Oil Solvent Extraction vs. Traditional Refining
Obtaining high-quality base oils, the foundation of lubricants, and many industrial products rely on efficient oil extraction methods. Two primary techniques dominate the industry: traditional refining and oil solvent extraction. While both methods achieve the desired outcome, their approaches differ significantly.
Oil Solvent Extraction
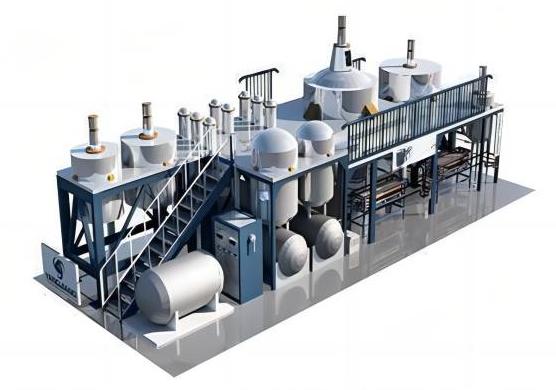
Oil solvent extraction is a modern method used to separate oil from its raw materials, such as seeds or nuts. This process involves the use of solvents—chemical compounds that dissolve substances—to extract oil efficiently and effectively. One of the most commonly used solvents in this process is hexane, due to its high solvency power and low boiling point, making it easy to recover and reuse.
The process begins by cleaning and drying the raw material to remove impurities and moisture. The cleaned material is then ground into smaller particles to increase the surface area for the solvent to act upon. The prepared material is mixed with the solvent, allowing the oil to dissolve into the solvent. The mixture is then filtered to separate the solid residue, known as meal, from the oil-solvent solution. The oil is recovered from the solution through a process called distillation, where the solvent is evaporated and condensed for reuse.
Oil solvent extraction is highly efficient, often extracting nearly 99% of the oil content from the raw material. This method is widely used in the production of vegetable oils, such as soybean, sunflower, and canola oils.
Traditional Refining
Traditional refining, also known as mechanical pressing or expeller pressing, is one of the oldest methods for extracting oil from raw materials. This process involves the physical extraction of oil through mechanical means, without the use of chemical solvents.
In traditional refining, the raw material is first cleaned and conditioned to remove impurities and excess moisture. The prepared material is then fed into an expeller, a machine that uses a screw press to crush and press the material, forcing the oil out. The extracted oil is collected and filtered to remove solid particles, resulting in a crude oil that can be further refined if necessary.
This method is known for producing high-quality oil with minimal processing, retaining more of the natural flavors and nutrients. However, traditional refining is less efficient compared to oil solvent extraction, often leaving behind a significant amount of residual oil in the meal.
Despite its lower efficiency, traditional refining remains popular for producing specialty oils, such as olive and coconut oils, where maintaining the natural characteristics of the oil is crucial.
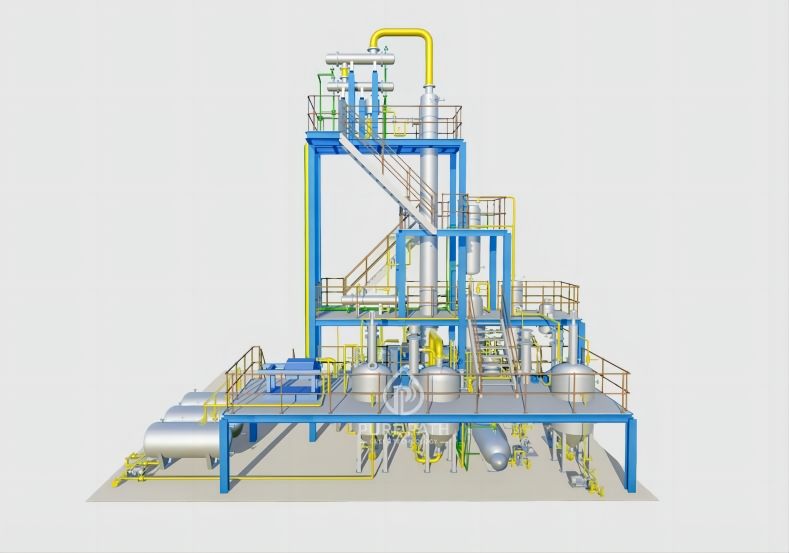
Oil Solvent Extraction vs. Traditional Refining
Both oil solvent extraction and traditional refining are effective methods for obtaining high-quality base oils, but they differ significantly in their approaches. This table provides a detailed comparison of these two processes across several key features:
Feature | Oil Solvent Extraction | Traditional Refining |
Yield | High | Moderate |
Temperature | Lower | Higher |
Processing Speed | Faster | Slower |
Energy Consumption | Lower | Higher |
Suitability for Specialty Oils | More Suitable | Less Suitable |
Environmental Impact | Can be Lower (depending on solvent and recovery methods) | Can be Higher |
Investment Costs | Can be Higher (initially) | Lower (initially) |
Operational Complexity | Moderate | Moderate to High |
Oil solvent extraction and traditional refining each offer unique advantages and disadvantages. Selecting the optimal method hinges on the specific needs of the application.
For high-yield extraction of specialty oils with heat-sensitive components, oil solvent extraction is often the preferred choice. Traditional refining remains a well-established and cost-effective method for large-scale production of base oils from various crude oil sources.
As technology advances, both methods may see further development, leading to even greater efficiency, lower environmental impact, and improved product quality.
Purepath Tech Solvent Extraction Plant
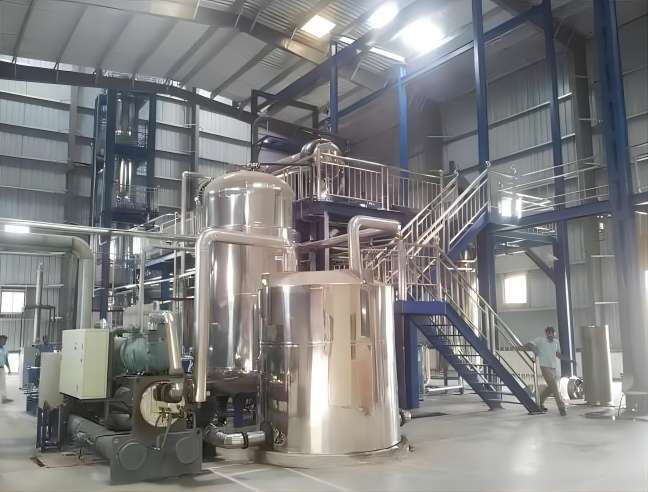
PurePath Tech offers a successful solution for recycling used oil with their PPGT-BE solvent extraction plant. This innovative technology removes impurities from used oil, transforming it into high-quality base oil, a key ingredient in lubricants. PurePath’s technology boasts significant advantages over competing methods, requiring less solvent and minimizing environmental impact.
This translates to substantial benefits for customers. By utilizing recycled base oil, PurePath’s plants contribute to environmental sustainability and resource conservation. Additionally, their efficient solvent extraction process reduces operational costs.
Here are some features of PurePath solvent extraction plant:
- Advanced Technology: PurePath Technology’s PPGT-BE Base Oil Solvent Extraction Plant utilizes a multi-stage centrifugal extraction system.
- Contaminant Removal: Effectively eliminates PAHs, gums, asphaltenes, and sulfur compounds.
- Enhanced Quality: Improves the viscosity index and oxidation stability of the oil.
- High Yield: Achieves over 98% yield of Group 1+ base oil.
- Environmental Efficiency: Designed for minimal environmental impact with innovative solvent recovery technologies.
- Applications: Suitable for refining base oils for various industrial uses.
Conclusion
Both oil solvent extraction and traditional refining have distinct advantages and challenges. Oil solvent extraction excels in efficiency and cost-effectiveness, making it suitable for large-scale production. Traditional refining, though less efficient, produces high-quality oils with natural flavors and nutrients, ideal for specialty oils. The choice between these methods depends on the type of oil, desired quality, production scale, and environmental considerations. PurePath Technology’s solvent extraction plant exemplifies innovation in this field, offering a highly efficient and environmentally friendly solution for base oil refining.
For more information, please contact PurePath.