Technological Advancements and Efficiency of Waste Oil Distillation
Every year, millions of gallons of used oil reach the end of their lifespan. Disposing of this waste oil improperly can have disastrous consequences for the environment, contaminating soil and water sources. Thankfully, waste oil distillation offers a solution, transforming this hazardous waste into valuable resources. However, traditional methods have limitations, prompting the development of new technologies that are enhancing efficiency and sustainability.
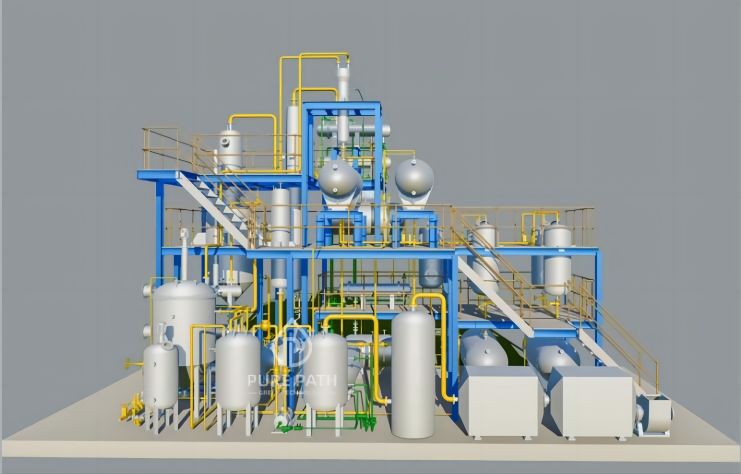
Traditional Ways of Waste Oil Distillation
While effective in its function, traditional atmospheric distillation for waste oil processing has limitations that modern technologies aim to overcome. Here’s a deeper dive into this method:
The Process:
- Pre-treatment: The used oil undergoes an initial stage to remove impurities like water, dirt, and metal shavings. This often involves settling, filtration, or centrifugation.
- Heating: The oil is then fed into a distillation tank equipped with a heating element. The temperature is gradually increased, typically reaching between 300°C and 400°C (572°F – 752°F).
- Vaporization and Separation: As the oil heats, its various components begin to vaporize at different temperatures due to their varying volatilities. Lighter components like gasoline and diesel evaporate first, followed by heavier fractions like lubricating oils and asphaltic residues.
- Condensation and Collection: The vaporized components rise through a fractionation column containing trays or packing materials that help condense them at specific temperatures. These condensed fractions are then collected in separate containers.
- Residue Removal: The remaining heavy residue, often called bottom oil or asphalt, is drained from the distillation tank.
Limitations of Traditional Methods:
- High Energy Consumption: Maintaining such high temperatures throughout the process requires significant energy input, making it expensive and leaving a large carbon footprint.
- Limited Control and Product Quality: The high temperatures can lead to the breakdown of valuable components in the oil, reducing its quality and limiting its potential uses. Some lighter fractions might even be lost due to excessive heat.
- Environmental Concerns: Traditional methods often lack proper emission control systems, releasing harmful fumes and volatile organic compounds (VOCs) into the atmosphere, contributing to air pollution.
- Safety Risks: Operating at high temperatures and handling flammable materials inherently poses safety risks if not conducted with proper precautions and equipment.
While traditional distillation has played a crucial role in managing waste oil, these limitations highlight the need for cleaner and more efficient technologies that are driving the future of waste oil processing.
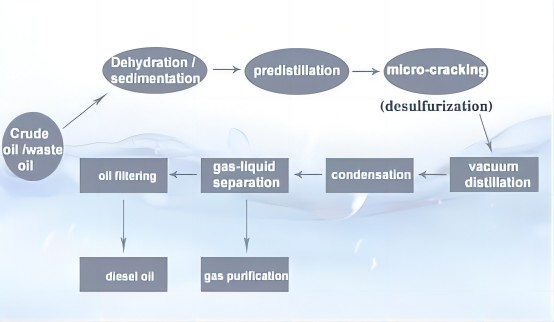
Efficiency improvements in Waste Oil Distillation
The advancements in waste oil distillation technology go beyond mere buzzwords and translate into tangible benefits for both the environment and your bottom line. Let’s delve deeper into the specific efficiency improvements offered by these innovative methods:
1. Energy Efficiency:
- Vacuum Distillation: Operating under reduced pressures enables substantial decreases in energy usage. Research indicates that compared to atmospheric distillation, vacuum distillation can cut energy consumption for the process by up to 50%.
- Thin-Film Distillation: The thin layer of oil facilitates greater heat transfer surface area, resulting in quicker processing times and notable energy savings. When contrasted with conventional techniques, thin-film distillation can achieve similar product quality while consuming up to 70% less energy.
2. Enhanced Product Quality:
- Lower Operating Temperatures: Conventional methods often subject oil to high temperatures, causing thermal cracking, which degrades valuable components and compromises final product quality. Modern technologies such as vacuum and thin-film distillation operate at lower temperatures, minimizing thermal cracking and preserving the oil’s valuable properties.
- Improved Distillation Efficiency: By establishing a more controlled environment with precise temperature and pressure management, these advanced methods ensure better separation of various oil components, leading to a higher-quality and more uniform final product.
3. Reduced Environmental Impact:
- Lower Emissions: The reduced energy consumption linked with newer technologies results in decreased greenhouse gas emissions, contributing to a smaller carbon footprint and a more sustainable waste management strategy.
- Cleaner Processing: Conventional methods may produce harmful emissions during the heating process. Newer technologies often employ closed-loop systems to capture and condense these emissions, mitigating their release into the environment. This helps minimize air pollution and safeguard human health.
4. Other Considerations:
- Reduced Waste Generation: Some advanced distillation technologies also minimize the generation of waste sludge during the process, further lessening the environmental impact and simplifying waste disposal procedures.
- Cost Savings through Increased Efficiency: By reducing energy consumption and potentially lowering waste disposal expenses, these innovations can yield significant cost savings for waste oil processors, rendering the process more economically feasible and encouraging wider adoption.
Overall, the efficiency improvements offered by these advancements are substantial and multifaceted. They contribute to a more sustainable future by reducing the environmental impact of waste oil management, while also providing economic benefits for businesses and organizations involved in waste oil processing.
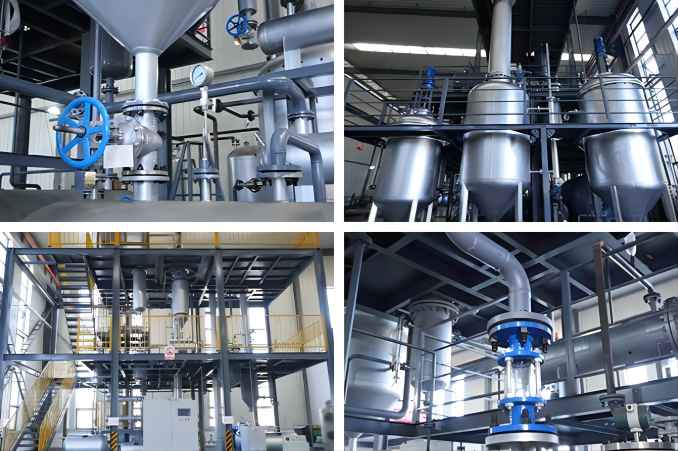
Where to Find Good Waste Oil Distillation Machine?
PurpathTech, a leading Chinese manufacturer specializing in waste oil recycling solutions, is dedicated to driving efficiency and sustainability in the waste management sector. The company offers customized waste oil distillation machines designed to cater to diverse processing needs. Their state-of-the-art equipment seamlessly integrates advanced technologies. These innovations ensure significant energy savings, superior product quality, and minimized environmental impact throughout the recycling process.
PurpathTech‘s solutions are tailored to transform various types of waste oil, including used engine oil, lubricant oil, and pyrolysis oil, into valuable resources like diesel fuel and base oil. With a strong focus on research and development, PurpathTech remains at the forefront of technological advancements, continuously enhancing the efficiency and environmental friendliness of its waste oil distillation solutions.
If you have any interest in our products and services, do not hesitate to contact us!