Lube Oil Blending Plants: From Tradition to Automation
Lubricating oil, the lifeblood of machinery, plays a critical role in minimizing friction and wear, thereby extending the lifespan of equipment across various industries. Lube oil blending plants are the unsung heroes behind this essential product, meticulously formulating and processing lubricants to meet specific performance demands. This article explores the world of lubricating oil blending plants, delving into their functions, historical evolution, and the increasing integration of automation into their processes.
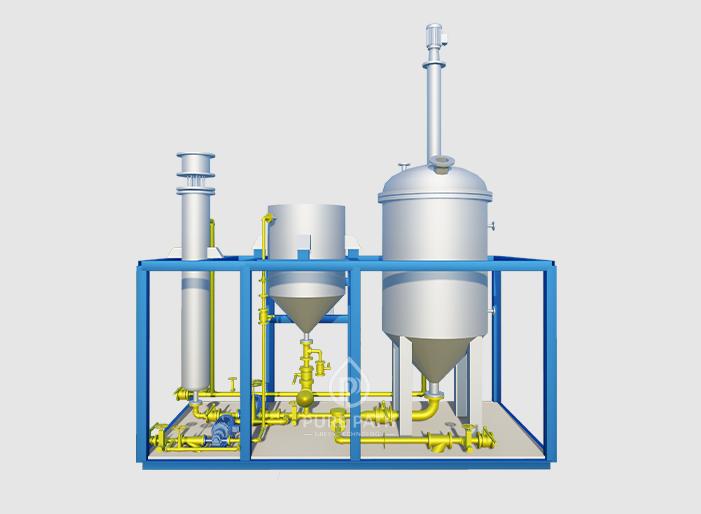
Functions of Lube Oil Blending Plants
Lubricating oil blending plants serve a vital purpose in the industrial landscape. These facilities specialize in the precise blending and processing of base oils and additives to create finished lubricants. Base oils, the foundation of any lubricant, are derived from crude oil and can be synthetic or mineral-based. Additives, on the other hand, are specific chemical compounds that enhance the performance characteristics of base oils. By combining these elements in carefully formulated ratios, blending plants create lubricants tailored to the specific needs of various applications.
The primary functions of lubricating oil blending plants include:
- Blending and Processing: Using specialized equipment and following established formulations, blending plants precisely combine base oils and additives to create the desired lubricant properties. This process involves meticulous measurement and efficient mixing to ensure homogeneity throughout the final product.
- Meeting Specific Requirements: Lubricants are not a one-size-fits-all solution. Different machinery and applications have varying requirements in terms of viscosity, anti-wear properties, and resistance to extreme temperatures. Blending plants cater to these diverse needs by formulating lubricants that meet the specific performance criteria of each application.
- Ensuring Smooth Operation: By providing lubricants that effectively reduce friction and wear, blending plants contribute significantly to the smooth operation of machinery and equipment. This translates to extended equipment lifespans, reduced downtime, and improved overall efficiency across industries.
- Quality Control and Environmental Compliance: Maintaining stringent quality control measures is paramount for blending plants. Rigorous testing ensures that the produced lubricants meet the required specifications and performance standards. Additionally, blending plants adhere to environmental regulations by implementing responsible waste management practices and minimizing their environmental footprint.
The Evolution of Lube Oil Blending Plants
The history of lubricating oil blending plants mirrors the evolution of the lubrication industry itself. In the early days, blending processes were primarily manual or semi-automated. This involved manual calculations, imprecise measurements, and a greater reliance on human intervention. While these methods sufficed for the rudimentary needs of the time, they lacked the accuracy and efficiency required by modern industrial applications.
The latter half of the 20th century witnessed a significant shift towards automation in lubricating oil blending plants. The introduction of highly automated production equipment and sophisticated control systems revolutionized the industry. These advancements led to several key benefits:
- Enhanced Precision: Automated systems with advanced metering devices ensure precise measurement of base oils and additives, guaranteeing consistent and accurate blending ratios in every batch.
- Improved Efficiency: Automation streamlines the blending process, leading to increased production capacity and faster turnaround times.
- Reduced Human Error: Automated systems minimize the potential for human error during the blending process, leading to a more consistent and reliable product.
- Enhanced Quality Control: Integration of automated quality control checks within the blending process allows for real-time monitoring and ensures that the final product adheres to stringent quality standards.
The continuous advancements in automation technology pave the way for even smarter and more efficient blending processes in the future.
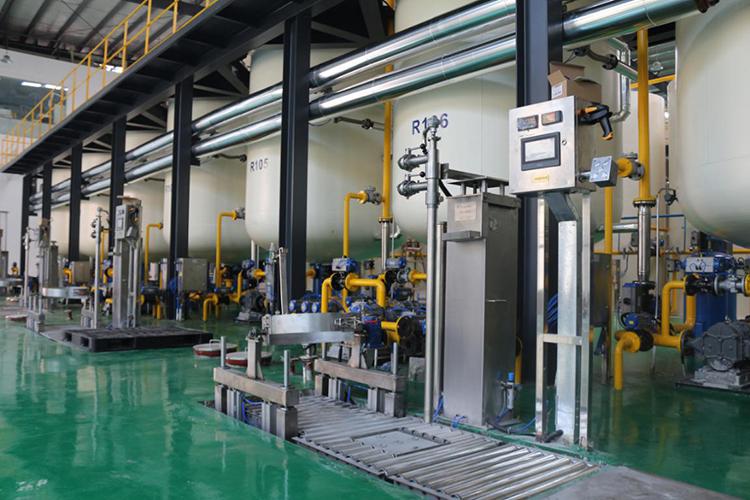
Lubricating Oil Blending Automation Technologies
Lubricating oil blending automation plays a pivotal role in modern production processes. It ensures precise measurements, efficient mixing, and consistent product quality. Here’s a closer look at the key technological aspects of lubricating oil blending automation:
- Precise Measurement: Accurate blending ratios are critical for achieving the desired performance characteristics in the final lubricant. Blending automation employs high-precision flow meters and other metering devices to ensure that base oils and additives are combined in exact proportions.
- Automatic Control: Programmable logic controllers (PLCs) or other automated control systems form the backbone of modern blending plants. These systems meticulously regulate the entire blending process, from ingredient metering to mixing speed and duration. This level of control allows for real-time adjustments and ensures consistent product quality.
- Information Management: Modern blending plants leverage information technology for intelligent management and tracking. Enterprise Resource Planning (ERP) systems or similar software solutions automate tasks like production planning, work order execution, and material inventory management. This integration of data allows for efficient resource allocation and improved production transparency.
- Intelligent Equipment: The use of intelligent blending vessels and high-speed filling lines represents another advancement in blending automation. These intelligent systems can adapt to variations in base oil viscosity and temperature, ensuring accurate and efficient blending and filling operations.
Lubricating Oil Automatic Quantitative Filling Technology
Automatic quantitative filling technology plays a crucial role in the final stage of the lubricating oil blending process. This technology ensures that the precisely formulated lubricant is dispensed into containers with exact and consistent volume.
The Significance of Precision
Inaccurate filling can have detrimental consequences. Overfilling containers leads to product waste and increased costs. Underfilling, on the other hand, compromises the effectiveness of the lubricant and can potentially damage machinery due to insufficient lubrication. Automatic quantitative filling technology eliminates these concerns by guaranteeing precise and consistent filling across every container.
Working Principle
The core of automatic quantitative filling technology lies in the utilization of high-precision metering devices. These devices can include:
- Flow Meters: These instruments measure the volumetric flow rate of the lubricant, ensuring the correct volume is dispensed into each container.
- Mass Flow Meters: By measuring the mass of the lubricant passing through the system, these meters provide an even more accurate filling solution, especially for lubricants with varying densities.
- Volumetric Positive Displacement Pumps: These pumps deliver a specific volume of lubricant with each cycle, guaranteeing consistent filling regardless of the lubricant’s viscosity.
These metering devices operate in conjunction with a control system that regulates the filling process. The control system receives pre-programmed data specifying the desired filling volume for each container size. Based on this information, the system controls the operation of the metering device and ensures the precise amount of lubricant is dispensed.
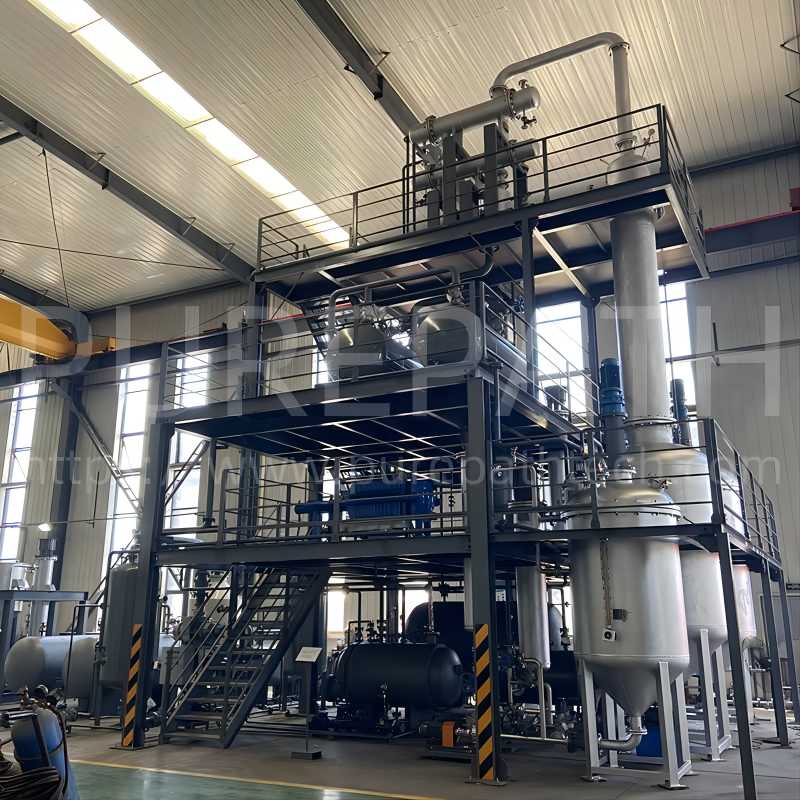
Applications and Benefits
Automatic quantitative filling technology finds widespread application across various industries that rely on lubricants, including:
- Automotive Industry: Ensuring accurate filling of engine oil, transmission fluid, and other automotive lubricants is crucial for optimal vehicle performance and fuel efficiency.
- Mechanical Equipment: Machinery used in construction, manufacturing, and other sectors requires precise lubrication for smooth operation and extended lifespan. Automatic filling guarantees consistent lubricant application in these machines.
- Industrial Production: Lubrication plays a vital role in various industrial processes. Automatic filling technology ensures consistent and efficient dispensing of lubricants across production lines.
- The benefits of automatic quantitative filling technology extend beyond just precision:
- Increased Efficiency: Automated filling significantly reduces the time and labor required compared to manual methods, leading to increased production throughput.
- Reduced Waste: Precise filling minimizes product giveaways, thereby reducing costs and environmental impact.
- Improved Consistency: Automatic filling ensures consistent volume across all containers, guaranteeing reliable performance of the lubricant in its intended application.
The Evolving Equipment Landscape
Lubricating oil blending plants utilize a range of equipment within the automatic quantitative filling system:
- Storage Tanks: These tanks house the finished lubricant after the blending process and serve as a reservoir for the filling operation.
- Metering Devices: As mentioned earlier, flow meters, mass flow meters, or volumetric positive displacement pumps form the core of the filling system, ensuring precise measurement.
- Filling Actuators: These actuators control the opening and closing of valves, regulating the flow of lubricant into the containers.
- Sensors and Control Systems: Sensors monitor various parameters like lubricant level and container weight, while the control system integrates with the metering devices and actuators to orchestrate the entire filling process.
Operational Procedures
The operation of an automatic quantitative filling system typically involves several key steps:
- Oil Preparation: The finished lubricant from the blending process is transferred to designated storage tanks for the filling operation.
- Metering: The chosen metering device precisely measures the pre-programmed volume of lubricant for each container size.
- Filling: The metered lubricant is dispensed into the container through a filling nozzle. The filling process may involve multiple stages for larger containers to minimize air entrapment within the lubricant.
- Inspection and Recording: Filled containers undergo automated or manual inspection to ensure they meet the required weight or volume specifications. Additionally, data related to the filling process may be recorded for quality control purposes.
Performance Testing and Verification
Maintaining high performance standards for automatic quantitative filling equipment is crucial. Regular testing and verification procedures ensure the accuracy and consistency of the filling process. These procedures may include:
- Calibration of Metering Devices: Flow meters, mass flow meters, and volumetric pumps are periodically calibrated using reference standards to guarantee their accuracy.
- Leakage Detection: Filling systems are inspected for leaks that could compromise the dispensed volume or contaminate the lubricant.
- Sample Testing: Periodically, lubricant samples from filled containers are weighed or measured to verify that the actual volume matches the programmed settings.
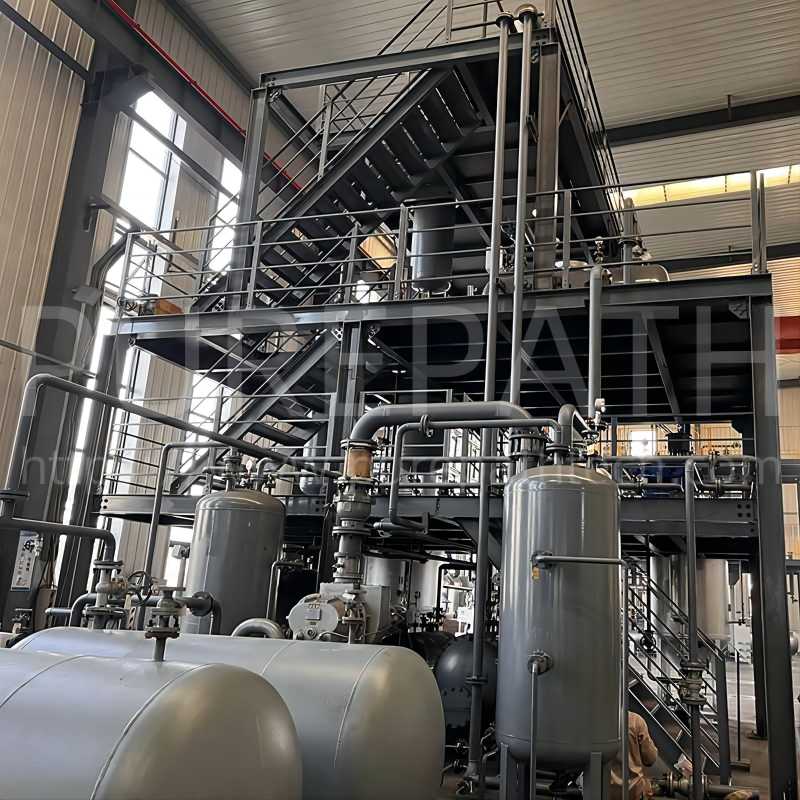
Future Development Trends
The future of lubricating oil blending automation is primed for further advancements, focusing on achieving even higher precision, efficiency, cost-effectiveness, and environmental sustainability. Here are some key trends shaping the future of this technology:
- Enhanced Intelligence: The integration of artificial intelligence (AI) and big data analytics will lead to smarter blending and filling systems. AI-powered systems can continuously learn and optimize blending processes based on real-time data, ensuring consistent quality and minimizing the risk of errors. Big data analytics can be used to identify patterns and predict potential issues within the blending and filling system, allowing for proactive maintenance and minimizing downtime.
- Green and Sustainable Practices: As environmental concerns take center stage, the lubricating oil blending industry will prioritize eco-friendly practices. This may involve:
- Utilizing biodegradable lubricants: The use of environmentally friendly base oils and additives will minimize the environmental impact of lubricants throughout their lifecycle.
- Minimizing waste: Implementing closed-loop systems for waste oil and solvent recovery will reduce the environmental footprint and potentially create opportunities for reusing these materials.
- Optimizing energy consumption: Utilizing energy-efficient equipment and processes will reduce the overall environmental impact of blending plant operations.
- System Integration: Future blending plants will likely witness a higher degree of system integration. This could involve:
- End-to-End Automation: Integrating the entire production process, from raw material intake to finished product packaging, will further enhance efficiency and minimize human intervention.
- Real-time Data Tracking: Implementing a robust data management system will allow for real-time monitoring of all production stages, enabling operators to make informed decisions and optimize overall performance.
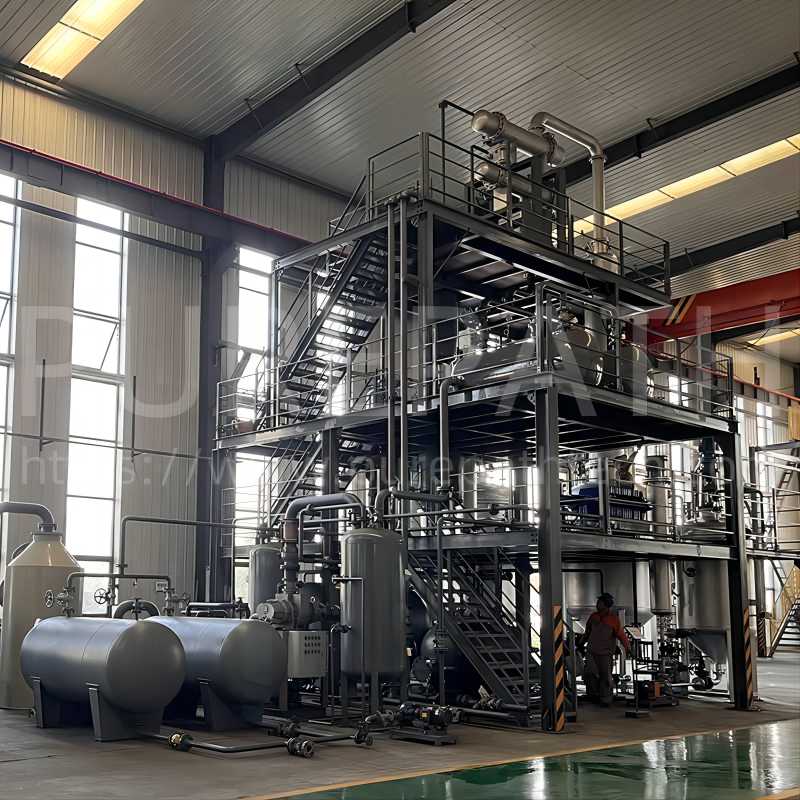
Conclusion
Lube oil blending plants play a critical role in ensuring the smooth operation of machinery across various industries. With the increasing sophistication of automated systems, these facilities are poised to deliver even higher levels of precision, efficiency, and environmental responsibility in the years to come. As the demand for high-performance lubricants continues to grow, advancements in blending automation will be instrumental in meeting the evolving needs of modern industrial applications.