Safety Measures in White Spirit Production Plants
White spirit, often known as mineral spirits, is a commonly used solvent in a variety of sectors, including paint manufacture, cleaning, and degreasing. While white spirits are useful in a variety of applications, their manufacturing requires the handling of combustible chemicals, which poses major safety risks. Therefore, the safety procedures in white spirit production plants are vital for protecting personnel, the environment, and the facility. In this article, we will look at the risks involved with white spirit manufacturing, the regulatory standards in place to reduce them, critical safety measures, and best practices for continual safety improvement.
Understanding White Spirit and Its Hazards
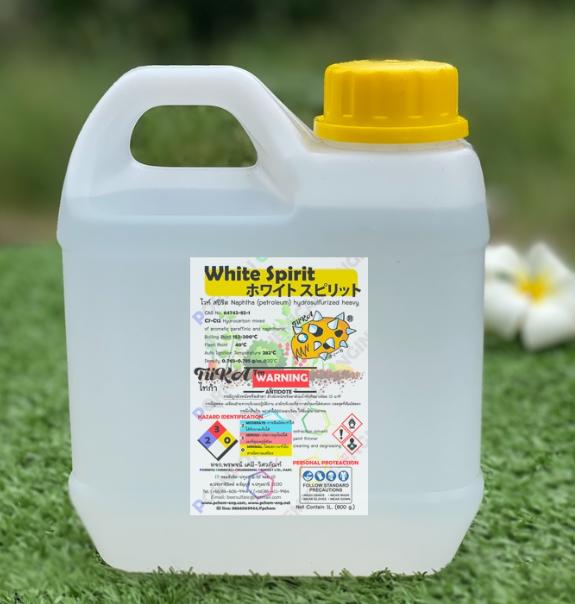
White Spirit is a petroleum-derived liquid solvent primarily composed of hydrocarbons. Its primary uses include thinning paints, cleaning brushes, and removing grease and oils from surfaces. Although versatile, white spirit is flammable and can present significant health risks, especially when inhaled or absorbed through the skin.
The primary hazards associated with white spirit production include:
- Flammability: White spirit is extremely flammable, and its fumes can react explosively with air. This increases the risk of fires and explosions in production plants.
- Toxicity: Prolonged exposure to white spirit vapors can result in respiratory problems, dizziness, migraines, and potentially long-term harm to the central nervous system. Skin exposure can cause irritation or dermatitis.
- Environmental Impact: If not managed appropriately, white spirits can contaminate water supplies and soil, causing environmental damage.
Given these risks, effective safety protocols are essential to prevent accidents and protect both workers and the environment.
Regulatory Standards and Compliance
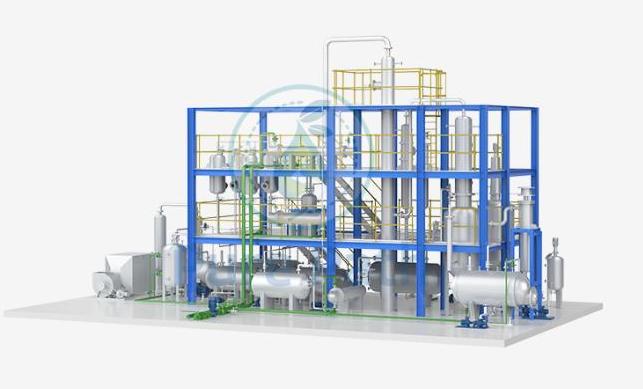
White spirit production plants must adhere to several regulatory standards designed to ensure safety and mitigate risks. These regulations cover aspects like chemical handling, worker protection, and fire safety, and are enforced by various agencies globally.
- OSHA Regulations: In the United States, the Occupational Safety and Health Administration (OSHA) establishes strict requirements for handling hazardous compounds such as white spirits. OSHA mandates sufficient ventilation, the use of personal protective equipment (PPE), and explicit safety regulations to reduce exposure to hazardous fumes and prevent accidents.
- REACH Compliance (EU): The European Union’s REACH (Registration, Evaluation, Authorization, and Restriction of Chemicals) law covers the manufacture and use of chemicals, including white spirit. It requires producers to assess the risks of chemicals and convey safety information to guarantee their safe use in industrial settings.
- NFPA Standards: The National Fire Protection Association (NFPA) provides standards on fire safety, specifically for plants handling flammable materials. This includes guidelines on fire suppression systems, safe storage practices, and hazard assessments.
- ISO Standards: ISO 45001, an international standard for occupational health and safety, assists facilities in implementing systematic approaches to risk management, assuring ongoing monitoring and compliance with best practices.
Compliance with these standards protects workers, decreases environmental damage, and ensures legal operational integrity.
Key Safety Measures in White Spirit Production Plants
The production of white spirits involves the handling of hazardous chemicals, making safety a top priority. Below are the most critical safety measures that should be implemented in white spirit production plants, each elaborated for maximum effectiveness.
Effective Ventilation Systems
One of the most important safety precautions in any white spirit production facility is the installation of effective ventilation systems. Because white spirit is a volatile material that emits dangerous vapors, adequate airflow is required to prevent the accumulation of toxic fumes, which could cause major health problems or fire threats. Localized exhaust ventilation (LEV) should be employed in regions with high vapor concentrations, such as mixing or filling stations. Furthermore, the facility should have a general ventilation system that provides a continuous flow of fresh air to dilute and remove any airborne contaminants. To ensure its continued efficiency, the ventilation system must be tested and serviced on a regular basis.
Personal Protective Equipment (PPE)
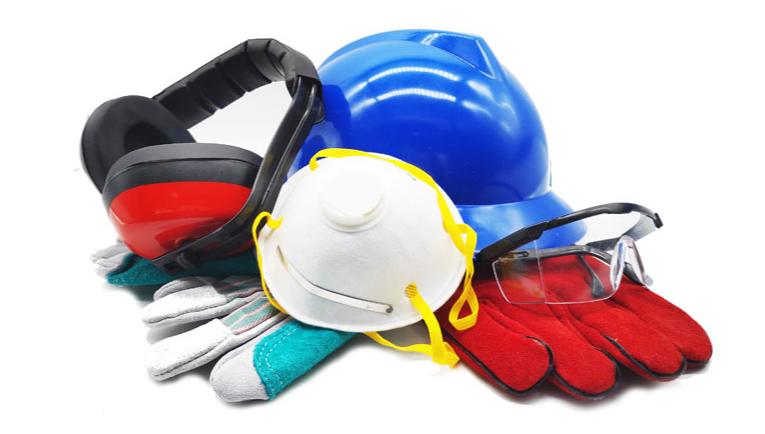
Personal Protective Equipment (PPE) plays a crucial role in safeguarding workers from direct exposure to white spirit, which can irritate the skin, eyes, and respiratory system. PPE must be provided based on the specific risks of the production process and include flame-resistant clothing, gloves, goggles, and respiratory protection. Workers involved in tasks with a higher risk of exposure, such as handling or transferring white spirit, should wear specialized chemical-resistant clothing and gloves. In areas with high vapor concentrations, appropriate respiratory protection like half or full-face respirators with organic vapor cartridges is essential. Ensuring workers are trained in how to use and maintain PPE is just as important as supplying it.
Explosion-Proof Equipment and Electrical Systems
Due to the highly combustible nature of white spirit and its fumes, all plant equipment and electrical systems must be explosion-proof. This comprises electrical cables, motors, control panels, and lighting fixtures. Standard electrical equipment can spark or generate heat, igniting flammable gasses and resulting in a catastrophic explosion. Explosion-proof equipment is specifically intended to retain any sparks or heat generated within the instrument, preventing them from coming into touch with the surroundings. In addition, places where white spirit is stored, processed, or utilized should have explosion-proof lighting and grounding systems to prevent the risk of static discharge.
Fire Suppression and Emergency Response Systems
Due to the flammable nature of the white spirit, a well-designed fire suppression system is a non-negotiable safety measure. Fire detection systems should be in place to monitor for signs of fire or heat, and automatic fire suppression systems, such as sprinklers or foam-based extinguishers, should be installed in high-risk areas. These systems should be regularly tested and maintained to ensure they function correctly in the event of an emergency. In addition to fire suppression, a comprehensive emergency response plan should be in place, detailing the actions to take in case of a spill, fire, or chemical release. Emergency exits, clearly marked evacuation routes, and access to first aid stations should be part of the safety plan.
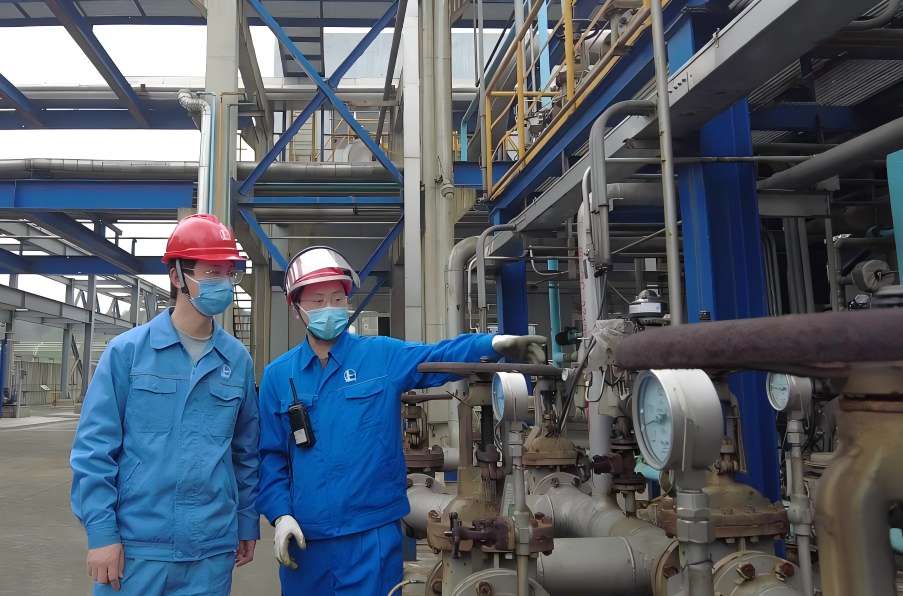
Best Practices for Continuous Improvement
- Continuous improvement in safety practices within white spirit production plants is key to ensuring long-term protection and efficiency. One of the best ways to drive improvement is through regular safety audits. These audits assess existing safety protocols, check for compliance with regulatory standards, and identify areas where practices can be enhanced. A thorough audit helps pinpoint any weaknesses and ensures that safety measures remain up to date.
- Employee training is another critical component. Ongoing education ensures that workers stay informed about the latest safety protocols, correct handling techniques, and emergency procedures. Regular training sessions not only reinforce safe practices but also foster a culture where safety is a top priority. Providing refresher courses and promoting knowledge-sharing among staff can significantly reduce risks.
- Adopting new technologies is also essential for improving safety. Advanced monitoring systems, such as real-time air quality sensors and automatic leak detection, can assist discover possible risks before they become a problem. These advances enable faster reactions and more precise monitoring of safety circumstances.
- Finally, creating a strong safety culture throughout the organization guarantees that everyone is responsible for safety. Encouraging open communication, encouraging safe conduct, and integrating staff in safety efforts results in a proactive rather than reactive approach to safety. This approach results in a safer working environment and ongoing development in procedures throughout time.
Conclusion
Safety in white spirit production plants is more than a legislative requirement; it is a moral commitment to protect workers, the environment, and the community. Plant operators may assure safe and efficient operations by knowing the threats, adhering to regulations, putting in place strong safety measures, and cultivating a continuous improvement culture.
Investing in safety now not only prevents accidents, but it also increases productivity, lowers costs, and fosters a reputation for dependability and responsibility. Prioritize safety in your white spirit production facility—it will pay you in the long term.