Re-Refining Used Oil: A Sustainable Approach to Lubricant Management
Every year, millions of gallons of used motor oil are generated from vehicles and industrial machinery. Improper disposal of this oil can have serious environmental consequences, contaminating soil and water sources. Thankfully, re-refining used oil offers a sustainable solution, transforming it back into high-quality lubricant. This article explores the process of used oil re-refining, its benefits for the environment, and the applications of re-refined lubricating oil.
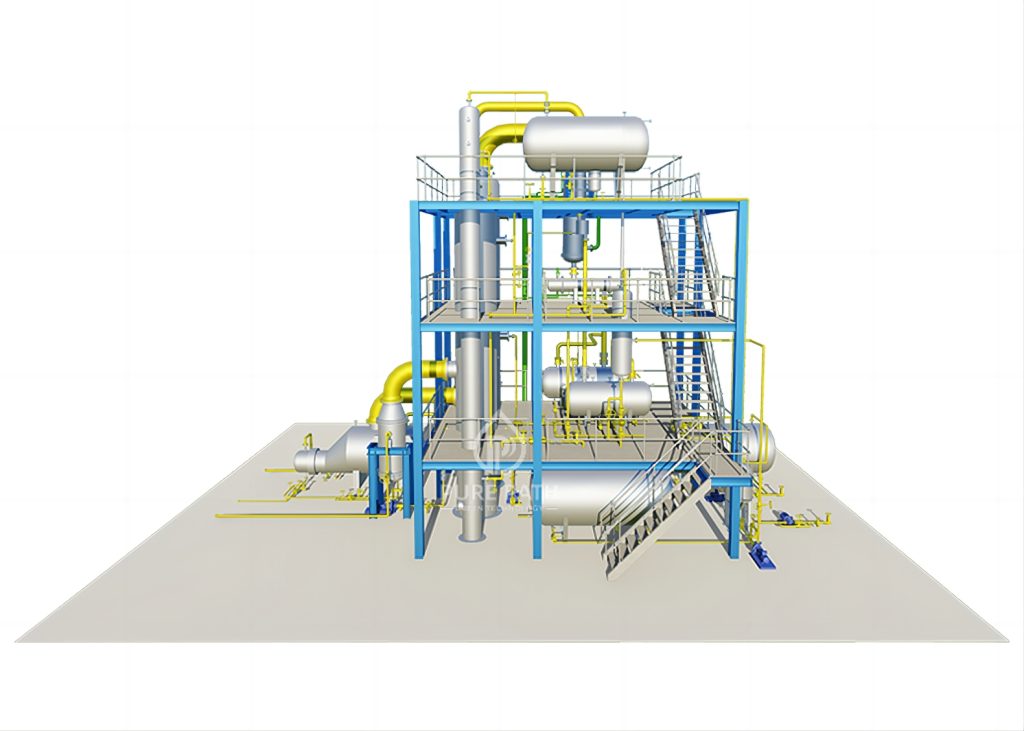
What is Used Oil Re-Refining?
Unlike recycling, which breaks down materials into basic components for new products, re-refining specifically targets the valuable lubricating properties remaining in used oil. During engine operation, oil picks up contaminants like dirt, metal shavings, and combustion byproducts. Re-refining removes these impurities, restoring the oil’s lubricating base oil to a near-virgin state. This process offers significant environmental and economic advantages compared to traditional used oil management practices, such as burning it as fuel.
Benefits of Re-Refining Used Oil
One of the most significant benefits of re-refining used oil is the conservation of virgin crude oil, a non-renewable resource. The re-refining process extracts the base oil from used oil, which can then be blended with additives to create new high-quality lubricants. This reduces the need to extract and refine virgin crude oil, a process that consumes significant energy and can have a negative impact on the environment.
Re-refining also offers environmental benefits by minimizing waste and reducing greenhouse gas emissions. Burning used oil as fuel releases harmful pollutants into the atmosphere. Re-refining, on the other hand, utilizes a closed-loop system, significantly reducing air and water pollution compared to traditional disposal methods. Studies indicate that re-refining used oil can achieve energy savings of up to 80% compared to virgin crude oil refining.
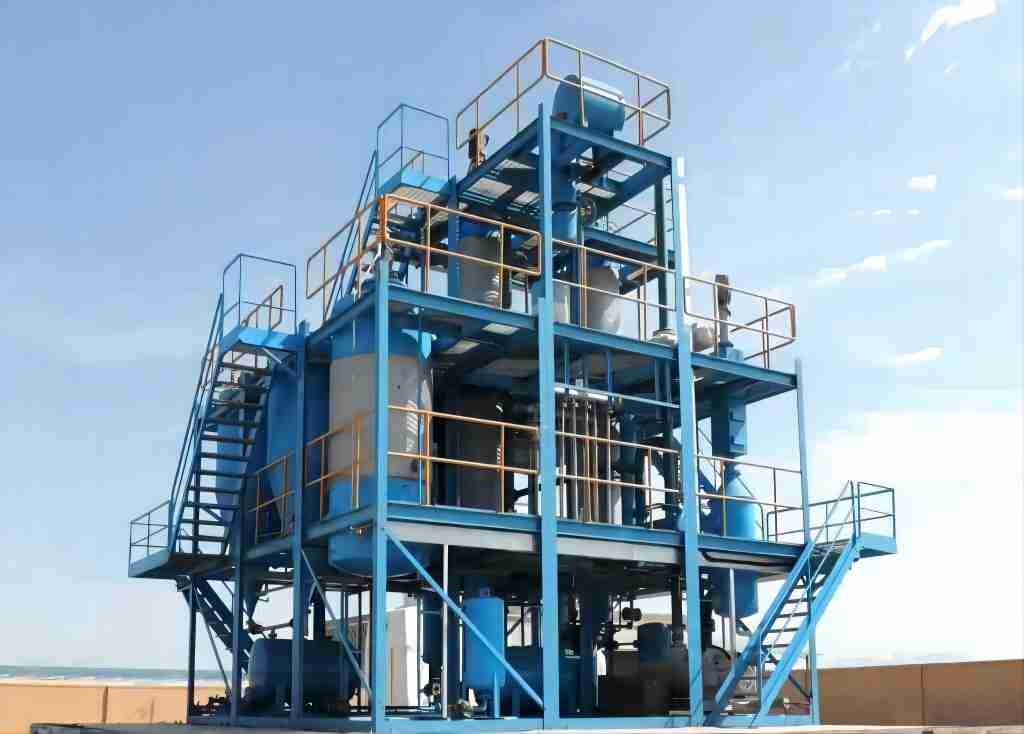
A Step-by-Step Process of Re-refining Used Oil
Used oil re-refining involves a series of meticulous steps to remove impurities and restore the oil’s lubricating properties. Let’s delve into the key stages of this process:
- Collection and Transportation: The process begins with the collection of used oil from various sources, including automotive service centers, industrial facilities, and do-it-yourself oil changers. Specialized collection facilities gather the used oil and transport it to the re-refinery in designated containers to prevent spills and leaks.
- Pre-treatment: Upon arrival at the re-refinery, the used oil undergoes pre-treatment to remove large particles and contaminants like water. This stage typically involves filtration, settling, and sometimes centrifugation to separate the usable oil from heavier impurities and residual water.
- Distillation and Separation: The pre-treated oil then enters a distillation unit. Here, the oil is subjected to high temperatures under a vacuum environment. This process separates the oil into various fractions based on their boiling points. The desired fraction is the base oil, the primary component for new lubricating oil.
- Hydrotreating: The base oil obtained from distillation still contains some impurities and residual additives from its previous use. To achieve high-quality lubricating oil, the base oil undergoes hydrotreating. In this stage, the oil is exposed to hydrogen gas at high pressure and temperature in the presence of a catalyst. This process removes contaminants like sulfur, nitrogen, and oxygen, further purifying the base oil.
- Blending with Additives: The final stage involves blending the re-refined base oil with a specific package of additives. These additives enhance the oil’s performance characteristics, such as viscosity index improvers for optimal performance across temperature ranges, anti-wear additives to minimize friction, and detergents to keep the engine clean. The specific blend of additives depends on the intended application of the finished lubricating oil.
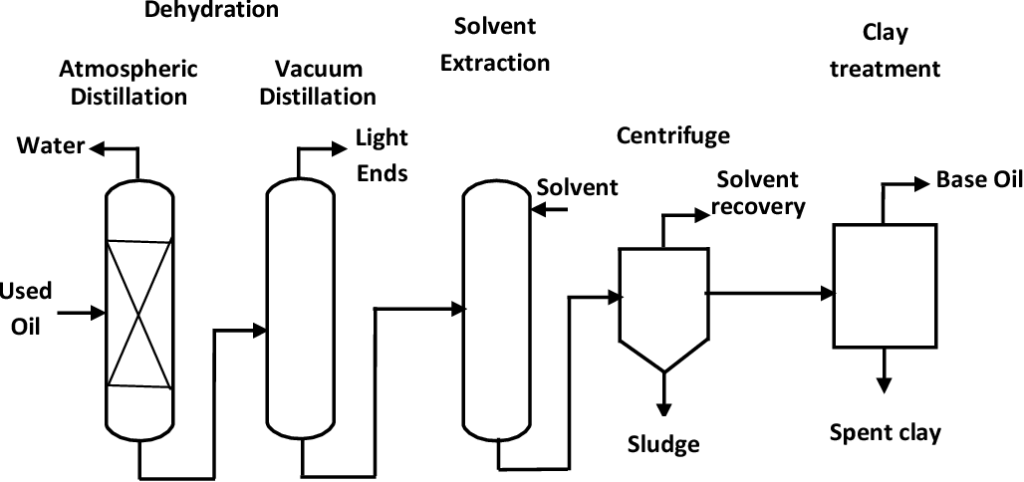
Inside a Used Oil Re-Refining Plant
A used oil re-refining plant houses a complex network of equipment designed to efficiently process used oil. Some of the essential components include:
- Storage tanks: Used oil is stored in designated tanks before being processed.
- Pre-treatment equipment: Filtration units, settling tanks, and centrifuges are used for initial cleaning and separation.
- Distillation units: These units separate the used oil into various fractions based on boiling points.
- Hydrotreating reactors: These reactors remove impurities from the base oil using hydrogen gas and catalysts.
- Blending equipment: Blending tanks and mixers combine the re-refined base oil with specific additive packages to create the final product.
- Quality control laboratory: Throughout the process, samples are rigorously tested to ensure the re-refined oil meets stringent quality standards.
Re-refining plants strictly adhere to safety regulations and environmental guidelines. These regulations govern aspects like storage procedures, emissions control, and wastewater treatment to minimize environmental risks.
Applications of Re-Refined Lubricating Oil
Re-refined lubricating oil undergoes rigorous testing to ensure it meets the same performance standards as virgin oil-based lubricants. These tests evaluate viscosity index, oxidation stability, wear protection, and anti-foaming properties. High-quality re-refined oils meet or exceed the American Petroleum Institute (API) standards for various lubricant categories, making them suitable for a wide range of applications, including:
- Automotive Engine Oils: Re-refined oils can be used in gasoline and diesel engines, providing optimal lubrication and wear protection for passenger cars, light trucks, and heavy-duty vehicles.
- Industrial Lubricants: Re-refined oils are well-suited for industrial machinery lubrication, including gearboxes, hydraulic systems, and compressors. Their anti-wear properties and resistance to thermal breakdown ensure smooth operation and extended equipment life.
- Specialty Lubricants: The versatility of re-refined oils allows them to be used in various specialty applications, such as greases, metalworking fluids, and railroad lubricants.
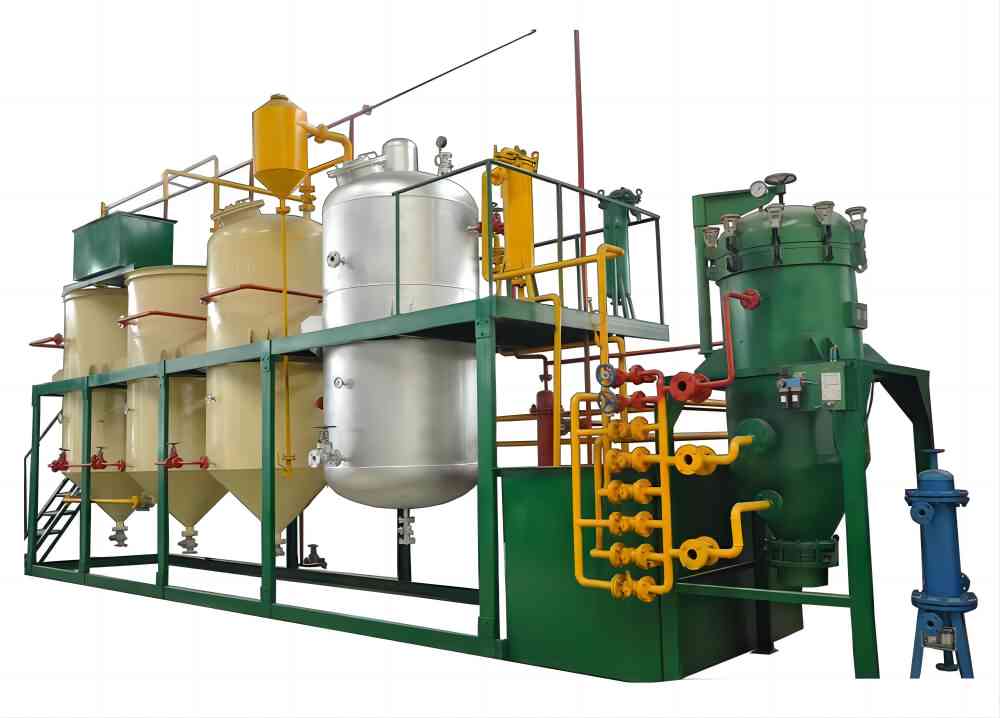
Challenges and the Future of Re-Refining
While re-refining offers numerous environmental and economic benefits, the industry faces some challenges. One obstacle is the misconception that re-refined oil is inferior to virgin oil. As discussed earlier, rigorous testing ensures that re-refined oils meet the same performance standards. Another challenge lies in the collection infrastructure. Expanding and improving the collection network for used oil is crucial to ensuring a steady supply for re-refineries.
Despite these challenges, the future of used oil re-refining appears bright. Governments around the world are increasingly recognizing the environmental benefits of re-refining and are implementing policies to encourage its growth. Consumers are also becoming more environmentally conscious and are seeking sustainable alternatives for their lubricant needs.
Conclusion
Used oil re-refining offers a compelling solution for responsible used oil management. By conserving virgin crude oil, minimizing waste, and reducing greenhouse gas emissions, re-refining contributes significantly to a more sustainable future. The performance and versatility of re-refined lubricating oils make them a viable and environmentally friendly choice for various applications. By promoting responsible used oil collection practices and supporting the growth of the re-refining industry, we can move towards a more sustainable future for our planet.
Additional Information:
The American Petroleum Institute (API): https://www.api.org/ provides information on used oil management and lubricant standards.
The National Lubricating Grease Institute (NLGI): https://www.nlgi.org/ offers resources on lubricants and their applications.
Local recycling and waste management organizations can provide information on responsible used oil disposal options in your area.