Thin Film Evaporator
Professional R&D design, Customizable
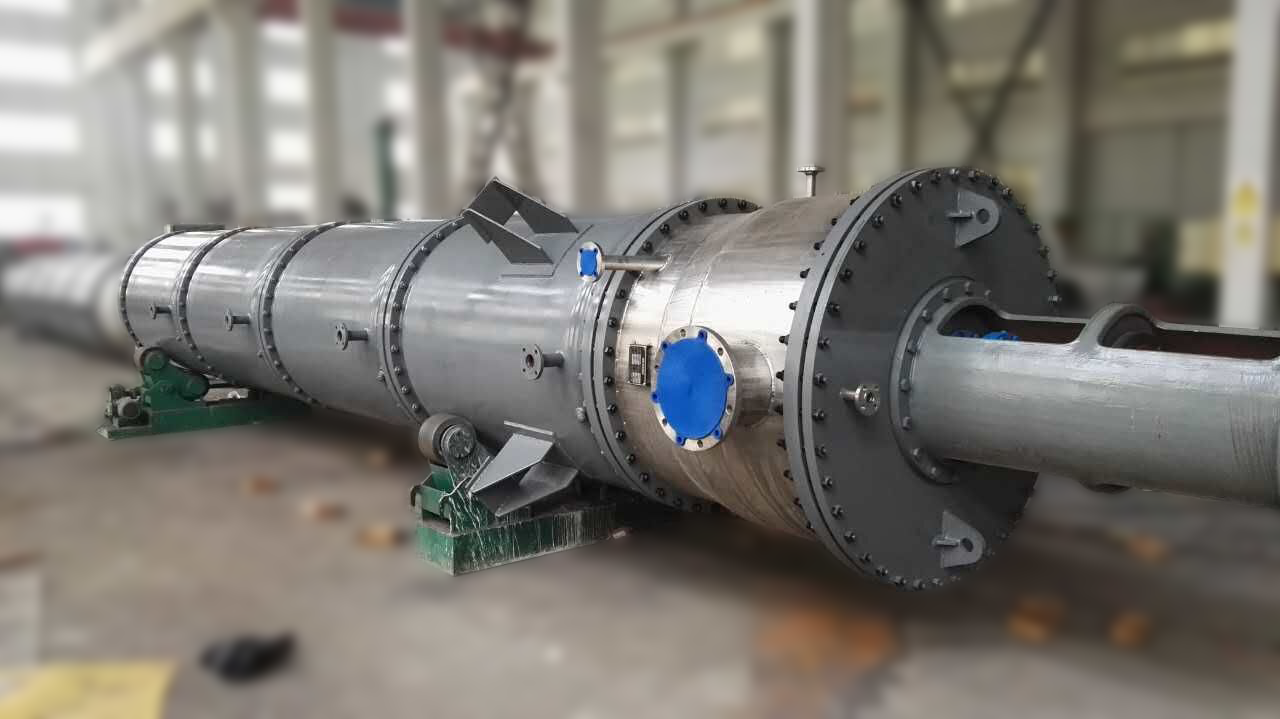
Wiped Film Evaporator (WFE) for Advanced Petrochemical Processing
1. Overview of Wiped Film Evaporator
The Wiped Film Evaporator (WFE) consists primarily of a heating jacket and a set of rotating blades. The heating jacket is supplied with steam, and the blades are mounted on a rotating shaft, maintaining a small gap, usually between 0.5 to 1.5 mm, between the blades and the inner wall of the heating jacket. After preheating, the feed liquid is introduced tangentially at the top of the evaporator. Under the influence of gravity and the rotating blades, the liquid forms a thin film on the inner wall, which descends and is continuously evaporated and concentrated. The concentrated liquid exits at the bottom, while the secondary steam escapes from the top. In some cases, this evaporator can dry the solution, producing a solid product directly at the bottom.
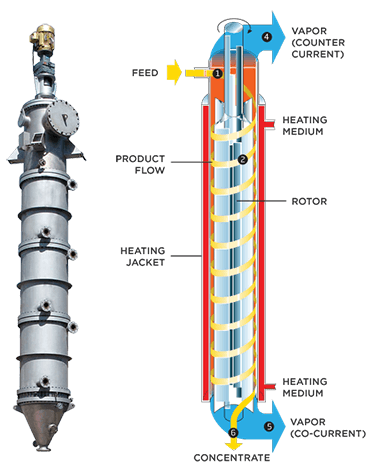
2. Performance and Features of Wiped Film Evaporator
The WFE uses a centrifugal sliding groove rotor, which is a new structural design found in advanced evaporators. Even under low flow conditions, it can form a thin film. The build-up of deposits on the evaporator’s inner wall can be quickly removed by the rotating blades. Compared to fixed gap blade evaporators, the evaporation rate can be increased by 40-69%. The following are the key features and performance characteristics of this equipment:
- Low Vacuum Pressure Drop: The WFE is designed with a larger gas passage space, which allows the pressure inside the evaporator to be nearly equal to the pressure in the external condenser. This results in a minimal pressure drop, as low as 5 mmHg, ensuring stable operation and reducing energy consumption.
- Low Operating Temperature: Operating under high vacuum conditions allows the WFE to lower the boiling point of materials, enabling the evaporation process to occur at lower temperatures. This is especially advantageous for heat-sensitive materials, preventing degradation or decomposition and preserving product quality.
- Short Heating Time: Thanks to its unique design, the WFE ensures extremely short residence times for the material, typically between 5 to 10 seconds. The wiping blades not only accelerate the material but also prevent it from staying too long on the heating surface, reducing thermal exposure and protecting sensitive compounds.
- High Evaporation Intensity: By increasing the temperature difference between the heating medium and the material, the WFE significantly enhances evaporation intensity. The wiping action reduces the liquid film thickness, minimizing thermal resistance and improving heat transfer. This leads to higher evaporation rates and more efficient processing.
- High Operational Flexibility: The WFE is highly versatile, capable of processing materials with varying viscosities, from low to high-viscosity substances. The evaporator is also capable of handling materials whose viscosity increases as their concentration rises, offering great flexibility for a wide range of applications.
- Efficient and Consistent Performance: The WFE provides consistent, stable evaporation even under varying feed conditions. The system’s ability to handle both heat-sensitive and high-viscosity materials makes it an ideal choice for a variety of challenging evaporation applications.
- Space-Saving and Easy Maintenance: With its compact design, the WFE takes up minimal space while maintaining easy maintenance and cleaning. The equipment’s simple structure also makes it easy to operate and adjust, helping ensure smooth, continuous operation.
3. Working Principle of Wiped Film Evaporator
The material enters the evaporator radially from the top of the heating zone. It is then distributed onto the heating surface of the evaporator by a distributor. The rotating wiper blades continuously and evenly spread the material into a thin, uniform liquid film on the heating surface, and propel it downward in a spiral motion. During this process, the rotating wiper blades ensure the continuous and uniform formation of the liquid film, generating high-speed turbulence and preventing the liquid film from fouling on the heating surface, thereby improving the overall heat transfer coefficient. The light components are evaporated and form a steam flow that rises and passes through a vapor-liquid separator, reaching the external condenser connected directly to the evaporator. The heavy components are discharged from the evaporator.
A unique distributor not only evenly spreads the material onto the inner walls of the evaporator, preventing splashing of material into the steam flow, but also prevents flash evaporation at the entry point. This helps eliminate foam and ensures that the material evaporates only along the heating surface.
At the upper part of the wiper evaporator, a centrifugal separator is installed, designed according to the material’s properties. This separator removes droplets from the rising steam flow and returns them to the distributor.
4. Ideal Applications of Wiped Film Evaporators
These combined advantages make the WFE especially well-suited for use in:
- Petrochemical processing: For refining oils and solvents.
- Food and beverage industries: For evaporating delicate, heat-sensitive products.
- Pharmaceutical and chemical manufacturing: For handling viscous or thermally sensitive materials.
- Environmental and waste processing: For efficient separation and purification processes.
With its exceptional performance, energy efficiency, and operational flexibility, the Wiped Film Evaporator is a crucial piece of equipment in many high-demand industrial applications. It ensures that materials are processed effectively, maintaining quality while reducing energy and operational costs.
Parameters | Type 1 | Type 2 | Type 3 | Type 4 | Type 5 | Type 6 | Type 7 |
Trans surface (㎡) | 1 | 2 | 4 | 6 | 10 | 12 | 20 |
Vapor pressure (Mpa) | 0.3 | ||||||
Vacuum (Mpa) | -0.08 | ||||||
Evaporating capacity (kg/h) | 100 | 200 | 300 | 600 | 1000 | 1200 | 2000 |
Steam consumption (kg/h) | 110 | 220 | 330 | 660 | 1100 | 1300 | 2200 |
B.H.P (kW) | 1.5 | 3 | 4 | 5.5 | 11 | 11 | 15 |
Agitator speed (rpm) | 0-160 | 0-150 | 0-176 | 0-136 | 0-110 | 0-110 | 0-110 |
Height (mm) | 3100 | 4800 | 5680 | 6410 | 7200 | 7800 | 9850 |
Why Choose Our WFE?
Our Wiped Film Evaporators are engineered to provide superior performance in a range of industries, including petrochemical processing, oil refining, and solvent recovery. With years of expertise in the field, we are committed to offering cutting-edge technology that enhances efficiency, lowers energy costs, and improves overall production.
Contact Us
Interested in learning more about how the Wiped Film Evaporator (WFE) can optimize your operations? Contact us today to get detailed product specifications and pricing information. Our team is ready to provide tailored solutions to meet your unique processing needs.
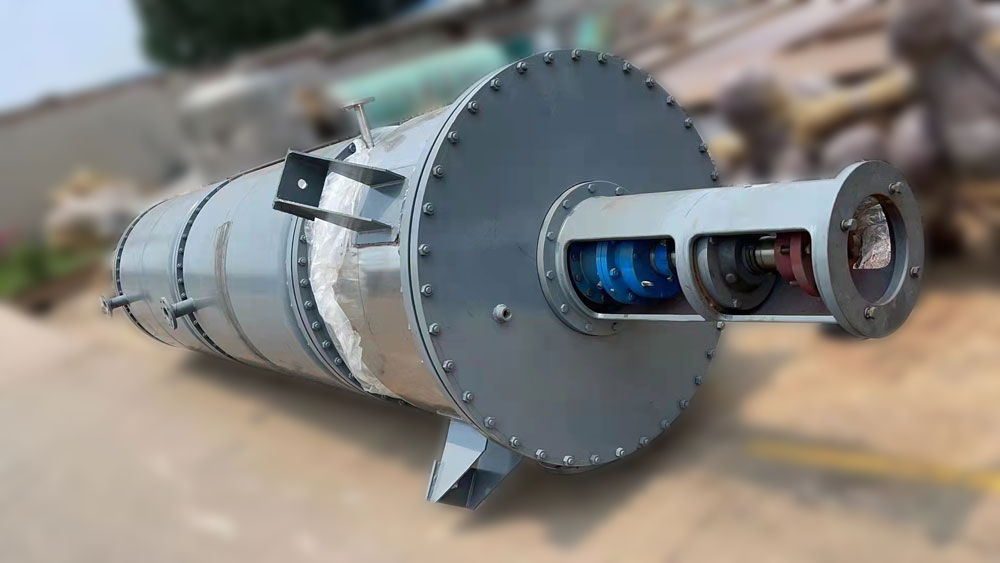
Short Path Evaporator: Advanced Solutions for Efficient Separation
Introduction to Short Path Evaporators
Short path evaporators (SPE) are cutting-edge equipment designed for the efficient separation and purification of heat-sensitive materials. This innovative technology leverages a high vacuum environment and a short path for vapor to travel, minimizing the thermal degradation of the product. Our state-of-the-art short path evaporators ensure optimal performance in a variety of applications, from pharmaceuticals to chemical processing.
How Short Path Evaporators Work
Short path evaporators operate by heating the feed material in a controlled manner, causing it to vaporize. The vapor travels a short distance to the condenser, where it is condensed back into a liquid. The short path reduces the residence time and exposure to high temperatures, preserving the integrity of the heat-sensitive compounds.
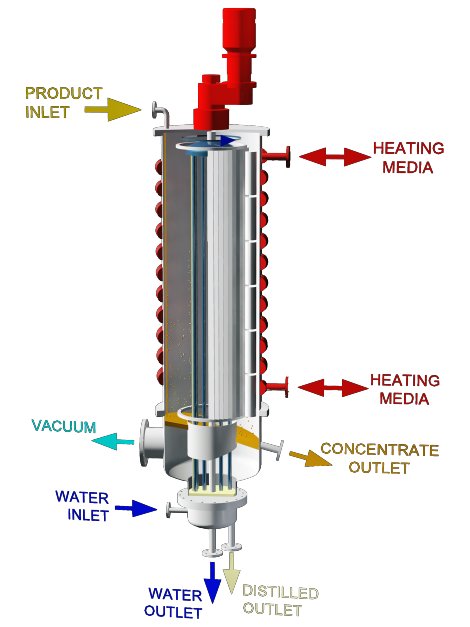
Key Features and Technical Specifications
- High Vacuum Environment: Achieves a vacuum as low as 0.001 mbar, enhancing separation efficiency and reducing the boiling point of substances.
- Short Path Distance: Minimizes thermal degradation by ensuring vapors travel only a short distance to the condenser.
- Efficient Heat Transfer: Optimized heat transfer surfaces for uniform heating and efficient evaporation.
- Compact Design: Space-saving design suitable for various industrial settings.
- Material Compatibility: Constructed with high-quality stainless steel and borosilicate glass to withstand corrosive substances and high temperatures.
Advantages of Short Path Evaporators
- Thermal Efficiency: The short path design significantly reduces the residence time, minimizing thermal decomposition of sensitive materials.
- High Purity: Achieves high purity levels through efficient separation, essential for pharmaceutical and chemical applications.
- Energy Saving: Low operating temperatures result in reduced energy consumption.
- Versatility: Suitable for a wide range of applications including distillation, purification, and concentration of high-value products.
- Scalability: Available in various sizes to accommodate small-scale laboratory research to large-scale industrial production.
Applications of Short Path Evaporators
- Pharmaceuticals: Ideal for the purification of active pharmaceutical ingredients (APIs) and intermediates.
- Essential Oils: Used in the extraction and purification of essential oils to preserve delicate fragrances and therapeutic properties.
- Chemical Industry: Efficiently separates high-boiling-point compounds and recovers solvents.
- Food and Beverage: Concentrates flavors and removes unwanted components without compromising quality.
- Cannabis Processing: Extracts and refines cannabinoids and terpenes while maintaining their potency and purity.
Why Choose Our Short Path Evaporators?
- Expertise and Experience: With years of experience in the industry, we offer unmatched expertise in evaporation technology.
- Quality Assurance: Our evaporators are built to the highest quality standards, ensuring reliability and longevity.
- Customer Support: Dedicated customer support team ready to assist with installation, operation, and maintenance.
- Customization: Tailor-made solutions to meet the specific needs of your process and industry requirements.
Contact Us
Ready to optimize your separation and purification processes with our advanced short path evaporators? Contact us today to learn more about our products and request a quote. Our team of experts is here to help you find the perfect solution for your application.
Call to Action
Don’t miss out on the opportunity to enhance your production efficiency and product quality. Reach out to us now and take the first step towards integrating the best short path evaporators in the market into your operations. Fill out our inquiry form below, and we’ll get back to you promptly with a customized solution.
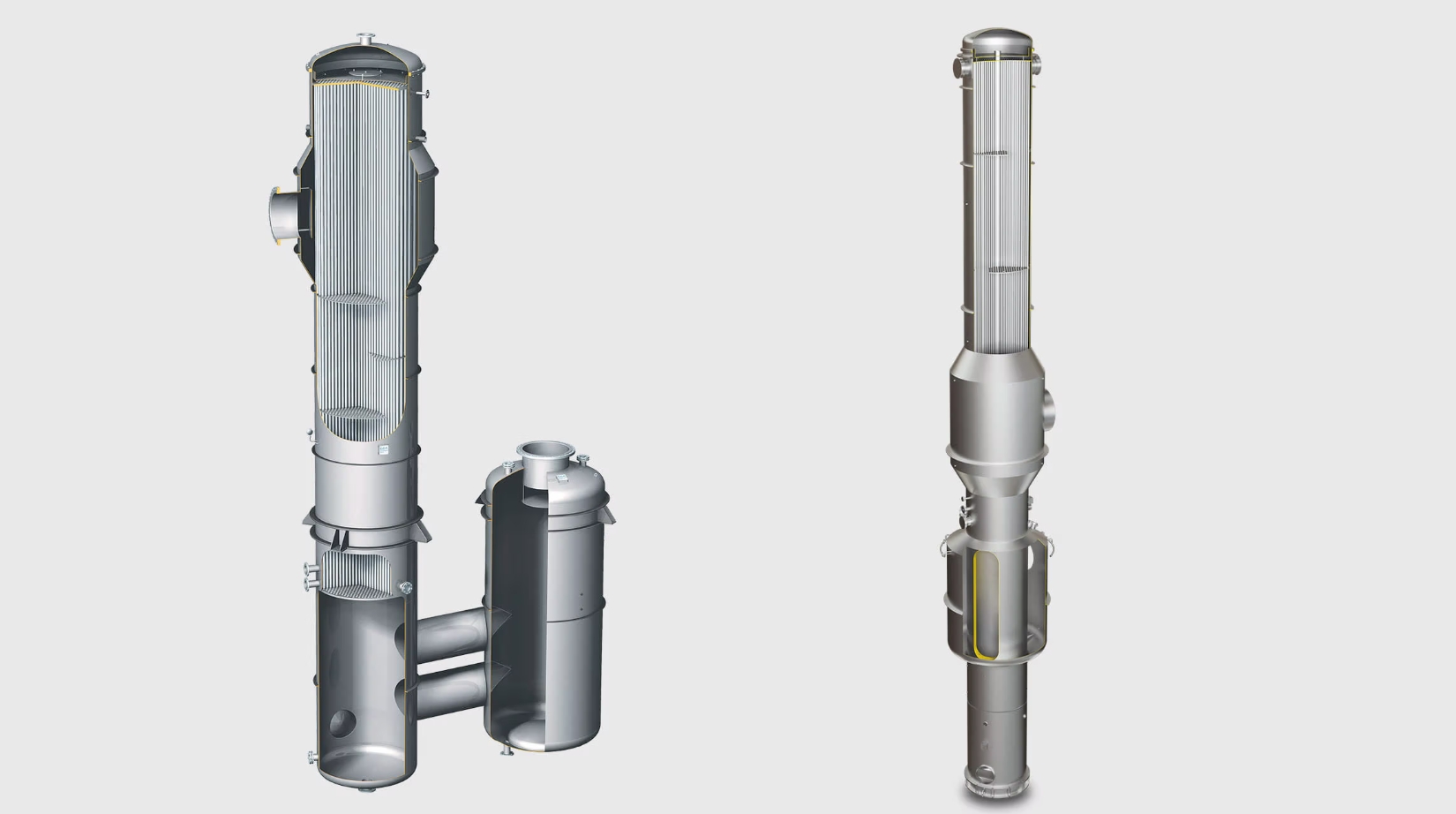
Falling Film Evaporator: Superior Technology for Efficient Evaporation
Introduction to Falling Film Evaporators
Falling film evaporators (FFE) are highly efficient heat exchangers designed for the evaporation and concentration of heat-sensitive and viscous liquids. These systems provide gentle processing conditions, making them ideal for a variety of industries, including food and beverage, pharmaceuticals, and chemicals. Our falling film evaporators are engineered to deliver exceptional performance and reliability, ensuring optimal operational efficiency.
How Falling Film Evaporators Work
In a falling film evaporator, the liquid to be concentrated is evenly distributed as a thin film along the inner surface of vertical tubes. As the liquid film flows downward by gravity, it is heated by steam or hot water on the outer surface of the tubes, causing the solvent to evaporate. The vapor is then separated from the concentrated liquid, which is collected at the bottom of the evaporator. This process allows for efficient heat transfer and minimal thermal degradation.
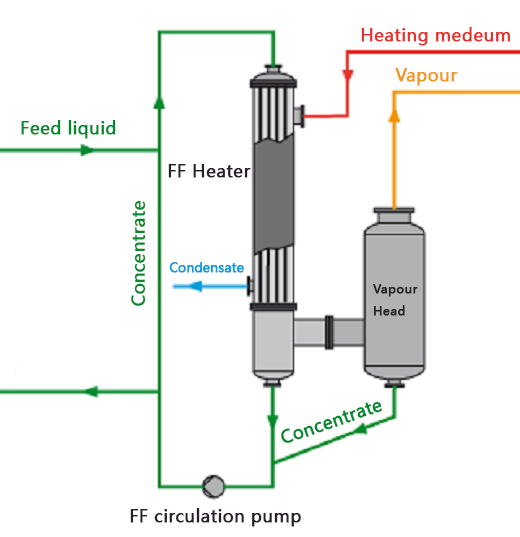
Key Features and Technical Specifications
- High Heat Transfer Efficiency: Optimized tube design and high heat transfer coefficients ensure rapid and uniform evaporation.
- Low Residence Time: Short residence time minimizes thermal exposure, preserving the quality of heat-sensitive materials.
- Flexible Operation: Capable of handling a wide range of feed viscosities and concentrations.
- Scalable Design: Modular construction allows for easy scalability from pilot plant to full-scale production.
- Material Compatibility: Built with corrosion-resistant materials such as stainless steel and special alloys to handle aggressive substances.
Advantages of Falling Film Evaporators
- Energy Efficiency: High heat transfer rates reduce energy consumption, lowering operational costs.
- Gentle Processing: Ideal for heat-sensitive products due to low temperature differentials and short residence times.
- Versatility: Suitable for a broad range of applications, including food processing, chemical production, and wastewater treatment.
- Operational Flexibility: Capable of continuous operation, improving throughput and process efficiency.
- Easy Maintenance: Simple design with easy access to components for cleaning and maintenance.
Applications of Falling Film Evaporators
- Food and Beverage: Concentration of fruit juices, dairy products, and other heat-sensitive liquids without compromising flavor and nutritional value.
- Pharmaceuticals: Concentration of active pharmaceutical ingredients (APIs) and intermediates while maintaining product integrity.
- Chemicals: Efficient evaporation and concentration of chemical solutions and solvents.
- Biofuels: Concentration of bioethanol and other biofuels for increased efficiency and purity.
- Wastewater Treatment: Reducing the volume of wastewater by concentrating the solids content for easier disposal or further processing.
Why Choose Our Falling Film Evaporators?
- Proven Expertise: Extensive experience in designing and manufacturing high-performance evaporators.
- Quality Manufacturing: Stringent quality control ensures each evaporator meets the highest standards of reliability and durability.
- Customer-Centric Approach: Tailored solutions to meet the specific needs of your application and process requirements.
- Comprehensive Support: From initial consultation to after-sales service, our team is dedicated to ensuring your success.
- Innovative Technology: Continuous innovation to enhance efficiency, reduce costs, and improve product quality.
Contact Us
Enhance your evaporation processes with our cutting-edge falling film evaporators. Contact us today to discuss your specific needs and request a detailed quote. Our expert team is ready to provide you with the best solution for your application.
Get a quote for Customizable Petrochemical Pressure Vessels
Invest in quality, invest in PurePath. We build robust and reliable petrochemical pressure vessels, reactors, and heat exchangers designed for long-term performance and minimal downtime. Our commitment to superior materials and precision manufacturing ensures your operations run smoothly and efficiently. Get in touch to learn more about our commitment to excellence.