Solvent Extraction for Lubricant Oil Recycling
The ever-growing demand for lubricants in our industrialized world necessitates responsible management of used oil. Lubricant oil recycling offers a sustainable alternative to traditional disposal methods, reducing environmental impact and conserving valuable resources. Solvent extraction is a highly effective method for recycling used lubricant oil, transforming it into high-quality base oil for reuse.
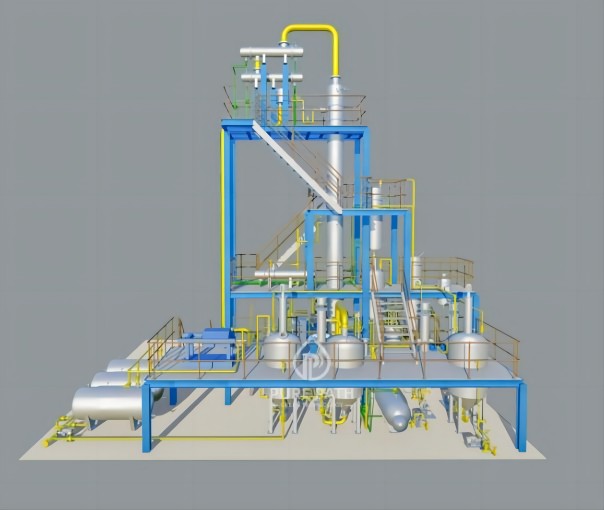
Importance of Lubricant Oil Recycling
Used lubricant oil, if not disposed of properly, poses a significant threat to the environment. Improper disposal can contaminate soil and water sources, harming wildlife and ecosystems. Recycling used oil offers a multitude of benefits:
- Environmental Protection: Recycling used oil reduces the need to extract virgin crude oil, a non-renewable resource. It also prevents contamination from improper disposal, protecting soil and water resources.
- Resource Conservation: By recycling used oil, we conserve a valuable resource and reduce our dependence on virgin crude oil extraction.
- Energy Savings: Recycling used oil requires less energy than refining virgin crude oil.
- Economic Benefits: A robust used oil recycling industry creates jobs and promotes a circular economy.
Solvent Extraction Technology
Solvent extraction is a process that utilizes a solvent to selectively dissolve desired components from a mixture. In the context of lubricant oil recycling, the solvent selectively dissolves valuable base oil from the used oil, leaving behind contaminants like water, dirt, and degraded additives.
A solvent extraction plant for used oil recycling consists of several key components:
- Feedstock Pre-treatment: Used oil undergoes pre-treatment to remove large solids and water. This may involve filtration, settling tanks, or centrifuges.
- Extraction Unit: The pre-treated oil is mixed with a carefully chosen solvent in the extraction unit. The solvent dissolves the desired base oil components, while the contaminants remain undissolved. Common solvents used include N-methyl-2-pyrrolidone (NMP) and furfural.
- Separation Unit: The mixture from the extraction unit is transferred to a separation unit, where the oil and solvent are separated. This may involve settling tanks or centrifuges.
- Distillation Unit: The separated oil-solvent mixture is fed into a distillation unit, typically a thin-film evaporator. This unit operates under vacuum and low temperatures, allowing for efficient separation of the oil from the solvent. The clean, re-refined base oil is recovered, and the solvent is evaporated for reuse in the process.
- Solvent Recovery Unit: The evaporated solvent from the distillation unit is captured and purified in the solvent recovery unit. This ensures the solvent remains clean and can be continuously recycled within the system.
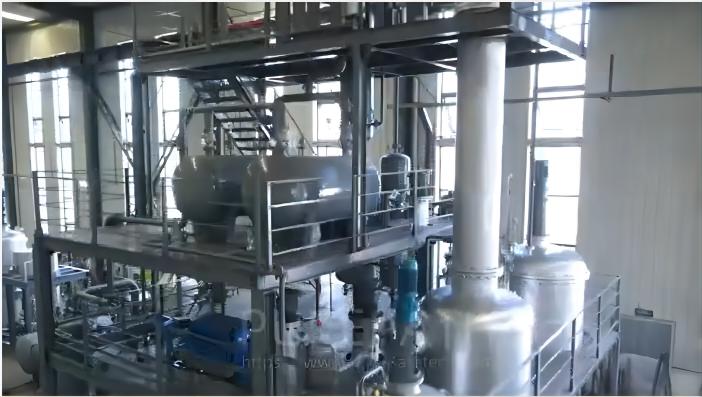
The Solvent Extraction Process
The solvent extraction process for lubricant oil recycling can be broken down into three main stages:
1. Used Oil Pre-treatment: The used oil undergoes a rigorous pre-treatment stage to remove any large contaminants that could interfere with the extraction process. This typically involves filtration to remove solid particles and potentially settling tanks or centrifuges to remove water. Pre-treatment ensures optimal performance in the subsequent stages.
2. Solvent Extraction and Separation of Contaminants: The pre-treated oil is mixed with the chosen solvent in the extraction unit. The solvent selectively dissolves the valuable base oil components, leaving behind contaminants like water, dirt, and degraded additives. The mixture then enters a separation unit, where the oil and solvent are separated using settling tanks or centrifuges.
3. Distillation of Clean Oil and Solvent Recovery: The separated oil-solvent mixture is fed into a thin-film evaporator operating under vacuum and low temperatures. This allows for efficient separation of the re-refined base oil from the solvent. The clean oil is recovered, and the evaporated solvent is captured and sent to the solvent recovery unit. Here, the solvent is purified and recycled back into the extraction process, minimizing solvent waste.
Products and Applications of Solvent Extraction
A. Re-refined Base Oil: The primary product of a solvent extraction plant is high-quality re-refined base oil. This base oil can be further processed and blended with additives to create various types of lubricants, including:
- Engine oils
- Hydraulic fluids
- Gear oils
- Industrial lubricants
The quality of re-refined base oil from solvent extraction can be comparable to virgin base oil, making it a viable and sustainable alternative for a wide range of lubricant applications.
B. Byproducts and Waste Management: The solvent extraction process generates some byproducts, such as asphaltenes (heavy hydrocarbons) and sludge containing contaminants removed from the used oil. These byproducts can be further processed for energy recovery or used in specific industrial applications. Strict regulations govern the management of these byproducts to minimize environmental impact.
Considerations for Setting Up a Solvent Extraction Plant
1. Cost Factors: Setting up a solvent extraction plant requires significant investment in capital equipment, including pre-treatment units, extraction vessels, distillation units, and solvent recovery systems. Operational costs include solvent purchase, energy consumption, and waste management. However, these costs can be offset by the value of the recovered base oil and potential government incentives for used oil recycling programs.
2. Environmental Regulations and Safety Measures: Solvent extraction plants are subject to stringent environmental regulations regarding solvent emissions, wastewater treatment, and byproduct disposal. Safety measures are crucial to prevent accidents and environmental contamination. These factors necessitate careful planning, adherence to regulations, and implementation of robust safety protocols.
3. Market for Re-refined Oil: The success of a solvent extraction plant depends heavily on the market for re-refined base oil. Factors to consider include demand for recycled lubricants, competition from virgin base oil producers, and pricing strategies. Building strong relationships with lubricant manufacturers and exploring potential applications in industrial sectors can help ensure a steady market for re-refined oil.
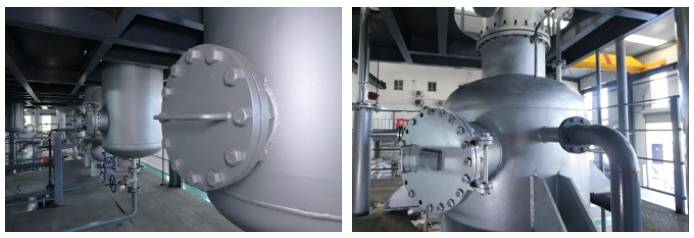
Conclusion
Solvent extraction offers a powerful solution for lubricant oil recycling. This technology not only protects the environment by reducing reliance on virgin crude oil and preventing improper disposal of used oil, but it also conserves resources and promotes a circular economy. While factors like cost, regulations, and market demand require careful consideration, the benefits of solvent extraction for lubricant oil recycling are undeniable. As technology continues to develop and environmental concerns rise, solvent extraction is poised to play a key role in a more sustainable future for the lubricant industry.