies: Modern reactors, such as fluidized bed systems, ensure better contact between oil and catalysts, enhancing output.
- Recycling Heavy Residues: Unconverted fractions and heavier hydrocarbons can be reprocessed to extract additional diesel, optimizing overall yield.
Quality Standards of Making Diesel from Used Motor Oil
1. Essential Quality Metrics
Diesel derived from waste oil must meet rigorous standards to match or surpass conventional diesel in performance:
- Cetane Number: A high cetane number ensures better combustion efficiency and engine performance, which is achievable with refined waste oil diesel.
- Sulfur Content: Environmental regulations require low-sulfur diesel to reduce emissions, making desulfurization a key step in processing.
- Viscosity and Flash Point: The final product must maintain proper viscosity for smooth fuel injection and a safe flash point to minimize fire hazards.
- Density: Density influences the fuel’s energy content and storage characteristics.
2. Influencing Factors on Quality
- Impurities in the Feedstock: Residual contaminants in the raw material can affect diesel purity.
- Efficiency of Refinement Steps: Effective acid-alkali washing, distillation, and desulfurization are critical to achieving high-quality diesel.
- Additive Blending: Adding stabilizers, lubricants, or combustion improvers ensures the diesel meets modern performance standards.
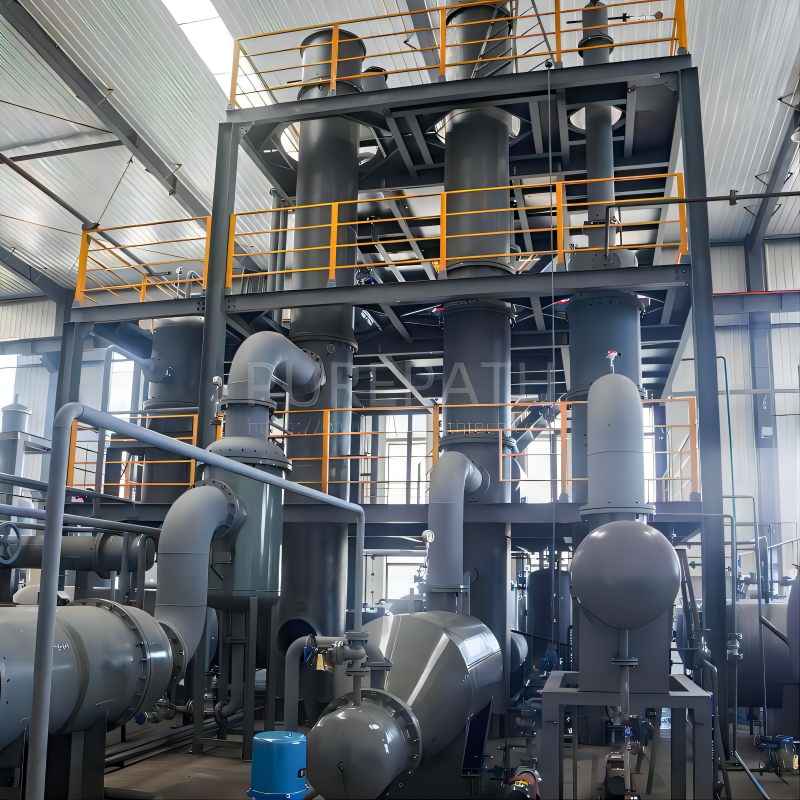
Applications of Diesel Produced from Used Engine Oil
Diesel produced from used engine oil can be used in various applications:
- Industrial Boilers: Due to its lower cetane number, it is often used in industrial boilers where ignition quality is less critical.
- Large Vehicles: Some large vehicles, such as trucks and buses, can use blends of conventional diesel and diesel from used engine oil.
- Small-scale Power Generation: It can be used in small-scale power generation units.
- Marine Applications: In some regions, it is used in marine applications.
Limitations and Future Directions
While the conversion of waste oil into diesel fuel offers many benefits, there are still challenges to overcome. These include:
- Feedstock Variability: The composition of waste oil can vary widely, making it difficult to optimize the process.
- Catalyst Deactivation: Catalysts can become deactivated over time due to coke formation and poisoning.
- Environmental Regulations: Stringent environmental regulations can increase the cost of the process.
Future research is focused on developing more efficient and sustainable processes, as well as expanding the range of feedstocks that can be converted into diesel fuel.

Final Thoughts
The conversion of used engine oil to diesel fuel represents a significant opportunity to address environmental concerns and create a more sustainable future. While there are still challenges to be overcome, ongoing research and development efforts are paving the way for the commercialization of this technology. By transforming waste into a valuable resource, we can reduce our reliance on fossil fuels and minimize the environmental impact of our transportation systems.