Hydrotreating Process in Renewable Diesel Production
As the global transition towards cleaner energy intensifies, renewable diesel has become a key solution for reducing greenhouse gas emissions and decreasing dependence on fossil fuels. Unlike conventional biodiesel, renewable diesel delivers enhanced performance, higher energy density, and superior compatibility with existing diesel engines and infrastructure. Its production hinges on advanced refining techniques, with hydrotreating serving as a critical technology. This process is essential for transforming renewable feedstocks into high-quality, sustainable diesel fuel.
Deep Look into Hydrotreating Process
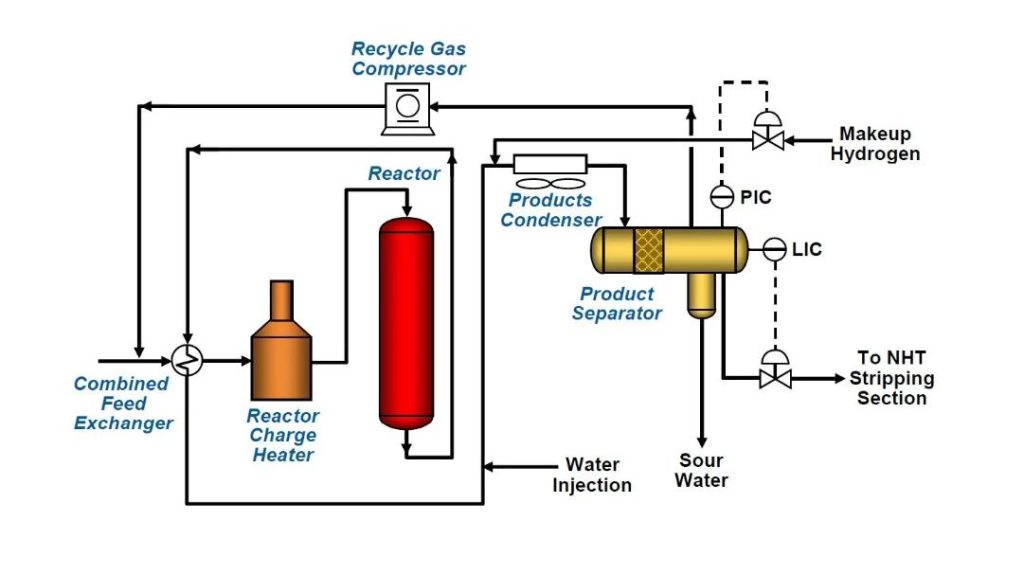
In the case of renewable diesel production, hydrotreating is crucial for converting vegetable oils, animal fats, and waste oils into high-quality, hydrocarbon-based fuels. It involves the addition of hydrogen to the feedstock under high pressure and temperature conditions, which leads to the removal of unwanted elements and the conversion of triglycerides into paraffinic hydrocarbons.
Key Reactions Involved in Hydrotreating Process
The hydrotreating process involves a series of crucial chemical reactions that transform feedstocks into clean diesel fuel. These key reactions include:
- Hydrodeoxygenation (HDO): This reaction removes oxygen from the feedstock by converting it into water (H₂O), turning oxygenated compounds into non-oxygenated hydrocarbons. It plays a vital role in reducing oxygen content in biodiesel, improving its stability and performance.
- Hydrodesulfurization (HDS): Hydrogen is added to remove sulfur compounds, which react with hydrogen to form hydrogen sulfide (H₂S). Sulfur is a contaminant that can degrade fuel quality and engine performance, and its removal is essential for meeting stringent emission regulations.
- Hydrodenitrogenation (HDN): Nitrogen compounds are eliminated through a reaction with hydrogen, producing ammonia (NH₃). Nitrogen contaminants can cause issues like catalyst poisoning and contribute to emission-related problems in diesel engines.
- Hydrocracking: In certain cases, hydrocracking occurs during hydrotreating, where larger molecules are broken down into smaller, lighter hydrocarbons. This process improves the overall yield of high-quality diesel fuel.
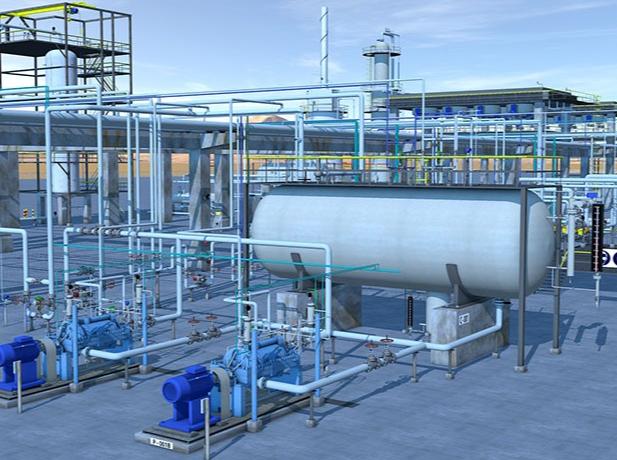
Types of Hydrotreating Catalysts in the Process
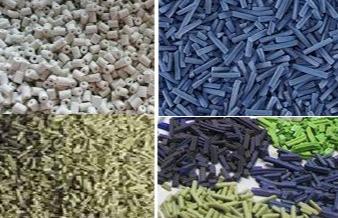
Hydrotreating catalysts are essential for enhancing the efficiency and selectivity of chemical reactions in renewable diesel production. Different types of catalysts are used depending on the feedstock and specific reaction requirements:
- Nickel-Molybdenum (Ni-Mo) Catalysts: These catalysts are commonly employed in hydrodesulfurization (HDS) and hydrodenitrogenation (HDN) reactions, where they effectively remove sulfur and nitrogen compounds from feedstocks such as animal fats and vegetable oils. By eliminating these contaminants, Ni-Mo catalysts enhance fuel quality, improving engine performance and reducing harmful emissions.
- Bifunctional Catalysts: These catalysts integrate both hydrogenation and cracking functions, enabling simultaneous reactions that improve product yield and fuel quality. They are particularly effective for processing complex feedstocksCobalt-Molybdenum (Co-Mo) Catalysts: Often used in combination with Ni-Mo catalysts, Co-Mo catalysts excel at desulfurizing heavier oils, such as those from used cooking oils or waste greases. They support both HDS and hydrodeoxygenation (HDO) processes.
- Precious Metal Catalysts (Ruthenium and Palladium-based): These catalysts are highly efficient for hydrodeoxygenation, especially when processing feedstocks with elevated oxygen content, such as algae oils and animal fats. While more expensive, they deliver exceptional performance in removing oxygen from the feedstock.
What is Renewable Diesel?
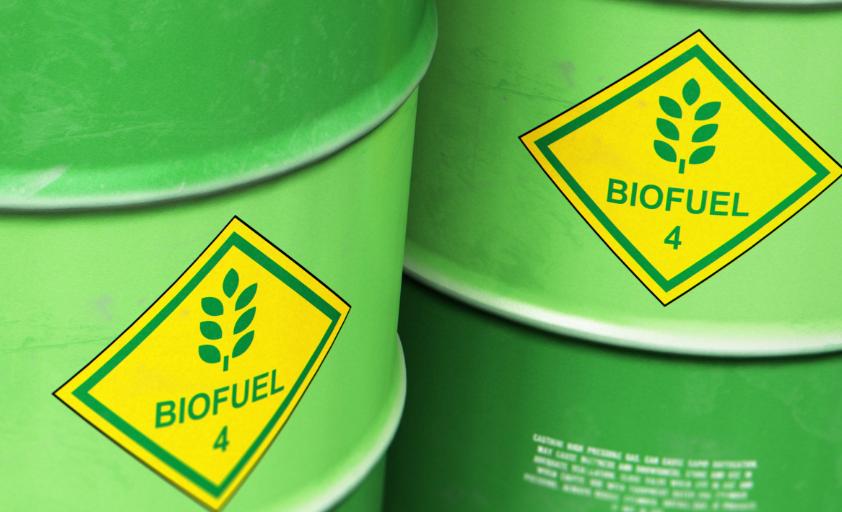
Renewable diesel is a high-quality, bio-based fuel that can directly replace traditional petroleum diesel. Unlike biodiesel, which is produced through a transesterification process, renewable diesel is made using hydrotreating technology. This method transforms renewable feedstocks such as vegetable oils, animal fats, and waste greases into hydrocarbon-based fuels that are chemically identical to fossil diesel. As a result, renewable diesel can be used in existing diesel engines and infrastructure without any modifications, making it a true “drop-in” fuel.
The primary feedstocks for renewable diesel production include:
- Vegetable oils (e.g., soybean, canola, palm)
- Animal fats (e.g., tallow, lard)
- Used cooking oils
- Algae oils
Renewable diesel presents multiple advantages over traditional diesel and biodiesel. It boasts higher energy density, superior cold-flow properties, and enhanced compatibility with diesel engines. Additionally, it generates fewer greenhouse gas emissions during both production and combustion compared to fossil diesel, positioning it as a more sustainable alternative. These qualities make renewable diesel a vital solution for lowering the carbon footprint of the transportation and energy sectors, supporting the shift toward a more sustainable energy system.
Importance of Hydrotreating Process in Renewable Diesel Production
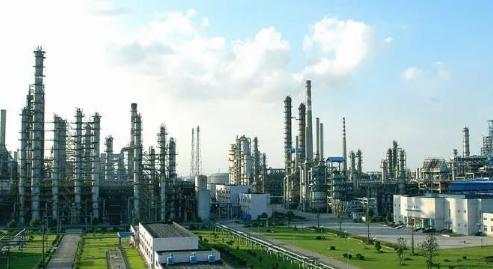
The hydrotreating process is a cornerstone technology in the production of renewable diesel, playing a critical role in converting renewable feedstocks into high-quality, sustainable diesel fuel. Here are the key reasons why hydrotreating is essential for renewable diesel production:
- Enhances Fuel Quality: Hydrotreating eliminates impurities like oxygen, sulfur, nitrogen, and metals from feedstocks, converting them into high-quality, non-oxygenated hydrocarbons. This improves the stability, performance, and combustion characteristics of renewable diesel.
- Improves Compatibility with Existing Infrastructure: Hydrotreating produces a “drop-in” fuel, allowing renewable diesel to replace fossil diesel in current diesel engines and infrastructure without requiring modifications. This makes it a convenient and immediate solution for adoption.
- Ensures Compliance with Emission Standards: By utilizing processes such as hydrodesulfurization (HDS) and hydrodenitrogenation (HDN), hydrotreating efficiently removes sulfur and nitrogen compounds. This ensures that renewable diesel meets strict environmental regulations and reduces emissions, contributing to cleaner air quality.
- Supports Feedstock Flexibility: Hydrotreating allows the use of a wide range of renewable feedstocks, including vegetable oils, animal fats, and waste oils. This flexibility enables the production of renewable diesel from diverse and sustainable sources, reducing reliance on any single feedstock.
- Boosts Yield of High-Quality Diesel: The hydrotreating process, including hydrocracking, breaks down larger molecules into smaller, lighter hydrocarbons, optimizing the output of high-quality diesel. This leads to improved energy density and better cold-flow properties, making renewable diesel more efficient across different environmental conditions.
Hydrotreating Plants Used for Hydrotreating Process
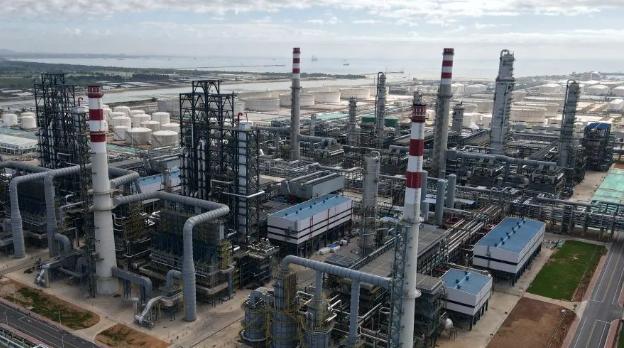
Hydrotreating takes place in specialized facilities called hydrotreating units or reactors, which are engineered to handle the intricate reactions involved in transforming feedstocks into renewable diesel. These plants are designed to withstand high-pressure and high-temperature environments, facilitating the hydrogenation and catalytic processes necessary to remove impurities such as sulfur, nitrogen, and oxygen.
Key components of a hydrotreating plant include:
- Hydrotreating Reactors: The heart of the plant, where feedstock and hydrogen are introduced under high pressure and temperature. These reactors typically feature fixed-bed or trickle-bed designs, with catalysts placed inside to drive the necessary chemical reactions.
- Hydrogen Supply Unit: This unit provides a continuous, high-pressure hydrogen supply, essential for the hydrotreating process. It ensures the availability of sufficient hydrogen, which is crucial for maintaining the process’s efficiency and effectiveness.
- Catalyst Management: Catalysts in hydrotreating units can lose effectiveness over time due to contamination or deactivation. To sustain optimal performance and efficiency, plants implement catalyst regeneration or replacement systems.
- Separation and Purification Units: Following the hydrotreating reactions, the product is processed through separation and purification stages to remove impurities such as hydrogen sulfide and excess hydrogen. This ensures the final fuel complies with quality standards.
These plants are critical in ensuring a steady and high-quality output of renewable diesel, which is crucial for meeting the increasing demand for sustainable fuel alternatives.
In Summary
The hydrotreating process is crucial for transforming renewable feedstocks into high-quality renewable diesel, effectively removing impurities and producing cleaner fuel. Utilizing advanced catalysts and specialized hydrotreating plants, this process results in a sustainable, “drop-in” diesel that is fully compatible with existing infrastructure. As the demand for renewable energy increases, hydrotreating will continue to be a vital technology driving the future of green fuel production.