Enhancing Used Oil Recycling: Decolorization and Deodorization in the Refining Process
The increasing demand for sustainable practices in energy and resource management has elevated the importance of refining used motor oil and other waste oils. Used oils, such as spent lubricants, hydraulic oils, transformer oils, and even cooking grease, represent a significant resource for re-refining into valuable products like base oil, biodiesel, and industrial lubricants. One of the most critical aspects of the used oil refining process is the decolorization and deodorization stage, which determines the appearance, odor, and overall quality of the final product. This article explores in detail the techniques employed in these stages, the role of the used oil refining machine, and the factors influencing method selection and optimization.
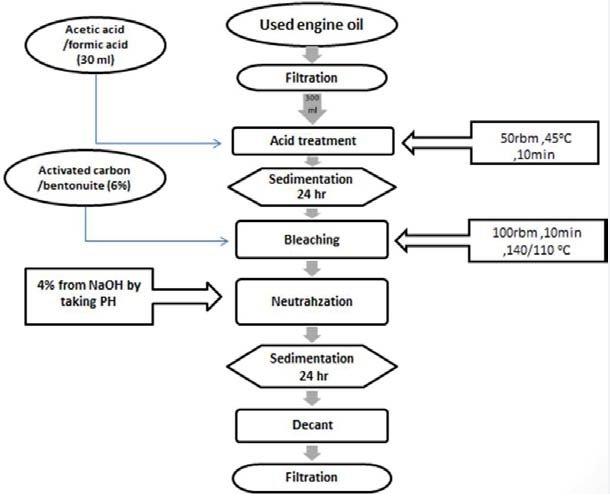
The Significance of Used Oil Refining
Used oil contains a complex mixture of contaminants, including heavy metals, water, oxidized hydrocarbons, and degraded additives. If improperly handled, it poses severe environmental and health hazards, polluting soil, water, and air. However, with proper treatment using a used oil refining machine, these waste oils can be transformed into clean, reusable base oils or alternative fuels, significantly contributing to circular economy initiatives and reducing dependence on virgin crude oil.
The used oil refining process typically involves several stages: pretreatment (such as dewatering and demetallization), chemical or thermal cracking (depending on the type of oil), decolorization, deodorization, distillation, and final polishing. Among these, decolorization and deodorization play crucial roles in improving the aesthetic and sensory qualities of the oil, rendering it fit for reuse in sensitive applications such as industrial lubricants or fuel additives.
Purpose and Importance of Decolorization and Deodorization
1. Decolorization
Decolorization aims to remove the dark coloration caused by oxidized hydrocarbons, metallic soaps, pigments, and other polar compounds. These colored bodies not only make the oil visually unappealing but may also impact its chemical stability and performance. Removal of these compounds is necessary to meet regulatory and consumer quality expectations.
2. Deodorization
Used oil typically contains a variety of odorous substances such as aldehydes, ketones, fatty acids, and sulfur compounds. These arise from the breakdown of base oil molecules or contamination from external sources. Effective deodorization is critical for the acceptability of refined oils, particularly when they are reused in environments where smell is a concern, such as indoor machinery or automotive fluids.
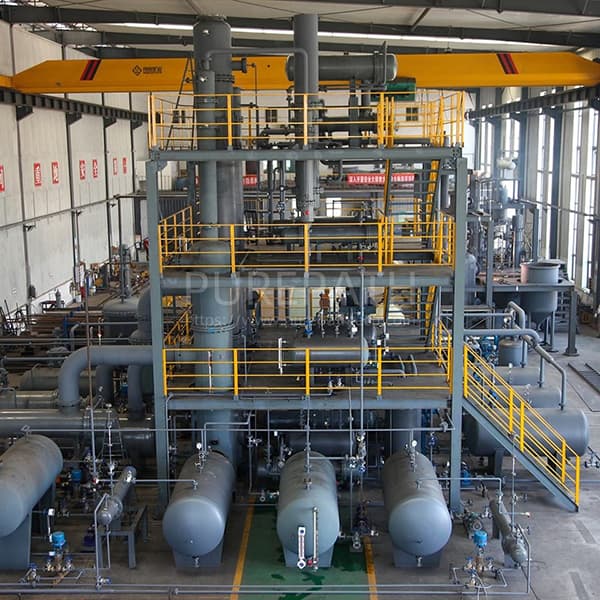
Common Methods for Decolorization in Used Oil Refining
1. Adsorption Decolorization
This is the most widespread method, owing to its simplicity and cost-efficiency. It uses adsorbent materials to trap and remove color-causing compounds from the oil.
- Activated Clay (Fuller’s Earth or Bleaching Clay): Activated clay is widely used due to its high surface area and strong polar affinity. It effectively removes metal soaps, pigments, and polymers from oil. In a typical used oil refining machine, activated clay is mixed with heated oil and stirred to allow for adsorption before being separated through filtration.
- Activated Carbon: With its highly porous structure, activated carbon is excellent at removing both color and some odor molecules. It is particularly suitable for oils requiring a high degree of purification, though it is more expensive than bleaching earth and may result in oil losses due to strong adsorption.
- Diatomaceous Earth: While not a strong adsorbent by itself, diatomaceous earth is often used as a filtration aid. It enhances the efficiency of the filtration process by preventing filter clogging and allowing for more uniform flow during the separation of adsorbents.
- Advanced Adsorbents: Emerging materials such as molecular sieves and modified zeolites show promising capabilities for selective removal of specific contaminants. Though not yet widely adopted due to cost or scale limitations, these could revolutionize the future of refining used motor oil.
2. Chemical Decolorization
Chemical methods involve modifying the structure of color bodies to render them colorless or easier to adsorb.
- Acid Washing: Acids such as sulfuric or phosphoric acid react with polar contaminants to break them down. Acid washing is often used as a pre-treatment to adsorption. However, it requires careful handling due to corrosion risks and the need for neutralization steps.
- Oxidative Bleaching: Strong oxidizers like hydrogen peroxide can decompose color bodies. While effective, these methods are seldom used in modern refining due to the potential introduction of new contaminants and higher operational costs.
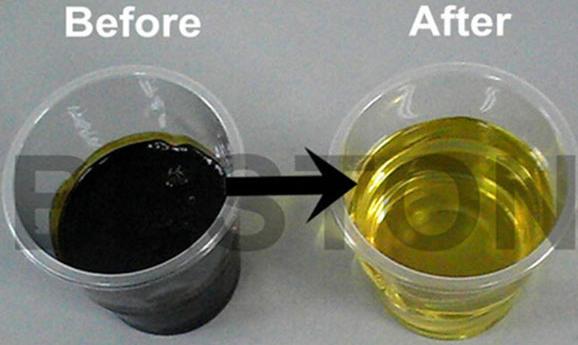
Deodorization Techniques in the Used Oil Refining Process
1. Steam Stripping (Vacuum Deodorization)
One of the most effective deodorization techniques, steam stripping involves introducing superheated steam into the oil under high vacuum conditions (typically below 5 mmHg). This lowers the boiling points of volatile odor-causing compounds, allowing them to vaporize and be removed from the oil.
In a high-performance used oil refining machine, steam stripping is conducted in a distillation tower equipped with trays or packing materials to enhance contact between oil and steam. The process is energy-intensive but ensures thorough removal of light fractions and unpleasant odors.
2. Activated Carbon Deodorization
Activated carbon is used not just for color removal but also for absorbing volatile organic compounds responsible for odor. It is often employed as a polishing step after steam stripping to ensure complete deodorization. This method is particularly useful for removing sulfur- and nitrogen-based compounds that are difficult to strip through distillation alone.
3. Molecular Distillation
This high-vacuum, low-temperature distillation technique leverages the difference in molecular weight and vapor pressure of oil constituents. It allows for the selective removal of volatile odor compounds without degrading the base oil. Though expensive, molecular distillation is gaining popularity in premium-grade used oil refining machines, especially those targeting high-end base oil production.
4. Use of Deodorants or Neutralizing Agents
Some processes may involve the addition of masking agents or chemical neutralizers. These compounds either chemically bind odor molecules or mask them with more pleasant scents. While effective in short-term applications, they are not a substitute for physical removal and may not be acceptable for high-specification industrial products.
Integrating Application of Decolorization and Deodorization in Used Oil Refining
In practical used oil refining processes utilizing a used oil refining machine, decolorization and deodorization are often closely linked. Decolorization creates favorable conditions for deodorization, as removing colored impurities can reduce potential side reactions during the subsequent deodorization stage. The selection and combination of different decolorization and deodorization methods are flexible, depending on the nature of the used oil and the requirements of the final product. For instance, the refining of cooking oil typically involves pretreatment to remove solid impurities, followed by activated clay adsorption for decolorization, and finally high-temperature vacuum steam stripping for deodorization. Industrial used oils may necessitate more complex pretreatment and decolorization processes, combined with steam stripping or molecular distillation for thorough deodorization.
Selecting appropriate decolorization and deodorization methods requires careful consideration of the following key factors:
- Initial quality and impurity characteristics of the used oil: Used oils from different sources vary significantly in their impurity types and concentrations, necessitating tailored treatment approaches.
- Quality requirements and intended use of the final product: Different applications have varying specifications for oil color, odor, purity, and other parameters.
- Processing costs and economic feasibility: The chosen treatment process should be economically viable while ensuring the desired product quality.
- Environmental regulations and sustainability considerations: Compliance with relevant environmental regulations and the adoption of environmentally friendly treatment technologies to minimize secondary pollution are essential.
- Operational safety and feasibility: The process flow should be safe, reliable, and easy to operate and control within the used oil refining machine.
Continuous advancements in technology are driving optimization and innovation in the field of used oil refining. For example, the development of novel high-efficiency adsorbents, the exploration of membrane separation technology for decolorization and deodorization, and the introduction of supercritical fluid extraction techniques offer new avenues for enhancing used oil refining efficiency, reducing energy consumption, and minimizing environmental impact.
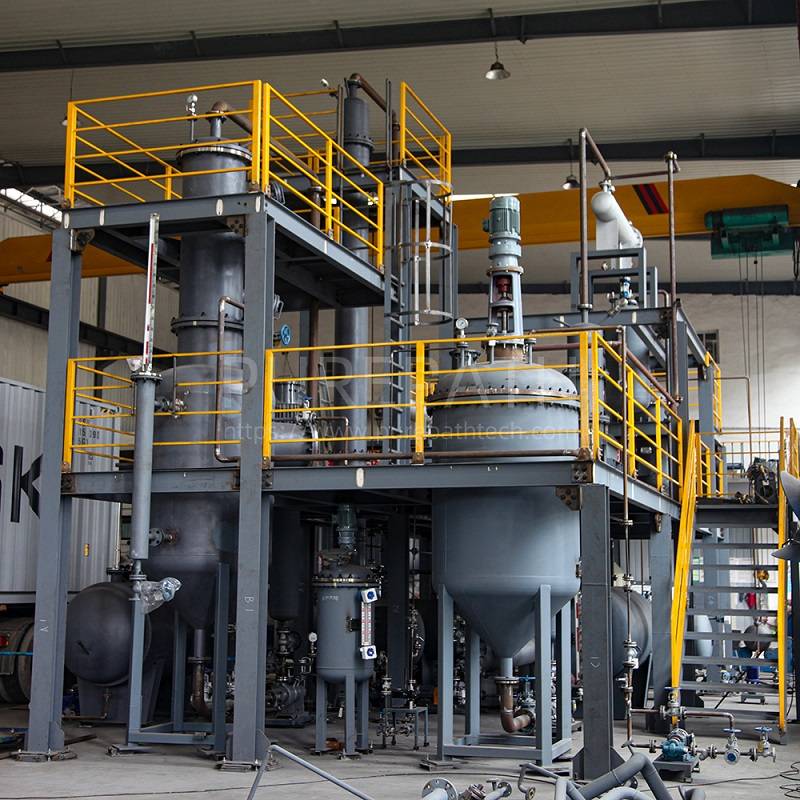
Conclusion
Decolorization and deodorization are essential processes in refining used motor oil and other waste oils. By removing unwanted color and odor, these steps significantly enhance the quality and marketability of the recycled products. Adsorption and steam stripping remain the mainstay methods, with advanced techniques like molecular distillation offering additional refinement for premium applications. As technology evolves, the used oil refining process will continue to become more efficient, environmentally friendly, and economically viable, paving the way for broader adoption and higher-value recycling of this critical resource.