Transform Your Refining Process with Our Advanced HFO Visbreaking Units
By integrating our HFO (Heavy Fuel Oil) visbreaking units into your refinery processes, you ensure maximum efficiency, cost savings, and environmental compliance. Let us be your partner in achieving superior results.
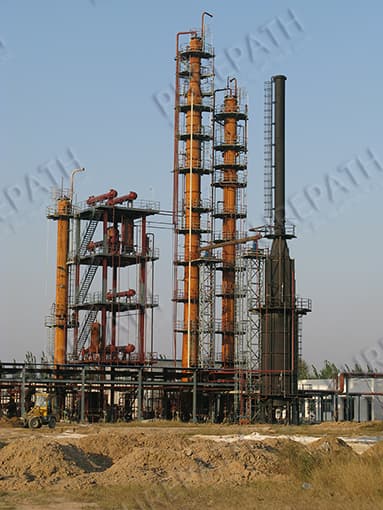
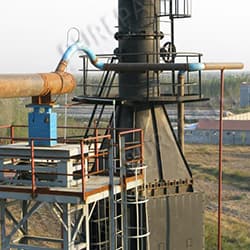

Visbreaking Process in Petroleum Refinery
Heavy Fuel Oil (HFO) is a crucial but often underutilized resource in refineries. Visbreaking, short for viscosity breaking, involves the thermal cracking of heavy residual oils at high temperatures to reduce their viscosity. In a typical visbreaking unit, the feedstock (heavy fuel oil) is heated in a furnace to a high temperature, where thermal cracking occurs. The process breaks down large hydrocarbon molecules into smaller, more valuable ones, producing lighter products such as naphtha, gas oil, diesel and residual fuel.
Our state-of-the-art HFO Visbreaking Units offer an innovative solution to convert these heavy residues into valuable, high-quality products, optimizing your refining operations while improving profitability. Whether you’re looking to reduce viscosity, increase yields, or boost operational efficiency, our visbreaking units are engineered to deliver superior results.
Industries That Benefit from Our HFO Visbreaking Units
- Refining: Convert heavy crude residues into valuable lighter products such as diesel, naphtha, and gas oil.
- Marine: Produce bunker fuels with optimal viscosity for marine engines.
- Power Generation: Supply lower-viscosity fuels for industrial boilers and power plants.
- Petrochemicals: Provide feedstocks for cracking, refining, and other petrochemical processes.
Why Choose Our HFO Visbreaking Units?
Key Features & Benefits
Energy-Efficient:
Optimized furnace designs and heat transfer surfaces ensure minimal energy wastage.
High Throughput:
Maximize production with consistent performance and minimal downtime.
Robust Construction:
High-quality materials that withstand extreme operating conditions for long-lasting durability.
Customizable Solutions:
Tailored designs to suit a wide range of feedstocks and production capacities.
Eco-Conscious:
Low-emission systems reduce environmental impact and ensure compliance with regulatory standards.
Cost-Effective:
Achieve a greater yield of lighter products with less operational input.
Coil Visbreaking Process & Soaker Visbreaking Process
- Coil Visbreaking, also known as Furnace Visbreaking, involves the thermal cracking of heavy hydrocarbons in a furnace. This process is characterized by short residence times at high temperatures, which help to break down large hydrocarbon molecules into smaller, more valuable ones.
- Soaker Visbreaking, also known as Drum Visbreaking, involves lower temperatures and longer residence times compared to Coil Visbreaking. The process is characterized by allowing the feedstock to “soak” at a controlled temperature in a soaker drum.
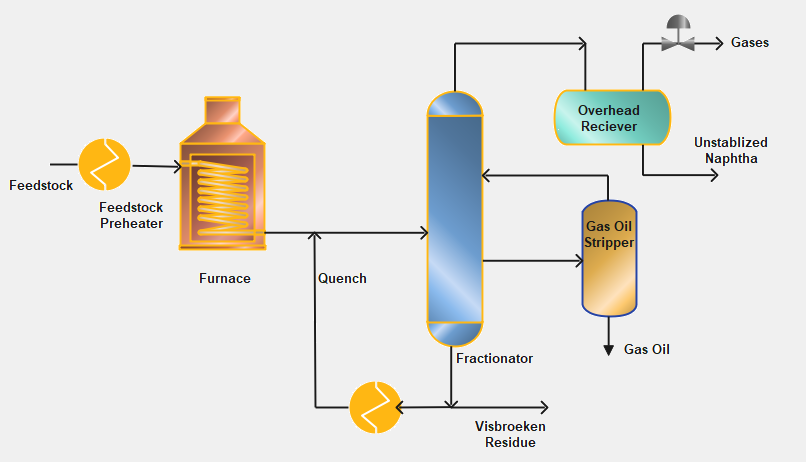
Coil Visbreaking Process Description
- Preheating: The heavy residual oil feedstock is preheated in a heat exchanger using hot products from the process.
- Furnace Heating: The preheated feedstock is then passed through a coil inside a furnace where it is rapidly heated to high temperatures (typically 450-500°C or 842-932°F) for a very short time (a few seconds).
- Thermal Cracking: The high temperature causes thermal cracking of the heavy hydrocarbons, reducing the viscosity of the oil.
- Quenching: The cracked products are rapidly quenched to stop further cracking reactions. This is usually done by mixing the hot cracked products with a cooler liquid stream.
- Separation: The products are sent to a fractionator where lighter fractions (like naphtha and gas oil) are separated from the heavier residue.
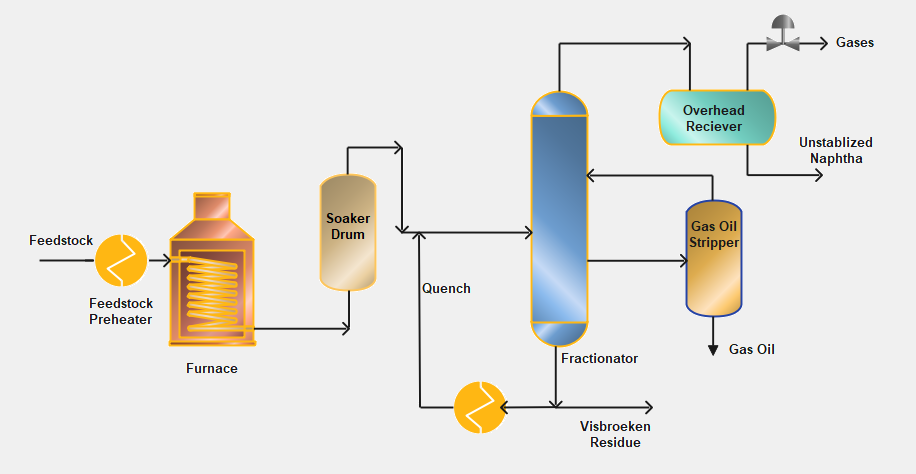
Soaker Visbreaking Process Process Description
- Preheating: The heavy residual oil feedstock is preheated using heat exchangers.
- Furnace Heating: The preheated feedstock is then mildly heated in a furnace to a lower temperature (typically 420-450°C or 788-842°F) than in Coil Visbreaking.
- Soaking: Instead of being rapidly quenched, the heated feedstock is passed into a soaker drum where it is allowed to soak at a controlled temperature for a longer residence time (typically 20-60 minutes).
- Thermal Cracking: During the soaking period, thermal cracking occurs, reducing the viscosity of the oil.
- Separation: The cracked products are then sent to a fractionator where lighter fractions are separated from the heavier residue.
What Sets Us Apart?
Proven Expertise:
We have years of experience delivering top-tier equipment to refineries worldwide.
Innovative Design:
Our engineering team uses the latest technologies to optimize performance, safety, and efficiency.
Dedicated Support:
From initial consultation to installation and maintenance, we ensure seamless operation of your equipment.
Global Reach:
With a strong presence in the refining sector, we’ve established long-term relationships with industry leaders across the globe.
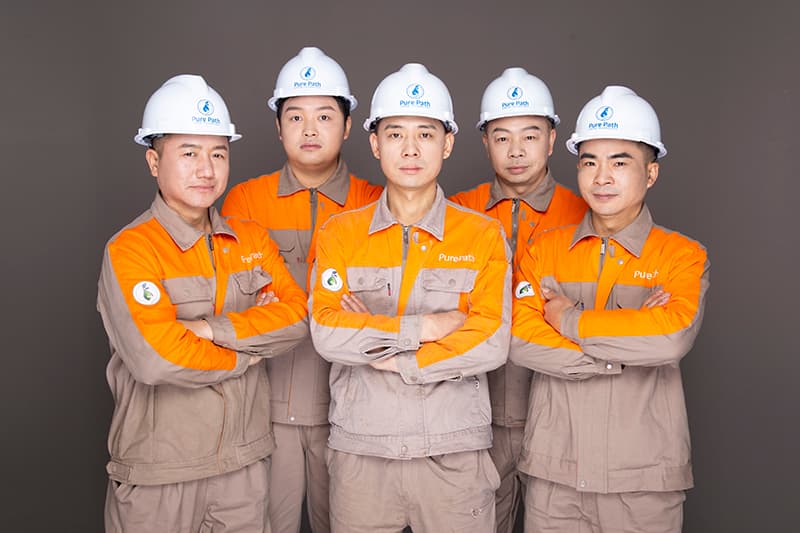
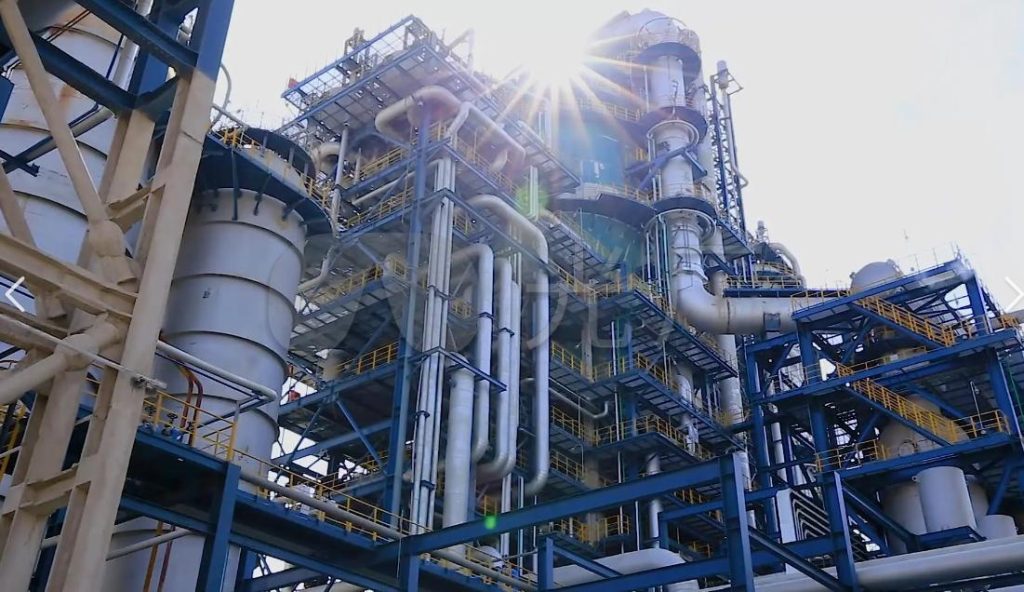
See the Difference: A Customized Solution for Your Refinery
Every refinery is unique, and so are its needs. That’s why we offer tailored solutions designed specifically to enhance your refining process. Whether you’re processing HFO for the marine industry, power generation, or simply to improve your refinery’s overall performance, we have the perfect system for you.
Ready to Optimize Your Refining Operations?
Let’s start a conversation. Our team of experts is ready to help you unlock the full potential of your refinery with advanced HFO Visbreaking Units. Contact us today to receive a personalized consultation and quote.
Get Your Customized Quote
We’re here to provide you with the most efficient and cost-effective HFO visbreaking solution. Fill out the form below, and one of our specialists will reach out to you with a tailored quote based on your specific needs.