The End Products of a Waste Oil Recycling Plant: From Waste to Wealth
For far too long, used oil was viewed as a dirty byproduct of our technological world, destined to pollute soils and waterways. But thanks to the ingenuity of waste oil recycling plants, this grimy residue is undergoing a remarkable transformation, becoming the source of a diverse range of valuable commodities. Understanding the end products of these plants not only sheds light on their environmental significance but also reveals the intricate dance between waste oil processing and its subsequent economic benefits.

Understanding the Type of Base Oil
Prior to delving into the downstream derivatives, a thorough understanding of the foundational element is crucial – base oil, the very lifeblood of lubricants. These hydrocarbon fluids, meticulously categorized based on their intrinsic properties like viscosity and chemical composition, permeate a vast array of applications, from the engines of our personal vehicles to the intricate gears of industrial machinery. For waste oil recycling facilities, the initial step lies in meticulously analyzing the type of base oil present within the used oil, as this critical element dictates the potential and limitations of the final products. Let us now embark on a technical odyssey, dissecting the intricacies of base oil classifications:
Group I: Representing the bedrock of conventional lubrication, Group I oils are derived directly from crude oil, exemplified by the mineral oils found in older automobiles. While not the most pristine option in terms of environmental impact, their inherent robustness allows for effective recycling after appropriate treatment.
Group II: Ascending the ladder of sophistication, Group II oils undergo a hydrotreating process, significantly enhancing their performance characteristics and extending drain intervals. Due to this improved functionality, many waste oil recycling plants prioritize the recovery and refinement of this base oil for reuse.
Group III: Entering the realm of synthetic marvels, Group III oils boast exceptional performance attributes and environmental advantages. Often derived from natural gas or other non-petroleum sources, these oils offer unparalleled thermal stability and oxidation resistance, contributing to extended equipment lifespans and reduced energy consumption. While technically recyclable, the intricate molecular architecture of Group III oils presents unique challenges in the recycling process, requiring specialized technologies and methodologies.
How One Industry Transforms Waste into Treasure?
Waste oil recycling machines aren’t mere waste disposal centers; they’re miniature refineries that transmute what was once considered spent lubricant into a spectrum of valuable products. The journey begins with a meticulous pre-treatment stage, where the oil undergoes a rigorous feedstock characterization to assess its composition and potential. This crucial step employs a battery of analytical techniques, from Fourier-transform infrared spectroscopy (FTIR) to Karl Fischer titration, to identify and quantify contaminants like water, solids, and trace metals. These unwanted elements are then efficiently removed through a combination of gravity separation, centrifugation, and microfiltration, akin to meticulously sifting precious jewels from the dust.
Next comes the fractional distillation, the heart of the operation and a testament to the ingenuity of chemical engineering. Imagine a multi-stage behemoth, a towering column meticulously heated to precise temperature gradients. As the oil ascends this thermal ladder, its diverse constituents succumb to the dictates of their volatilities. Lighter fractions, like gasoline and diesel, evaporate first, captured and destined for a second life in fuel blends. Heavier components, along with asphaltenes and resins, condense at higher temperatures, forming sludges and residues earmarked for further processing or responsible disposal through dedicated pathways like co-processing in cement kilns.
The remaining base oil, the very essence of the lubricant, now undergoes deep purification to reclaim its former glory. This stage is a symphony of chemical refinement, where targeted acid-base neutralization, hydrotreating, and clay adsorption techniques meticulously strip away residual impurities, enhance oxidation stability, and fine-tune viscosity. Finally, a series of final polishing steps, employing advanced filtration technologies, transform the once-darkened oil into a crystal-clear, high-quality base oil, ready to embark on its second act as the lifeblood of new lubricants.
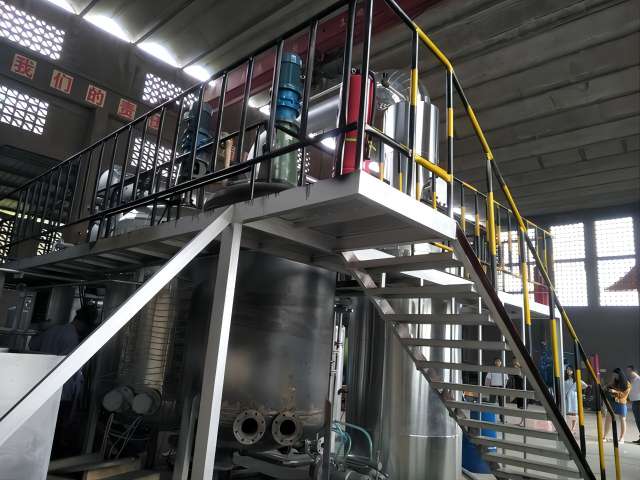
The Multifaceted Potential of Regenerated Base Oil and Beyond
The regenerated base oil, having risen from the ashes of its pre-recycled state, stands as a potent testament to the transformative power of waste oil recycling. This rejuvenated fluid, boasting restored viscosity and performance characteristics, can be directly employed in the formulation of new lubricants. Often blended with virgin oil to create specific viscosity grades and cater to diverse lubrication demands, this recycled base oil offers a compelling alternative to virgin crude oil. This not only reduces our dependence on finite fossil resources but also mitigates the environmental footprint associated with traditional oil extraction and refining, contributing to a more circular economy for lubricants.
However, the magic of waste oil recycling extends far beyond base oil regeneration. These miniature refineries hold a treasure trove of valuable products waiting to be extracted. From the heavier fractions, asphalt emulsions emerge, ready to lend their superior performance and environmental benefits to road paving and construction projects. These emulsions offer a sustainable alternative to traditional asphalt, significantly reducing its associated reliance on fossil fuels and greenhouse gas emissions.
Lighter fractions, on the other hand, find their second life as fuel oil, a potent energy source for industrial boilers and furnaces. This renewable fuel alternative not only provides valuable heat and power but also diverts waste oil from landfills and incineration, contributing to a more sustainable waste management strategy.
The versatility of waste oil doesn’t stop there. Specific oil fractions can be transformed into grease, a crucial lubricant for various industrial and automotive applications. This recycled grease offers a sustainable and cost-effective alternative to traditional petroleum-based lubricants, further reducing our reliance on virgin fossil resources. Finally, solvents extracted from the recycling process offer a sustainable and effective alternative to traditional chemical options for cleaning and degreasing purposes. These eco-friendly solvents minimize the environmental impact associated with traditional cleaning agents, further solidifying the multifaceted benefits of waste oil recycling.
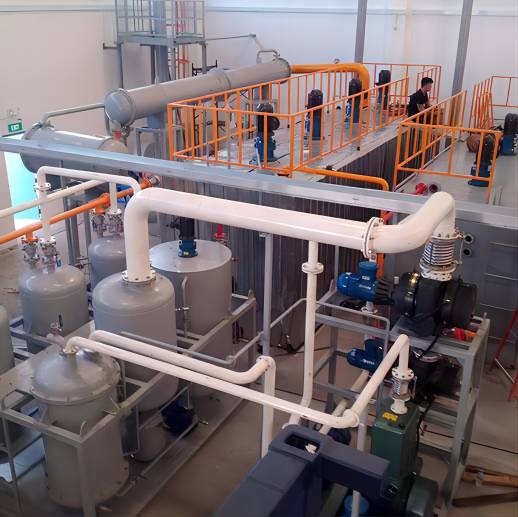
How Waste Oil Fuels a Sustainable Future?
The narrative of waste oil recycling transcends the mere creation of valuable products; it’s a tapestry woven with threads of responsible waste management and a commitment to a sustainable future. While the spotlight shines brightly on the regenerated base oils and repurposed fractions, the story also delves into the responsible handling of what remains – the non-recyclable residues and byproducts.
These residues, a seemingly inevitable consequence of the transformative process, are treated with utmost care. Some, like heavier asphaltene-rich fractions, find new life through energy recovery. These fractions can be co-processed in cement kilns or dedicated facilities, generating valuable thermal energy while diverting waste from landfills. Others, like trace metals or persistent contaminants, are meticulously separated and disposed of in accordance with stringent environmental regulations, ensuring they pose no threat to the environment or human health.
Waste oil recycling facilities, therefore, are not just factories churning out rejuvenated oil; they are vital players in the burgeoning circular economy, where resources are not discarded but cycled through a loop of reuse and recycling. By minimizing reliance on virgin oil extraction, these facilities reduce our dependence on finite fossil resources and the environmental footprint associated with their acquisition. They also play a crucial role in diverting waste oil from landfills and incineration, mitigating the associated environmental and public health risks.
Furthermore, by transforming waste oil into valuable products like fuel oil and asphalt emulsions, waste oil recycling plants contribute to resource conservation. These renewable alternatives not only displace fossil fuel consumption but also offer superior performance and environmental benefits. This shift towards sustainable materials paves the way for a future less reliant on finite resources and more mindful of our ecological footprint.
The journey of waste oil doesn’t end with its transformation into new products. The byproducts, too, are woven into the fabric of this sustainable narrative. Responsible disposal ensures they don’t pose environmental threats, while energy recovery from certain fractions contributes to a greener future. This holistic approach, encompassing the entire lifecycle of the oil from pre-treatment to final disposal, exemplifies the true potential of waste oil recycling.
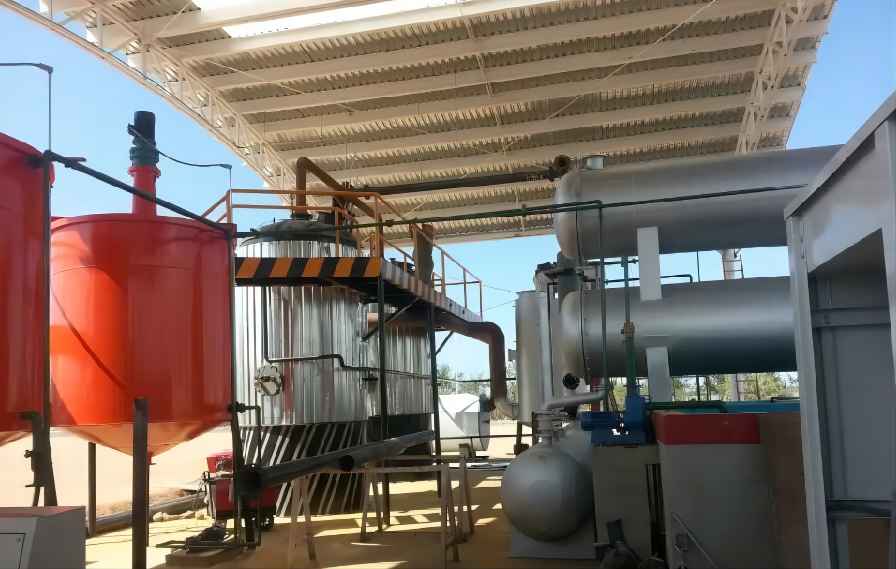
In conclusion, the story of waste oil recycling is not just a tale of ingenuity and innovation; it’s a testament to our collective ability to turn waste into valuable resources. As technology continues to advance and our understanding of waste oil’s potential deepens, the spectrum of end products is bound to expand further. This ongoing evolution not only holds immense promise for environmental sustainability and resource conservation but also paints a brighter picture for a future where waste is not a burden, but an opportunity for transformation and progress. So, the next time you encounter that grimy used oil, remember, it might not be just a dirty byproduct, but a potential treasure trove waiting to be unearthed.