Solvent Extraction Plant for Group 1 Based Oil Extraction from Waste Oil
The disposal of waste oil poses a significant environmental challenge worldwide. Traditional disposal methods, such as incineration and landfilling, contribute to air and soil pollution. As environmental regulations become increasingly stringent, there is a growing need for sustainable and efficient waste oil treatment technologies. The recovery of valuable resources from waste oil, particularly base oils, has gained significant attention. Among the various types of base oils, Group 1 base oil remains a crucial component in the lubricant industry due to its versatile properties. This article explores the application of a solvent extraction plant for the efficient extraction of Group I base oil from waste oil.
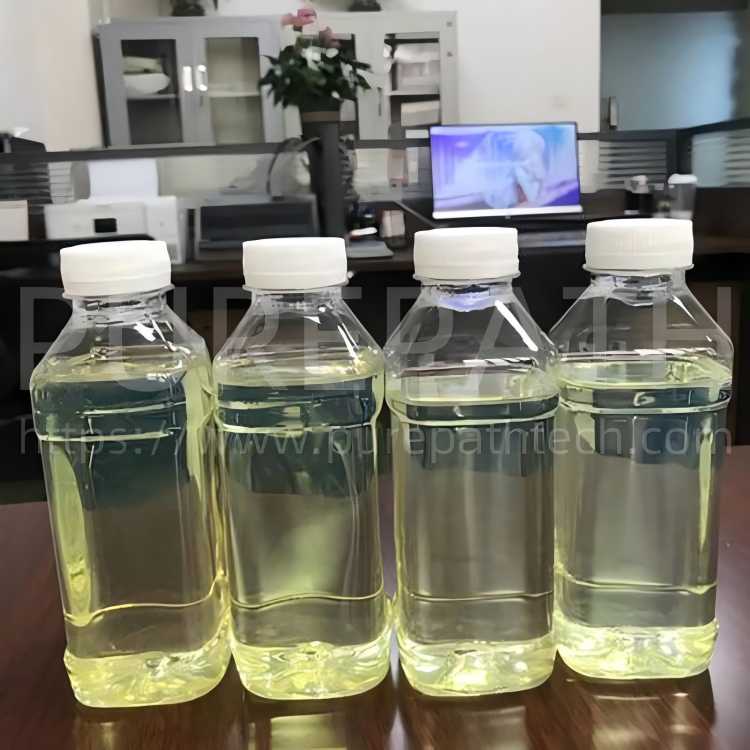
Solvent Extraction Principle
Solvent extraction is a separation technique that uses a solvent to selectively dissolve and remove unwanted components from a mixture. In the context of waste oil recycling, solvent extraction helps separate Group 1 base oil from contaminants such as oxidation byproducts, heavy metals, and sludge.
The efficiency of solvent extraction depends on the principle of differential solubility—where certain compounds dissolve more readily in a chosen solvent than others. By carefully selecting a suitable solvent, impurities can be effectively removed, leaving behind high-purity base oil.
Commonly used solvents in waste oil extraction include propane, butane, and N-methyl-2-pyrrolidone (NMP). These solvents have different solubility characteristics for different components in waste oil, and their selection depends on the specific composition of the waste oil and the requirements of the extraction process.
The solvent extraction process typically involves the following steps:
- Pretreatment: Before extraction, waste oil needs to be pre-treated to remove large-sized impurities, water, and some solid particles. This can be achieved through methods such as filtration and centrifugation.
- Extraction: The pretreated waste oil is mixed with the selected solvent in a countercurrent extraction column or other suitable equipment. The mixing process can be carried out in a stirred tank or a continuous mixer to ensure good contact between the two phases. The solvent selectively dissolves the base oil components, forming a solvent-rich phase (extract).
- Separation: The extract is separated from the extract phase containing the extracted Group 1 base oil and the raffinate phase containing the remaining impurities and unextracted components using gravity separation, centrifugation, or other separation techniques.
- Solvent Recovery: The solvent is recovered from the extract through distillation or other separation methods and recycled back into the process.
- Base Oil Refining: The recovered base oil may undergo further refining steps, such as hydrotreating or clay treatment, to improve its quality and meet the required specifications.
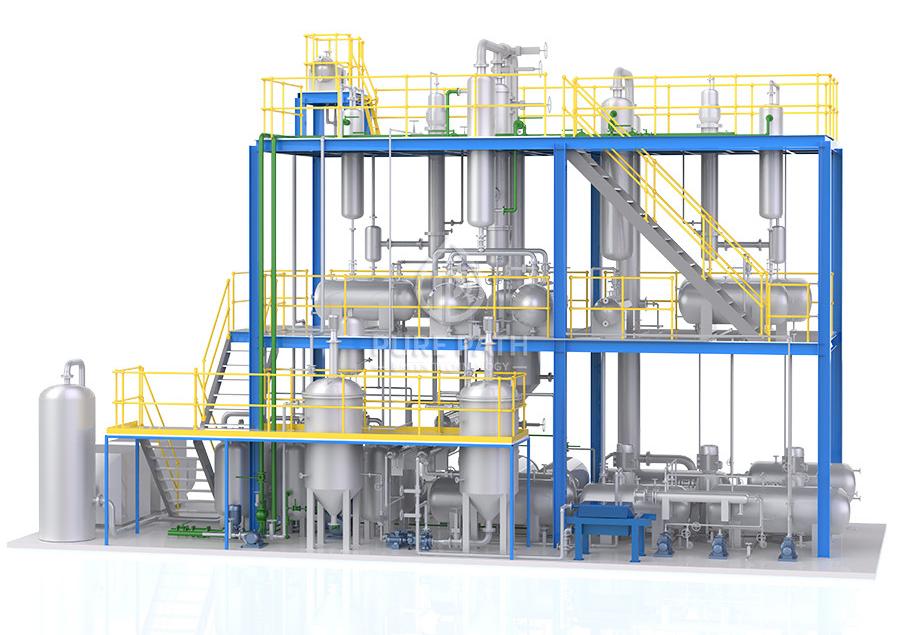
Characteristics of Group 1 Base Oil
Chemical Composition and Physical Properties of Group 1 Base Oil
Group 1 base oils are characterized by their relatively low viscosity index (80-120) and high sulfur content (>0.03%). They are typically produced through solvent refining processes, which involve the removal of impurities and undesirable components from the crude oil. Group 1 base oils are composed mainly of saturated hydrocarbons (<90%), with a significant proportion of aromatic compounds.
The physical properties of Group 1 base oils, such as viscosity, pour point, and flash point, make them suitable for a wide range of lubricant applications. However, their relatively low viscosity index and high sulfur content limit their use in high-performance lubricants, where higher-quality base oils, such as Group 2 or Group 3, are preferred.
Advantages and Applications of Group 1 Base Oil in the Lubricant Industry
Despite their limitations, Group I base oils offer several advantages in the lubricant industry. They are cost-effective and readily available, making them a popular choice for general-purpose lubricants. Group 1 base oils are commonly used in the formulation of industrial lubricants, automotive engine oils, and metalworking fluids.
Comparison with Other Base Oil Groups
Group 1 base oils differ significantly from other base oil groups, such as Group 2 and Group 3, in terms of their chemical composition and performance characteristics. Group 2 base oils, for example, have a higher VI and lower sulfur content, making them more suitable for high-performance lubricants. Group 3 base oils, on the other hand, are highly refined and have an even higher viscosity index, making them ideal for premium lubricants.
Despite these differences, Group 1 base oils remain an important component of the lubricant industry, particularly in applications where cost and availability are critical factors.
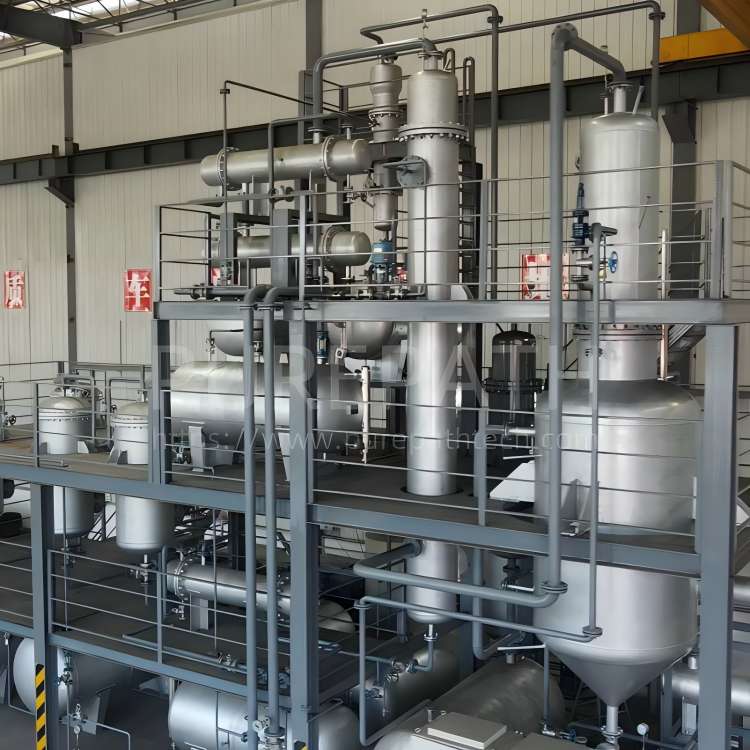
Quality Standards and Group 1 Base Oil Specifications for Recycled Base Oils
The production of high-quality recycled base oils, particularly Group 1 base oils, necessitates adherence to stringent quality standards to ensure they are suitable for diverse applications. These standards are not merely guidelines; they are critical benchmarks that define the performance and reliability of the final product. Specifically, these standards encompass a range of essential specifications, including viscosity at various temperatures, viscosity index (VI), flash point, pour point, sulfur content, saturates content, and total acid number (TAN). These parameters collectively determine the suitability of the base oil for its intended use.
For Group 1 base oils, these specifications are particularly important due to their inherent characteristics. The group 1 base oil specifications typically outline ranges for these properties, ensuring that the oil performs predictably under varying conditions. For instance, viscosity specifications define the oil’s resistance to flow, which is crucial for lubrication performance. The viscosity index indicates how the viscosity changes with temperature, a vital factor for applications in extreme temperature environments. Flashpoint specifies the temperature at which the oil vapors ignite, ensuring safety during handling and operation. Sulfur content and saturated content influence the oil’s oxidation stability and overall performance.
Organizations like the American Petroleum Institute (API), the International Organization for Standardization (ISO), and the European Lubricating Grease Institute (ELGI) have established comprehensive guidelines and specifications for base oil quality. These standards provide a framework for manufacturers and users to ensure consistency and reliability. For regenerated Group 1 base oils, these specifications must be rigorously met to guarantee their equivalence to virgin base oils.
Solvent extraction plant plays a pivotal role in achieving these quality standards. The ability to precisely control the regeneration process through optimization of extraction parameters, such as solvent-to-oil ratio, extraction temperature, and the number of extraction stages, is essential. By fine-tuning these variables, it is possible to tailor the properties of the regenerated base oil to meet or even exceed the required specifications. This level of control is crucial for consistently producing Group 1 base oils that adhere to rigorous standards.
To ensure compliance with the group 1 base oil specifications, a variety of analytical techniques are employed. Common quality assessment methods include:
- Viscosity Measurements: These tests determine the oil’s resistance to flow at specific temperatures, crucial for lubrication performance.
- Gas Chromatography (GC): This technique separates and quantifies the different hydrocarbon components in the base oil, providing detailed information about its composition.
- Mass Spectrometry (MS): This method identifies the molecular weight and structure of the oil’s components, aiding in the determination of saturates and other critical parameters.
- Infrared Spectroscopy (IR): This technique identifies functional groups and chemical bonds in the oil, providing insights into its chemical composition and potential contaminants.
- Total Acid Number (TAN) and Total Base Number (TBN) tests: These determine the acidity or alkalinity of the oil, which impact the oils degradation overtime.
- Flash and Pour Point Testing: These tests determine the temperature at which the oil will ignite and the temperature at which it ceases to flow.
These analytical methods provide detailed information about the chemical composition and physical properties of the regenerated base oil, enabling manufacturers to verify compliance with the group 1 base oil specifications. This rigorous quality control process ensures that regenerated base oils can be used confidently in a wide range of applications, contributing to both environmental sustainability and economic efficiency.
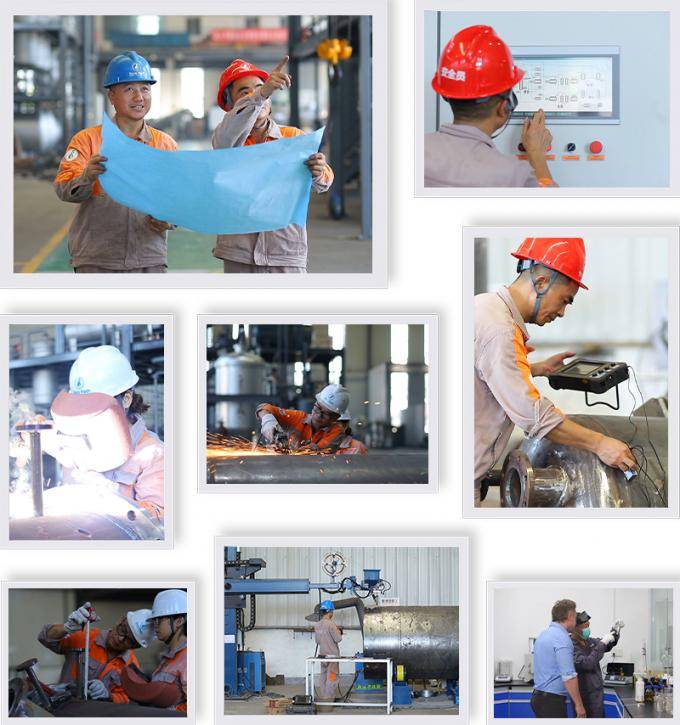
Applications of Recycled Group 1 Base Oils
Recycled Group 1 base oils find applications in a wide range of industries, including automotive, industrial, and marine. In the automotive sector, they are used in engine oils, transmission fluids, and hydraulic fluids. In the industrial sector, they are used in gear oils, turbine oils, and compressor oils. The use of recycled Group 1 base oil offers significant environmental and economic advantages. It reduces the demand for virgin base oils, conserving natural resources and reducing greenhouse gas emissions. Additionally, it lowers the cost of waste oil disposal and creates a circular economy for lubricants.
The market for recycled base oils is expected to grow significantly in the coming years, driven by increasing environmental awareness and stricter regulations. Advances in solvent extraction plants and other recycling processes will further enhance the quality and availability of recycled base oils.
Advantages of Using a Solvent Extraction Plant for Group I Base Oil Extraction from Waste Oil
The use of solvent extraction units to recover Group 1 base oils from waste oil offers several significant advantages, making it a highly efficient and sustainable method for resource recovery.
- Efficient Separation: Solvent extraction effectively isolates the desired components from waste oil, significantly enhancing the extraction efficiency of base oils. This precision ensures that the target substances are extracted with minimal loss, maximizing the yield of usable base oils.
- Quality Assurance: By meticulously controlling the extraction conditions—such as temperature, pressure, and solvent composition—the process guarantees that the final product meets stringent quality standards. This level of control is crucial for industries that rely on consistent and high-quality base oils for their operations.
- Environmental Benefits: Solvent extraction reduces the environmental impact of waste oil by preventing its improper disposal, which can lead to soil and water contamination. Instead, it promotes the recycling and reuse of resources, contributing to a more sustainable and eco-friendly approach to waste management.
- Economic Benefits: Solvent extraction process lowers the production costs of base oils by utilizing waste oil as a raw material, thereby reducing the need for virgin resources. Additionally, it adds value to what would otherwise be considered waste, creating a new revenue stream and enhancing the overall profitability of the operation.
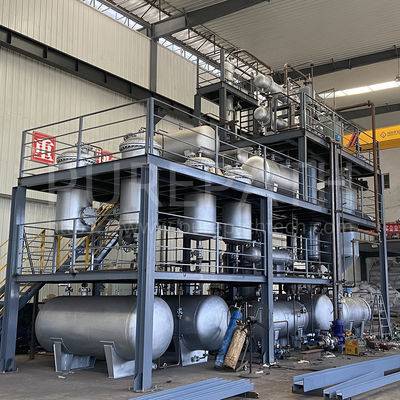
In Summary
Solvent extraction plant plays a crucial role in the efficient and sustainable regeneration of Group I base oils from waste oil. It offers a viable solution to the environmental challenges associated with waste oil disposal, while also providing economic benefits. The future of regenerated base oils looks promising, with increasing demand and advancements in technology driving further growth. As we move towards a more sustainable future, the importance of waste oil recycling and resource recovery will continue to grow.