Equipment Used in Petrochemical Refineries
Petrochemical refineries are sophisticated complexes where raw materials such as crude oil and natural gas are converted into a wide array of valuable products, including fuels, plastics, and chemicals. The efficiency, safety, and profitability of these operations hinge on the use of specialized equipment. This article delves into the key equipment used in petrochemical refineries, their roles, and their contributions to refinery efficiency.
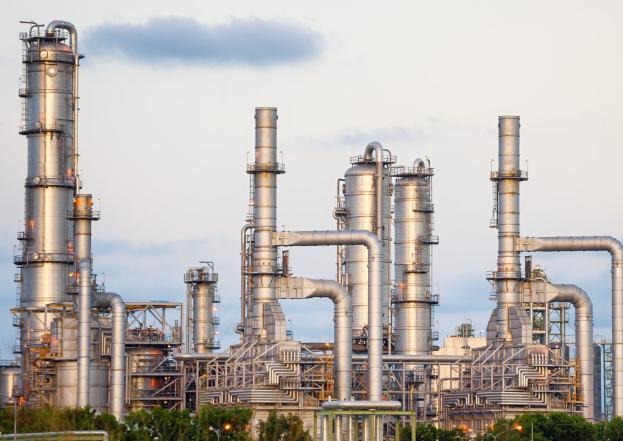
Key Equipment in Petrochemical Refineries
Distillation Columns
Distillation columns are crucial in petrochemical refineries, serving as the primary method for separating mixtures into individual components based on their boiling points. This separation process is essential for extracting various valuable products such as gasoline, diesel, and jet fuel from crude oil. The columns operate by heating the crude oil, causing it to vaporize and then condense at different levels within the column, depending on the boiling points of the components.
Types of Distillation Columns:
- Atmospheric Distillation Columns: These are used for the initial separation of crude oil at atmospheric pressure. They handle the bulk separation of lighter components.
- Vacuum Distillation Columns: These columns operate under reduced pressure to allow for the distillation of heavier fractions that cannot be distilled at atmospheric pressure without decomposing. This method is crucial for processing heavy residues and maximizing yield from crude oil.
Distillation columns are indispensable for refining crude oil into various usable products, making them a backbone of petrochemical refineries.
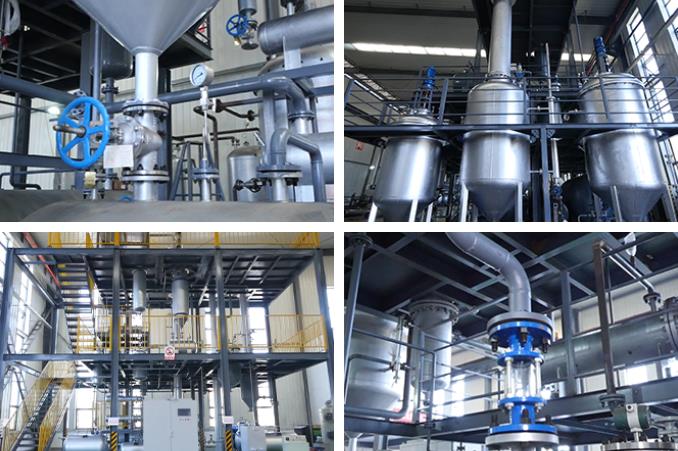
Heat Exchangers
Heat exchangers are crucial in petrochemical refineries for transferring heat between fluids, which is vital for energy conservation and process efficiency. They preheat crude oil before it enters distillation columns and cool down processed products, making the refining process more efficient and cost-effective.
Types of Heat Exchangers:
- Shell and Tube Heat Exchangers: These consist of a series of tubes, with one set carrying hot fluid and the other cold fluid. This design facilitates efficient heat transfer and is commonly used due to its robustness and versatility.
- Plate Heat Exchangers: Made up of multiple thin plates that create channels for the fluids, these exchangers are highly efficient in transferring heat due to their large surface area. They are compact and easy to clean, making them suitable for various refinery applications.
By efficiently managing heat transfer, heat exchangers play a pivotal role in reducing energy consumption, lowering operational costs, and improving the overall sustainability of refinery operations.
Reactors
Reactors are essential vessels in petrochemical refineries where chemical reactions occur to transform raw hydrocarbons into more valuable products. They facilitate processes such as catalytic cracking, reforming, and hydrocracking. These processes break down complex, heavy hydrocarbons into simpler, lighter molecules, increasing the yield of desirable products like gasoline, kerosene, and diesel.
Types of Reactors:
- Fixed-Bed Reactors: These contain a stationary catalyst through which reactants flow. They are widely used for their simplicity and effectiveness in processes like hydrocracking and reforming.
- Fluidized-Bed Reactors: In these reactors, catalysts are suspended in the reactant flow, enhancing contact and improving reaction rates. This design is particularly effective for catalytic cracking, where it allows for better mixing and more efficient conversion of heavy hydrocarbons.
The choice of reactor type depends on the specific chemical processes and desired products, making reactors a critical component for optimizing refinery performance and product quality.
Compressors and Pumps
Compressors and pumps are indispensable for ensuring the continuous flow of gases and liquids throughout the refinery’s intricate piping network. They play a crucial role in maintaining the necessary pressure and flow rates for various processing stages.
Types of Compressors and Pumps:
- Centrifugal Pumps: Employ rotational kinetic energy to move liquids, known for their efficiency and durability.
- Reciprocating Compressors: Utilize a piston mechanism to increase gas pressure, ideal for applications requiring high pressure and low flow rates.
These devices ensure smooth operation and are vital for the consistent delivery of materials between different units within the refinery.
Furnaces and Boilers
Furnaces and boilers are critical in providing the heat required for various refinery processes. Furnaces are used to heat raw materials to the necessary temperatures for further processing, while boilers generate steam used in different operations throughout the refinery.
- Direct-Fired Furnaces: These burn fuel directly to produce heat, which is transferred to the process stream.
- Indirect-Fired Furnaces: Heat is generated by burning fuel and then transferred via a heat exchanger, ensuring the process stream does not come into direct contact with combustion gases.
By ensuring efficient heat generation and transfer, furnaces, and boilers play a key role in the overall efficiency and safety of refinery operations.
Storage Tanks
Storage tanks are essential for holding raw materials, intermediate products, and finished goods within petrochemical refineries. These tanks are crucial for managing inventory, ensuring a steady supply for processing, and safely storing products before distribution.
Types of Storage Tanks:
- Floating Roof Tanks: Designed with a roof that rises and falls with the liquid level, minimizing vapor loss and reducing the risk of explosion.
- Fixed Roof Tanks: Feature a permanent roof, ideal for storing stable, non-volatile liquids.
Proper storage tank management is vital for operational efficiency, safety, and environmental protection in refinery operations.
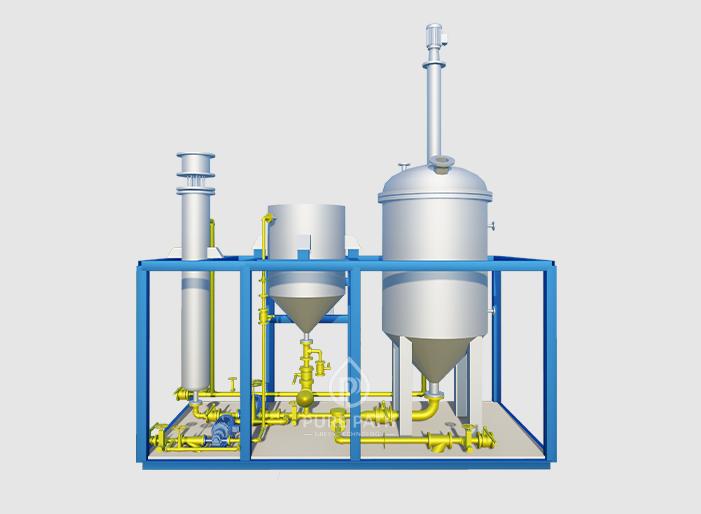
Valves and Instrumentation
Valves and instrumentation are critical for controlling and monitoring fluid flow and process conditions within a refinery. Valves regulate the movement of liquids and gases, ensuring precise control over various processes. They are essential for maintaining the operational integrity and efficiency of the refinery by enabling the management of flow rates and pressures throughout the system.
Instrumentation provides essential data on parameters such as temperature, pressure, and flow rates, enabling real-time monitoring and adjustments. This data is crucial for optimizing process conditions, ensuring safety, and preventing potential issues before they escalate. Types of valves used in refineries include gate valves, primarily for on/off control with minimal resistance when fully open, and globe valves, designed for precise flow regulation. Instrumentation typically includes temperature sensors to track and manage process temperatures and pressure transmitters to measure and relay pressure information.
The Role of Equipment in Refinery Efficiency
The efficiency of a petrochemical refinery is intricately tied to the performance of its equipment. These machines are the backbone of the operation, converting raw crude oil into a multitude of valuable products. The equipment’s condition, capacity, and technological advancement directly impact the refinery’s overall productivity, energy consumption, and environmental footprint.
Optimizing equipment performance is crucial for maximizing refinery efficiency. This involves a combination of factors, including:
- Regular Maintenance and Inspection: Proactive maintenance schedules and thorough inspections help prevent equipment failures, reduce downtime, and extend the lifespan of machinery.
- Advanced Analytics: Employing data analytics to monitor equipment performance in real-time allows for early detection of anomalies, predictive maintenance, and optimized operations.
- Energy Efficiency: Upgrading equipment with energy-efficient technologies can significantly reduce energy consumption, leading to lower operating costs and a smaller environmental impact.
- Process Optimization: Continuously refining processes and optimizing equipment configurations can improve product yield, reduce waste, and enhance overall efficiency.
- Automation and Control: Implementing advanced automation systems can enhance precision, consistency, and safety while reducing labor costs.
Beyond operational efficiency, the equipment used in refineries also influences product quality. For instance, the design and materials of distillation columns impact the purity of the separated fractions, while the catalysts in reactors determine the product composition.
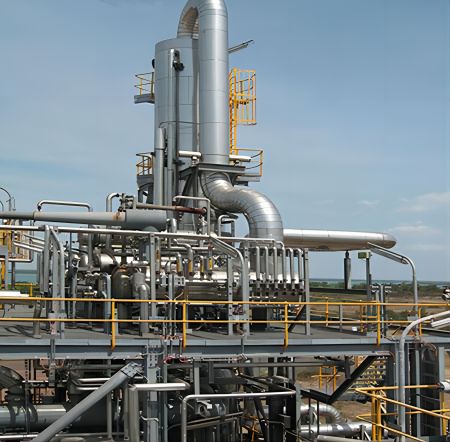
Purepath: Leading Engineering Solutions for Customized Petrochemical Projects
Purepath is a leading engineering firm specializing in the design and execution of customized petrochemical projects. With a strong focus on innovation and precision, Purepath offers a comprehensive suite of services including distillation, extraction, desulfurization, and more. Our team of seasoned engineers and technical experts collaborates closely with clients to develop tailored solutions that optimize efficiency, enhance safety, and drive sustainable growth in the petrochemical industry. At Purepath, we are committed to delivering excellence through cutting-edge technology and unparalleled expertise, ensuring each project meets the highest standards of quality and performance.