How Waste Oil Refinery Plants Reduce Emissions and Save Energy
Waste oil refinery plants play a crucial role in managing and recycling used motor oil, transforming it into valuable, reusable products. These plants not only help in conserving natural resources but also significantly reduce environmental pollution. By implementing advanced technologies and specialized equipment, waste oil refinery plants ensure efficient and eco-friendly refining processes. This article explores the key equipment used in waste oil refineries, common refining technologies, types of catalysts employed, methods for handling sulfides, and energy-saving and emission-reduction measures.
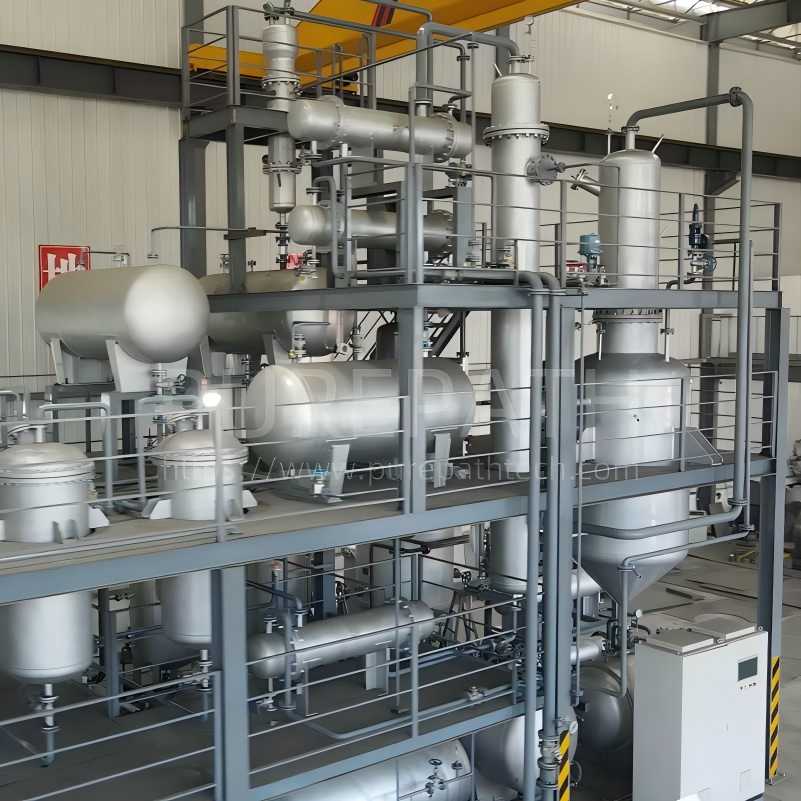
Essential Equipment for Waste Oil Refineries
Waste oil refinery plants utilize a variety of specialized equipment to ensure high efficiency and environmental compliance throughout the refining process. Here are some key equipment as follows:
- Distillation reactors are pivotal in heating waste oil, causing it to undergo distillation at high temperatures to separate different components. These reactors are designed to withstand high pressures and temperatures, facilitating the breakdown of complex oil molecules into simpler, more valuable fractions.
- Catalytic towers enhance the quality and yield of refined oil by promoting chemical reactions during the vacuum distillation process. The towers contain catalysts that aid in breaking down larger hydrocarbon molecules into smaller, more usable ones, thus improving the efficiency and effectiveness of the refining process.
- Condensation systems are used to cool the vaporized oil fractions post-distillation, converting them back into liquid form. This process is crucial for collecting and further refining the separated oil fractions. Efficient condensation systems ensure maximum recovery of valuable oil products.
- Decolorization filtration systems are designed to remove pigments, impurities, and other undesirable substances from the oil, enhancing its transparency and appearance. The decolorization process is essential for producing high-quality, visually appealing oil products.
- Water film dust removal systems effectively capture and eliminate dust and particulate matter generated during the refining process. This not only improves air quality within the refinery but also minimizes environmental pollution, ensuring compliance with stringent environmental regulations.
- Desulfurization purification towers play a vital role in removing sulfur compounds from the oil, reducing its environmental impact. These towers utilize various methods, such as hydrogenation, to convert sulfur compounds into less harmful substances, thereby producing cleaner, more eco-friendly oil products.
- Heat oil systems, including thermal oil systems, provide the necessary heat to maintain the required temperatures for the refining process. These systems ensure stable and efficient heating, contributing to the overall efficiency of the refinery.
- Burners, such as heavy oil burners, supply the energy needed for fuel combustion, facilitating the refining process. Efficient burners reduce fuel consumption and emissions, contributing to the refinery’s energy-saving and emission-reduction goals.
Common Technologies Used in Waste Oil Refinery Plants
Waste oil refinery plants employ various advanced technologies to optimize the refining process, enhance oil quality, and minimize environmental impact.
- Vacuum Distillation Technology: Vacuum distillation allows distillation to occur at lower temperatures by reducing the pressure within the distillation column. This technology minimizes thermal cracking and oxidation, leading to higher-quality oil products. Vacuum distillation is particularly effective in refining high-boiling-point components of waste oil.
- Solvent Extraction Technology: Solvent extraction involves using solvents to selectively remove impurities from waste oil. This technology improves the purity of the refined oil by dissolving unwanted substances and separating them from the desired oil fractions. Solvent extraction is highly effective in enhancing the overall quality of the refined oil.
- Rapid Heating Systems: This system utilizes circulating heating mediums and simultaneous fuel heating to accelerate the distillation process. These systems enhance the efficiency of the refinery by reducing processing times and conserving raw materials, resulting in cost savings and increased productivity.
- Diesel Purification Systems: This system further refines the diesel fraction obtained from waste oil, improving its color and quality. These systems employ advanced filtration and treatment methods to remove residual impurities, ensuring the production of high-quality diesel that meets industry standards.

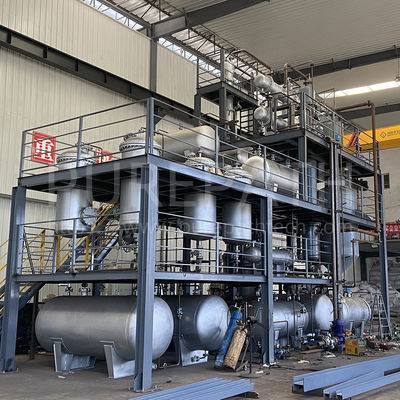
The Role of Catalysts in Waste Oil Refining
Catalysts play a crucial role in many waste oil refinery processes. These substances accelerate chemical reactions without being consumed themselves. Different types of catalysts are employed depending on the specific goal:
- Liquid catalysts: These catalysts are directly added to the used oil during processing. They are generally simpler to implement but may require more frequent replacement.
- Gas-phase catalysts: Located within the catalytic tower, these catalysts interact with the vaporized oil fractions. They can be highly effective but require careful maintenance to prevent clogging by contaminants in the oil.
- Special high-efficiency catalysts: These advanced catalysts are designed to maximize refining efficiency and reduce processing temperatures. They can shorten processing times and increase the yield of desirable products like diesel fuel.
- Desulfurization catalysts: Specifically targeted at removing sulfur compounds from the oil, these catalysts help meet stricter environmental regulations for cleaner fuel products.
- Dewaxing catalysts: In colder climates, wax formation in diesel fuel can be problematic. Dewaxing catalysts aid in removing these wax components, ensuring the diesel remains fluid at low temperatures.
- Deodorizing catalysts: Used oil can retain unpleasant odors. Deodorizing catalysts help eliminate these odors, improving the overall quality and marketability of the refined products.
- Fully hydrogenated regeneration catalysts: These catalysts are employed in a specific process for regenerating used lubricating oils. They operate under relatively mild conditions and effectively remove contaminants like sulfur, nitrogen, oxygen, and heavy metals from the used oil.
The specific type and combination of catalysts used in a waste oil refinery will depend on the type of feedstock (used oil), the desired end products, and the specific technology employed by the facility.
Methods for Handling Sulfides in Waste Oil
Sulfur compounds present in used motor oil can pose environmental and operational challenges. Several methods are employed to remove these contaminants:
- Hydrorefining: This widely used technique involves reacting the oil with hydrogen under high pressure and temperature in the presence of a catalyst. The hydrogen breaks down sulfur molecules into hydrogen sulfide (H2S) gas, which can then be removed through absorption or other chemical processes. Hydrorefining effectively removes not only sulfur but also nitrogen and oxygen contaminants from the oil.
- Catalytic cracking: In this process, the used oil is exposed to high temperatures and a catalyst, causing the larger hydrocarbon molecules in the oil to break down into smaller molecules. While catalytic cracking can be effective in removing some sulfur compounds, it may also lead to the formation of lighter sulfur-containing molecules that require further removal steps.
- Membrane separation technology: This technique utilizes specialized membranes with pores that allow oil molecules to pass through while blocking larger sulfur molecules. Membrane separation offers a potentially cleaner and more energy-efficient alternative to traditional methods.
- High-temperature distillation: While not as effective on its own, high-temperature distillation can be used in conjunction with other methods to remove sulfur compounds. By driving off lighter sulfur-containing fractions, it can help prepare the oil for further processing with other desulfurization techniques.
- Plasma oxidation: This emerging technology utilizes plasma, a state of matter consisting of charged particles, to oxidize organic sulfur compounds in the oil. The oxidized sulfur can then be converted into inorganic sulfates, which are easier to remove from the oil.
The specific method or combination of methods chosen for sulfur removal will depend on factors like the type of used oil being processed, the desired level of sulfur reduction, and economic considerations.
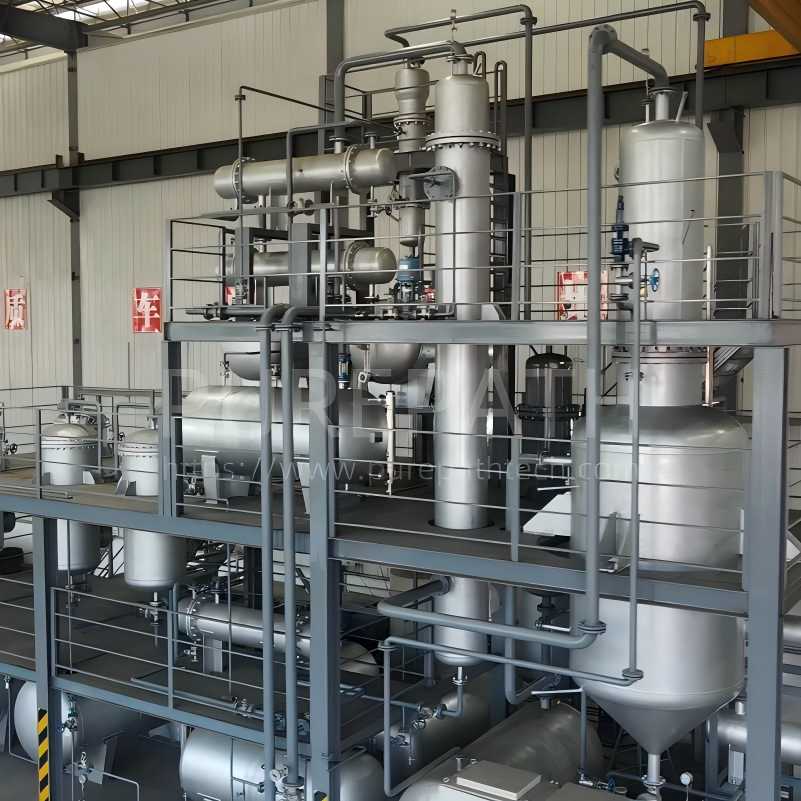
Energy Saving and Emission Reduction in Waste Oil Refineries
The waste oil refinery industry is increasingly focused on minimizing its environmental footprint. Several strategies are employed to achieve this goal:
- Low-temperature refining technology: This approach utilizes techniques like liquid membrane distillation and vacuum distillation at lower temperatures. By reducing the heat required for processing, it helps conserve energy and minimize the formation of harmful pollutants.
- New catalytic cracking process: By incorporating a catalytic tower and temperature control systems into the cracking process, this technology allows for more efficient cracking while reducing fuel consumption. This not only conserves energy but also improves the quality of the refined oil products, particularly their density and viscosity.
- Use of energy-saving equipment: Modern refineries are increasingly employing energy-efficient equipment like high-efficiency furnaces and compressors. These advancements optimize energy consumption throughout the refining process.
- Energy management system: Implementing a comprehensive energy management system allows refineries to monitor and analyze their energy usage in real time. This data can be used to identify areas for improvement and implement targeted strategies to reduce energy waste.
- Resource utilization of waste: Innovative technologies are being developed to utilize waste materials generated during the refining process. For example, some refineries are exploring using the solid residue from distillation as a fuel source within the refinery itself, promoting resource recovery and reducing reliance on external fuels.
- Reduce pollutant emissions: Waste oil refineries are subject to strict environmental regulations regarding air and water emissions. Advanced treatment technologies are employed to capture and remove pollutants like dust particles, volatile organic compounds (VOCs), and wastewater contaminants before they are released into the environment.
- Automation and intelligent control: Automating various processes within the refinery not only improves efficiency and safety but also helps to reduce energy consumption. Intelligent control systems can optimize process parameters based on real-time data, further minimizing energy waste and ensuring consistent product quality.
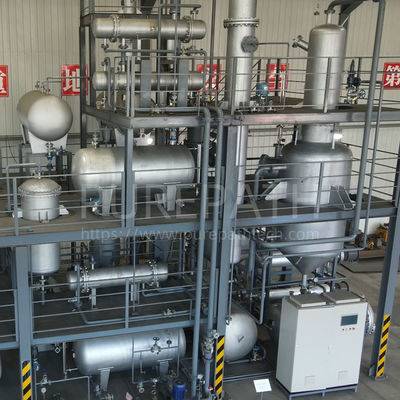
Conclusion
Waste oil refinery plants play a vital role in transforming a potential environmental hazard into a valuable resource. By employing advanced technologies and prioritizing environmental responsibility, these facilities can contribute to a more sustainable future. As research and development continue, we can expect further advancements in waste oil refining processes, leading to even greater efficiency, cleaner operations, and the production of high-quality recycled oil products. Ultimately, a robust waste oil refinery industry not only benefits the environment by preventing improper disposal but also contributes to a more circular economy by reducing our reliance on virgin crude oil extraction.