How to Minimize the Maintenance Cost of Used Oil Recycling Plant?
Used oil recycling plants play a vital role in protecting the environment by transforming used oil into a valuable resource. However, maintaining these plants can be a significant ongoing expense. By implementing proactive strategies, you can minimize maintenance costs and ensure the smooth operation of your facility.
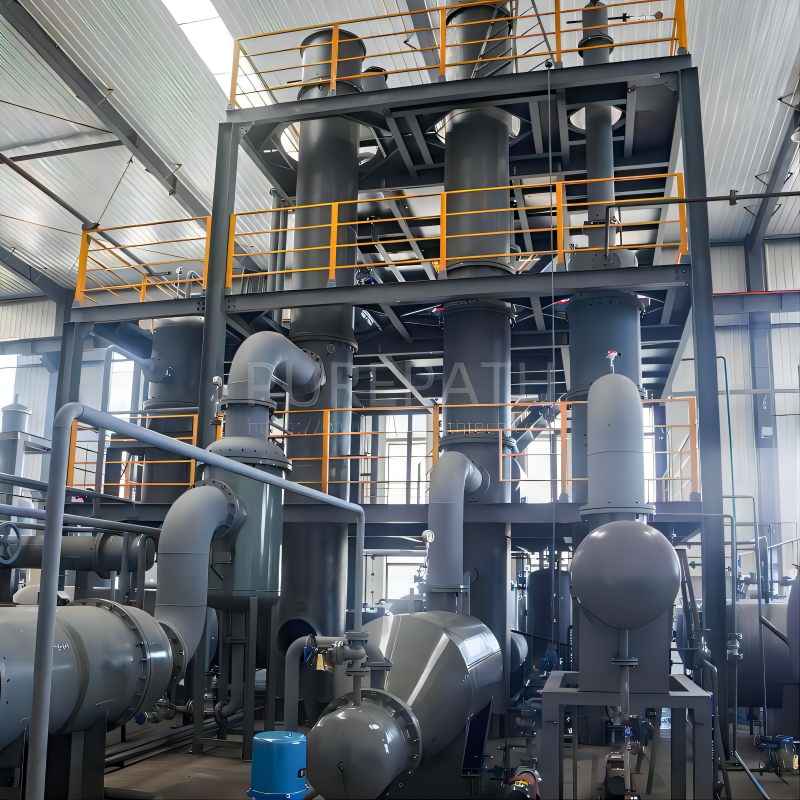
Understanding the Components of a Used Oil Recycling Plant
A used oil recycling plant is an intricate system with various components working together to transform used oil into a valuable resource. Here’s a closer look at the key components and their significance in maintaining a cost-effective operation:
- Pretreatment Equipment: This stage acts as the gatekeeper, removing contaminants that could harm downstream equipment or hinder the recycling process. Common pretreatment equipment includes:
- Storage Tanks: These receive and temporarily store the used oil for initial processing. Regular cleaning and inspection of these tanks are crucial to prevent sediment buildup that can clog pipelines.
- Settling Tanks: These allow heavier solids like dirt and metal shavings to settle out of the oil due to gravity. Efficient removal of these solids reduces wear and tear on pumps and filters in later stages.
- Coalescers: These use a variety of methods to separate water from the oil. Water can interfere with the distillation process and lead to corrosion in pipes, so effective removal is essential.
- Filtration Systems: These remove finer particles suspended in the oil. Regularly replacing filters ensures optimal performance and prevents them from becoming overloaded, potentially leading to contamination of the treated oil.
- Distillation Unit: This is the heart of the recycling process, where the actual separation of oil from contaminants occurs. Here’s where a deeper understanding is beneficial:
- Heaters: These raise the temperature of the oil to a point where various components begin to vaporize at different rates. Maintaining proper heating element functionality and monitoring temperatures closely is vital to avoid overheating and damaging the oil.
- Fractionation Column: This multi-layered tower acts like a separator, allowing different fractions of the oil to condense based on their boiling points. Regular cleaning of the column and ensuring proper packing material (used to enhance separation) are crucial for optimal oil quality and yield.
- Filtration System (Post-Distillation): After distillation, another filtration stage removes any remaining impurities that may have passed through the pretreatment stage. This final cleaning ensures the recycled oil meets the desired quality specifications. Selecting the right filter media and replacing them at recommended intervals is important to prevent them from becoming saturated and compromising filtration efficiency.
- Storage Tanks (Treated Oil): Here, the clean, recycled oil is stored before being transported for further processing or use. Maintaining the integrity of these tanks is essential to prevent leaks or contamination of the final product.
- Control Systems: These are the brains of the operation, monitoring and regulating various aspects of the process, such as temperatures, pressures, and flow rates. Regular calibration and maintenance of control systems ensure the entire plant operates efficiently and safely.
By understanding the function and criticality of each component, you can develop a targeted maintenance plan. This empowers your team to prioritize tasks and identify potential issues before they escalate into costly repairs or downtime. Remember, a well-maintained plant not only saves money but also ensures the quality of the recycled oil and the overall environmental benefit of your operation.
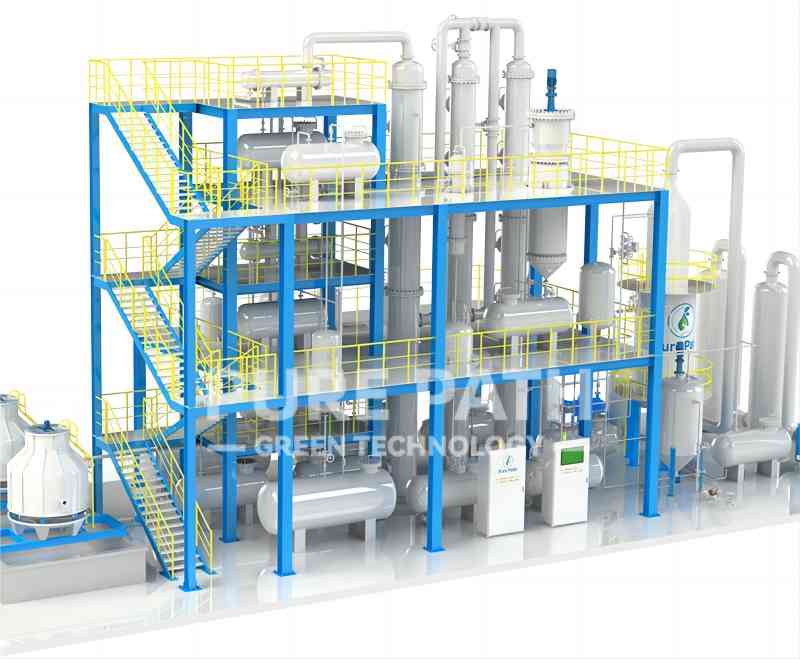
Proactive Maintenance Strategies
Moving beyond reactive maintenance (fixing things when they break), a proactive approach focuses on preventing problems before they occur. Here’s a breakdown of key strategies to minimize maintenance costs:
- Regular Inspections: Schedule frequent inspections tailored to each piece of equipment. Develop checklists that cover critical components like pumps, valves, filters, and safety features. Look for signs of wear and tear, leaks, and corrosion. Weekly or bi-weekly inspections for critical equipment and monthly checks for less critical components are a good starting point.
- Preventative Maintenance Programs: Implement preventative maintenance programs that involve routine servicing of equipment according to manufacturer recommendations. These programs should be documented and include tasks like:
- Oil Changes: Regular oil changes in gearboxes, motors, and hydraulic systems ensure proper lubrication and prevent overheating and component wear.
- Filter Replacements: Clogged filters can restrict flow and damage equipment. Replacing air, oil, and water filters at prescribed intervals is vital.
- Cleaning Procedures: Regular cleaning of equipment, especially heat exchangers and filtration systems, removes built-up contaminants that can impede performance and lead to corrosion.
- Calibration: Regularly calibrate sensors and instruments to ensure accurate readings and optimal process control.
- Oil Analysis: Don’t just focus on the equipment itself. Regularly analyze the used oil being processed to identify potential contaminants that can damage equipment. For example, high levels of chlorine or certain metals can be detrimental to distillation towers. Early detection allows you to adjust the pre-treatment process to safeguard your machinery and potentially extend its lifespan.
- Predictive Maintenance: As your maintenance program matures, consider incorporating predictive maintenance techniques. This involves using vibration analysis, oil analysis trends, and temperature monitoring to predict potential equipment failures before they occur. While this may require additional investment in equipment and expertise, it can significantly reduce downtime and associated costs in the long run.
By implementing a comprehensive proactive maintenance strategy, you can catch problems early, prevent costly breakdowns, and extend the lifespan of your equipment. This not only translates to financial savings but also ensures the smooth and efficient operation of your used oil recycling plant, ultimately contributing to a cleaner environment.
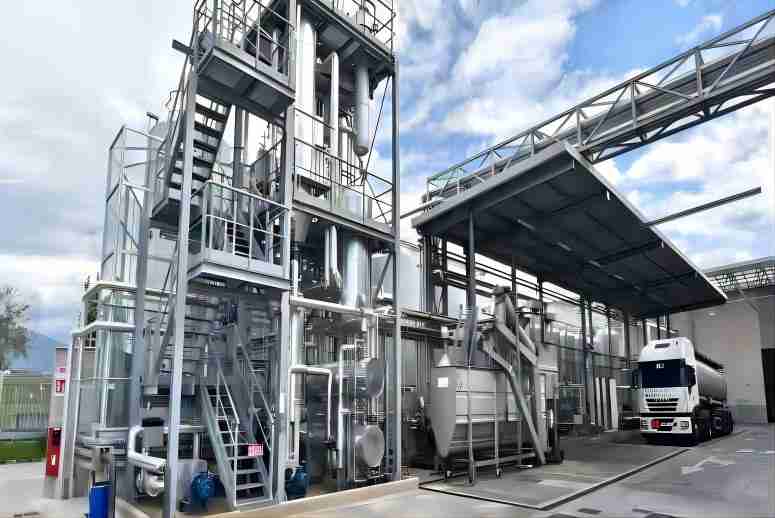
Investing in High-Quality Equipment and Components
While the upfront cost of high-quality equipment and components for your used oil recycling plant might seem daunting, it’s a wise investment that pays off in the long run. Here’s a deeper dive into the benefits:
- Reduced Downtime: High-quality equipment is less prone to breakdowns, minimizing unplanned downtime that disrupts production and cuts into profits. This translates to a more consistent flow of recycled oil and increased revenue potential.
- Lower Repair Costs: Durable equipment requires fewer repairs, saving you money on labor and replacement parts. Additionally, robust construction minimizes the risk of catastrophic failures that necessitate expensive overhauls.
- Improved Efficiency: Advanced equipment often utilizes innovative technologies that optimize the recycling process. This can lead to increased processing capacity, better oil yield, and lower energy consumption. The operational cost savings from these factors can be substantial over the lifespan of the equipment.
- Warranty Coverage: Reputable manufacturers of high-quality equipment typically offer extended warranties that cover repairs and component replacements in case of unforeseen malfunctions. This provides peace of mind and protects your investment against unexpected expenses.
- Enhanced Safety: High-quality equipment prioritizes safety features to minimize the risk of accidents that could injure employees or damage the processing plant. This not only protects your workforce but also reduces the potential for costly liability issues.
Beyond the initial cost, consider these factors when evaluating equipment:
- Manufacturer Reputation: Choose an established manufacturer known for its commitment to quality and reliability.
- Material Quality: Look for equipment constructed from robust materials that can withstand the demanding environment of a used oil recycling plant.
- Spare Parts Availability: Ensure easy access to spare parts to minimize downtime during repairs.
- Energy Efficiency: Prioritize equipment that utilizes energy-saving technologies to reduce your long-term operational costs.
By carefully evaluating these factors and investing in high-quality equipment, you can create a more reliable, efficient, and cost-effective used oil recycling operation. Remember, a well-equipped plant is a sustainable investment that benefits your business and the environment for years to come.
Conclusion
By implementing these strategies, you can significantly reduce maintenance costs and ensure the smooth operation of your used oil recycling plant. Remember, a well-maintained plant not only saves money but also contributes to a cleaner environment by maximizing the efficiency of the recycling process.