The Role of Hydrotreater in Refinery: A Comprehensive Guide
Hydrotreating is a critical process in the petroleum refining industry, playing a pivotal role in transforming crude oil into high-quality, usable products. At its core, hydrotreating involves the use of hydrogen and catalysts to remove impurities from petroleum fractions, ensuring compliance with environmental standards and improving the performance of refined products.
This article explores the significance of hydrotreating, detailing its process, benefits, and key products. It also discusses different types of hydrotreating units, their roles in refineries, and future trends in hydrotreating technology.
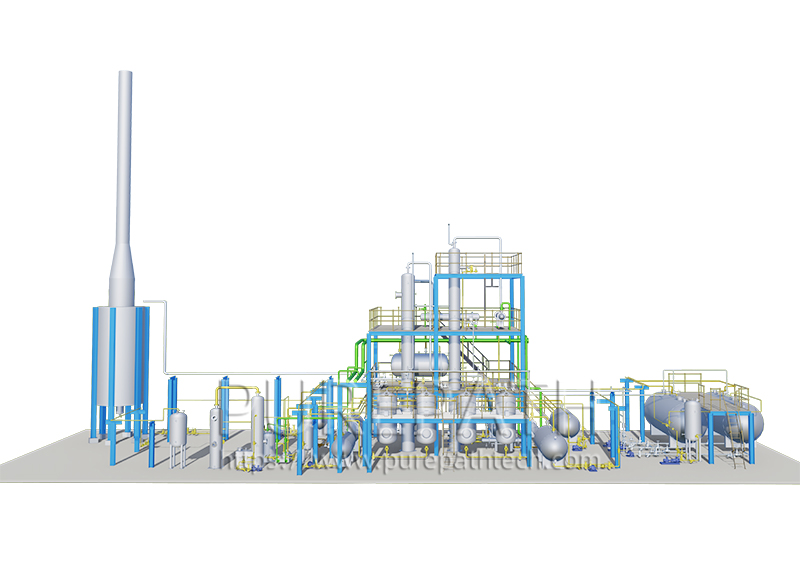
What is Hydrotreating?
Hydrotreating is a catalytic chemical process used in refineries to purify petroleum fractions by removing undesirable elements such as sulfur, nitrogen, oxygen, and metals. The process involves reacting these impurities with hydrogen in the presence of a catalyst, converting them into harmless by-products like hydrogen sulfide (H₂S) and ammonia (NH₃), and improving the quality and usability of the final products.
What is the Hydrotreating Process?
The hydrotreating process typically takes place in a hydrotreating unit, which is a specialized reactor system designed to handle specific feedstocks. The process can be broken down into several key steps:
- Feedstock Preparation:
The feedstock, which could be naphtha, diesel, kerosene, or other petroleum fractions, is first preheated and mixed with hydrogen. This mixture is then fed into the hydrotreating reactor.
- Catalytic Reaction:
Inside the reactor, the feedstock comes into contact with a catalyst, usually composed of metals like cobalt, molybdenum, or nickel supported on alumina. The catalyst facilitates the chemical reactions between hydrogen and the impurities in the feedstock.
- Sulfur compounds are converted into hydrogen sulfide (H₂S).
- Nitrogen compounds are transformed into ammonia (NH₃).
- Oxygen-containing compounds are turned into water (H₂O).
- Metals are trapped within the catalyst or removed as solid residues.
- Separation and Purification:
After the reaction, the mixture exits the reactor and is cooled. The treated feedstock is then separated from the gaseous by-products (e.g., H₂S and NH₃) in a high-pressure separator. The hydrogen sulfide is typically sent to a sulfur recovery unit to produce elemental sulfur, while the ammonia is removed through water washing or other methods.
- Recycling of Hydrogen:
The hydrogen-rich gas from the separator is often recycled back into the process to improve efficiency and reduce costs. Any remaining impurities in the gas are removed before reuse.

Why is Hydrotreating Important?
Hydrotreating is indispensable in modern refineries for several reasons:
1. Removal of Impurities:
The primary function of hydrotreating is to eliminate sulfur, nitrogen, oxygen, and metals from petroleum fractions. Sulfur, in particular, is a major concern due to its contribution to air pollution and acid rain. By removing these impurities, hydrotreating ensures compliance with environmental regulations, such as the production of ultra-low sulfur diesel (ULSD) with less than 15 parts per million (ppm) sulfur content.
2. Improvement of Product Quality:
Hydrotreating enhances the stability, purity, and performance of refined products. For example, treated naphtha is a key feedstock for catalytic reformers, where it is converted into high-octane gasoline. Similarly, hydrotreated diesel exhibits better combustion properties, reducing engine wear and emissions.
3. Environmental Benefits:
By producing cleaner fuels, hydrotreating significantly reduces the emission of harmful pollutants, including sulfur oxides (SOx) and nitrogen oxides (NOx). This aligns with global efforts to combat climate change and improve air quality.
4. Economic Value:
Hydrotreating adds economic value to refined products by making them more marketable. Additionally, it extends the lifespan of refinery equipment by preventing corrosion and fouling caused by impurities.
What are the Products of Hydrotreating?
Hydrotreating yields a range of high-quality products, each with specific applications in the energy and transportation sectors:
1. Treated Naphtha:
Naphtha hydrotreating units produce treated naphtha, which serves as a feedstock for catalytic reformers. In these reformers, naphtha is converted into high-octane gasoline, a critical component of the global fuel supply.
2. Ultra-Low Sulfur Diesel (ULSD):
Hydrotreating is essential for producing ULSD, a clean-burning diesel fuel with sulfur content below 15 ppm. ULSD is widely used in transportation and industrial applications, offering significant environmental benefits over traditional diesel.
3. Jet Fuel:
Hydrotreated kerosene is a key component of jet fuel, ensuring its stability and compliance with aviation standards. The process removes impurities that could compromise the performance of aircraft engines.
4. Other Products:
Hydrotreating also produces treated liquefied petroleum gas (LPG) and hydrogen-rich off-gas. The latter can be recycled within the refinery to support other processes, such as hydrocracking.
5. By-products:
The process generates by-products like elemental sulfur and ammonia, which can be further processed and sold for industrial use. For example, sulfur is a key raw material for sulfuric acid production.
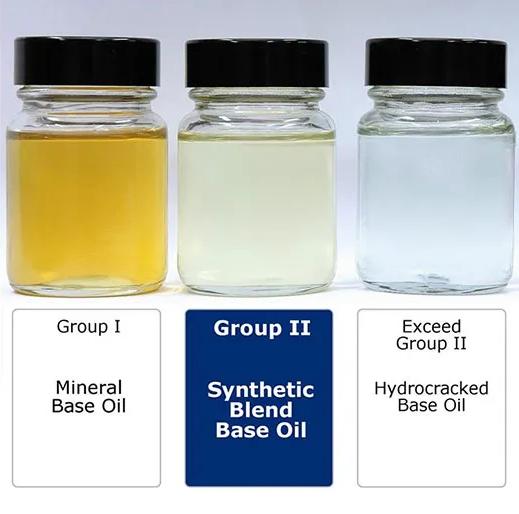
Types of Hydrotreating Units in Refineries
Refineries utilize a variety of hydrotreating units, each specifically designed to handle different feedstocks and achieve distinct refining objectives. These units are integral to the refining process, ensuring that petroleum fractions are purified and upgraded to meet quality standards and environmental regulations. Below, we explore the key types of hydrotreating units and their roles in refinery operations.
1. Naphtha Hydrotreating Unit
The naphtha hydrotreating unit is a specialized system designed to treat naphtha, a light petroleum fraction derived from crude oil distillation. Naphtha is a critical feedstock for producing gasoline and other high-value petrochemicals. The primary purpose of this unit is to remove impurities such as sulfur, nitrogen, and olefins, which can negatively impact downstream processes and product quality.
Key Functions:
- Removes sulfur compounds to prevent catalyst poisoning in catalytic reformers.
- Eliminates nitrogen and oxygen compounds that could degrade product stability.
- Saturates olefins (unsaturated hydrocarbons) to improve feedstock quality.
Applications:
- Treated naphtha is sent to catalytic reformers, where it is converted into high-octane gasoline components.
- It can also be used as a feedstock for steam crackers in petrochemical production.
Importance:
The naphtha hydrotreating unit ensures that the feedstock meets the stringent purity requirements of downstream processes, enabling the production of cleaner and higher-performance gasoline.
2. Diesel Hydrotreater
The diesel hydrotreater is a critical unit in modern refineries, primarily focused on processing diesel feedstocks to produce ultra-low sulfur diesel (ULSD). Diesel hydrotreating is essential for meeting environmental regulations, which mandate extremely low sulfur levels in transportation fuels (typically below 15 parts per million, or ppm).
Key Functions:
- Removes sulfur compounds, including refractory sulfur species that are difficult to eliminate.
- Reduces nitrogen and aromatic content, improving the combustion properties of diesel.
- Enhances the stability and storage life of diesel fuel.
Applications:
- Produces ULSD for use in transportation, including trucks, buses, and trains.
- Supplies cleaner diesel for industrial and agricultural machinery.
Importance:
Diesel hydrotreaters play a vital role in reducing air pollution by minimizing sulfur oxide (SOx) emissions, which are harmful to human health and the environment. They also ensure compliance with global fuel standards, such as Euro 6 and Tier 3 regulations.
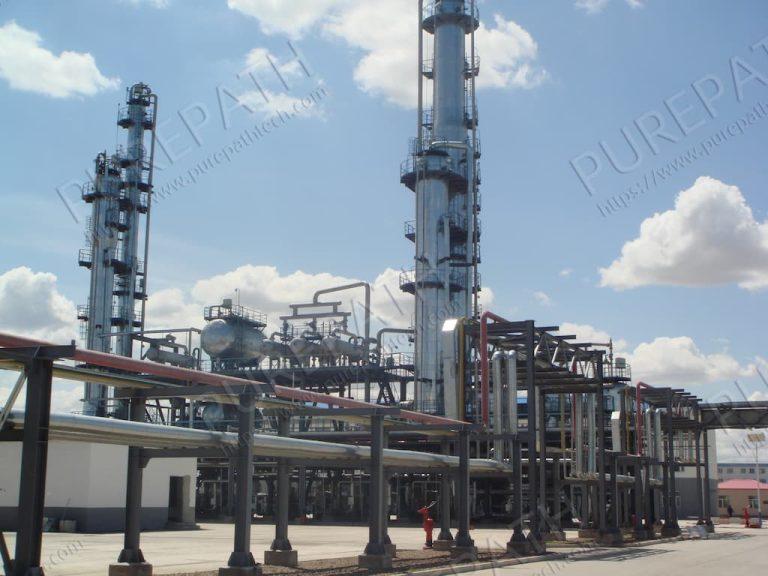
3. Full-Range Hydrotreater
The full-range hydrotreater is a versatile unit capable of processing a wide variety of feedstocks, including naphtha, kerosene, and diesel. This flexibility makes it an invaluable asset in refineries with diverse product slates or those processing different types of crude oil.
Key Functions:
- Treats multiple feedstocks simultaneously or sequentially, depending on refinery needs.
- Removes sulfur, nitrogen, oxygen, and metals from various petroleum fractions.
- Produces high-quality intermediate products for further processing or final use.
Applications:
- Treats naphtha for catalytic reforming or petrochemical production.
- Processes kerosene to produce jet fuel with improved combustion characteristics.
- Upgrades diesel feedstocks to meet ULSD specifications.
Importance:
Full-range hydrotreaters offer operational flexibility, allowing refineries to adapt to changing market demands and feedstock availability. They also streamline operations by consolidating multiple treatment processes into a single unit, reducing capital and operational costs.
4. Kerosene Hydrotreater
While not always a standalone unit, kerosene hydrotreating is often performed in dedicated sections of full-range hydrotreaters or specialized units. The primary goal is to produce high-quality jet fuel and kerosene for lighting and heating.
Key Functions:
- Removes sulfur and nitrogen compounds to meet aviation fuel specifications.
- Reduces aromatic content to improve combustion efficiency and reduce emissions.
- Enhances the thermal stability of jet fuel, which is critical for high-temperature operations in aircraft engines.
Applications:
- Produces jet fuel for commercial and military aviation.
- Supplies kerosene for household and industrial use.
Importance:
Kerosene hydrotreating ensures the safety and performance of aviation fuels, which must meet rigorous international standards. It also supports the production of cleaner-burning kerosene for other applications.
5. Vacuum Gas Oil (VGO) Hydrotreater
The VGO hydrotreater processes heavier feedstocks, such as vacuum gas oil, which is derived from the vacuum distillation of crude oil. This unit is often integrated with hydrocracking units to produce lighter, more valuable products.
Key Functions:
- Removes sulfur, nitrogen, and metals from heavy feedstocks.
- Prepares VGO for further processing in hydrocrackers or fluid catalytic crackers (FCCs).
- Converts heavy hydrocarbons into lighter, more useful products.
Applications:
- Produces feedstocks for diesel, jet fuel, and gasoline production.
- Supplies raw materials for lubricant base oils and other specialty products.
Importance:
VGO hydrotreaters maximize the value of heavy feedstocks by converting them into high-demand products. They also play a crucial role in integrated refining processes, enhancing overall refinery efficiency.
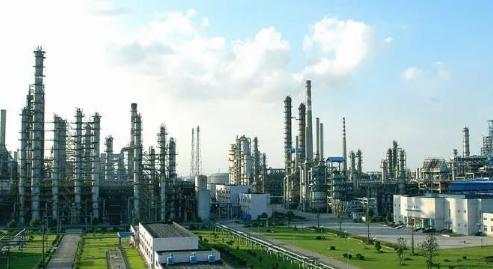
6. Residue Hydrotreater
The residue hydrotreater is designed to process the heaviest and most challenging feedstocks, such as atmospheric residue or vacuum residue. These units are essential for upgrading bottom-of-the-barrel materials into usable products.
Key Functions:
- Removes sulfur, nitrogen, and metals from residual feedstocks.
- Converts heavy hydrocarbons into lighter fractions, such as diesel and naphtha.
- Reduces the production of low-value by-products like coke and heavy fuel oil.
Applications:
- Produces lighter products for further refining or direct use.
- Supplies feedstocks for advanced conversion processes, such as delayed coking or visbreaking.
Importance:
Residue hydrotreaters enable refineries to process heavier and lower-quality crude oils, improving profitability and resource utilization. They also support the production of cleaner fuels from challenging feedstocks.
Challenges and Future Trends in Hydrotreating
Despite its many benefits, hydrotreating faces several challenges:
- High Operating Costs: The process consumes significant amounts of hydrogen, which can be expensive to produce or purchase. Additionally, catalysts require periodic regeneration or replacement, adding to operational expenses.
- Catalyst Deactivation: Over time, catalysts lose their effectiveness due to fouling or poisoning by impurities. Managing catalyst life is a key challenge for refinery operators.
The hydrotreating industry is evolving to address these challenges and adapt to changing market demands. Key trends include:
- Development of more efficient and durable catalysts.
- Integration with renewable fuel production, such as hydrotreated vegetable oil (HVO).
- Adoption of advanced process control technologies to optimize performance and reduce costs.
Wrap Up
Hydrotreating is a cornerstone of modern refining, enabling the production of high-quality, environmentally friendly fuels. By removing impurities and enhancing product performance, hydrotreating units, including naphtha hydrotreating units and diesel hydrotreaters, play a vital role in meeting both regulatory requirements and consumer expectations. As the industry evolves, innovations in catalysts, renewable fuel integration, and process optimization will ensure that hydrotreating remains a key driver of sustainability and efficiency in the refining sector. Through its economic and environmental benefits, hydrotreating continues to underscore its importance in the global energy landscape.