Hydrocracking vs Hydrotreating: Two Types of Hydroprocessing In Petroleum Refining
Hydroprocessing plays a vital role in petroleum refining, focusing on enhancing the quality of crude oil derivatives by eliminating impurities and refining their chemical composition. This category encompasses two key techniques: hydrocracking and hydrotreating, which fulfill unique but interrelated functions within refining operations. The following sections explore the details of these processes, including their catalysts, distinctions, and how they complement each other.
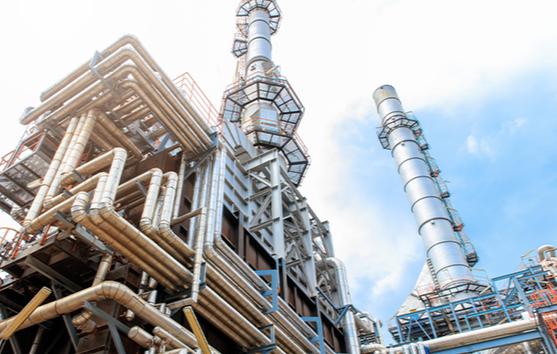
What are Hydrocracking and Hydrotreating?
Hydrocracking is a catalytic process in refining that transforms heavy hydrocarbon molecules into lighter and more valuable products such as gasoline, diesel, and jet fuel. This method relies on elevated temperatures, typically ranging from 400 to 700°F, and high pressures of 1,000 to 3,000 psi, with hydrogen and specialized catalysts playing key roles. Hydrogen serves a dual purpose: stabilizing the resulting smaller hydrocarbon molecules and minimizing the production of undesired byproducts like coke. Hydrocracking is particularly advantageous for upgrading low-value feedstocks, including vacuum gas oils and residual oils, into high-grade fuel products.
In contrast, hydrotreating focuses on purifying petroleum fractions by eliminating impurities such as sulfur, nitrogen, oxygen, and metals. These contaminants can degrade fuel quality, harm refining equipment, or contribute to environmental pollution. Operating at moderate temperatures between 300 and 800°F and pressures of 400 to 2,000 psi, hydrotreating uses hydrogen and catalysts to chemically remove these unwanted substances. Unlike hydrocracking, hydrotreating does not significantly alter the molecular structure of hydrocarbons but instead enhances feedstock quality and ensures adherence to environmental regulations, such as those governing ultra-low sulfur fuels.
Catalyst Types in Hydrocracking and Hydrotreating
Catalysts play a pivotal role in both hydrocracking and hydrotreating, dictating the efficiency, selectivity, and effectiveness of each process.
Hydrocracking Catalysts
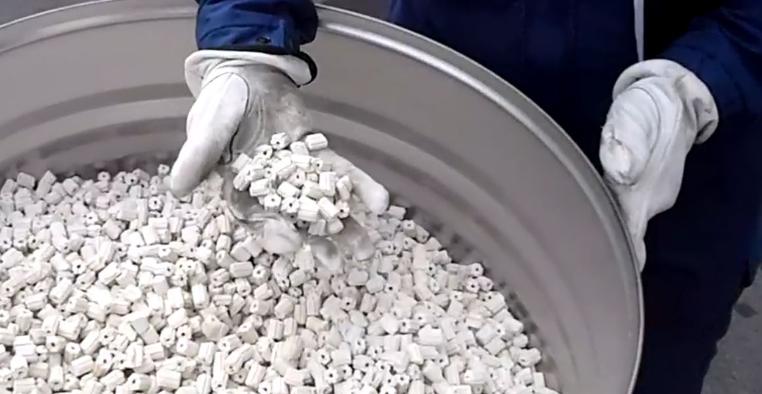
Hydrocracking relies on bifunctional catalysts that combine two key components:
- Acidic Support: Zeolites and amorphous silica-alumina are examples of materials that act as acidic sites. Their role is crucial in facilitating cracking reactions, which break large hydrocarbon molecules into smaller, more valuable products.
- Active Metals: Reactions like hydrogenation and dehydrogenation are driven by metals such as platinum and palladium (noble metals) or base metals like nickel-molybdenum (Ni-Mo) and cobalt-molybdenum (Co-Mo). These metals play a key role in ensuring stability and encouraging the development of desired hydrocarbon structures.
Hydrotreating Catalysts
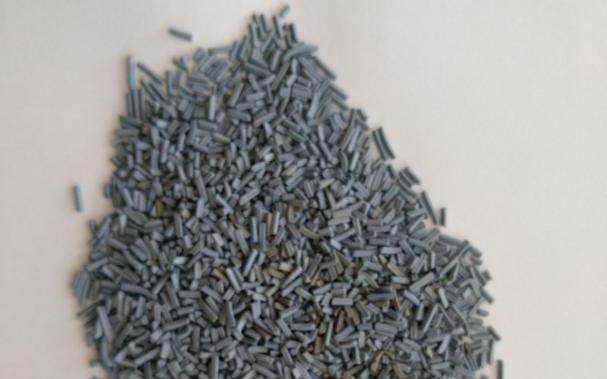
Hydrotreating catalysts are specifically designed to remove impurities like sulfur, nitrogen, oxygen, and metals from feedstocks.
- Active Metals: Cobalt-molybdenum (Co-Mo) or nickel-molybdenum (Ni-Mo) combinations are commonly employed. These sulfide-based metals excel at eliminating impurities, especially sulfur and nitrogen compounds.
- Support Material: To maximize their efficiency, the active metals are distributed across high-surface-area alumina support. This support not only stabilizes the metals but also enhances their interaction with the feedstock.
The carefully engineered structure of these catalysts is designed to address the specific requirements of hydrocracking and hydrotreating, ensuring effective processing and the production of high-quality outputs.
Hydrocracking vs Hydrotreating: What’s the Difference?
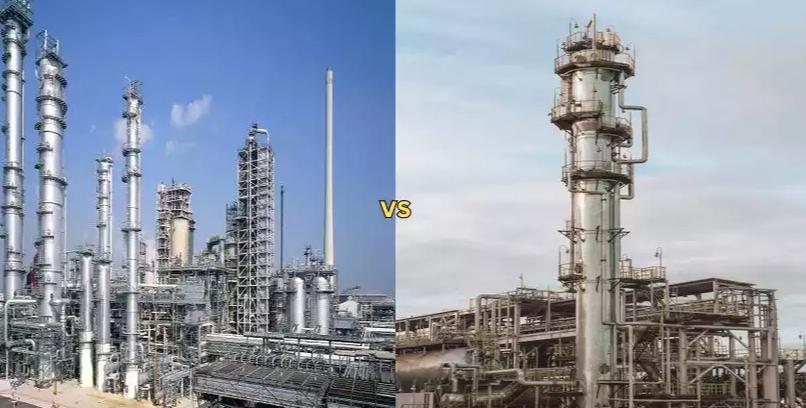
Hydrocracking and hydrotreating are distinct processes with different goals, operating conditions, and outcomes. Here’s a comparison of their key characteristics:
Aspect | Hydrocracking | Hydrotreating |
Primary Purpose | Converts heavy hydrocarbons into lighter, high-value products like diesel, jet fuel, and gasoline. | Removes impurities such as sulfur, nitrogen, oxygen, and metals from feedstocks. |
Key Reaction | Breaks down (cracks) large hydrocarbon molecules using hydrogen. | Hydrogenates and removes impurities without altering the feedstock structure. |
Operating Conditions | Requires higher temperatures (400–450°C) and pressures (up to 200 bar). | Operates at lower temperatures (300–400°C) and pressures (typically 50–100 bar). |
Catalyst Composition | Bifunctional catalysts combining an acidic component (e.g., zeolite) and metals (e.g., Ni-Mo, Co-Mo, or noble metals). | Metal sulfides (e.g., Co-Mo or Ni-Mo) supported on alumina. |
Hydrogen Consumption | High hydrogen demand for saturation and cracking. | Moderate hydrogen usage for impurity removal. |
Product Output | Produces lighter, high-value fuels with improved yield flexibility. | Maintains the feedstock’s molecular structure while producing cleaner, compliant fuels. |
End Use | Produces fuels for direct use (diesel, jet fuel, etc.) or blending. | Prepares feedstocks for further refining or as final products that meet environmental standards. |
Environmental Role | Produces ultra-clean fuels with reduced emissions. | Ensures compliance with sulfur and other regulatory limits. |
This comparison emphasizes that hydrocracking primarily aims at conversion and enhancing product quality, whereas hydrotreating focuses on purification and the removal of impurities. Despite their distinct objectives, these two processes frequently work together to complement one another in refinery operations.
Synergy Between Hydrocracking and Hydrotreating
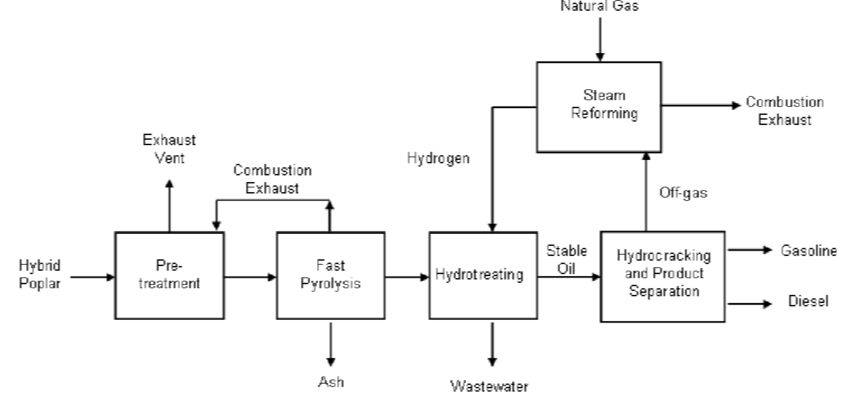
Although hydrocracking and hydrotreating serve different functions, they are often integrated within the same refining system to optimize overall performance and product quality.
- Hydrotreating is often used before hydrocracking to remove sulfur, nitrogen, and other impurities from the feedstock. This step is crucial because impurities can degrade the performance of hydrocracking catalysts and reduce their lifespan.
- Once hydrotreating has purified the feed, hydrocracking further enhances the quality of the products by breaking down heavier hydrocarbons into lighter, more valuable fuels and chemicals. This two-step process ensures that the end products meet strict environmental and performance standards.
- Together, these processes provide refineries with the flexibility to handle a wide range of crude oils and feedstocks, optimizing yields and minimizing waste. The combination also allows for more efficient use of hydrogen, as hydrotreating reduces the need for excessive hydrogen consumption in subsequent stages.
By working together, hydrocracking and hydrotreating enable refineries to produce cleaner, higher-quality fuels while maintaining operational efficiency and meeting environmental regulations.
To Sum Up
Hydrocracking and hydrotreating are essential hydroprocessing techniques in contemporary petroleum refining. Hydrocracking primarily aims to break down heavy hydrocarbons into lighter, more valuable products, whereas hydrotreating focuses on purifying feedstocks by eliminating impurities. Together, these processes work in tandem to enhance operational efficiency, improve product quality, and ensure compliance with environmental standards, making them crucial components of the refining industry.