How is Distillation Used in Waste Oil?
In the realm of environmental responsibility, waste oil management has become a pressing concern. Waste oil, an inevitable byproduct of industrial and automotive activities, demands effective solutions to mitigate its environmental impact. Distillation, a time-tested separation process, has emerged as a pivotal technology in transforming waste oil into a valuable resource. By leveraging differences in boiling points, distillation facilitates the selective extraction of components, offering a sustainable approach to waste oil treatment.
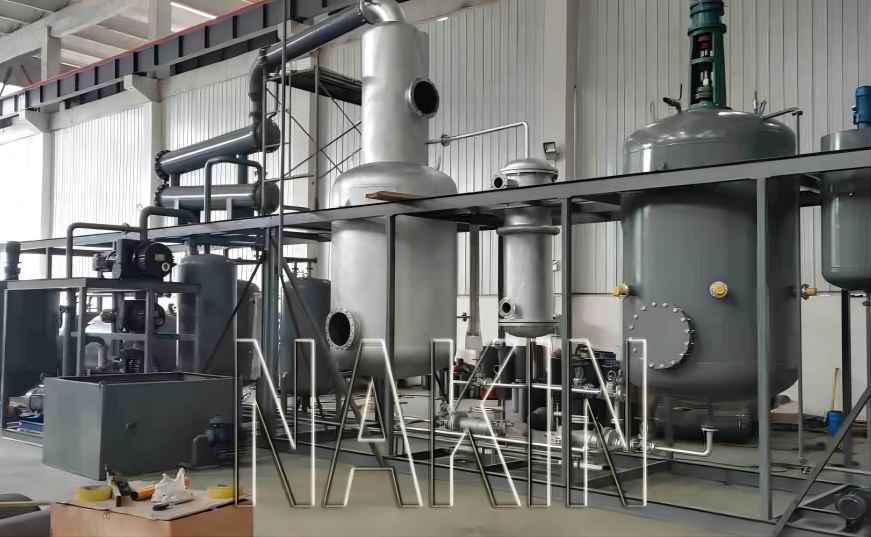
Waste Oil Distillation Principles
Waste oil distillation is a complex and scientifically grounded process that relies on fundamental principles of thermodynamics and separation science. The method hinges on the unique boiling points of various components within waste oil. By applying heat to collected waste oil, a vaporization process ensues, initiating a selective separation of constituents based on their distinct boiling points. Fractional distillation, taking place in a specialized column, facilitates the condensation and collection of different fractions at various levels, ultimately leading to the recovery of valuable base oil.
The process begins with the introduction of heat to the waste oil, prompting vaporization and initiating a meticulous separation based on boiling points. Fractional distillation, a pivotal step in this process, unfolds in a specialized column where vaporized waste oil encounters different temperature zones. This spatial temperature variation orchestrates the condensation and collection of distinct fractions at different levels within the column. Lighter fractions, characterized by lower boiling points, condense at higher levels, while heavier fractions, with higher boiling points, condense at lower levels.
Understanding this principle is essential for optimizing the waste oil distillation process, ensuring efficient separation, and obtaining high-quality recovered products. The application of these principles underscores the potential of waste oil distillation as a key technology in the recycling and reclamation of used oils.
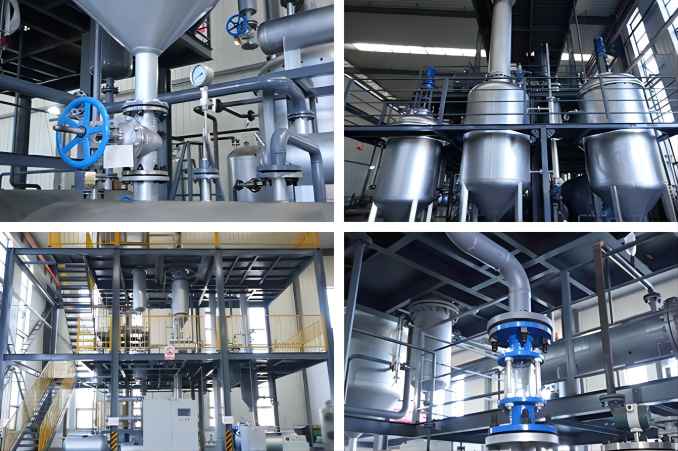
Waste Oil Distillation Process
The distillation process for waste oil is a systematic and multi-step procedure designed to separate and recover valuable components from used or contaminated oils. The primary objective is to reclaim base oil, which can then be reused as a lubricant. The process involves several key stages:
1. Pre-Treatment:
The collected waste oil undergoes initial pre-treatment to remove larger particles, water, and easily separable contaminants. Filtration and settling processes are commonly employed in this phase to enhance the efficiency of subsequent distillation steps.
2. Heating the Waste Oil:
The pre-treated waste oil is then heated in a distillation unit or column. The application of heat raises the temperature of the oil, leading to its vaporization. This step is critical for initiating the separation of various components based on their distinct boiling points.
3. Fractional Distillation:
The vaporized waste oil is introduced into a distillation column, where fractional distillation occurs. As the vapor rises through the column, it undergoes cooling at different temperatures. This results in the condensation of different fractions at various levels within the column. Lighter fractions, with lower boiling points, condense at higher levels, while heavier fractions, with higher boiling points, condense at lower levels.
4. Condensation and Collection:
The condensed fractions, representing different components of the waste oil, are then cooled and collected separately. The collection process is essential for obtaining specific products, with the primary focus on recovering base oil.
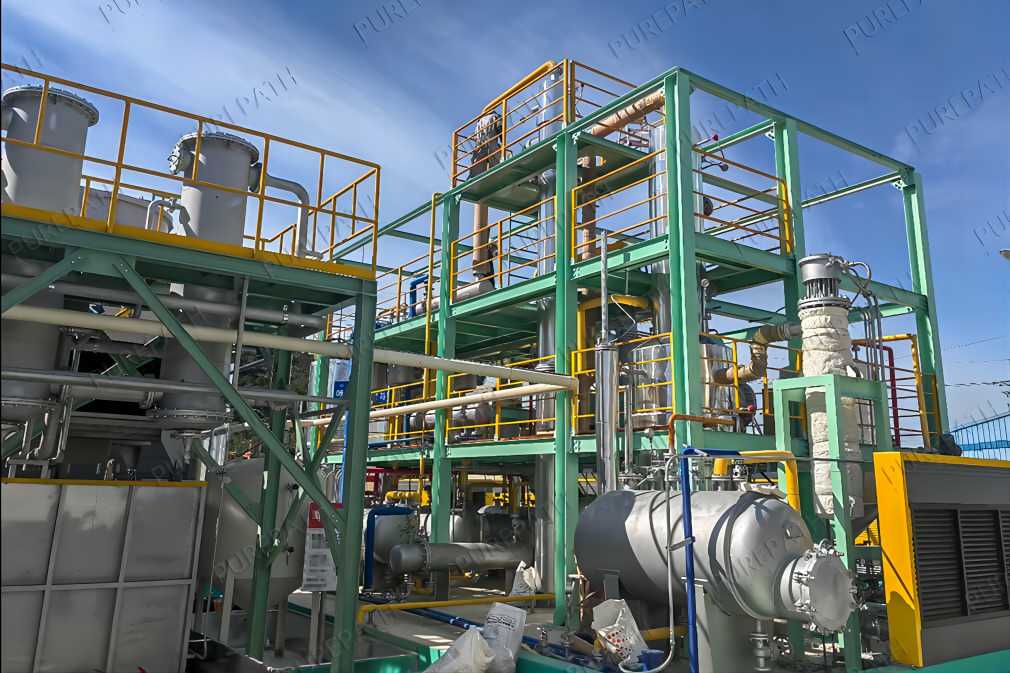
5. Post-Treatment and Refining:
The collected fractions often undergo post-treatment and refining processes to further purify the base oil. Techniques such as hydrotreating or hydrofinishing may be employed to remove remaining impurities and enhance the quality of the recovered oil.
6. Recovery of Additives:
In some instances, the waste oil may contain additives. The distillation process allows for the separation and potential recovery of these additives, contributing to the overall efficiency of the recycling process.
7. Quality Control:
Throughout the distillation process, quality control measures are implemented to ensure that the recovered base oil meets industry standards. This may involve testing for viscosity, flash point, and other relevant properties.
The entire distillation process for waste oil is aimed at transforming a discarded resource into a valuable product with potential applications in various industrial settings. It aligns with sustainable practices by reducing the environmental impact associated with the disposal of used oils and contributes to the circular economy by promoting the reuse of recovered materials.
Types of Distillation Used in Waste Oil
When it comes to reclaiming valuable resources from used oil, there’s not just one distillation technique in the toolbox. Different types of distillation cater to specific needs and yield distinct products. Let’s explore some of the most common methods used in waste oil processing.
1. Batch Distillation:
Imagine a large pot simmering on a stove, gradually separating its contents. That’s the essence of batch distillation. This method involves heating a fixed amount of pre-treated waste oil in a closed chamber until its various components boil off at their respective temperatures.
As vapors rise, they travel up a column and condense at different levels based on their boiling points, eventually collected in separate containers.
Batch distillation is often preferred for smaller operations or when processing diverse batches of waste oil with varying compositions.
2. Continuous Distillation:
Picture a production line continuously churning out products. Continuous distillation operates on a similar principle, continuously feeding pre-treated waste oil into a heated chamber and withdrawing separated fractions as they condense.
This method is ideal for large-scale operations, offering improved efficiency and higher production rates compared to batch distillation.
However, continuous distillation requires a more complex setup and precise control of temperatures and flow rates.
3. Fractional Distillation:
Both batch and continuous distillation rely on the principle of fractional separation. This technique utilizes a column equipped with numerous trays or plates maintained at different temperatures.
As vapors rise up the column, they encounter these temperature zones, condensing at the level where their boiling point matches the prevailing temperature, effectively segregating different components.
Fractional distillation allows for highly precise separation of various fractions, catering to the production of specific products like gasoline, diesel, or lubricating oils.
4. Vacuum Distillation:
Some heavy components in waste oil, like asphalt, have extremely high boiling points. Here’s where vacuum distillation comes in handy. This technique reduces the pressure in the distillation chamber, effectively lowering the boiling points of these components without needing excessively high temperatures.
This prevents thermal degradation and preserves the quality of the extracted product.
Vacuum distillation is typically used to refine heavy fractions into products like bitumen or fuel oil.
5. Advanced Techniques:
Besides these core methods, advancements in technology have brought forth specialized distillation techniques tailored for specific applications. For example, thin-film evaporation offers efficient processing of heavy residues, while solar-powered distillation harnesses renewable energy for the process.
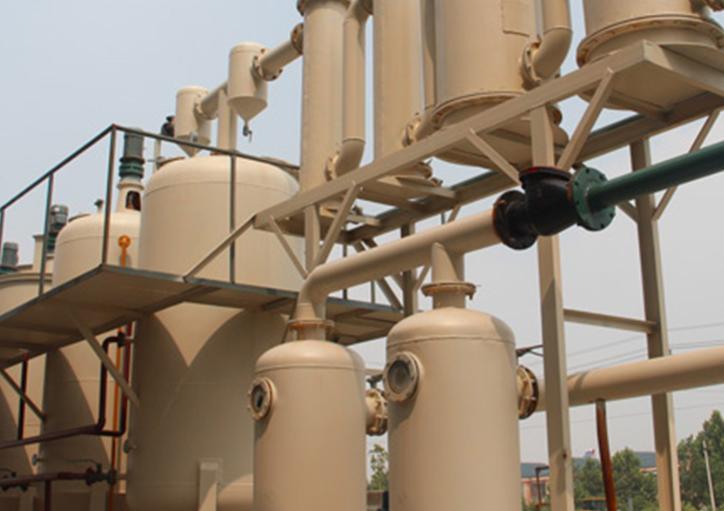
Benefits of Distillation in Waste Oil Management
The utilization of distillation in waste oil management brings forth a myriad of benefits, making it a crucial technology in the quest for sustainable solutions. One primary advantage lies in the recovery of valuable components from waste oil, with distillation enabling the separation of base oils and other high-value byproducts. This not only mitigates the environmental impact of improper waste oil disposal but also transforms discarded resources into reusable materials. Distillation plays a pivotal role in reducing harmful emissions and minimizing the overall environmental footprint associated with waste oil.
From an economic standpoint, the cost-effectiveness of distillation contributes to creating value from waste oil resources, aligning with principles of circular economy and resource efficiency. In essence, the application of distillation in waste oil management emerges as an environmentally sound and economically viable approach, embodying the principles of sustainable resource utilization.
Conclusion
Waste oil distillation is a pivotal technology in waste oil management, embodying principles that not only recover valuable resources but also contribute to sustainable practices.
Utilizing waste oil distillation presents a practical approach to mitigate pollution and establish a sustainable fuel source. Nevertheless, ensuring the proper selection of waste oil types and adherence to safety protocols is crucial to prevent potential accidents. Should you contemplate the conversion of waste oil into diesel fuel, thorough research and consultation with a qualified professional are imperative steps to guarantee a safe and effective process.