Hydrocracking vs.Catalytic Reforming Technologies in Crude Oil Refining
Crude oil refining is an intricate process involving various techniques to convert heavy hydrocarbons into valuable, lighter products like gasoline, diesel, jet fuel, and petrochemical feedstocks. Two key technologies employed in this refining process are hydrocracking and catalytic reforming. Both technologies play critical roles, though they differ significantly in their mechanisms, products, and industrial applications. This article explores these technologies, their differences, and their respective impacts on the refining industry.
Hydrocracking and Catalytic Reforming in Crude Oil Refining
Crude oil refining is a multi-stage process where crude oil is transformed into a variety of marketable products such as gasoline, diesel, jet fuel, lubricants, and petrochemical feedstocks. Among the various refining processes, hydrocracking and catalytic reforming are vital secondary processes. These advanced refining techniques help improve fuel quality, optimize yields, and meet both market demand and stringent environmental regulations.
Hydrocracking
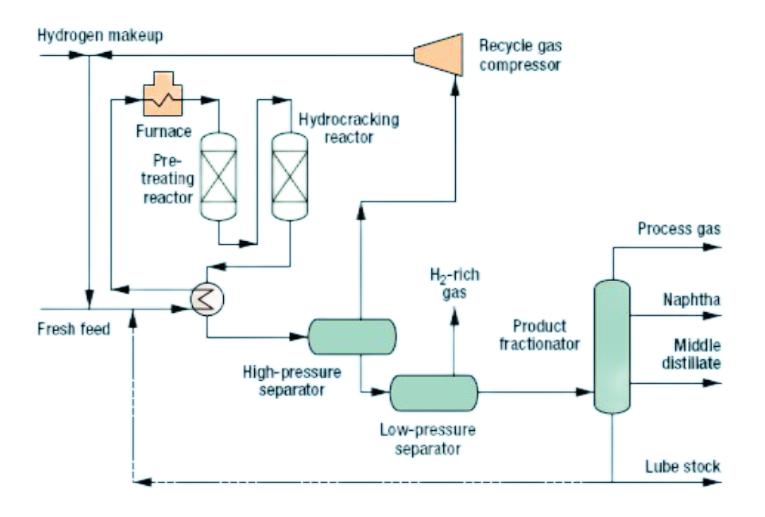
Hydrocracking is a catalytic process used to break down large, heavy hydrocarbon molecules into smaller, more valuable products. This process plays a crucial role in upgrading lower-quality feedstocks, such as vacuum gas oil and atmospheric residue, into cleaner fuels.
Objective: Converts heavy hydrocarbons into lighter fractions like gasoline, diesel, and jet fuel.
Process:
- Operates at high pressure (2,000–3,000 psi) and moderate to high temperatures (250–450°C).
- Involves the use of hydrogen to stabilize cracked molecules and reduce sulfur content.
- Utilizes bifunctional catalysts (platinum, palladium, or nickel-molybdenum) to perform both cracking and hydrogenation reactions.
Products: Produces clean-burning fuels, such as ultra-low sulfur diesel (ULSD), gasoline, kerosene, and petrochemical feedstocks like naphtha and isobutane.
Flexibility:
- Can handle a wide variety of feedstocks, allowing refiners to optimize production based on market demands.
- It can be adjusted to produce more diesel, jet fuel, or petrochemical feedstocks depending on demand.
Catalytic Reforming
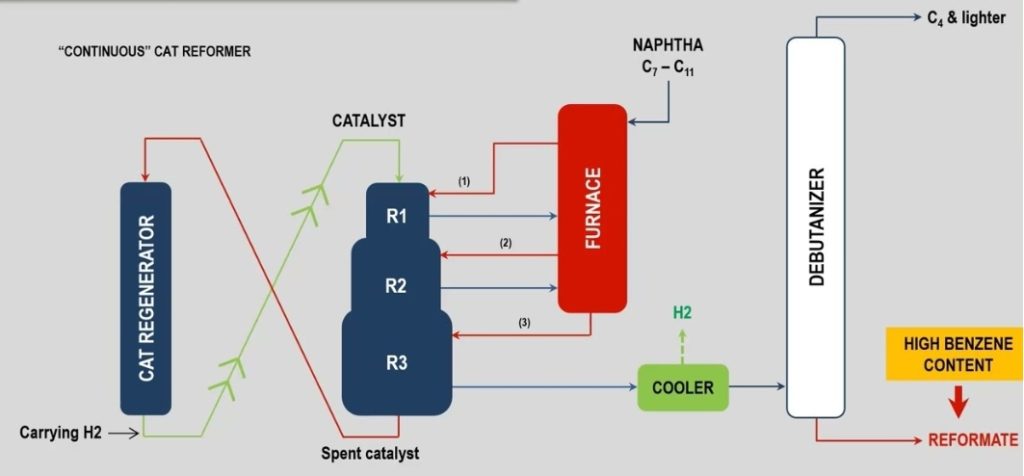
Catalytic reforming focuses on improving the quality of naphtha by increasing its octane number, making it suitable for blending into gasoline. This process is essential for producing high-octane gasoline and valuable aromatic compounds used in petrochemicals.
Key features of catalytic reforming:
- Feedstocks: Primarily processes low-octane naphtha fractions obtained from crude distillation or hydrocracking units.
- Catalysts: Uses platinum-based catalysts, sometimes combined with rhenium, supported on alumina.
- Hydrogen: Produces hydrogen as a by-product, which is useful for other refining processes like hydrocracking or desulfurization.
- Products: Produces high-octane reformate for gasoline blending, along with aromatics such as benzene, toluene, and xylene (BTX), used in the petrochemical industry.
- Operating Conditions: Operates at lower pressures (100–500 psi) but higher temperatures (450–550°C) than hydrocracking.
- Environmental Impact: Increases fuel efficiency and performance by enhancing the octane rating of gasoline.
Catalytic reforming is also a major contributor to the petrochemical industry, providing critical building blocks for plastics, resins, and synthetic fibers.
Differences between Hydrocracking vs. Catalytic Reforming Technologies
Although both hydrocracking and catalytic reforming are essential in refining crude oil, they serve different purposes and operate under distinct conditions. The following table outlines the key differences between the two processes in terms of function, feedstocks, hydrogen usage, and end products.
Aspect | Hydrocracking | Catalytic Reforming |
Primary Function | Breaks down heavy hydrocarbons into lighter fuels like gasoline, diesel, and jet fuel. | Converts low-octane naphtha into high-octane gasoline and produces aromatics. |
Feedstock Variety | Can process heavy feedstocks like vacuum gas oil and atmospheric residues. | Primarily processes light naphtha fractions. |
Hydrogen Usage | Consumes large amounts of hydrogen to saturate cracked molecules. | Produces hydrogen as a by-product. |
End Products | Produces clean fuels with low sulfur content and petrochemical feedstocks. | Produces high-octane reformate for gasoline and aromatics for petrochemicals. |
Operating Conditions | High pressure (2,000–3,000 psi) and moderate to high temperature (250–450°C). | Lower pressure (100–500 psi) but higher temperature (450–550°C). |
Hydrocracking excels in breaking down heavier molecules for clean fuels, while catalytic reforming focuses on enhancing gasoline quality and producing key petrochemical feedstocks.
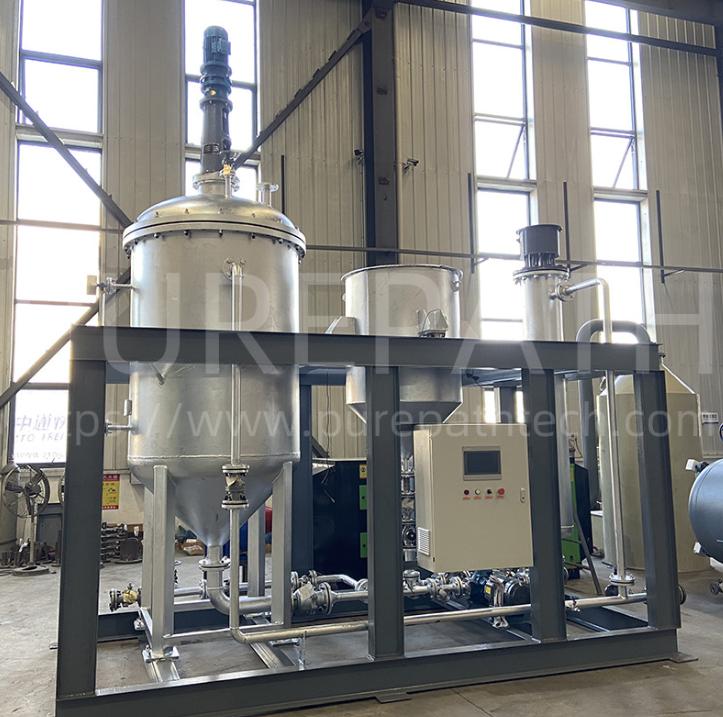
Applications and Industry Impact of Hydrocracking and Catalytic Reforming
Hydrocracking and catalytic reforming are not just technical processes; they significantly influence the crude oil refining industry and the broader energy and petrochemical sectors. Their applications and impacts are profound, contributing to fuel production, environmental compliance, and economic viability.
Hydrocracking Applications and Industry Impact
1. Fuel Production:
- Clean Fuels: Hydrocracking is critical for producing ultra-low-sulfur diesel (ULSD), which is essential for meeting stringent emission regulations, such as those outlined by the Environmental Protection Agency (EPA) in the U.S. and similar regulatory bodies worldwide. This is increasingly important as governments impose stricter standards to reduce air pollution and greenhouse gas emissions.
- Flexibility in Product Output: Hydrocracking units can adapt to market demands, allowing refineries to adjust production between gasoline, diesel, and other products. This flexibility is particularly valuable during periods of fluctuating demand for different fuel types.
2. Petrochemical Feedstocks:
- High-Quality Naphtha: Hydrocracking produces high-quality naphtha that serves as a critical feedstock for the petrochemical industry. Naphtha can be further processed in steam crackers to produce essential building blocks like ethylene, propylene, and butadiene, which are used in manufacturing plastics, synthetic fibers, and other chemicals.
- Increasing Petrochemical Production: With the growing demand for petrochemicals, particularly in emerging markets, hydrocracking helps refineries diversify their product slate and capitalize on the high-value petrochemical sector.
3. Environmental Compliance:
- Reduction of Sulfur Emissions: By producing clean fuels with low sulfur content, hydrocracking processes play a vital role in helping refineries comply with global environmental regulations. This compliance not only meets legal requirements but also enhances the refinery’s reputation and marketability.
4. Economic Viability:
- Cost Efficiency: Hydrocracking enables the economic processing of heavy crude oils, which are becoming more prevalent as lighter crudes diminish. By converting these less desirable feedstocks into high-value products, hydrocracking enhances the overall profitability of refining operations.
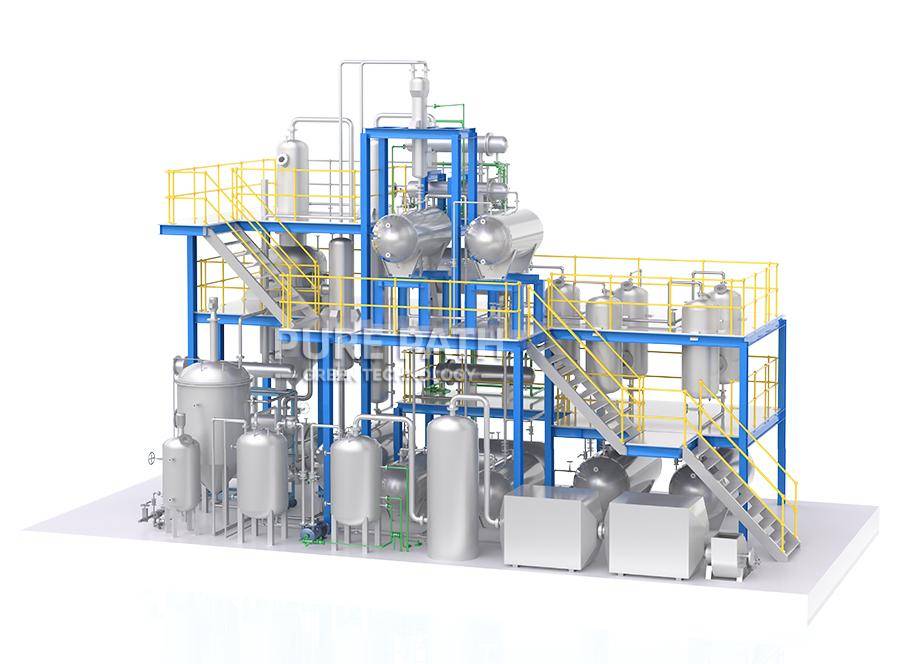
Catalytic Reforming Applications and Industry Impact
1. Gasoline Production:
- High-Octane Gasoline: Catalytic reforming plays a crucial role in producing high-octane reformate, which is blended with gasoline to enhance performance and fuel efficiency. This is especially vital as automotive technology advances towards more fuel-efficient engines with higher compression ratios for better power output.
- Meeting Market Demand: With increasing consumer demand for high-performance vehicles, the need for superior gasoline quality has grown. Catalytic reforming helps refineries meet this demand by producing fuel with optimal combustion properties.
2. Production of Aromatics:
- Key Petrochemical Intermediates: The process yields valuable aromatic compounds like benzene, toluene, and xylene (BTX), which are essential for manufacturing chemicals such as solvents, resins, and plastics.
- Boosting the Petrochemical Industry: The availability of BTX from catalytic reforming supports the expansion of the petrochemical sector, enabling the production of a wide array of consumer and industrial products.
3. Hydrogen Supply:
- In-House Hydrogen Generation: Hydrogen generated during catalytic reforming is critical for other refinery processes, including hydrocracking and hydrotreating. This internal hydrogen supply streamlines refinery operations, reducing the need for external hydrogen sources and lowering operational costs.
4. Environmental Benefits:
- Improved Fuel Efficiency: By increasing the octane rating of gasoline, catalytic reforming contributes to better fuel efficiency and reduced vehicle emissions, aligning with global efforts to lower carbon footprints and enhance air quality.
5. Economic Impact:
- Cost-Effective Refinery Upgrades: Catalytic reforming offers an economical solution for upgrading naphtha to meet market standards without requiring substantial new investments, making refineries more competitive in a fluctuating market.
Hydrocracking and catalytic reforming are vital refining processes that complement each other in producing cleaner fuels and valuable petrochemical products. Hydrocracking focuses on converting heavy fractions into lighter fuels, while catalytic reforming upgrades naphtha for high-octane gasoline and aromatics. Together, they enhance crude oil refinery efficiency, meet environmental standards, and support the evolving energy and petrochemical markets.