Pyrolysis Oil to Diesel: A Path To Sustainable Fuels
The transportation sector is a major contributor to global greenhouse gas emissions, and finding alternative fuels is crucial for mitigating climate change. Pyrolysis oil to diesel technology presents a promising approach by converting waste materials into a fuel compatible with existing diesel engines. This article explores the potential of pyrolysis oil to diesel technology, examining the equipment involved, technical challenges, and its viability as a replacement for conventional diesel.
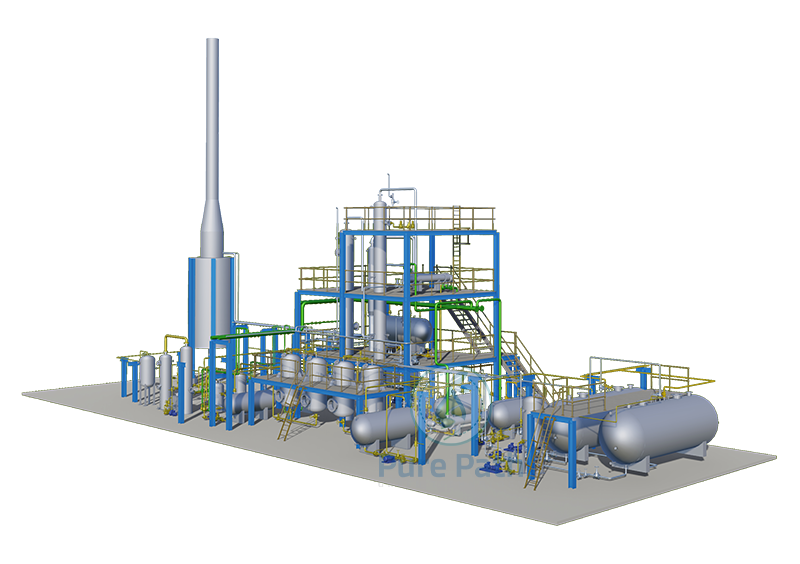
Understanding the Pyrolysis Oil to Diesel Technology
Pyrolysis oil to diesel technology utilizes a thermochemical process called pyrolysis to convert organic materials, such as waste plastics, used tires, and biomass, into a bio-oil known as pyrolysis oil. This oil can then be further upgraded through various refining processes to produce a diesel-like fuel. Compared to traditional diesel derived from crude oil, pyrolysis oil to diesel offers several potential benefits:
- Waste utilization: Pyrolysis oil to diesel technology provides a valuable pathway for waste management by diverting plastic waste, used tires, and biomass from landfills, thereby reducing environmental pollution and promoting a more circular economy.
- Reduced emissions: Depending on the feedstock used, pyrolysis oil to diesel can potentially lead to lower greenhouse gas emissions compared to traditional diesel. Biomass-derived pyrolysis oil to diesel, for instance, can contribute to a closed carbon loop where the released CO2 during combustion was previously captured from the atmosphere by the biomass feedstock.
Common Equipment Used in Pyrolysis Oil to Diesel Technology
The process of converting pyrolysis oil to diesel involves several stages, each requiring specific equipment to ensure efficiency and effectiveness. Here are some of the most common pieces of equipment used in this technology:
- Pyrolysis Reactor: The pyrolysis reactor is the heart of the process, where the thermal decomposition of biomass or plastic waste occurs. This reactor operates at high temperatures, typically between 300°C and 600°C, in an oxygen-free environment. The type of reactor used can vary, with common types including fixed-bed, fluidized-bed, and rotary kiln reactors. Each type has its advantages and is chosen based on the specific requirements of the process.
- Condensers: After pyrolysis, the gaseous products are cooled and condensed into liquid form. Condensers play a crucial role in this phase, converting vapors into pyrolysis oil. The efficiency of condensers directly impacts the yield and quality of the pyrolysis oil produced.
- Fractionating Column: This equipment is used for the distillation of pyrolysis oil. The fractionating column separates the oil into different fractions based on boiling points. The goal is to isolate the diesel fraction from other components like naphtha, kerosene, and heavy oils. This separation is essential for obtaining a product that meets the specifications for diesel fuel.
- Hydrotreating Unit: The hydrotreating unit is used to improve the quality of the diesel fraction. It involves the removal of impurities such as sulfur, nitrogen, and oxygen compounds through hydrogenation. This step enhances the stability, calorific value, and combustion characteristics of the diesel.
- Catalytic Cracking Unit: In some processes, a catalytic cracking unit is employed to break down larger hydrocarbon molecules into smaller ones, further refining the pyrolysis oil into diesel. This unit uses a catalyst to facilitate the cracking process, increasing the yield of diesel-range hydrocarbons.
- Storage Tanks: Storage tanks are necessary for holding raw materials, intermediate products, and the final diesel product. These tanks are designed to prevent contamination and degradation of the stored substances.
- Heating Systems: Efficient heating systems are critical in maintaining the required temperatures in various stages of the process. These systems ensure that the thermal conditions for pyrolysis and subsequent refining steps are met.
- Cooling Systems: Cooling systems, including water and air coolers, are essential for managing temperatures during condensation and hydrotreating. Proper cooling is crucial to maintaining process efficiency and safety.
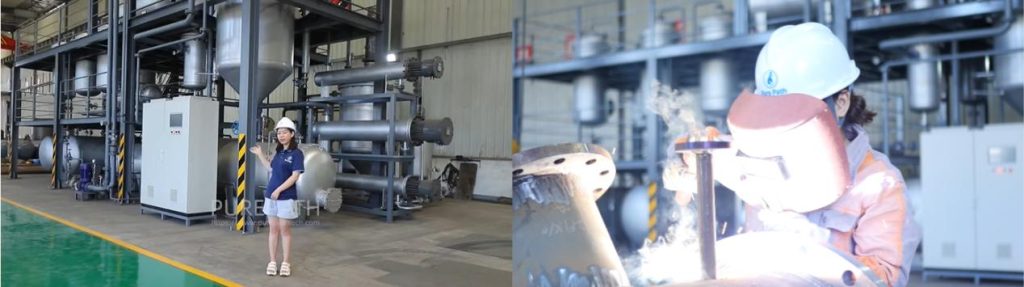
Technical Challenges in Pyrolysis Oil to Diesel
Despite the potential benefits, converting pyrolysis oil to diesel presents several technical challenges:
- Feedstock Variability: The quality and composition of the feedstock significantly impact the pyrolysis process and the quality of the resulting oil. Biomass and plastic wastes can vary widely in their chemical makeup, which affects the consistency and efficiency of the conversion process. Addressing this variability requires robust feedstock preprocessing and selection strategies.
- Impurities in Pyrolysis Oil: Pyrolysis oil contains various impurities, including oxygenates, sulfur, nitrogen, and ash. These impurities can hinder the hydrotreating process and affect the quality of the final diesel product. Effective removal of these contaminants is essential but challenging.
- Catalyst Deactivation: Catalysts used in the hydrotreating and catalytic cracking units are prone to deactivation due to coking, poisoning by impurities, and thermal degradation. Maintaining catalyst activity and longevity requires careful management and periodic regeneration or replacement, adding to the operational complexity and cost.
- Energy Consumption: The pyrolysis process is energy-intensive, requiring significant amounts of heat. The energy consumption in heating, cooling, and hydrotreating processes can impact the overall economic viability and environmental sustainability of the technology. Optimizing energy use and integrating renewable energy sources can help mitigate these issues.
- Product Yield and Quality: Achieving high yields of diesel-range hydrocarbons with desirable properties (e.g., cetane number, viscosity, and sulfur content) is challenging. The process conditions, reactor design, and catalyst choice all influence the yield and quality of the final product. Continuous optimization and innovation are necessary to meet stringent fuel standards.
- Scalability: Scaling up the pyrolysis oil to diesel process from laboratory or pilot scale to commercial scale involves significant technical and economic hurdles. Ensuring consistent performance, managing larger volumes of feedstock, and maintaining product quality are key challenges that need to be addressed.
- Environmental Impact: Managing the environmental impact of the process, including emissions and waste disposal, is critical. Pyrolysis and refining processes can generate pollutants that need to be controlled through appropriate treatment systems. Ensuring compliance with environmental regulations is essential for sustainable operations.
Can Pyrolysis Oil to Diesel Replace Conventional Diesel?
While pyrolysis oil to diesel cannot be directly used as a substitute for conventional diesel in existing engines due to differences in properties like viscosity and cetane number (a measure of ignition quality), refined pyrolysis oil to diesel offers significant potential as a replacement fuel.
- Properties and Performance: Upgraded pyrolysis oil to diesel exhibits properties similar to conventional diesel in terms of energy density, making it a viable alternative for powering diesel engines. Additionally, depending on the feedstock used, pyrolysis oil to diesel can potentially have lower emissions of particulate matter and sulfur oxides compared to traditional diesel.
- Environmental Benefits: The use of pyrolysis oil to diesel can contribute to a reduction in greenhouse gas emissions, particularly when using biomass-derived feedstock. Additionally, pyrolysis oil to diesel technology offers a valuable waste management solution by diverting waste materials from landfills.
- Economic Considerations: The economic viability of pyrolysis oil to diesel technology depends on several factors, including the cost of feedstock, processing costs, and infrastructure development. While the technology is still under development, advancements in process efficiency and cost reduction are ongoing, making pyrolysis oil to diesel a potentially competitive alternative in the long run.
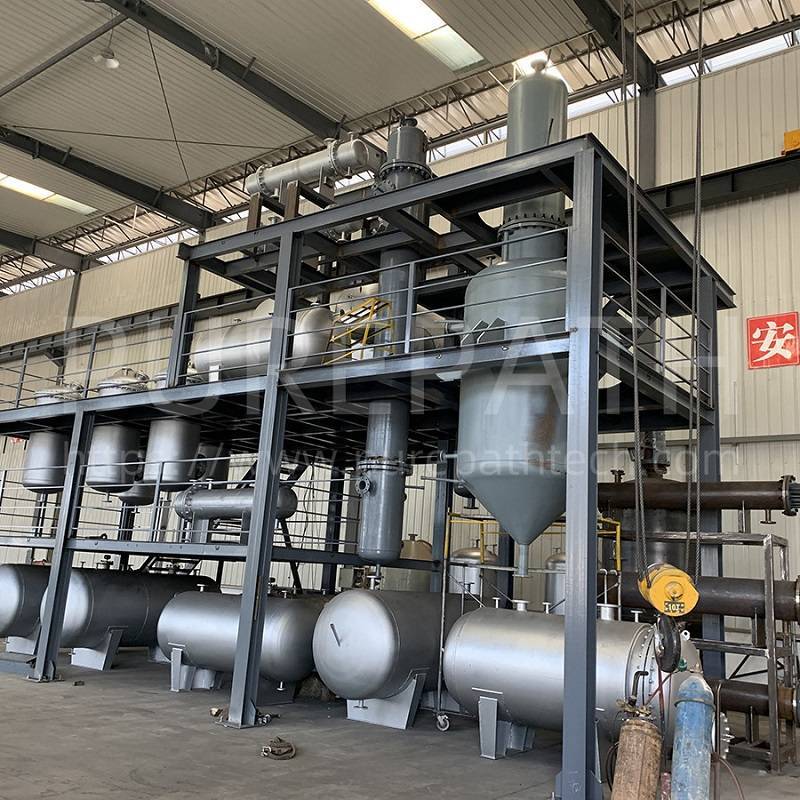
Conclusion
Converting pyrolysis oil to diesel presents a promising pathway for producing renewable and sustainable fuels. The technology involves a series of complex processes and equipment, each with its own challenges. Overcoming technical hurdles such as feedstock variability, impurity removal, catalyst deactivation, and energy consumption is crucial for the successful implementation of this technology.
While there are significant challenges, the potential benefits of pyrolysis oil-based diesel, including environmental sustainability and reduced dependence on fossil fuels, make it a compelling alternative. Achieving economic viability, ensuring product quality, and developing supportive policies and infrastructure are key to realizing the full potential of this technology. With continued research, innovation, and collaboration, pyrolysis oil-based diesel could become a viable and significant contributor to the global energy landscape.