The Role and Process of the Visbreaking Unit in Petroleum Refineries
Visbreaking, also known as viscosity breaking, is a crucial thermal cracking process employed in petroleum refineries to enhance the quality and value of heavy fuel oil. This process involves subjecting heavy feedstocks, such as residual oils and heavy fuel oils, to high temperatures in the absence or presence of a catalyst. This thermal stress breaks down large, complex hydrocarbon molecules into smaller, more desirable products, effectively reducing the viscosity of the feedstock.
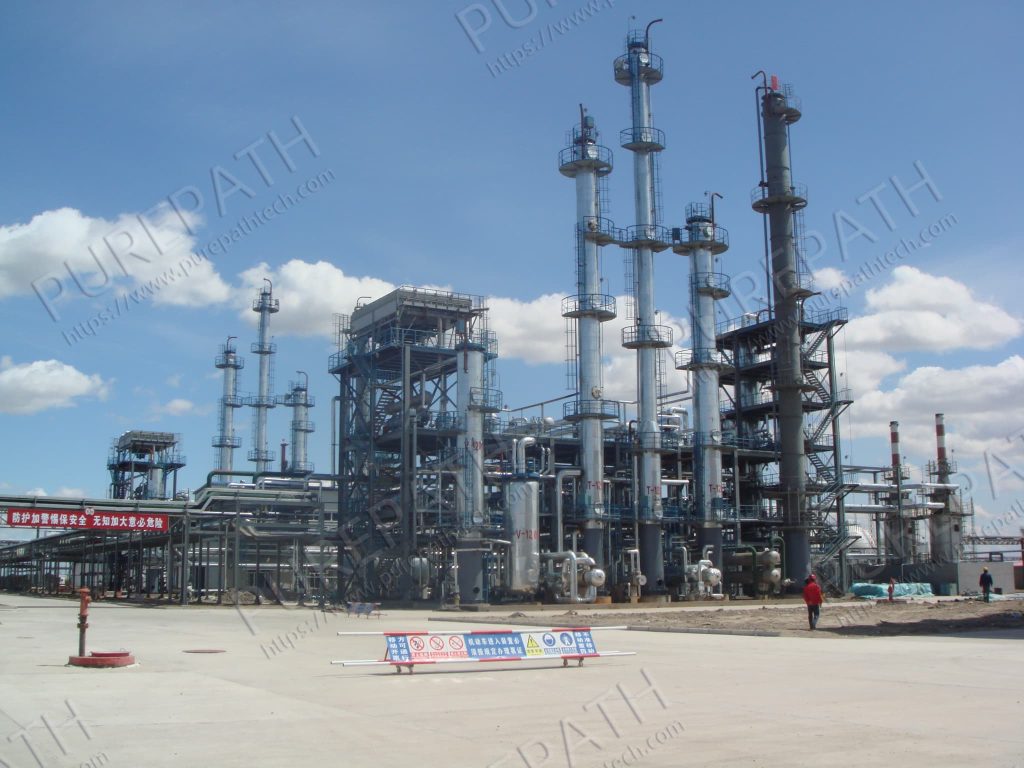
What Is the Purpose of Visbreaking Process in Petroleum Refining?
In petroleum refining, visbreaking (short for viscosity breaking) is a thermal cracking process designed primarily to reduce the viscosity of heavy residual oils. This process enhances the economic value and usability of these heavy fractions. The key purposes and significance of visbreaking in refining include:
1. Reducing the Viscosity of Heavy Residuals
- Heavy residues, such as vacuum residue (VR), are by-products of atmospheric and vacuum distillation processes.
- These residues are highly viscous, making them difficult to store, transport, or directly use.
- By partially cracking long-chain hydrocarbons, visbreaking lowers the viscosity of these heavy fractions, transforming them into marketable products suitable for industrial applications.
2. Producing Market-Ready Heavy Fuel Oil (HFO)
- One of the primary outputs of visbreaking is heavy fuel oil (HFO), which meets market specifications for industrial boilers, power plants, and marine engines.
- Modern visbreaking technologies can also produce low-sulfur heavy fuel oils to comply with increasingly stringent environmental regulations.
3. Enhancing Refinery Profitability
- Visbreaking allows refineries to convert low-value, heavy residues into higher-value products.
- Compared to full-scale cracking processes, visbreaking is more energy-efficient and cost-effective, offering significant economic advantages.
4. Minimizing Coke Formation
- Visbreaking operates under milder thermal cracking conditions compared to coking processes, which significantly reduces coke formation.
- This minimizes fouling in equipment and lowers the cost and complexity of handling coke as a by-product.
5. Increasing Refinery Flexibility
- Visbreaking can process a wide range of feedstocks, including atmospheric residue (AR), vacuum residue, and crude oil sludge.
- Refineries can adjust process parameters to accommodate feedstock variations and changing market demands, optimizing the production of valuable outputs.
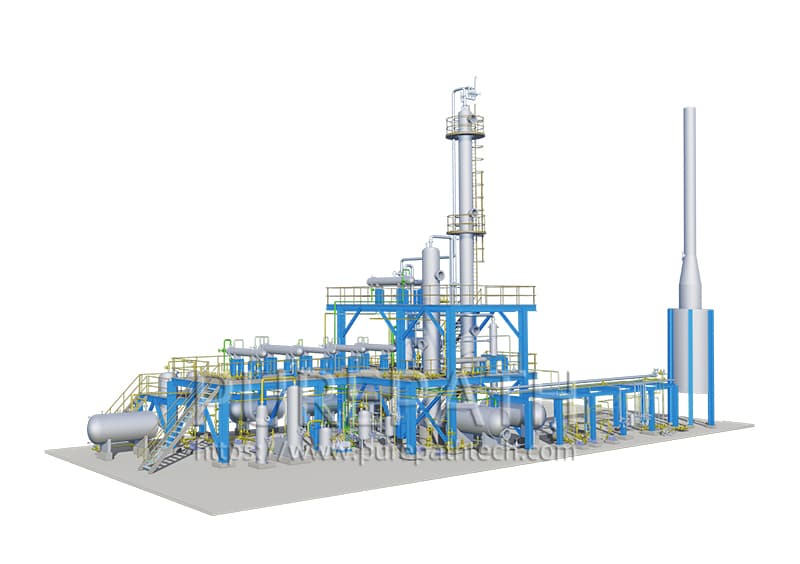
What Are the Feedstocks for the Visbreaking Process in Refinery?
The visbreaking process in a refinery is designed to process heavy residual oils left over from crude oil distillation. These feedstocks are typically viscous, high-boiling-point fractions that require viscosity reduction for easier handling and greater economic value. Below are the primary types of feedstocks used in the visbreaking process:
1. Vacuum Residue (VR)
Vacuum residue is one of the most common feedstocks for the visbreaking process. It is the heaviest fraction obtained from the vacuum distillation unit (VDU), which processes the heavier residues left after crude oil undergoes atmospheric distillation.
Characteristics:
- High viscosity
- High asphaltene and sulfur content
- Low hydrogen-to-carbon ratio
Reason for use:
VR is highly viscous and cannot be directly used in most applications. The visbreaking process lowers its viscosity, enabling its use in heavy fuel oil (HFO) or as a blending component.
2. Atmospheric Residue (AR)
Atmospheric residue is the heavy bottom fraction from the atmospheric distillation unit (ADU) of crude oil. While it is less dense and viscous than vacuum residue, it is still a suitable feedstock for visbreaking.
Characteristics:
- Contains long-chain hydrocarbons
- Relatively lower asphaltene content compared to VR
Reason for use:
AR is processed in visbreaking units either on its own or blended with vacuum residue to achieve the desired viscosity reduction.
3. Blended Residues
Refineries often use a blend of vacuum residue, atmospheric residue, and other heavy streams for visbreaking.
Why blends are used:
- Optimizes the feedstock composition to improve product yield.
- Balances the processing characteristics of different streams.
4. Crude Oil Sludges and Tank Bottoms
Visbreaking units can also process lower-value streams such as crude oil sludges, tank bottoms, and other refinery residues.
Characteristics:
- Typically contains a mix of hydrocarbons and impurities.
Reason for use:
Allows refineries to handle waste streams and recover valuable products from them.
5. Residues from Heavy Crude Oils
Residues obtained from processing heavy crude oils, such as bitumen-based crude or high-asphaltene crude, are ideal for visbreaking.
Challenges with heavy crudes:
- Higher sulfur and metal content.
- Increased coke formation risk during processing.
Why they are suitable:
Visbreaking is an effective way to reduce the viscosity of such residues while minimizing coke production.
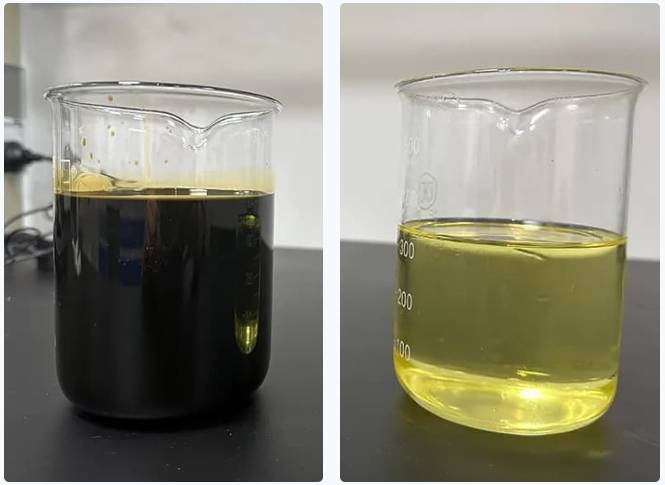
What Are the Products of the Visbreaking Process?
The visbreaking process is designed to reduce the viscosity of heavy residual oils, such as vacuum residues and atmospheric residues, making them more usable and valuable. During the visbreaking process, long-chain hydrocarbons are thermally cracked to produce a range of products, depending on the specific operating conditions and feedstock composition. Below are the main products typically obtained from the visbreaking process:
Product | Description | Characteristics | Applications |
Heavy Fuel Oil (HFO) | Heavy Fuel Oil (HFO) is one of the primary products of the visbreaking process. This is the most significant output, and it is widely used in industrial and marine applications. | Reduced viscosity, high calorific value | Industrial fuel, marine fuel, power generation |
Naphtha | Naphtha is a lighter fraction that results from the partial cracking of heavy hydrocarbons in the visbreaking process. | Light distillate, used in gasoline blending or petrochemical feedstock | Gasoline blending, petrochemical production |
Middle Distillates | Middle distillates produced from visbreaking are heavier than naphtha but lighter than the final residue. These fractions resemble diesel fuel and are valuable as a feedstock for blending high-quality diesel fuel or for industrial use. | Diesel-like fractions | Diesel fuel, industrial fuel |
Light Gases | Fuel gas is another important product from the visbreaking process. It consists of light hydrocarbon gases like methane, ethane, and propane, which are produced during thermal cracking. | Methane, ethane, propane, butane | Refinery fuel, petrochemical feedstock |
Coke | While coke formation is a significant by-product in more severe thermal cracking processes like coking, the visbreaking process generally produces minimal coke. However, a small amount of coke may still form due to the partial cracking of heavy hydrocarbons. | Carbon-rich by-product | Industrial fuel, petroleum coke production |
Residuum | The primary objective of visbreaking is to reduce the viscosity of heavy oils, turning thick, tar-like substances into a more fluid material. This is useful for further processing or transportation. | Heavy, high-viscosity material | Further processing, blending into heavy fuels |
What is the Role of Visbreaking Unit in Heavy Fuel Oil Producing?
Visbreaking is a thermal cracking process used to reduce the viscosity of heavy petroleum products, and it plays a crucial role in the production of heavy fuel oil, such as residual oils or bunker fuel. The main functions of a visbreaking unit in heavy fuel oil production are as follows:
- Viscosity Reduction: A visbreaking unit significantly lowers the viscosity of crude oil or heavy oil, making it easier to flow and more suitable for combustion in industrial boilers, marine engines, and power plants. Highly viscous oils can lead to incomplete combustion, operational difficulties, and safety issues, so reducing viscosity is essential.
- Improvement in Product Quality: The visbreaking process reduces high molecular weight components in the crude oil, breaking them down into lighter molecules. This improves the flow properties and combustion characteristics of the fuel. It positively impacts fuel performance, such as burning efficiency and emissions reduction.
- Cost-Effectiveness: Visbreaking is a relatively low-cost process compared to other heavy oil upgrading methods like hydrocracking. As a result, it offers a cost-efficient way for refineries to process and convert heavy oils, making it an attractive option for large-scale refineries.
- Reduction of Asphaltene Content: Visbreaking helps break down some of the asphaltenic materials in heavy oils, reducing their impact on fuel properties. This contributes to less smoke and fewer pollutants during combustion, enhancing the environmental friendliness of the fuel.
- Production of Heavy Fuel Oils for Industrial and Marine Use: The products generated by a visbreaking unit are typically medium- to heavy-grade fuel oils, commonly used as bunker fuel for ships and industrial boilers. These products meet the demand for high-viscosity, high-energy fuels.
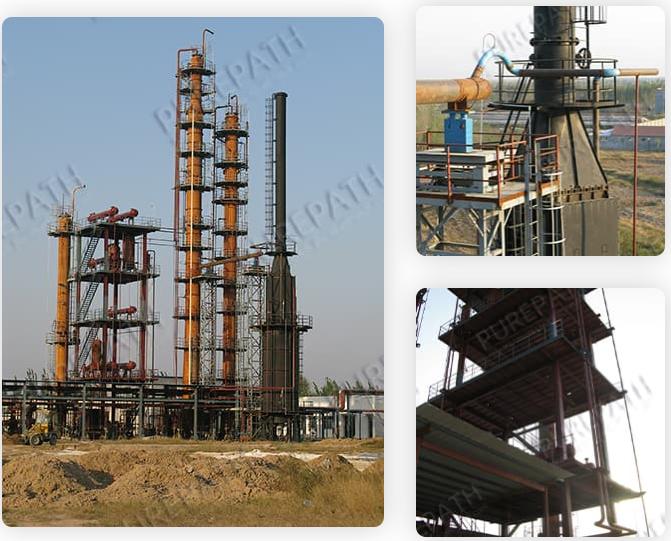
Final Thoughts
Visbreaking is a versatile and economically beneficial process in petroleum refineries, addressing the challenges posed by heavy residues. From producing heavy fuel oil to generating lighter distillates, its contributions are pivotal in maximizing refinery output and adapting to evolving market demands.
Understanding visbreaking’s purpose, feedstocks, and products highlights its importance as a cornerstone of modern refinery operations. As energy industries continue to evolve, visbreaking will remain a critical tool for ensuring efficient and sustainable crude oil processing.