Solvent Extraction and Hydrotreating in Used Oil Re-Refining – What are the Differences?
The re-refining of used oil encompasses several crucial steps, with the purification or refining stage being particularly critical in determining the quality of the final product. Among the various refining technologies employed, solvent extraction and hydrotreating stand out as prominent methods for removing contaminants and upgrading the quality of the re-refined base oil. This article aims to provide a comprehensive comparative analysis of these two pivotal techniques in used oil re-refining, examining their principles, advantages, disadvantages, and application considerations.
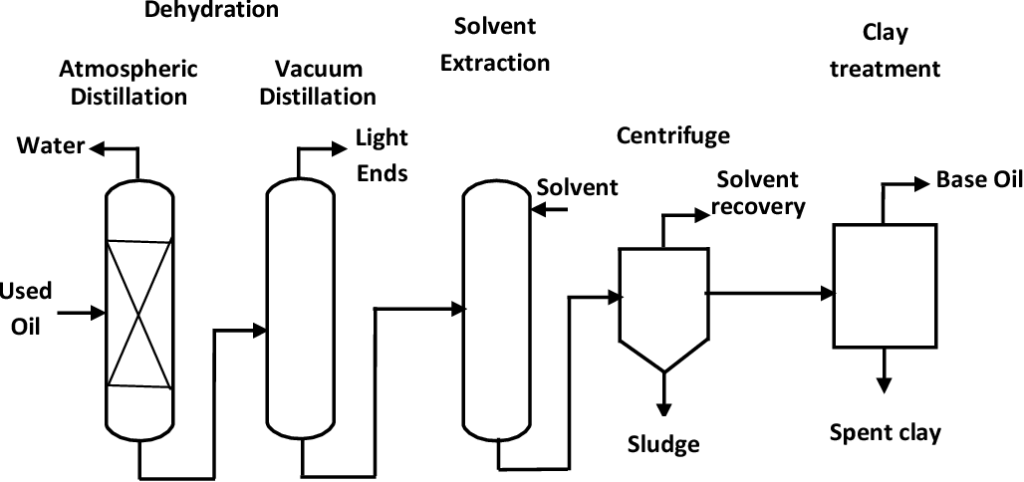
Part 1: What are Solvent Extraction Technologies in Used Oil Re-refining?
1. Principles and Process Flow of Solvent Extraction
In the field of used oil re-refining, solvent extraction is employed to separate unwanted components from valuable oil fractions. This process takes advantage of differential solubility, where a chosen solvent selectively dissolves impurities while leaving the desired oil behind.
Typically, the used oil is first pre-treated to remove water and solids. Then, it’s introduced into an extraction tower, where it comes into contact with solvents like propane, butane, phenol, furfural, or N-methylpyrrolidone (NMP). These solvents are selected for their ability to dissolve contaminants such as polycyclic aromatic hydrocarbons (PAHs), oxidized products, and additive residues.
The extraction usually occurs in a countercurrent system, where oil flows in the opposite direction to the solvent. This enhances contact and boosts the efficiency of separation. The process produces two streams:
- The raffinate, rich in useful oil components.
- The extract, which contains the dissolved contaminants.
Next, the solvent is recovered through distillation. It is reused in the system, making the process more sustainable. The raffinate stream may then undergo clay treatment or other finishing steps to improve color and odor, ultimately resulting in high-quality re-refined base oil.
2. Advantages of Solvent Extraction in Used Oil Re-refining
Solvent extraction provides several benefits in used oil re-refining:
- It is highly effective at removing PAHs and oxidation products—substances that are difficult to eliminate by other methods, such as hydrotreating.
- The capital cost for setting up a solvent extraction unit is generally lower than that of hydrotreating systems.
- Operating conditions are mild, with lower temperature and pressure requirements. This reduces energy consumption and safety risks.
- By selecting different solvents and adjusting parameters, refiners can tailor the viscosity of the re-refined base oil, offering flexibility in product output.
- This method avoids the need for expensive catalysts, eliminating concerns around catalyst deactivation and regeneration.
3. Disadvantages of Solvent Extraction in Used Oil Re-refining
Despite its benefits, solvent extraction also has limitations:
- Some solvent loss is inevitable, requiring complex solvent recovery systems that consume additional energy.
- The extract phase, rich in dissolved contaminants, must be treated or disposed of carefully to avoid environmental issues.
- The quality of the re-refined base oil is closely tied to the type of solvent used. Poor solvent choice can result in lower oil quality.
- Solvent extraction is less effective at removing sulfur and nitrogen compounds compared to hydrotreating.
- The chemical stability and shelf life of oil produced via solvent extraction may not match that of hydrotreated products.
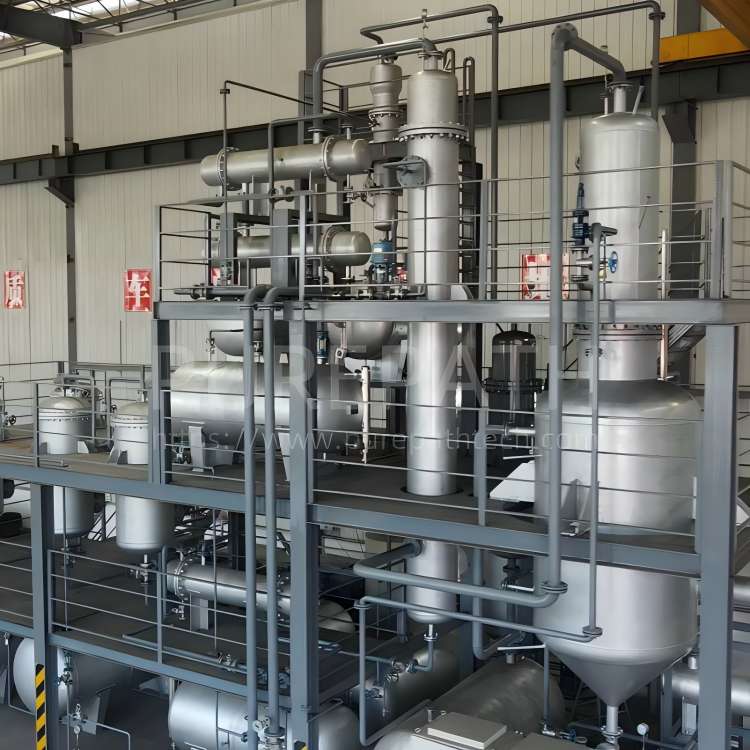
Part 2: What are the Hydrotreating Technologies in Used Oil Re-refining?
1. Principles and Process Flow of Hydrotreating Technologies
Hydrotreating is another core technology in used oil re-refining. It works by reacting the used oil with hydrogen under high temperature and pressure, in the presence of a catalyst.
Catalysts often consist of metal oxides or sulfides, such as cobalt-molybdenum (Co-Mo) or nickel-molybdenum (Ni-Mo) on an alumina support. The process targets impurities such as sulfur, nitrogen, metals, unsaturated hydrocarbons, and oxidation products.
Hydrogen reacts with these compounds, converting them into gases:
- Sulfur → hydrogen sulfide (H₂S)
- Nitrogen → ammonia (NH₃)
- Unsaturated hydrocarbons → saturated compounds
The product mixture then passes through separators and strippers to isolate the re-refined base oil. Unused hydrogen is captured and recycled to improve efficiency.
2. Advantages of Hydrotreating in Used Oil Re-refining
Hydrotreating delivers some of the highest-quality re-refined base oil in the industry:
- It can remove a broad range of impurities, including sulfur, nitrogen, oxygen, PAHs, and heavy metals.
- The resulting oil has excellent oxidation stability, color, and viscosity index.
- The product often meets the specifications for Group II or Group III base oils, suitable for high-performance lubricants.
- It generates mostly gaseous byproducts, which are easier to handle than the liquid or solid waste produced by some other processes.
- Hydrotreating is versatile, able to process used oil from various sources and of varying qualities.
3. Disadvantages of Hydrotreating in Used Oil Re-refining
However, hydrotreating has some significant challenges:
- The initial investment cost is high due to the need for high-pressure vessels, hydrogen infrastructure, and advanced control systems.
- It operates under intense conditions, requiring careful control of temperature, pressure, and hydrogen flow. This results in higher operational costs.
- The catalysts used can deactivate over time due to contamination or carbon build-up, requiring periodic regeneration or replacement.
- Removal of some heavy metals is less efficient, so robust pre-treatment is essential.
- Managing hydrogen safely and efficiently adds another layer of complexity to plant operations.
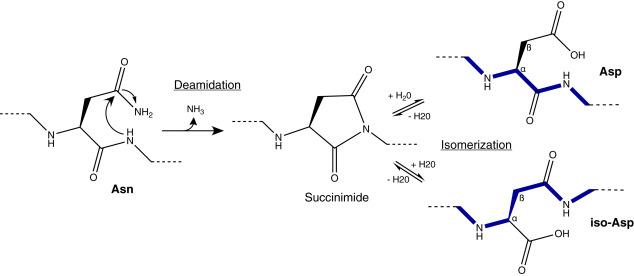
Part 3: Differences Between Solvent Extraction and Hydrotreating in Used Oil Re-refining
Feature | Solvent Extraction | Hydrotreating |
Fundamental Principle | Separation based on differential solubility | Catalytic chemical reactions with hydrogen |
Spectrum of Impurity Removal | Effective for specific organic compounds (e.g., PAHs), less broad | Broad spectrum (e.g., S, N, O, metals, unsaturates, PAHs) |
Quality of Re-Refined Base Oil | Dependent on solvent selection, potentially lower stability | High quality, excellent stability (Group II/III capable) |
Initial Capital Investment | Relatively lower | Higher |
Operational Conditions | Milder (lower temperature and pressure) | Severe (high temperature and pressure) |
Energy Consumption | Relatively lower (but solvent recovery can be energy-intensive) | Higher |
Nature of Byproducts | Primarily liquid or solid wastes (extract phase, potential sludge) | Primarily gaseous (H₂S, NH₃) |
Requirement for Catalyst | Not required | Required, with associated deactivation and regeneration/replacement |
Range of Applicability | More effective for specific used oil types and contaminants | Broadly applicable to a wider range of used oil qualities |
Technological Maturity | Well-established and relatively simpler | Widely adopted, highly mature, and more complex |
Part 4: Selection and Application Considerations for Used Oil Re-refining Technologies
Choosing between solvent extraction and hydrotreating in the context of used oil re-refining depends on a variety of technical, economic, and regulatory factors. Below is a breakdown of the key considerations:
1. Feedstock Characteristics
- Type of used oil: The source of the used oil—whether automotive, industrial, or marine—affects the choice of process. Oils with a high concentration of organic sludge, oxidized compounds, and additive residues may benefit more from hydrotreating.
- Contaminant profile: If the oil contains high levels of polycyclic aromatic hydrocarbons (PAHs) or other complex hydrocarbons, solvent extraction can be effective at targeting these specific pollutants.
- Presence of sulfur and nitrogen: Hydrotreating is generally more effective at removing sulfur- and nitrogen-containing compounds, which are harder to eliminate using solvent-based methods.
2. Product Quality Requirements
- End-use specifications: If the goal is to produce high-performance re-refined base oil that meets Group II or Group III standards, hydrotreating is the preferred method. It provides superior color, stability, and oxidation resistance.
- Tolerances for impurities: In applications where the re-refined base oil does not need to meet strict purity or viscosity index requirements, solvent extraction may be sufficient and more cost-effective.
3. Economic Considerations
- Capital investment: Solvent extraction requires less expensive equipment and a simpler setup, making it attractive for smaller facilities or developing markets.
- Operating costs: Hydrotreating demands high pressure, high temperature, and hydrogen supply, leading to higher energy consumption and operational complexity.
- Byproduct handling: Solvent extraction generates an extract phase that must be treated or disposed of, while hydrotreating produces mainly gaseous byproducts that are easier to manage.
4. Regulatory and Environmental Compliance
- Emission standards: Stricter environmental laws regarding emissions and residual contaminants in lubricants tend to favor hydrotreating, which offers more complete removal of harmful compounds.
- Waste management: The liquid and solid waste produced by solvent extraction, especially in older systems, may present challenges under modern regulatory frameworks.
5. Infrastructure and Technical Capability
- Existing facility layout: A facility already equipped for high-pressure operations or hydrogen use may find it more practical to implement hydrotreating.
- Workforce expertise: Solvent extraction systems are generally easier to operate and maintain, especially in regions with limited access to trained chemical engineers or catalyst specialists.
6. Hybrid Approach Opportunities
Combining technologies: In some cases, a dual-stage process is the optimal choice:
- Step 1: Solvent extraction to remove heavier contaminants, tars, and polar compounds.
- Step 2: Hydrotreating to upgrade the raffinate, remove remaining sulfur, nitrogen, and improve the chemical stability of the final re-refined base oil.
This hybrid model allows refiners to maximize both yield and quality, balancing cost-effectiveness with product performance.
In conclusion, there is no universal solution in used oil re-refining. Each facility must weigh its specific goals, feedstock profiles, and resource availability. While solvent extraction offers a cost-efficient pathway to moderate-quality oils, hydrotreating stands out for producing premium-grade re-refined base oils that meet today’s demanding lubricant standards.
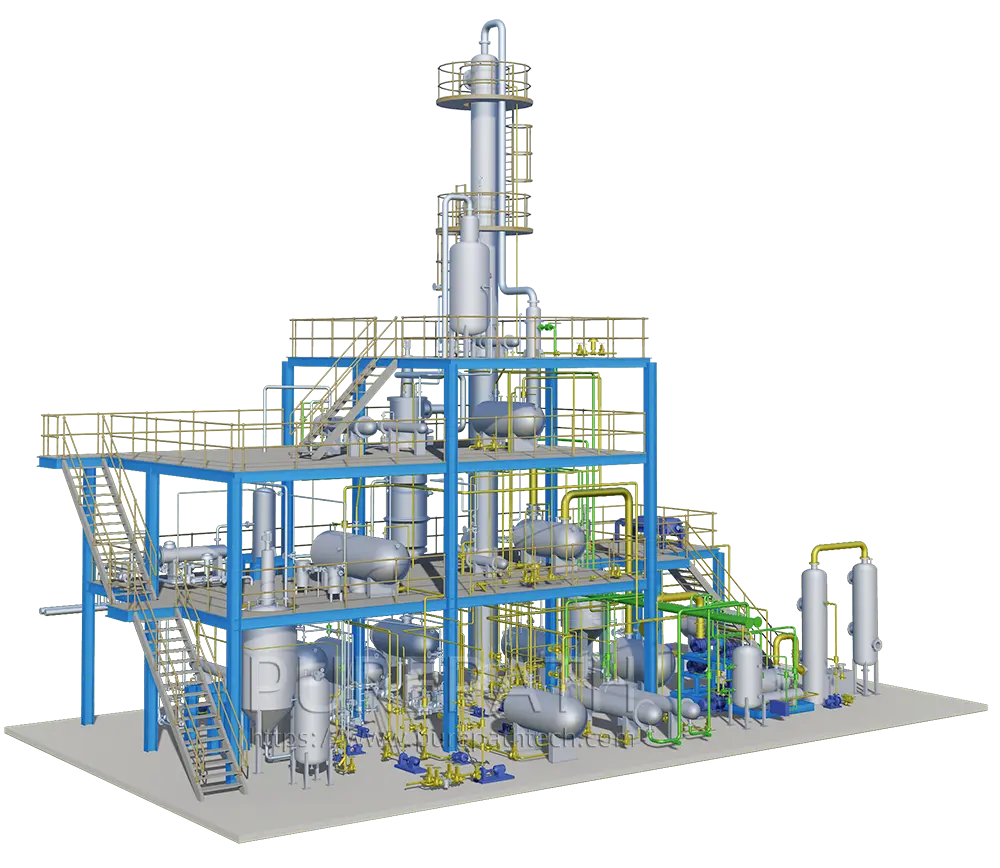
Conclusion and the Future of Used Oil Re-Refining
Both solvent extraction and hydrotreating represent indispensable technologies within the used oil re refining industry, each offering a distinct set of advantages and disadvantages. The selection of the most appropriate technology depends on a complex interplay of factors, including the feedstock characteristics, desired product quality, economic considerations, and environmental regulations.
As the global demand for sustainable industrial practices and high-performance lubricants continues to escalate, ongoing advancements in both solvent extraction and hydrotreating technologies, potentially leading to the development of more efficient and environmentally benign processes, will be crucial in maximizing the potential of used oil re-refining as a cornerstone of a truly circular economy for valuable petroleum resources. Continued innovation in this field is essential for a more sustainable future.