Exploring the Visbreaking Process in Petroleum Refineries
The visbreaking process is a cornerstone technology in modern petroleum refineries, playing a vital role in the conversion of heavy, high-viscosity oils into lighter, more marketable products. This thermal cracking technique reduces the viscosity of heavy oils, such as vacuum residues, improving their flowability and making them suitable for use as fuel oils. Known for its cost-effectiveness and operational simplicity, visbreaking has become an indispensable tool for refining operations worldwide.
In this article, we delve into the intricacies of the visbreaking process, focusing on its objectives, operational principles, various technological approaches such as the coil visbreaking process and soaker visbreaking process, and its environmental impacts.
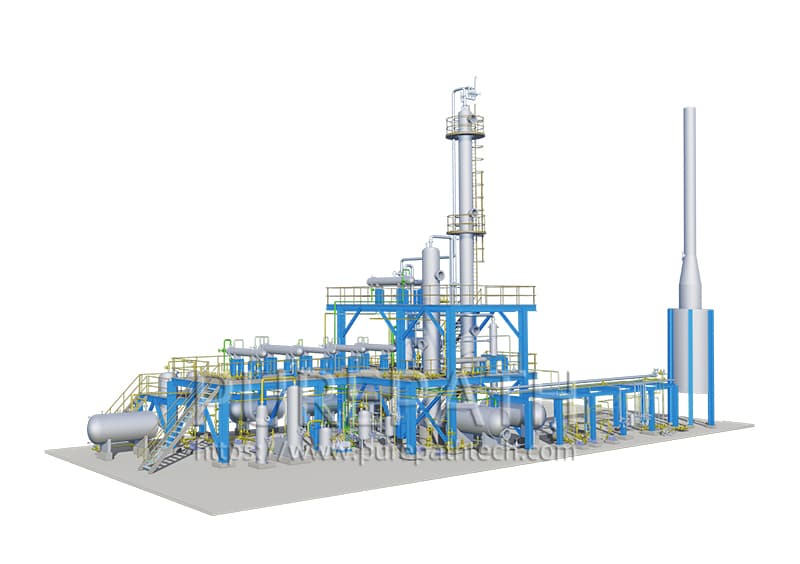
What is Visbreaking?
Visbreaking, short for viscosity breaking, is a thermal processing technique applied in petroleum refineries. Its primary goal is to reduce the viscosity and pour point of heavy oil residues, such as vacuum residue, by subjecting them to mild thermal cracking. This transformation makes these residues suitable for blending into lower-viscosity fuel oils.
Visbreaking is a preferred choice for many refineries because of its low capital investment, straightforward operation, and capability to process heavy residues economically. The process can effectively reduce viscosity while maintaining an acceptable yield of lighter fractions such as diesel and gasoline. Furthermore, the technique ensures that fuel oils meet market specifications without extensive blending, making it indispensable for fuel oil production.
Objectives of the Visbreaking Process
The visbreaking process serves two primary objectives in a petroleum refinery:
1. Viscosity Reduction
Heavy oils, such as vacuum residue, often exhibit high viscosity, making them challenging to handle and process. Visbreaking reduces viscosity significantly, allowing these oils to meet the specifications required for fuel oil production. By improving flowability and reducing the pour point, the process enhances the usability of heavy oils.
2. Maximizing Distillate Production
In addition to reducing viscosity, the process aims to maximize the production of lighter fractions like diesel and gasoline. While not always achieving standalone fuel specifications, these lighter products can be blended to improve the overall quality of refinery outputs.
The dual benefits of viscosity reduction and distillate maximization highlight the economic and operational importance of visbreaking, especially in refineries handling large quantities of heavy feedstocks.
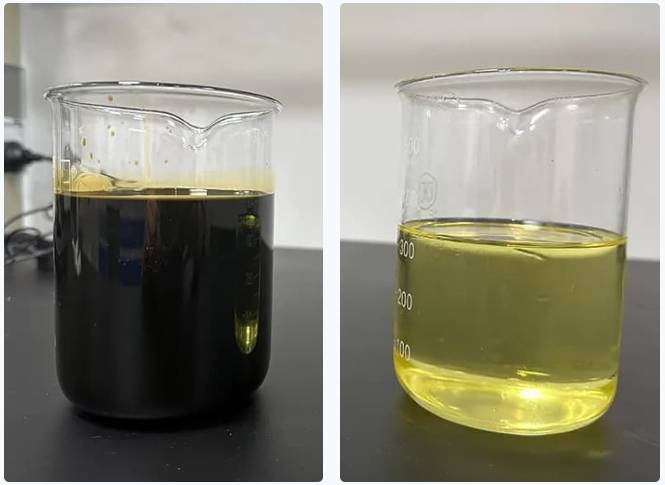
Principles of the Visbreaking Process
The visbreaking process involves complex thermal and chemical reactions that break down heavy hydrocarbons into lighter molecules. The primary principles include:
- Thermal Cracking: At the heart of visbreaking lies the thermal cracking reaction. Under high temperatures (400–450°C), long-chain hydrocarbons in the feedstock break into smaller, lighter molecules. The process is carefully controlled to avoid excessive cracking, which could lead to undesirable by-products like coke.
- Side Chain Cleavage: Hydrocarbons with long side chains are particularly susceptible to cleavage during visbreaking. Breaking these side chains significantly reduces the overall viscosity of the oil.
- Aromatic Ring Opening: Under high temperatures, aromatic compounds may undergo ring-opening reactions, contributing further to the reduction of molecular size and viscosity.
The operating conditions are finely tuned to balance the extent of cracking, ensuring optimal product distribution without compromising equipment integrity or operational stability.
Process Flow of Visbreaking Unit
The typical visbreaking unit process can be broken down into five key stages:
- Pre-heating and Heating: The feedstock, usually vacuum residue, is first pre-heated using heat exchangers. This step optimizes energy usage by recovering heat from the process’s hot streams. The pre-heated feed is then directed to a furnace, where it is heated to 400–450°C. To prevent coke formation inside the furnace tubes, approximately 1% water is injected, ensuring smooth operation.
- Reaction Phase: The heated feed enters the visbreaking unit’s reaction chamber, where the thermal cracking occurs. Depending on the process design, the reaction may take place in furnace tubes (as in the coil visbreaking process) or be extended into a soaker drum (as in the soaker visbreaking process). The reaction conditions, including temperature, pressure, and residence time, are controlled to achieve the desired cracking intensity.
- Product Separation: After the reaction, the product mixture is sent to a flash tower or separator, where it is divided into gaseous, liquid, and residual fractions. The lighter hydrocarbons, including cracked gases, gasoline, and diesel, are recovered from the top, while the heavier visbroken residue is collected at the bottom.
- Cooling and Fractionation: The gaseous and lighter liquid products are further cooled and separated into distinct fractions. Some of the diesel may be recycled as quenching oil to cool the reactor output rapidly, minimizing further cracking.
- Product Output: The visbroken residue, a less viscous and more manageable fuel oil, constitutes the primary product. Additional outputs include unstabilized gasoline, diesel, and small amounts of cracked gases.
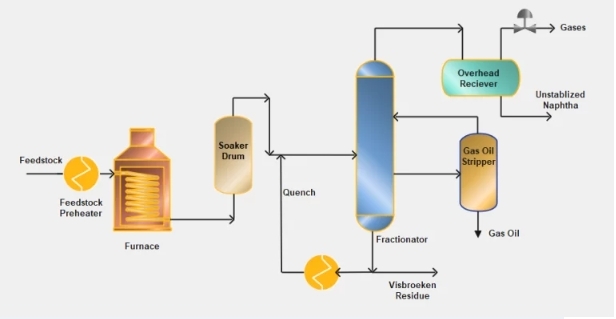
What Are the Types of Visbreaking Processes Technologies?
The visbreaking process can be classified into several variants based on the reactor design and operational methodology:
1. Coil Visbreaking Process
In this approach, the thermal cracking reaction occurs entirely within the furnace coils. The high-temperature and short-residence-time conditions ensure rapid cracking. This process is suitable for feedstocks requiring minimal cracking and offers high operational efficiency.
2. Soaker Visbreaking Process
The soaker visbreaking process extends the reaction time by incorporating a soaker drum downstream of the furnace. This allows the feedstock to undergo additional cracking at slightly lower temperatures, improving product yields and reducing furnace coking. It is particularly beneficial for refineries seeking a balance between light product recovery and equipment longevity.
3. Delayed Visbreaking
Here, the cracked feedstock is held in a tank or reactor for an extended period at lower temperatures. This allows for gentle cracking, minimizing coke formation while achieving significant viscosity reduction.
4. Hydrogen-assisted Visbreaking
In this advanced process, hydrogen is introduced to enhance the quality of lighter fractions and suppress coke formation. The added hydrogen reduces the formation of unsaturated hydrocarbons, improving product stability.
5. Hydrogen Donor Visbreaking
This process incorporates hydrogen donor compounds instead of gaseous hydrogen. These compounds release hydrogen during cracking, improving reaction outcomes without the operational challenges associated with hydrogen gas handling.
Environmental Impacts of the Visbreaking Process in Petroleum Refinery
While visbreaking offers significant economic benefits, it also poses environmental challenges:
- Greenhouse Gas Emissions: The process consumes large amounts of energy, typically derived from fossil fuels, leading to CO₂ emissions that contribute to climate change.
- Air Pollution: Gaseous emissions, including sulfur dioxide (SO₂), nitrogen oxides (NOₓ), and particulates, can harm air quality, causing acid rain and respiratory issues.
- Water Pollution: Wastewater generated during visbreaking contains hydrocarbons and other chemicals. Improper treatment can lead to contamination of water bodies.
- Solid Waste Generation: Coke and spent catalysts are among the solid wastes produced, requiring careful disposal to prevent soil and groundwater pollution.
- Noise Pollution: Equipment such as compressors and furnaces generates noise, which can impact worker health if not managed.
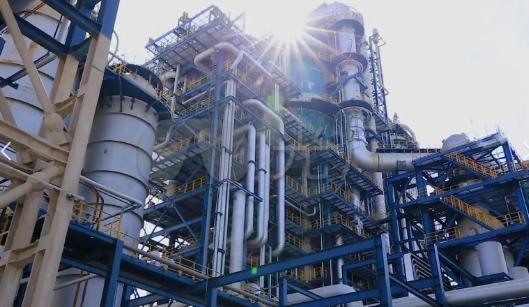
Strategies for Reducing Environmental Impacts in Visbreaking Process
Visbreaking, while a valuable process for upgrading heavy oils, can have significant environmental impacts. To minimize these, petroleum refineries employ a multi-pronged approach:
1. Advanced Emission Control Systems
Sulfur Dioxide (SO₂) Reduction:
- Flue Gas Desulfurization (FGD) Systems: These systems, such as wet scrubbers or dry sorbent injection, effectively remove SO₂ from the flue gas emitted by the visbreaker unit. This is crucial as SO₂ is a major contributor to acid rain and respiratory issues.
- Low-Sulfur Feedstocks: Utilizing feedstocks with inherently lower sulfur content significantly reduces the amount of SO₂ produced during the visbreaking process.
Nitrogen Oxides (NOₓ) Reduction:
- Low-NOₓ Burners: Employing burners designed to minimize the formation of NOₓ during combustion significantly reduces emissions.
- Selective Catalytic Reduction (SCR) Systems: These systems use catalysts to convert NOₓ into harmless nitrogen and water vapor.
2. Wastewater Treatment
- Dedicated Treatment Plants: Visbreaking processes generate various wastewater streams, including those containing hydrocarbons, suspended solids, and dissolved salts. Dedicated wastewater treatment plants are essential to:
- Remove pollutants: Processes like biological treatment, chemical precipitation, and filtration effectively remove contaminants from the wastewater before it is discharged into the environment.
- Recover valuable resources: Some treatment processes can recover valuable materials like oil and water from the wastewater for reuse within the refinery.
3. Energy Efficiency Measures
- Heat Recovery: Implementing heat exchangers to recover waste heat from the visbreaking process improves energy efficiency and reduces fuel consumption.
- Process Optimization: Continuous monitoring and optimization of process parameters, such as temperature and pressure, can minimize energy losses and maximize product yields.
- Improved Insulation: Proper insulation of equipment reduces heat loss and improves overall energy efficiency.
4. Feedstock Diversification and Blending
- Alternative Feedstocks: Utilizing alternative feedstocks, such as those with lower sulfur and higher API gravity, can reduce the environmental impact of the visbreaking process.
- Blending Strategies: Blending heavy feedstocks with lighter, lower-sulfur crudes can reduce the overall sulfur content of the feed to the visbreaker unit, minimizing SO₂ emissions.
5. Regular Maintenance and Inspections
- Equipment Upkeep: Regular maintenance and inspections of equipment, including furnaces, reactors, and heat exchangers, ensure optimal performance and minimize emissions and environmental risks.
- Leak Detection and Repair: Promptly identifying and repairing leaks in equipment and pipelines prevents the release of harmful substances into the environment.
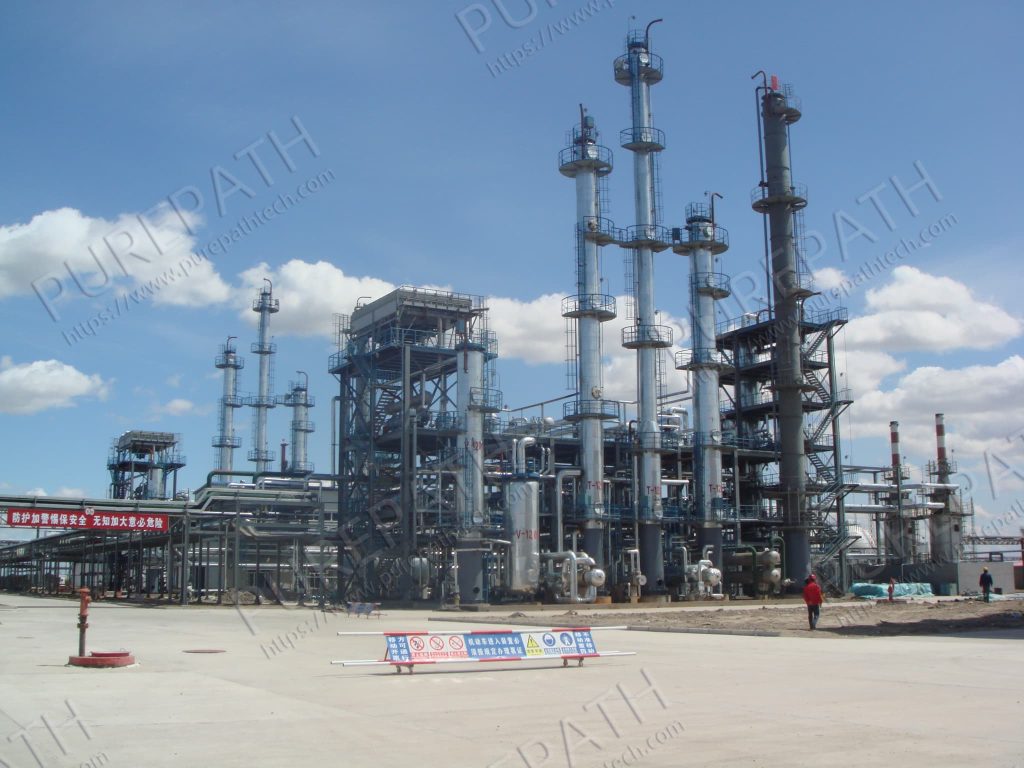
Final Thoughts
The visbreaking process remains an integral part of modern petroleum refining, offering a cost-effective and efficient method for processing heavy oils. By leveraging variations such as the coil visbreaking process and soaker visbreaking process, refineries can tailor operations to specific needs, balancing product yields and operational stability.
As environmental regulations tighten, integrating advanced technologies and adopting sustainable practices will ensure that visbreaking continues to play a pivotal role in the industry. Its adaptability, coupled with its potential for improvement, underscores its enduring relevance in the quest for refinery optimization and sustainability.