The Production Process of Lube Oil: Traditional Methods and Contemporary Developments
Lube oil is a crucial component in various industries, serving to reduce friction and wear in mechanical systems. The production of lubricating oil involves a series of intricate processes that transform raw materials into high-quality, functional products. The primary raw material for lube oil production is heavy oil extracted from crude oil. To create lube oils with different viscosities, heavy oil is distilled into various fractions and residues through a process known as vacuum distillation. These resulting fractions are categorized as fractional lube oils and residual lube oils, each serving different applications due to their varying viscosities.
This article explores the traditional lube oil production methods, commonly referred to as the “old three-step” process, which includes solvent refining, solvent dewaxing, and clay refining. It also touches upon the recent development of lube oil hydroprocessing. The following sections delve into each step of the traditional production process in detail.
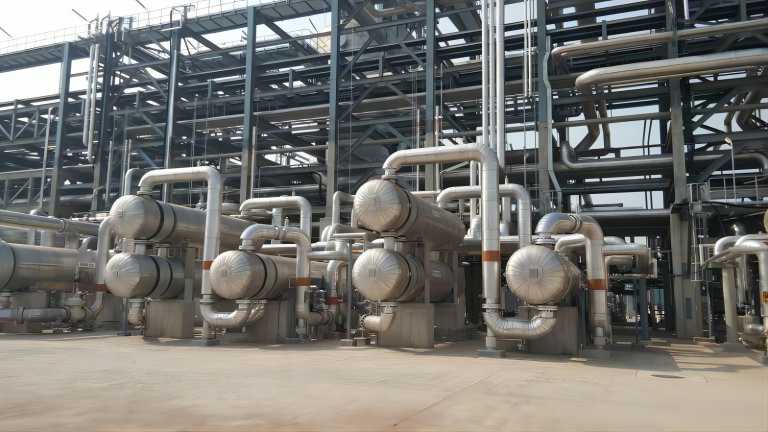
Solvent Refining
Solvent refining is a critical step in improving the quality of lubricating oil by removing undesirable components, such as polycyclic aromatic hydrocarbons, and impurities like resins and asphaltenes. Among various refining methods like acid-base refining, adsorption refining, and hydroprocessing, solvent refining is extensively employed in China.
Solvent refining involves dissolving non-ideal components from lube oil in a selective solvent, separating these components, and subsequently evaporating and recycling the solvent. The choice of solvent is essential for successful solvent refining:
1. Solvent Selection Criteria
- Strong selective dissolution: The solvent must dissolve non-ideal components in the raw oil while minimizing the dissolution of ideal components. This process is essentially solvent extraction.
- Higher density: The solvent, denser than the raw oil, is introduced from the top of the extraction tower, while the oil is introduced from the bottom. As they flow counter-currently, the solvent effectively dissolves non-ideal components from the oil.
- Low boiling point for easy recovery: As the solvent is mostly recycled, its boiling point should be lower than that of the lube oil. This ensures efficient solvent recovery.
- Stability and compatibility: The solvent should be stable at high temperatures and not react chemically with the raw material.
- Non-toxic, non-corrosive, and cost-effective.
Commonly used solvents in China’s refining industry include furfural.
2. Solvent Refining Process
The process involves several key steps:
- Solvent Extraction: The raw oil enters the extraction tower from the bottom and the solvent from the top. The two fluids flow countercurrently, with the solvent dissolving non-ideal components from the oil. The resultant solution is separated into an extract phase (containing non-ideal components) and a raffinate phase (ideal lube oil components).
- Solvent Recovery from Extract Phase: The solvent-rich extract phase is heated to evaporate the solvent. The resulting vapor is condensed, and the solvent is collected for reuse.
- Solvent Recovery from Raffinate Phase: The remaining raffinate phase, containing a small amount of solvent, is also heated to recover the solvent. This solvent can be used again in the extraction process.
- Water Washing of Extract Phase: A small amount of water is introduced to remove any remaining solvents and impurities. The water and solvent separate into distinct layers, making it easier to remove the remaining solvent.
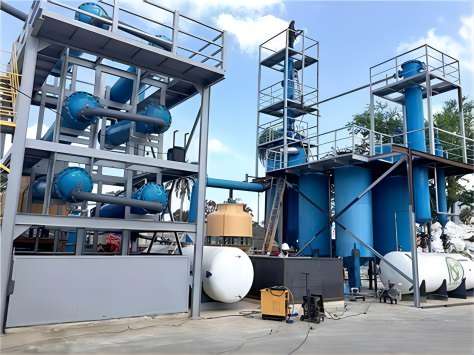
Solvent Dewaxing
Dewaxing aims to lower the pour point of lubricant oil and also yields valuable byproducts like paraffin wax. Solvent dewaxing, among various dewaxing methods, is widely utilized due to its applicability to various lube oil fractions.
In solvent dewaxing, a solvent is mixed with oil to reduce its viscosity. The mixture is then cooled to induce wax crystallization. After the separation of oil and wax, the solvent is recovered and reused. Ketone and benzene-based solvents are commonly used in solvent dewaxing. The process involves several steps, including solvent blending, heating, contact and crystallization, and solvent recovery.
Clay Refining
After solvent refining and dewaxing, the lube oil still contains impurities such as resins, asphaltenes, and residual solvents. Clay refining, also known as adsorption refining, employs activated clay to adsorb these impurities, enhancing oil color, and stability, and reducing remaining carbon.
Activated clay, featuring a porous structure with a large surface area, has strong adsorption capabilities. It selectively adsorbs impurities while sparing lube oil components. The refining process includes mixing oil with activated clay, heating the mixture to enhance adsorption, allowing the clay to adsorb impurities, and finally filtering out the clay. The refined oil can then be obtained.
Lubricant Oil Blending
The quality of lubricant oil relies heavily on both the quality of the base oil and the additives used. Additives can significantly enhance the performance of lube oil, allowing it to meet the specific requirements of various industrial applications. Blending is the final crucial step in the lubricant oil production process.
This involves mixing different viscosity lubricant oil base oils obtained through solvent refining, dewaxing, and clay refining. Appropriate additives are introduced to the mixture to achieve the desired performance characteristics. The selection of lube oil blending components and additives is tailored to the intended application. For instance, blending is performed using low-viscosity base oils and suitable additives to produce 20W machine oil with the desired low viscosity.
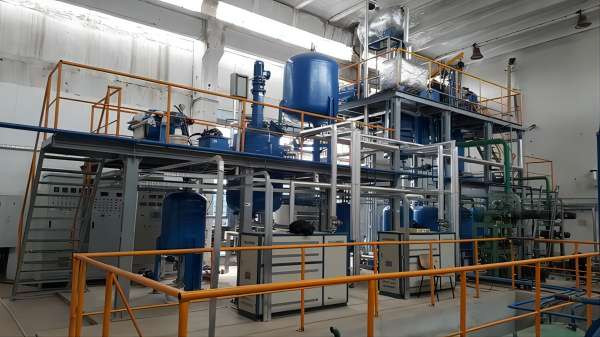
Conclusion
The production of lubricant oil involves intricate processes that significantly impact the final product’s quality and performance. Traditional methods like solvent refining, solvent dewaxing, and clay refining have been widely employed to enhance lube oil quality, and they continue to be essential in the industry. Moreover, contemporary developments such as hydroprocessing have emerged to address evolving demands for lube oil with enhanced properties. Through these processes, lubricating oils are transformed from their raw material state into high-quality products that play a pivotal role in ensuring efficient mechanical operation across various industries.