How to Choose the Right Waste Oil to Diesel Machine for Your Business
In an era of rising environmental consciousness and fluctuating fuel prices, businesses are actively looking for sustainable and cost-effective alternatives. One such idea gaining pace is the utilization of waste oil in diesel engines. These ingenious technologies turn wasted lubricants into usable diesel fuel, creating a win-win situation for the environment and your bottom line. But how can you select the appropriate waste oil to diesel machine for your individual requirements? Let’s get into the important details.
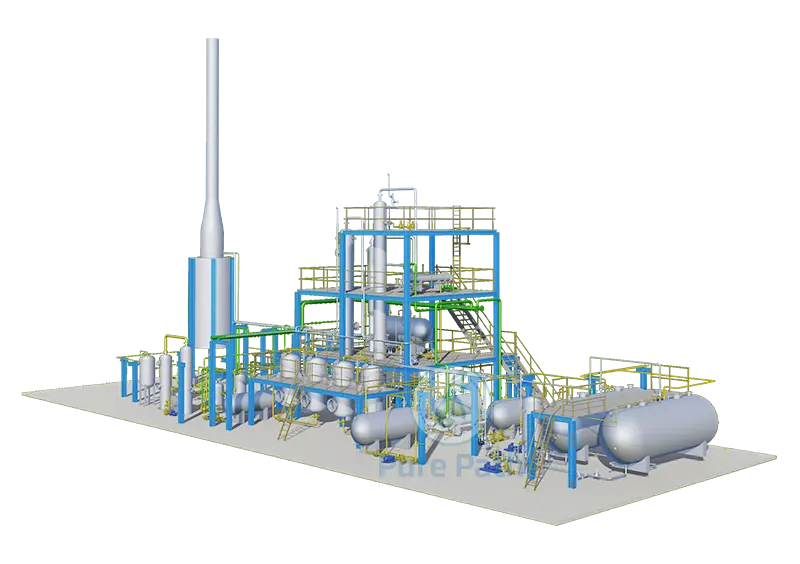
Importance of Waste Oil Recycling
Waste oil is a typical byproduct in industries like automobiles, manufacturing, and food services. If not handled appropriately, it can have serious environmental repercussions, such as soil and water contamination. Recycling waste oil is more than simply an environmentally friendly practice; it is a requirement for organizations seeking to decrease their environmental impact and comply with stringent disposal requirements.
By converting waste oil into diesel, companies can turn a costly waste product into a valuable resource. This process helps:
- Minimize environmental harm: Proper recycling prevents pollution and reduces the strain on natural resources.
- Cut disposal costs: Recycling eliminates the need for expensive waste oil disposal services.
- Generate value: Waste oil can be transformed into high-quality diesel fuel, creating an additional revenue stream or reducing fuel expenses.
In a world increasingly concerned with sustainability, waste oil recycling is a realistic step toward cleaner operations. It promotes the environment while also increasing a company’s productivity and profitability, making it a win-win option.
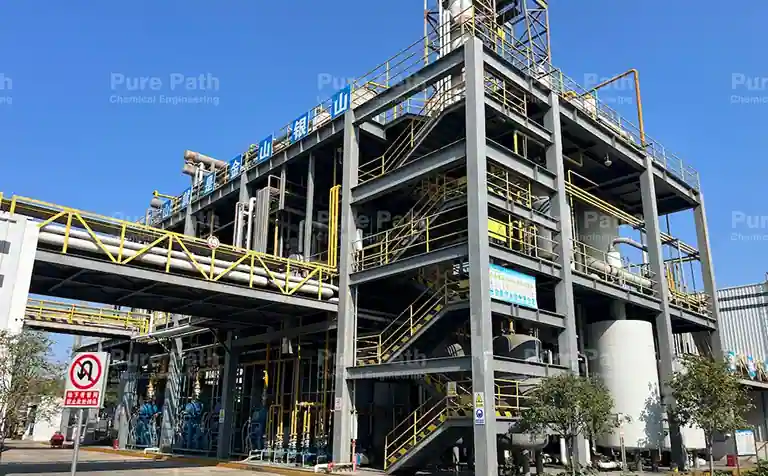
Principle of Waste Oil to Diesel Machines
Waste oil to diesel machines employ a combination of modern chemical and mechanical techniques to convert spent oil into high-quality diesel fuel. The most prevalent techniques are pyrolysis and transesterification, which reduce the complex hydrocarbons in waste oil to simpler, useable forms. Let’s take a deeper look at how it works.
- Pre-Treatment: The procedure starts with filtering the waste oil to eliminate contaminants including water, debris, and solid particles. This stage makes sure the oil is clean and ready for conversion.
- Heating and Conversion: The filtered oil is then heated to high temperatures in a reactor. During this stage, the long-chain hydrocarbons in the oil are broken down into shorter chains through a process called thermal cracking. This step is crucial for converting the oil into a lighter, more usable fuel.
- Distillation: The vapors produced during heating are condensed into liquid form. This liquid is then distilled to separate diesel from other byproducts like gasoline or heavy oils.
- Purification: The final stage is to refine the diesel to remove any remaining contaminants and ensure that it fulfills industry quality and performance standards.
This effective procedure not only recycles waste oil, but also creates diesel fuel for vehicles, generators, and machinery. Understanding how these devices work allows firms to make informed decisions about incorporating this technology into their operations.
Key Factors to Consider When Choosing a Waste Oil to Diesel Machine
Selecting the right waste oil to diesel machine is a critical decision that can significantly impact your business’ efficiency, profitability, and environmental goals. Here are the four most important factors to consider, explained in detail:
1. Capacity and Output
The machine’s capacity should be proportional to the amount of waste oil generated by your firm. For example, if your business generates 1,000 liters of waste oil each day, you’ll require a machine capable of processing that volume efficiently. Consider the output—how much diesel the machine can generate every hour or day. A high-output machine ensures that you satisfy your fuel demands without delay. Overestimating or underestimating capacity might result in inefficiencies, so carefully consider your waste oil volume and fuel requirements before making a decision.
2. Quality of Diesel Produced
The quality of the diesel fuel generated is crucial for its usability and performance. High-quality diesel should meet industry standards like ASTM D975, ensuring it can be used in engines without causing damage or inefficiencies. Poor-quality diesel can lead to engine clogging, increased maintenance costs, and operational downtime. Choose a machine that includes robust purification and filtration systems to produce clean, reliable fuel.
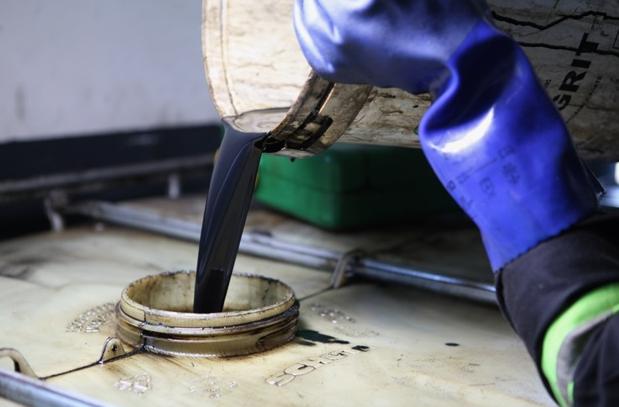
3. Conversion Efficiency
Conversion efficiency is the percentage of waste oil that is successfully converted into diesel fuel. Machines with higher efficiency rates (e.g., 90% or more) increase fuel production while reducing waste. This not only increases your ROI but also minimizes the amount of residual byproduct that needs to be disposed of. To ensure maximum efficiency, look for machines that use the latest technology and have verified performance metrics.
4. Ease of Operation and Maintenance
A user-friendly machine with automated controls and minimal maintenance requirements can save time and reduce operational costs. Look for features like self-cleaning systems, easy-to-replace filters, and clear troubleshooting guides. Additionally, consider the availability of spare parts and technical support from the supplier. A machine that’s simple to operate and maintain ensures smooth, uninterrupted production and extends the lifespan of your investment.
By concentrating on these four essential characteristics, you can choose a waste oil to diesel machine that fulfills your company’s requirements, delivers great performance, and maximizes your return on investment.
Benefits of Investing in a Waste Oil to Diesel Machine
Investing in waste oil to diesel machine offers a compelling array of benefits, both economically and environmentally. Primarily, businesses can achieve substantial cost savings. By producing their own diesel from readily available waste oil, reliance on expensive commercially purchased fuel diminishes. This translates to a direct reduction in operational expenses, particularly for industries with high fuel consumption.
Beyond financial benefits, implementing waste oil recycling significantly improves a company’s environmental stewardship. Transforming garbage into useful fuel minimizes the environmental footprint associated with traditional waste disposal methods and reduces reliance on fossil fuels. This commitment to sustainability can help a company’s brand image by recruiting environmentally conscientious customers and investors.
Furthermore, developing an internal fuel source increases energy independence, protecting firms from the instability of global fuel markets. In some situations, surplus diesel production can even generate a new revenue stream, ensuring the investment’s return.
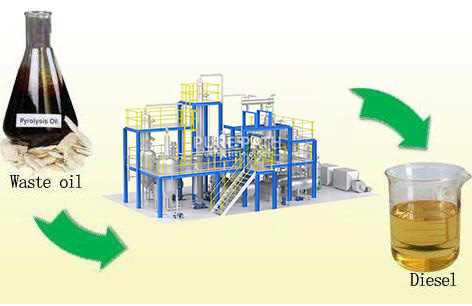
Interested in Waste Oil to Diesel Machine?
If you’re ready to transform waste oil into a valuable resource, consider partnering with PurePath, a leading manufacturer of waste oil to diesel machines. PurePath’s advanced technology ensures high conversion efficiency, producing premium-quality diesel that meets industry standards. Their machines are designed for ease of operation, low maintenance, and robust safety features, making them ideal for businesses of all sizes.
PurePath, with a focus on sustainability and innovation, provides customized solutions to meet your individual demands. Visit PurePath’s website to learn more about their cutting-edge waste oil to diesel plants and take the first step toward a more environmentally friendly, prosperous future.