Lubricant Blending Plants: The Precision Behind Lubrication Excellence
In the world of industrial machinery and automotive engines, the unsung heroes that ensure everything runs smoothly are lubricants. These essential fluids are the lifeblood of machinery, responsible for reducing friction and wear, dissipating heat, and extending the lifespan of moving parts. But what goes into creating the perfect lubricant for a specific application? The answer lies in the lubricant blending plant and the intricate lube oil blending process. In this comprehensive article, we will delve into the world of lubricant blending plants, exploring their major components, the lube oil blending process, and the critical role they play in industries worldwide.
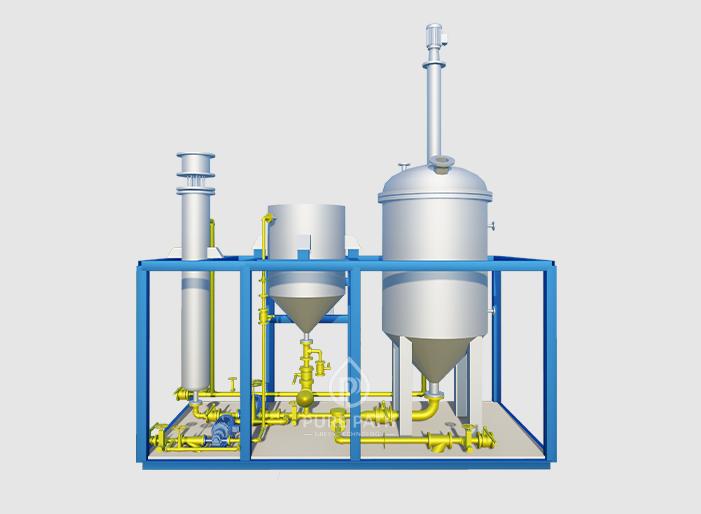
Why is It Important to Blend Lubricants?
There are several reasons why it is important to blend lubricants:
- To improve the performance of lubricants in specific applications. Additives can be used to improve the viscosity, wear protection, oxidation resistance, and other properties of lubricants. This allows lubricant blenders to create lubricants that are specifically designed for different applications, such as automotive engines, industrial machinery, and food processing equipment.
- To meet the requirements of different customers. Customers have different requirements for lubricants, depending on the specific application. For example, some customers may require lubricants that are biodegradable or have a low environmental impact. Lubricant blenders can meet these requirements by blending base oils and additives in different proportions.
- To reduce costs. Blended lubricants are often more cost-effective than base oils alone. This is because lubricant blenders can purchase base oils and additives in bulk and blend them to meet the specific needs of their customers.
What is a lubricant blending plant?
A lubricant blending plant is a specialized facility where various raw materials are combined to create lubricants tailored to specific applications. These plants serve as the epicenter of precision and quality in the lubricant industry, ensuring that the final product meets the required specifications and standards.
The major components of a lubricant blending plant include:
- Storage tanks for base oils and additives: Base oils and additives are typically stored in separate tanks to prevent contamination. The tanks are typically made of steel or concrete, and they are equipped with heaters and mixers to keep the contents flowing and homogeneous.
- Blending vessels and mixers: Blending vessels and mixers are used to blend the base oils and additives together. The blending vessels are typically made of stainless steel, and they are equipped with mixers to ensure that the base oils and additives are thoroughly mixed together.
- Packaging and storage facilities: The blended lubricants are packaged in drums, pails, or containers of other sizes. The packaged lubricants are then stored in a warehouse until they are shipped to customers.
- Quality control and testing facilities: Quality control and testing facilities are used to ensure that the blended lubricants meet the required quality specifications. The tests typically performed include viscosity tests, flash point tests, and pour point tests.
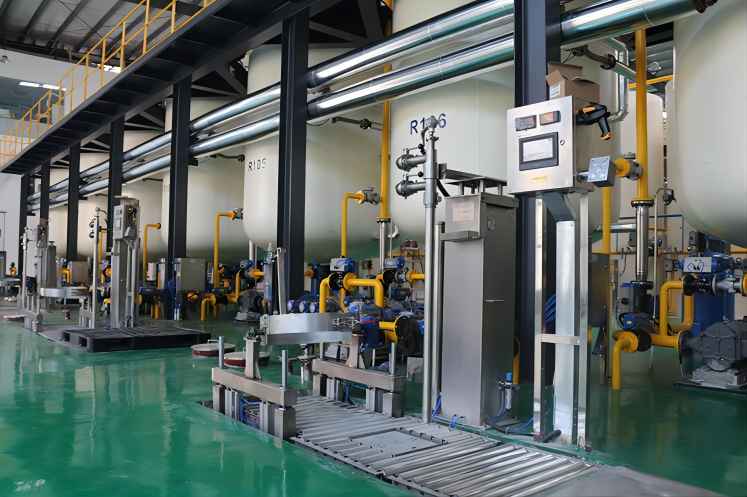
What is the lube oil blending process?
The lube oil blending process refers to the series of steps involved in creating lubricants. This process involves mixing base oils, additives, and other components in precise quantities and under controlled conditions to achieve the desired properties and performance characteristics.
The lube oil blending process can be summarized in the following steps:
- Receiving and storage of base oils and additives: Base oils and additives are received at the plant and stored in separate tanks. The base oils are typically stored in large tanks with capacities ranging from several thousand to tens of thousands of cubic meters. The additives are typically stored in smaller tanks with capacities ranging from several hundred to several thousand cubic meters.
- The blending of base oils and additives: The base oils and additives are blended together in a blending vessel. The blending vessel is typically equipped with a mixer to ensure that the base oils and additives are thoroughly mixed together. The blending process can be carried out using a variety of different methods, including batch blending, continuous blending, and hybrid blending.
- Quality control and testing of blended lubricants: Samples of the blended lubricants are taken and tested to ensure that they meet the required quality specifications. The tests typically performed include viscosity tests, flash point tests, and pour point tests. If the blended lubricants do not meet the required quality specifications, they may be rejected or reprocessed.
- Packaging and storage of blended lubricants: The blended lubricants are packaged in drums, pails, or containers of other sizes. The packaged lubricants are then stored in a warehouse until they are shipped to customers.
Types of Lubricant Blending Processes
There are three main types of lubricant blending processes: batch blending, continuous blending, and hybrid blending.
- Batch blending: Batch blending is the simplest type of lubricant blending. In batch blending, the base oils and additives are mixed together in a blending vessel. The blending process is typically completed in several hours.
- Continuous blending: Continuous blending is a more complex type of lubricant blending. In continuous blending, the base oils and additives are mixed together in a continuous mixer. The blending process is typically complete in a few minutes.
- Hybrid blending: Hybrid blending is a combination of batch blending and continuous blending. In hybrid blending, the base oils and additives are first mixed together in a batch blender. The blended lubricants are then passed through a continuous mixer to ensure that they are thoroughly mixed together.
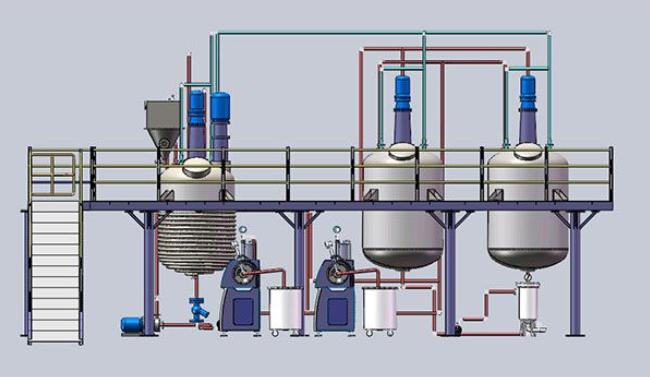
Conclusion
In conclusion, lubricant blending plants are the unsung heroes behind the machinery that drives our modern world. They ensure that the right lubricant is in the right place, at the right time, and in the right condition. Understanding the intricacies of these plants and the lube oil blending process allows us to appreciate the precision and dedication that goes into the creation of lubricants that keep our engines running smoothly. Whether in heavy industry or the family car, the work of lubricant blending plants plays an integral role in ensuring the longevity and efficiency of our machinery.