The Hydrotreating Process and Its Impact on Group II Base Oil
In the realm of lubricants, base oils form the fundamental component, determining the overall performance and longevity of a lubricant. Among the various grades of base oils, Group II base oil stands out as a popular choice due to its balance of performance and cost-effectiveness. However, to achieve the desired quality standards and meet stringent industry regulations, Group II base oil undergoes a crucial refining process known as hydrotreating.
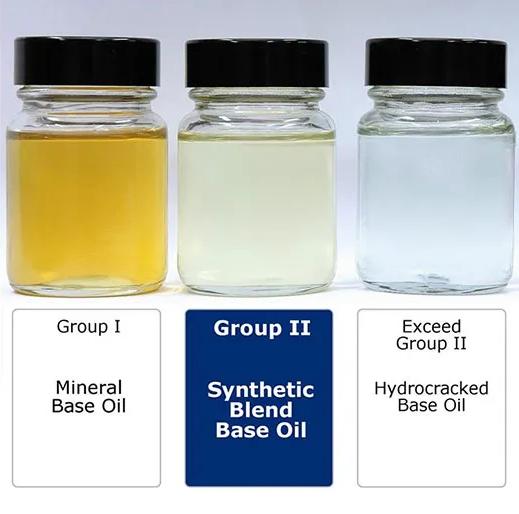
What is Group II Base Oil?
Group II base oils are part of a classification system established by the American Petroleum Institute (API) to categorize base oils based on their sulfur content, saturates, and viscosity index. Group II base oils are characterized by:
- Low Sulfur Content: Typically less than 0.03%, ensuring reduced environmental impact and improved performance in modern engines.
- High Saturate Content: Saturates account for 90% or more of the composition, contributing to their stability and resistance to oxidation.
- Moderate Viscosity Index (VI): A VI of 80–120, indicating a consistent viscosity across a wide temperature range.
These oils are primarily derived from crude oil through extensive refining processes. Their composition makes them a preferred choice for applications requiring high performance and long-lasting durability, such as automotive engine oils, industrial lubricants, and hydraulic fluids.
Why Does Group II Base Oil Need Hydrotreating?
While Group II base oil offers several advantages over its predecessor, Group I, it still contains impurities that can negatively impact its performance and stability. These impurities, if left untreated, can lead to various issues, including:
- Reduced Lubricating Properties: Impurities can interfere with the lubricant’s ability to form a protective film on metal surfaces, leading to increased friction, wear, and energy loss.
- Oxidation: Impurities, particularly unsaturated hydrocarbons and sulfur compounds, can accelerate oxidation, leading to the formation of sludge and varnish. This can clog engine components, reduce efficiency, and increase maintenance costs.
- Corrosion: Sulfur compounds, in particular, can be highly corrosive, leading to metal corrosion and equipment failure.
- Poor Thermal Stability: Impurities can reduce the thermal stability of the base oil, making it more susceptible to breakdown at high temperatures, leading to the formation of deposits and reduced lubricant life.
To mitigate these issues and enhance the overall quality of Group II base oil, it undergoes a rigorous refining process known as hydrotreating.
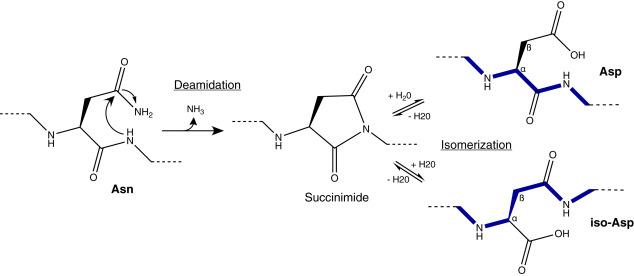
How Does Base Oil Hydrotreating Impact the Quality of Base Oil?
Hydrotreating involves subjecting the base oil to high pressure and temperature in the presence of hydrogen gas and a catalyst. This process leads to several significant improvements in the quality of the base oil:
- Sulfur Reduction: Sulfur compounds are detrimental to the oxidative stability and corrosive properties of lubricants. Hydrotreating effectively removes these compounds, resulting in a base oil with enhanced oxidation resistance and reduced corrosive tendencies.
- Nitrogen Reduction: Nitrogen compounds can contribute to the formation of deposits and sludge in engines and other machinery. Hydrotreating reduces the nitrogen content, minimizing the risk of these issues.
- Saturation of Unsaturated Hydrocarbons: Unsaturated hydrocarbons are susceptible to oxidation, leading to the formation of gums and varnish. Hydrotreating saturates these compounds, improving the oxidative stability and overall performance of the base oil.
- Color Improvement: Hydrotreating can significantly lighten the color of the base oil, making it more visually appealing and often indicative of higher quality.
How Hydrotreating Plants Transform Group II Base Oil
A hydrotreating plant is a complex facility that utilizes a sophisticated process to refine base oil. The key steps involved in the hydrotreating process are as follows:
- Feedstock Preparation: The crude oil or intermediate feedstock is first processed to remove impurities such as water, salt, and solid particles. This ensures a clean feedstock for the hydrotreating process.
- Pretreatment: In some cases, the feedstock may undergo a pretreatment step to remove heavy metals and other contaminants. This step is crucial for optimizing the performance of the hydrotreating catalyst.
- Hydrotreating Reactor: The pretreated feedstock is then pumped into a high-pressure reactor, where it is mixed with hydrogen gas and passed over a catalyst bed. The catalyst, typically composed of metals such as nickel, molybdenum, or cobalt, promotes chemical reactions that remove sulfur, nitrogen, and unsaturated hydrocarbons.
- Product Separation: The effluent from the reactor is cooled and separated into various product streams, including the hydrotreated base oil, hydrogen gas, and other byproducts.
- Product Polishing: The hydrotreated base oil may undergo further polishing steps, such as clay treatment or filtration, to remove any residual impurities and improve its clarity and color.
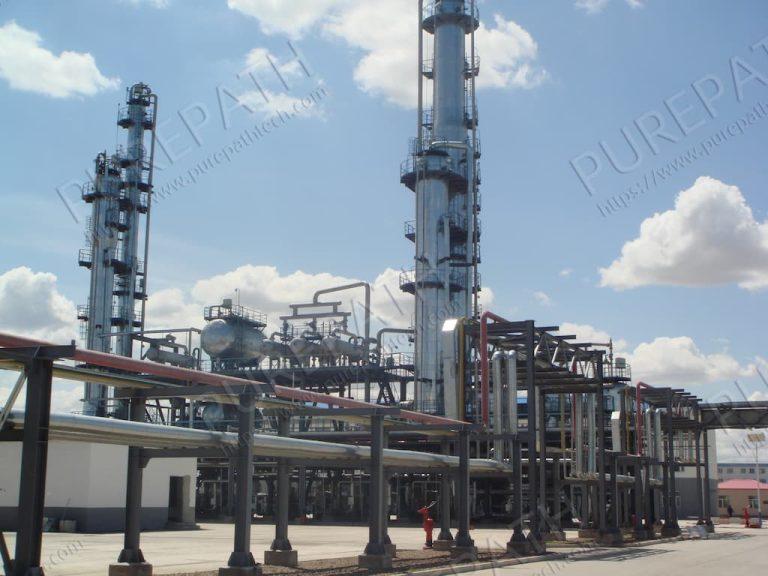
The Role of Hydrotreating Plants
Hydrotreating plants are specialized facilities equipped with advanced technology to carry out the hydrotreating process. These plants play a critical role in the production of high-quality base oils by:
- Optimizing Process Parameters: Hydrotreating plants employ sophisticated control systems to optimize process parameters such as temperature, pressure, and flow rates, ensuring efficient and effective hydrotreating.
- Utilizing Advanced Catalysts: These plants utilize advanced catalysts that are designed to maximize the removal of impurities and improve the overall quality of the base oil.
- Ensuring Product Quality: Rigorous quality control measures are implemented to monitor the quality of the hydrotreated base oil and ensure it meets stringent industry standards.
Wrap Up
Hydrotreating is an essential process for upgrading the quality of group II base oil. By removing impurities and improving the overall performance characteristics, hydrotreating ensures that Group II base oil can meet the demanding requirements of modern lubricants. The availability of advanced hydrotreating technologies and catalysts has enabled the production of high-quality Group II base oils that contribute to the efficient and reliable operation of various machinery and equipment.