The Environmental Impact of Waste Oil Distillation: Reducing Pollution Through Recycling
Waste oil, particularly from industries and automobiles, poses a significant environmental threat when improperly disposed of. Recycling through processes like waste oil distillation can mitigate these threats, reducing pollution and conserving resources.
Environmental Impact of Improper Waste Oil Disposal
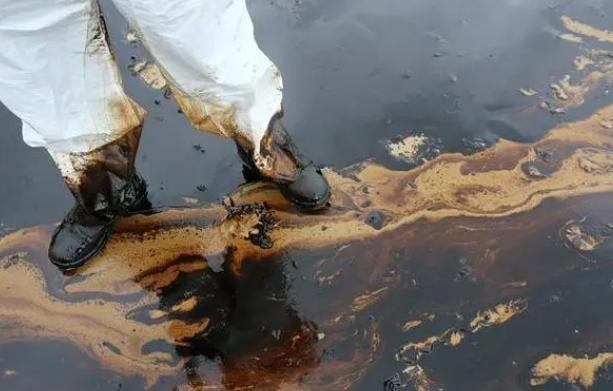
Improper disposal of waste oil poses severe risks to the environment, contaminating ecosystems and endangering public health. Waste oil, which includes used motor oil and industrial lubricants, is often contaminated with hazardous substances such as heavy metals, chemicals, and toxic compounds. When not managed responsibly, this waste can cause significant damage in several ways:
- Soil Contamination: When waste oil is dumped on land or in landfills, it seeps into the soil, disrupting the natural ecosystem. The harmful chemicals in waste oil can render the soil infertile, affecting plant life and microorganisms. Over time, contaminated soil becomes less capable of supporting vegetation and can spread toxins to nearby areas.
- Water Pollution: Waste oil that reaches water bodies is especially dangerous. A small amount of oil can spread over vast surfaces of water, creating a thin film that blocks sunlight and oxygen from reaching aquatic organisms. This leads to oxygen depletion, disrupting aquatic ecosystems and causing the death of fish and other marine life. Additionally, oil-contaminated water sources are difficult and expensive to clean, posing long-term risks to human drinking water supplies.
- Air Pollution: When waste oil is burned as a fuel without adequate filtration, it releases toxic substances into the atmosphere. These emissions contribute to air pollution, including the release of greenhouse gases, and can lead to respiratory problems for nearby populations.
- Wildlife Impact: Animals exposed to oil, particularly in aquatic environments, face dire consequences. Oil can coat the fur and feathers of animals, leading to poisoning, hypothermia, and other health issues that often result in death.
Overall, the improper disposal of waste oil not only causes direct environmental damage but also leads to costly and complex cleanup efforts. Preventing these impacts requires responsible management, such as recycling and distillation, which can transform waste oil into reusable resources and minimize pollution.
The Process of Waste Oil Distillation
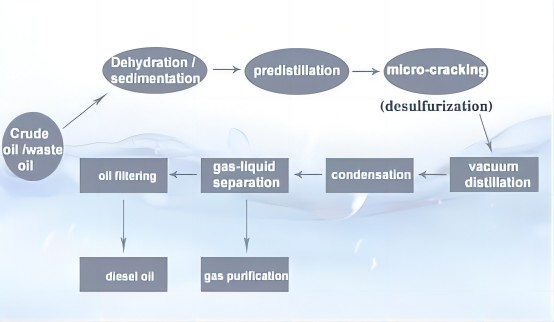
Waste oil distillation is a sophisticated recycling method that transforms used or contaminated oil into reusable products. The process is both environmentally friendly and economically viable, offering a way to manage waste oil while recovering valuable resources. By separating impurities from oil through heat and pressure, distillation allows waste oil to be refined into various useful products such as lubricants, base oils, and even fuels.
Step1: Pre-treatment
The first step in waste oil distillation is the pre-treatment phase. Waste oil, often collected from automotive engines, industrial machinery, and other sources, typically contains a mixture of water, solid particles, sludge, and chemical additives. Pre-treatment involves several filtration and dehydration processes to remove these unwanted contaminants before the oil undergoes distillation.
- Filtration: Solid particles, such as metal shavings, dirt, and debris, are filtered out to prevent them from interfering with the distillation process. This is usually achieved through mechanical filters and centrifuges.
- Water Removal: Waste oil often contains water, either due to contamination or condensation. The water is separated from the oil through processes like settling or heating. Removing water is crucial because it can create problems during the heating phase, causing inefficiencies or unwanted reactions.
- Chemical Treatment: In some cases, chemical additives are used to neutralize certain contaminants or improve the efficiency of the filtration and separation processes.
Step2: Heating and Evaporation
Once the waste oil has been pre-treated, it enters the distillation unit, where it is heated to very high temperatures. This heating causes the oil to vaporize. The distillation process typically occurs under a vacuum, which lowers the boiling point of the oil. This reduces the risk of thermal degradation—where oil molecules break down due to excessive heat—allowing for the recovery of higher-quality oil products.
- Vacuum Distillation: Vacuum distillation operates by lowering the atmospheric pressure inside the distillation chamber. This allows the oil to vaporize at much lower temperatures, preserving the quality of the oil fractions. It also saves energy, as less heat is required.
- Fractional Distillation: During the heating process, the oil breaks down into different components, each of which has a different boiling point. Lighter fractions, such as gasoline-like fuels, vaporize at lower temperatures, while heavier fractions, such as base oils and lubricants, require higher temperatures to vaporize.
The oil is separated into its various components based on their boiling points, with each component collected at different stages in the process.
Step3: Condensation and Fraction Collection
Once the oil is vaporized, the vapor is passed through a series of condensation chambers where it is cooled and condensed back into liquid form. The key to effective distillation is precise temperature control, as this allows for the separation of different fractions at distinct boiling points. As each fraction condenses, it is collected in separate containers for further processing.
- Base Oil Fraction: This fraction is the primary product of the distillation process. It consists of clean, reusable oil that can be refined further and used in various applications such as lubricants, hydraulic fluids, or even fuel.
- Light and Heavy Distillates: In addition to base oil, other fractions such as light distillates (similar to gasoline or kerosene) and heavier distillates (similar to diesel or fuel oil) are recovered. These can also be used for energy production or industrial fuel.
Step4: Post-treatment and Purification
After the distillation process, the collected oil fractions may require additional post-treatment to ensure they meet specific quality standards. This step is crucial to producing high-grade oils suitable for reuse in industries or vehicles. Post-treatment typically involves:
- Hydrogenation: This chemical process is used to remove any remaining impurities, such as sulfur or nitrogen compounds. Hydrogen is added under high pressure to “clean” the oil, resulting in higher purity and better performance in end-use applications.
- Filtration: Fine particulate matter or small contaminants that may have survived the distillation process are removed using specialized filters. This step ensures that the oil is free from any remaining dirt or sludge.
- Additive Blending: In some cases, additives such as anti-oxidants, detergents, or viscosity improvers are blended into the distilled oil to enhance its performance characteristics, particularly if the oil will be reused as a lubricant.
The post-treatment phase guarantees that the recovered oil is of high quality, meeting the necessary industry standards for reuse in engines, machinery, or as fuel.
Step5: Recycling and Reuse
The distillation process also generates by-products, such as residual sludge and ash, which need to be managed responsibly. Waste management systems in distillation plants typically include treatment of these by-products to minimize environmental impact. In some cases, residual products can be treated further for energy recovery or safe disposal. The goal is to minimize the waste generated and ensure that as much of the original waste oil is recycled into usable products as possible.
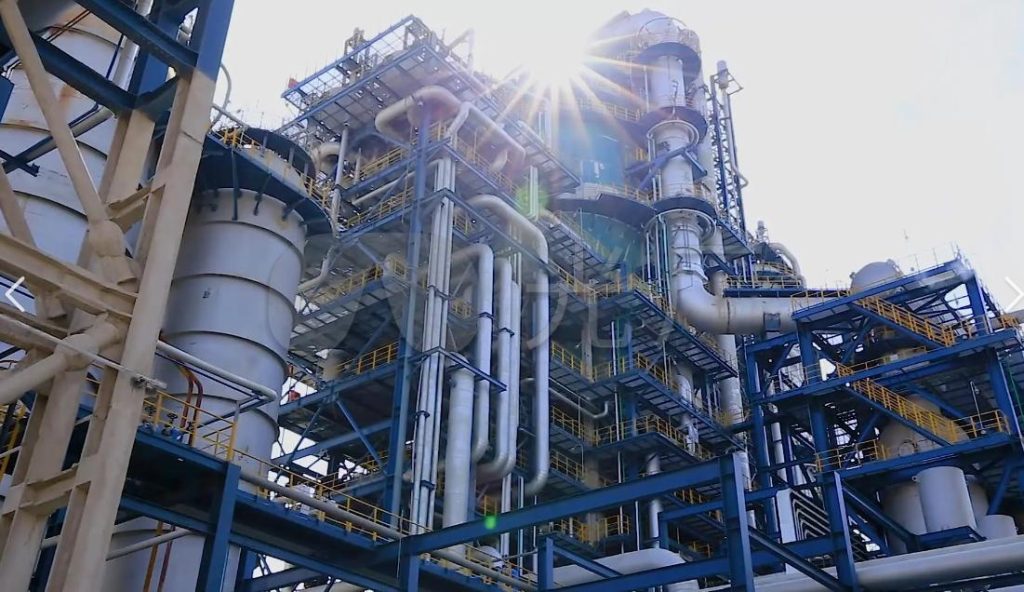
Environmental Benefits of Waste Oil Distillation
Waste oil distillation offers significant environmental benefits by addressing both pollution reduction and resource conservation.
- Reduce hazardous waste: One of the primary advantages is the drastic reduction of hazardous waste. Distillation converts used oil, which contains toxic contaminants like heavy metals and PAHs, into reusable products, reducing the risk of these substances entering ecosystems. This not only protects soil and water resources but also minimizes the health hazards posed to humans and wildlife.
- Protect natural resources: Another key benefit is the conservation of natural resources. Through distillation, valuable oil fractions such as base oils and fuels are recovered, reducing the need for virgin crude oil extraction. This lessens the environmental impact associated with oil drilling, transportation, and refining, while also conserving finite petroleum reserves. The recycled oil can be repurposed for industrial use, cutting down on the reliance on fresh oil production.
- Reduce greenhouse gas emissions: Furthermore, greenhouse gas emissions are significantly reduced through distillation compared to other disposal methods like incineration. Recycling the oil helps avoid the emissions associated with burning waste oil and contributes to a more sustainable approach to energy use.
- Minimize water and soil contamination risks: In addition, water and soil contamination risks are minimized, preventing pollutants from seeping into ecosystems and promoting cleaner, healthier environments. This makes waste oil distillation an environmentally responsible solution for managing industrial and automotive oil waste.
The Technology of Waste Oil Distillation Plant
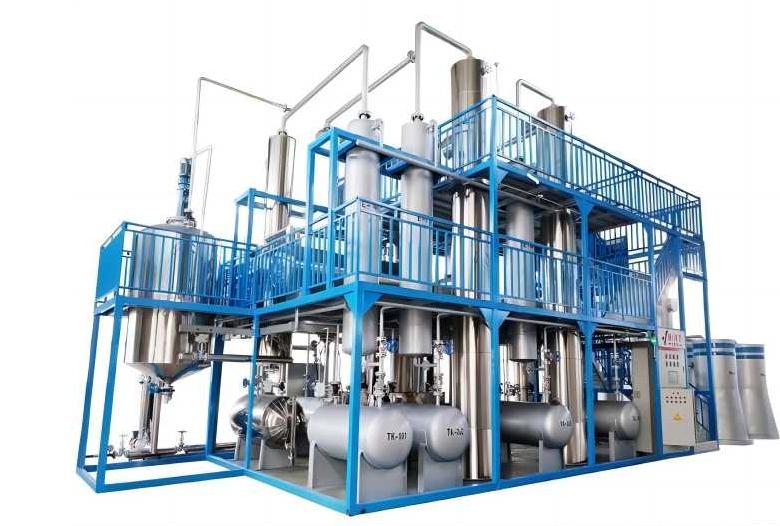
Waste oil distillation plants are equipped with advanced technologies that make the recycling process more efficient and environmentally friendly. These plants operate on both small and large scales, catering to different industries, from automotive service centers to large oil refineries. The technology typically includes:
- Vacuum Distillation Units: One of the primary technologies used is vacuum distillation, which lowers the pressure inside the distillation chamber. By reducing pressure, the oil can be distilled at lower temperatures, preventing thermal degradation of valuable oil fractions. This method improves the quality of the recycled oil and reduces energy consumption, making the process more sustainable.
- Thermal Cracking Systems: In some distillation plants, thermal cracking is utilized to break down large, complex oil molecules into smaller, more usable fractions. This process helps maximize the recovery of useful by-products like diesel or base oils, ensuring that a higher percentage of the waste oil is converted into reusable materials.
- Energy Recovery Systems: Modern distillation facilities often feature energy recovery systems that capture and reuse excess heat generated during the distillation process. By recycling this energy, plants can significantly reduce their overall energy consumption, making the operation more sustainable and cost-effective.
- Automated Control Systems: Automation plays a crucial role in enhancing the operational efficiency of waste oil distillation plants. Advanced control systems monitor critical parameters such as temperature, pressure, and flow rates in real time, ensuring optimal distillation performance and preventing equipment malfunctions. This level of automation also enhances safety by minimizing human error.
- Filtration and Purification Units: After distillation, additional filtration and purification systems are employed to remove residual contaminants from the recovered oil. These units enhance the purity of the recycled oil, making it suitable for reuse in various industries. High-efficiency filters and purification methods ensure that the final product meets stringent quality standards.
Together, these technologies enable waste oil distillation plants to operate with minimal environmental impact while producing high-quality recycled oil. This combination of energy efficiency, automation, and advanced filtration makes the distillation process a crucial component in reducing pollution and promoting sustainable oil recycling.
Improper waste oil disposal severely harms ecosystems, wildlife, and human health. Waste oil distillation offers a practical solution, reducing pollution, conserving resources, and saving energy. Advances in distillation technologies make recycling more efficient and sustainable. By adopting these methods, industries can protect the environment and benefit economically from recovered materials.