Recycling Used Motor Oil into Diesel: A Sustainable Waste Management
The escalating global demand for energy, coupled with the imperative for sustainable waste management, has propelled the exploration of innovative solutions for resource recovery. Among these, the conversion of used motor oil into diesel fuel stands out as a promising avenue. Used motor oil, a ubiquitous byproduct of industrial and automotive activities, poses a significant environmental hazard when improperly disposed of. However, through advanced chemical processes and technological interventions, this waste stream can be transformed into a valuable energy resource, mitigating pollution and bolstering energy security. This article delves into the intricate chemical processes, legal frameworks, byproduct management, and technological advancements associated with converting used motor oil into diesel, providing a comprehensive overview of this burgeoning field.
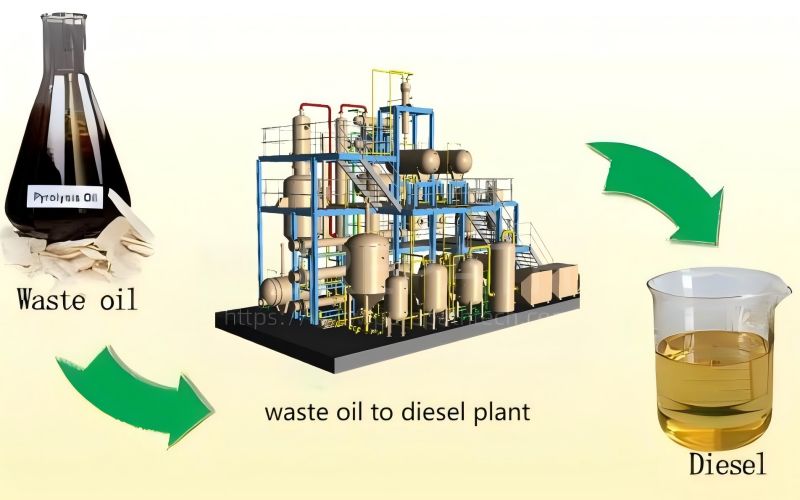
Is it Legal to Turn Used Motor Oil into Diesel?
The legality of converting used motor oil to diesel is a complex issue, governed by a patchwork of environmental regulations that vary significantly across jurisdictions. In many developed nations, used motor oil is classified as hazardous waste due to the presence of heavy metals, polycyclic aromatic hydrocarbons (PAHs), and other contaminants. Consequently, its handling, processing, and disposal are subject to stringent regulations aimed at minimizing environmental risk.
In the United States, for example, the Environmental Protection Agency (EPA) regulates used oil under the Resource Conservation and Recovery Act (RCRA). While recycling used oil is encouraged, the EPA imposes strict standards for processing and handling to prevent contamination. Facilities involved in converting used oil to diesel must obtain permits, comply with emission standards, and adhere to specific storage and transportation protocols. Similar regulatory frameworks exist in the European Union, where the Waste Framework Directive and specific directives on waste oils govern the management of used oil.
The primary legal concern revolves around ensuring that the conversion process does not result in the release of harmful pollutants into the environment. This necessitates rigorous monitoring of emissions, proper handling of byproducts, and adherence to established best practices. Non-compliance can lead to substantial fines and legal penalties, underscoring the importance of understanding and adhering to local and national regulations.
Furthermore, the legal landscape is evolving as environmental awareness grows and technology advances. Regulatory bodies are increasingly recognizing the potential of used oil recycling and are developing guidelines to facilitate safe and efficient conversion processes. Prospective operators must stay abreast of these developments and engage with regulatory authorities to ensure compliance.
How is the Chemical Process of Converting Motor Oil to Diesel?
The conversion of used motor oil to diesel involves a series of chemical processes designed to break down the complex hydrocarbon chains in the oil and reform them into diesel-range hydrocarbons. The most common methods employed are pyrolysis, distillation, and catalytic cracking.
- Pyrolysis: This process involves heating used motor oil in the absence of oxygen, causing it to decompose into gaseous and liquid fractions. The temperature and residence time are critical parameters that influence the composition of the resulting products. Pyrolysis typically yields a mixture of hydrocarbons, including diesel, gasoline, and heavy oils.
- Distillation: Distillation is used to separate the various hydrocarbon fractions produced by pyrolysis based on their boiling points. The liquid fraction from pyrolysis is heated, and the vapors are condensed at different temperatures to yield diesel, gasoline, and other products. This process is essential for refining the crude oil produced by pyrolysis into usable diesel fuel.
- Catalytic Cracking: This advanced technique employs catalysts to enhance the cracking of long-chain hydrocarbons into shorter, more desirable diesel-range hydrocarbons. Catalysts such as zeolites and alumina-silica are used to accelerate the reaction and improve the yield and quality of the diesel fuel. Catalytic cracking allows for operation at lower temperatures and pressures than thermal cracking, resulting in higher efficiency and lower energy consumption.
The chemical reactions involved in these processes are complex and require precise control to achieve optimal results. The composition of used motor oil can vary significantly depending on its source and usage, necessitating adjustments to the process parameters. The objective is to maximize the yield of diesel fuel while minimizing the production of undesirable byproducts.
The process usually involves pretreatment of the used engine oil to remove water, sludge, and other contaminants. Pretreatment can include filtration, settling, and chemical treatment. After pretreatment, the oil is fed into the pyrolysis reactor or catalytic cracker, where it undergoes the transformation into diesel fuel.
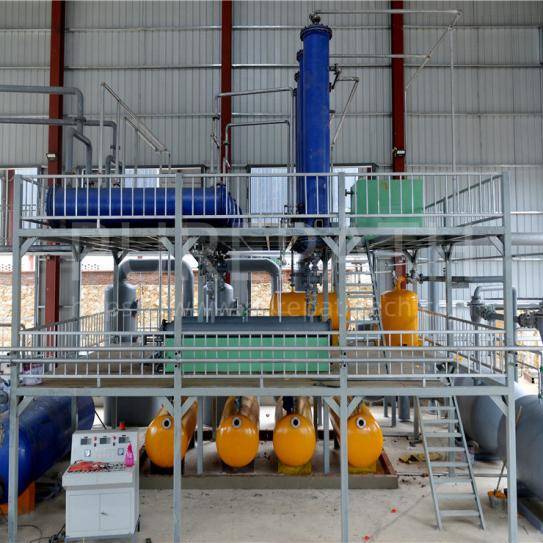
What are the Byproducts of Recycling Used Motor Oil?
The conversion of used motor oil to diesel inevitably generates byproducts that require careful management. These byproducts can include:
- Sludge: This is a semi-solid residue containing heavy metals, ash, and other contaminants. Sludge requires proper disposal in accordance with hazardous waste regulations.
- Gases: The pyrolysis and cracking processes produce gases, including methane, ethane, and propane. These gases can be used as fuel to power the conversion process or can be flared to prevent atmospheric pollution. The gases may also contain harmful compounds and require filtering.
- Water: Water can be present in used oil or generated during the conversion process. It must be treated to remove contaminants before being discharged or reused.
- Ash: Ash is a byproduct of combustion and contains heavy metals and other inorganic compounds. It requires disposal in accordance with hazardous waste regulations.
The management of these byproducts is critical to the environmental sustainability of used motor oil recycling. Proper disposal methods must be employed to prevent contamination of soil and water resources. The recycling of byproducts, where feasible, can also contribute to resource conservation.
For instance, the gases produced during pyrolysis can be used to generate heat for the process, reducing energy consumption. The sludge can be treated to recover valuable metals or used as a component in construction materials. Water can be treated and reused in the process or discharged after meeting environmental standards.
However, the disposal of hazardous byproducts remains a significant challenge. The cost of proper disposal can be substantial, and the availability of suitable disposal facilities may be limited. This underscores the need for ongoing research and development to identify more sustainable and cost-effective methods for managing byproducts.
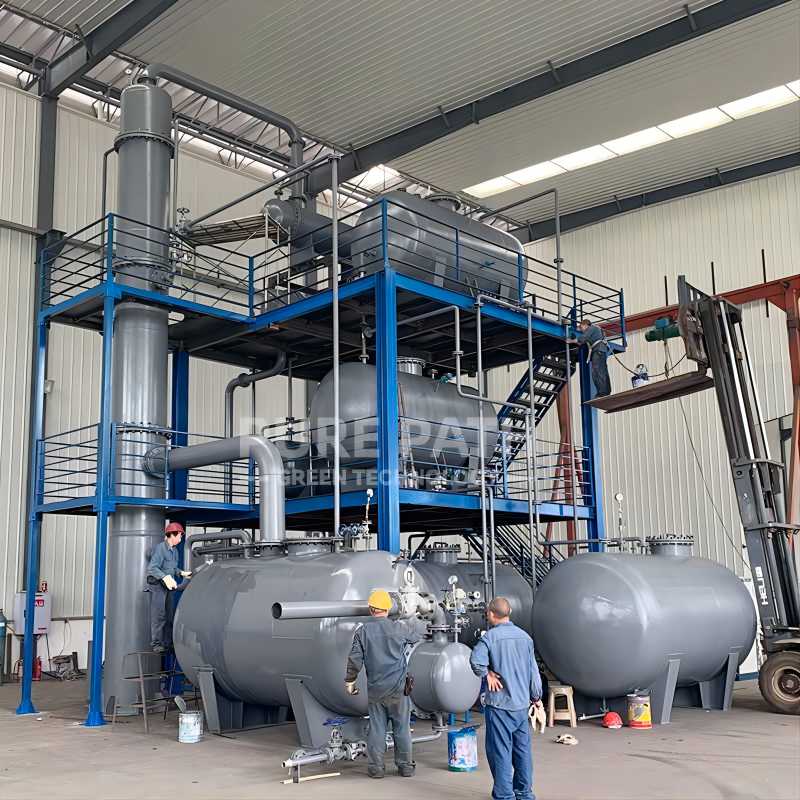
The Best Machine to Convert Used Motor Oil into Diesel
The efficiency and effectiveness of used motor oil conversion depend heavily on the technology employed. Several types of motor oil recycling machines are available, ranging from small-scale units suitable for on-site processing to large-scale industrial plants.
Key features to consider when selecting a used motor oil recycling machine include:
- Capacity: The capacity of the machine should match the volume of used oil to be processed.
- Efficiency: The machine should maximize the yield of diesel fuel and minimize energy consumption.
- Safety: The machine should incorporate safety features to prevent accidents and ensure operator safety.
- Automation: Automated systems can reduce labor costs and improve process control.
- Emission Control: The machine should be equipped with emission control systems to minimize air pollution.
- Maintenance: The machine should be designed for easy maintenance and repair.
Reputable manufacturers offer a range of used motor oil recycling machines that incorporate advanced technologies such as catalytic cracking and automated process control. These machines are designed to meet stringent environmental standards and ensure high efficiency.
Factors that affect machine efficiency include the quality of the used oil, the operating parameters, and the maintenance of the machine. Regular maintenance and calibration are essential to ensure optimal performance.
Safety precautions associated with the motor oil recycling machines include:
- Proper ventilation to prevent the accumulation of flammable gases.
- Fire suppression systems to extinguish fires.
- Pressure relief valves to prevent explosions.
- Personal protective equipment (PPE) for operators.
- Regular inspections and maintenance to identify and address potential hazards.
The cost-effectiveness of the conversion process depends on several factors, including the cost of used oil, the yield of diesel fuel, and the operating costs. Investing in high-efficiency machines and implementing effective byproduct management strategies can help to improve the economic viability of used oil recycling.
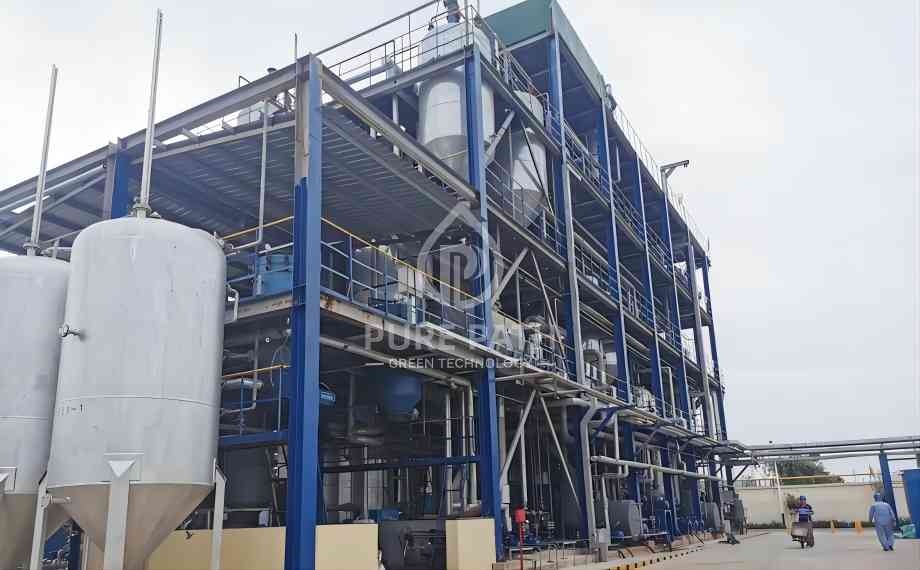
Wrap Up
Converting used motor oil to diesel presents a viable and sustainable solution to the growing problem of waste oil disposal. By transforming hazardous waste into a valuable resource, this process offers significant environmental and economic benefits. However, the successful implementation of used oil recycling requires adherence to legal regulations, careful management of byproducts, and the use of advanced technology. Ongoing research and development are essential to improve the efficiency and sustainability of the conversion process. As environmental awareness grows and technology advances, used oil recycling is poised to play an increasingly important role in waste management and resource conservation.