Refining Crude Oil to Petrol and Diesel: Differences and Similarities
In the vast expanse of the energy sector, diesel and petrol stand out as the most recognizable and widely used products derived from crude oil. Their ubiquity in our daily lives, powering everything from vehicles to generators, underscores the importance of understanding the processes by which they are produced. This article aims to delve into the processes involved in refining crude oil into diesel and petrol, examining their similarities and differences.
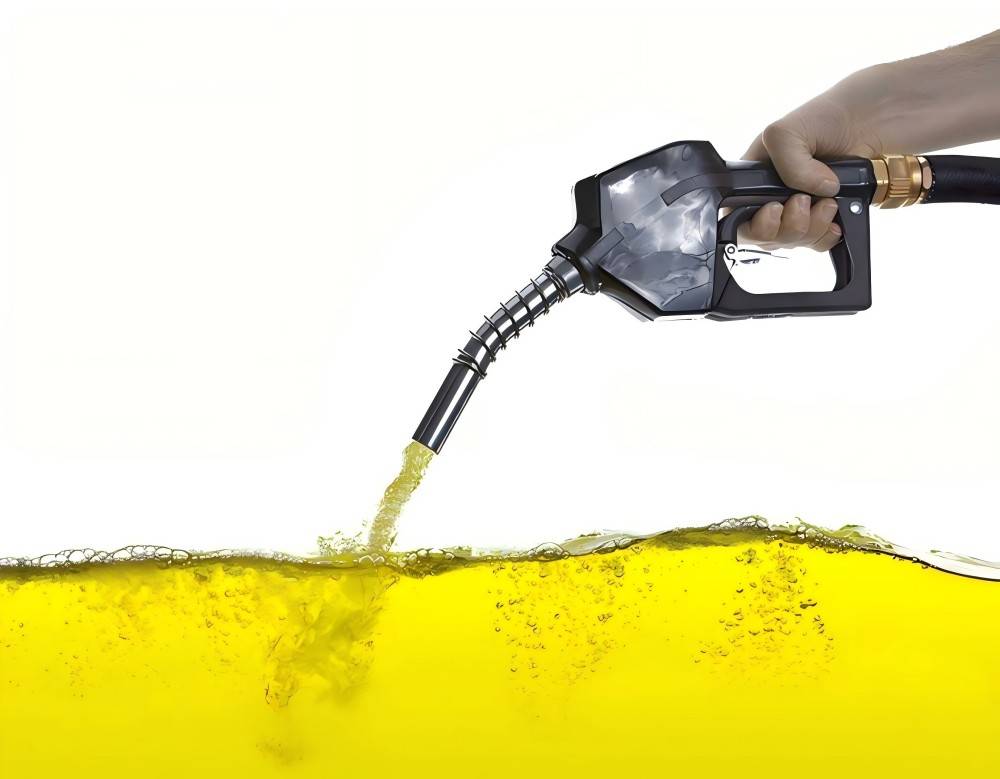
Common Processes in Refining Crude Oil to Diesel and Petrol
1. Same Crude Oil Extraction and Initial Refinement
Both diesel and petrol originate from crude oil, a complex mixture of hydrocarbons that have been formed over millions of years through the decomposition of ancient organic matter. Crude oil is a vital natural resource and serves as the primary raw material for producing a wide range of petroleum products. The first step in the production of diesel and petrol is the refining of crude oil.
Refining crude oil involves heating the raw material to break it down into its various components, which are then separated based on their boiling points. This process is essential for both diesel and petrol production and marks the common starting point in their respective journeys from crude oil to finished fuels. The initial refining stage is known as distillation, where crude oil is heated in a furnace to temperatures of around 350°C to 400°C. As the crude oil vaporizes, it enters a distillation column, where different fractions condense at different levels depending on their boiling points.
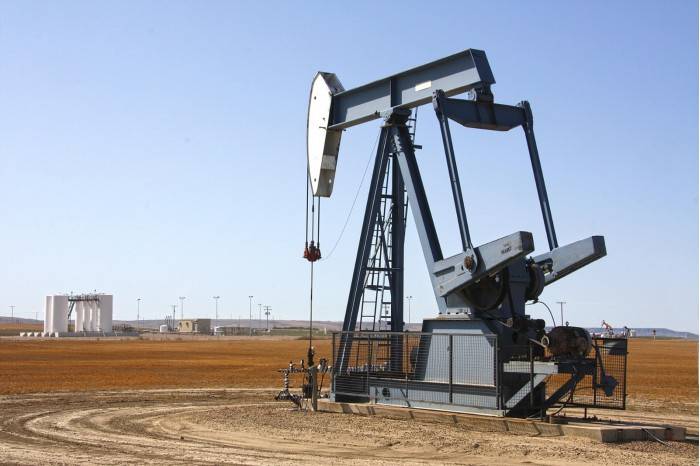
2. Distillation Process
The distillation process is central to separating the various components of crude oil, including petrol and diesel. The principle behind this process lies in the differing boiling points of the hydrocarbons present in crude oil. As the vaporized crude oil ascends the distillation column, the temperature decreases, allowing different fractions to condense at different heights within the column.
Petrol and diesel are separated primarily based on their boiling points. Petrol, being a lighter hydrocarbon, has a lower boiling point range of approximately 150°C to 205°C. As a result, it condenses at higher levels within the distillation column. Diesel, on the other hand, has a higher boiling point range of 180°C to 370°C, causing it to condense lower in the column. This difference in boiling points reflects the varying molecular structures of petrol and diesel, with diesel containing longer and heavier hydrocarbon chains.
The distillation process not only separates petrol and diesel but also produces other valuable petroleum products such as kerosene, jet fuel, and lubricating oils. The precise control of temperature and pressure within the distillation column is crucial for ensuring the efficient separation of these products, each of which serves a specific purpose in different industries.
3. Refining Techniques
Once diesel and petrol have been separated through distillation, they undergo additional refining processes to improve their quality and suitability for specific applications. Both fuels are subjected to various refining techniques aimed at enhancing their combustion properties, stability, and purity.
Catalytic Cracking is one such technique, employed to break down heavier hydrocarbons into lighter ones, thereby improving the overall yield of petrol and diesel from crude oil. In catalytic cracking, heavy oils are subjected to high temperatures in the presence of a catalyst, which facilitates the breaking of large hydrocarbon molecules into smaller, more desirable fractions. This process is particularly important for increasing the production of petrol, as it converts heavy residues into lighter, more valuable products.
Another common refining technique is hydrotreating, which is used to remove impurities such as sulfur, nitrogen, and metals from the fuel. Hydrotreating involves treating the fuel with hydrogen gas at high pressure and temperature, which helps to improve its purity and reduce the emission of pollutants when the fuel is burned. This process is crucial for both diesel and petrol, as it ensures that the fuels meet stringent environmental standards and perform efficiently in modern engines.
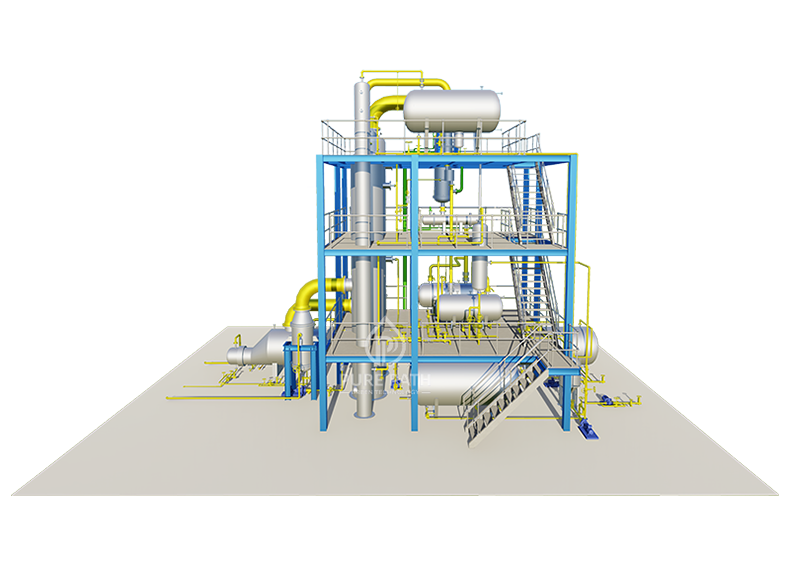
Differences in Refining Crude Oil to Diesel and Petrol Process
While refining crude oil to diesel and petrol processes share many similarities, there are also significant differences that cater to the unique requirements of each fuel.
Differences in Raw Material Handling
Diesel Production
Diesel production is not limited to crude oil alone. It can be produced from various sources, including:
- Crude Oil: The primary source, similar to petrol.
- Other Petroleum Products: Such as heavy oil and kerosene.
- Renewable Resources: Biodiesel, derived from plant oils or animal fats, can be blended with traditional diesel or used independently.
This broad range of raw materials makes diesel production more adaptable and versatile, allowing for alternative production methods and contributing to its widespread use in different sectors.
Petrol Production
Petrol is almost exclusively derived from crude oil, making its production highly dependent on the availability and quality of this single raw material source. This reliance can limit the flexibility of petrol production, especially in situations where crude oil supply or quality may be compromised.
Despite this limitation, the crude oil to petrol process is optimized to maximize its yield from crude oil. This ensures that petrol production meets the high demand for use in passenger vehicles and other applications, where its specific properties are essential.
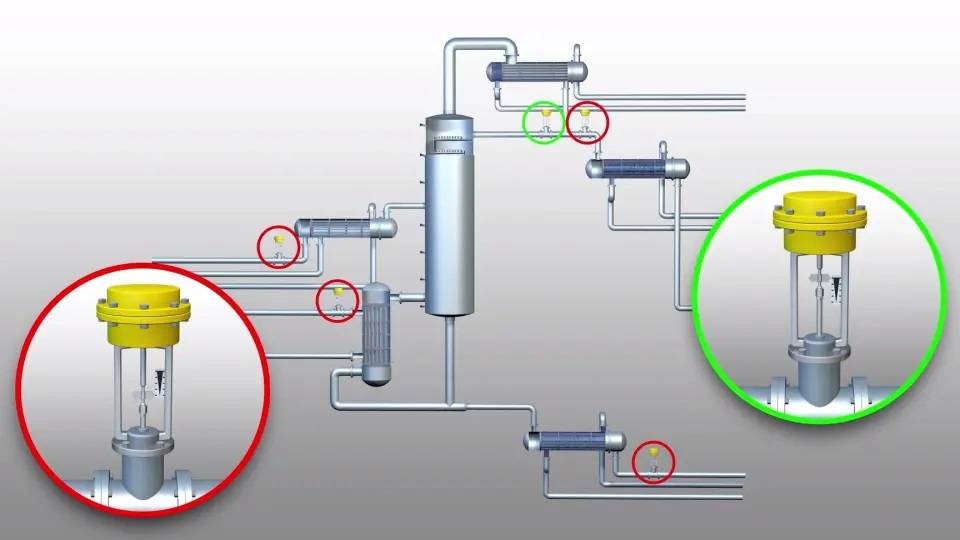
Different Distillation Process in Details
Difference | Petrol | Diesel |
Distillation Positions | 1. Higher Position in Distillation Column: Condenses higher up due to its lower boiling point. 2. Lighter Hydrocarbon Chains: Shorter chains make it burn quickly, optimized for high-speed engines. | 1. Lower Position in Distillation Column: Condenses at a lower level due to its higher boiling point. 2. Heavier Hydrocarbon Chains: Longer chains contribute to higher energy content and slower combustion rate. |
Impact on Physical Properties | 1. Quick Combustion: Necessary for rapid power delivery in petrol engines. 2. Volatility: Enhances performance in high-speed engines where efficient combustion is crucial. | 1. Higher Energy Content: Suited for heavy-duty applications due to higher energy density. 2. Slower Combustion Rate: Ideal for diesel engines that require a gradual energy release. |
Influence on Subsequent Refining Processes | Lighter Fractions: Extracted at a higher position, essential for efficient combustion in petrol engines. | Heavier Fractions: Collected at a lower position in the distillation column, ideal for diesel engines. |
Specialized Refining Steps for Petrol and Diesel
Crude Oil to Petrol Refining Process
1. Octane Rating Enhancement
- Focus on Octane Rating: Refining petrol involves processes aimed at increasing its octane rating, which is crucial for its ability to resist knocking during combustion.
- Anti-Knock Performance: A higher octane rating ensures that petrol can handle the high pressures and temperatures in modern engines without causing damage, particularly in high-performance petrol engines.
2. Removal of Olefins
- Improving Stability: Refiners also focus on removing olefins from petrol to enhance its stability and further improve its anti-knock properties.
- Engine Compatibility: The removal of olefins contributes to a more stable fuel that performs well under the demanding conditions of advanced petrol engines.
Crude Oil to Diesel Refining Process
1. Desulfurization and Denitrification
- Sulfur and Nitrogen Removal: The refining process for diesel emphasizes the removal of sulfur and nitrogen compounds to improve combustion efficiency and reduce harmful emissions.
- Hydrogen Treatment: This process involves treating diesel with hydrogen gas to effectively remove impurities, resulting in a cleaner-burning fuel that meets environmental standards.
2. Cetane Rating Enhancement
- Focus on Cetane Rating: Diesel refining may also include steps to enhance the fuel’s cetane rating, which measures its ignition quality.
- Improved Ignition and Combustion: A higher cetane rating ensures that diesel ignites more easily and burns more completely, leading to better engine performance and lower emissions.
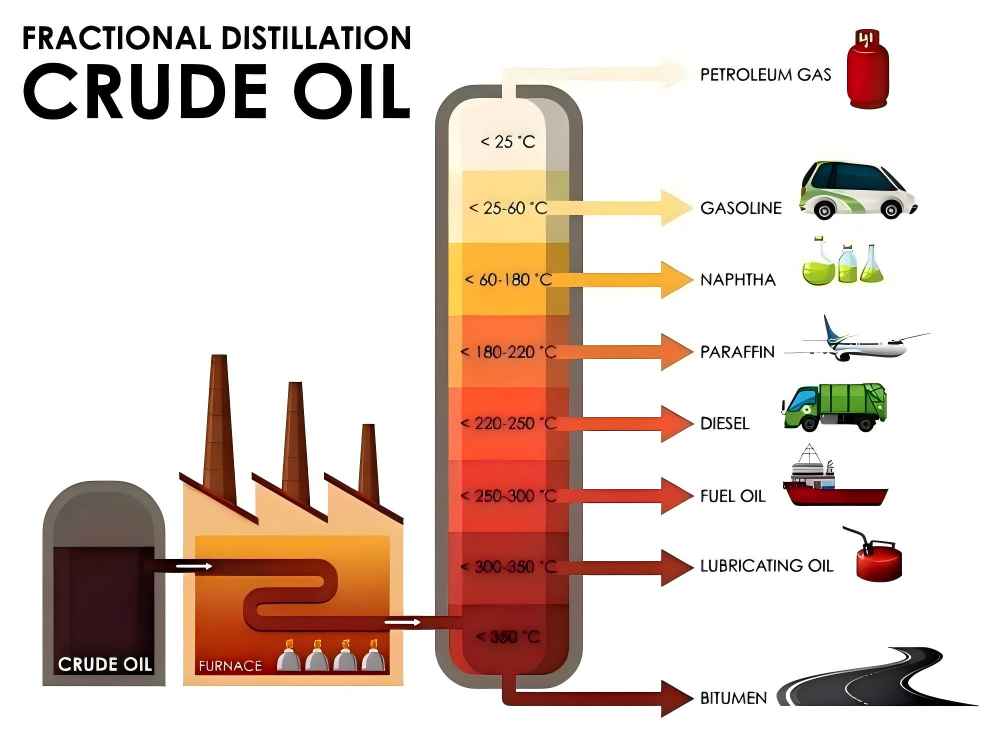
Different Additive Utilization in Crud Oil to Diesel and Petrol Process
Petrol Additives
1. Octane Boosters:
- Enhancing Anti-Knock Performance: Petrol often requires the addition of octane boosters to improve its resistance to knocking, which is critical for high-speed engines.
- Stability and Combustion: These additives help maintain the fuel’s stability and ensure consistent combustion characteristics under high-pressure conditions.
2. Common Additives
- Ethanol: Frequently added to petrol to increase its oxygen content, ethanol improves combustion efficiency and reduces emissions.
- Detergents: Used to keep engine components clean by preventing the buildup of deposits, which can affect engine performance.
Diesel Additives
1. Cold Weather Additives
- Flow Improvers (Cold Flow Additives): Diesel may require flow improvers to prevent the fuel from gelling or solidifying in low temperatures, ensuring it remains fluid and can pass through the engine’s fuel system.
2. Stabilizers
- Maintaining Chemical Stability: Stabilizers are added to diesel to preserve its chemical stability over time, preventing the formation of deposits that could clog fuel injectors.
- Ensuring Reliable Performance: These additives are essential for ensuring that diesel engines operate efficiently and reliably in various environmental conditions, particularly in colder climates.
In summary, the process of refining crude oil into diesel and petrol reveals both the similarities and differences between these two essential fuels. While they share common steps, such as crude oil refining, distillation, and certain refining techniques, the differences in their production processes reflect their distinct roles in the energy sector.