Types and Techniques of Lube Oil Blending Plants
Lubricant oil blending plants play a pivotal role in the production of various types of lubricants, essential for reducing friction and wear in mechanical systems. These plants are specialized facilities where base oils are mixed with additives to produce high-quality lubricants. The efficiency and effectiveness of the lube oil blending process directly impact the quality of the final product, making the choice of blending equipment and methods crucial. This article explores the different types of lube oil blending equipment, their advantages and disadvantages, and the measures to ensure product quality.
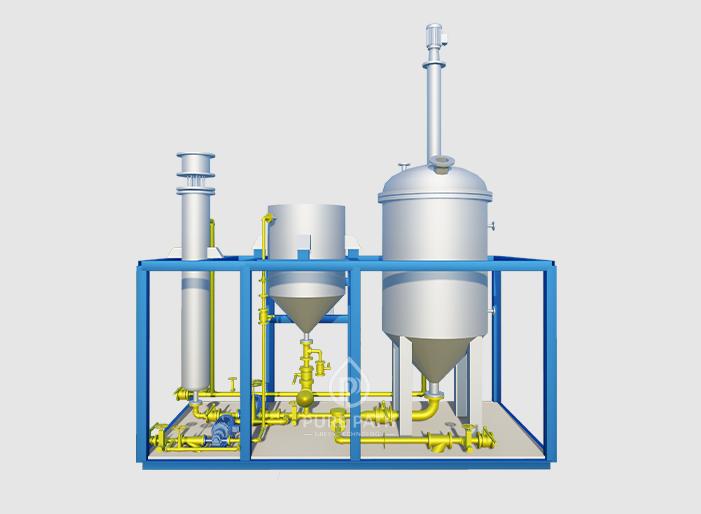
Types of Lubricant Oil Blending Equipment
According to different production needs and technical characteristics, lubricating oil blending plants can be divided into the following types:
1. Tank Blending Systems
Tank blending systems are the traditional and most commonly used method in lubricant oil blending plants. These systems involve one or more blending tanks where base oils and additives are directly fed in predetermined proportions. The mixture is then stirred to form the finished lubricant. A typical tank blending system comprises several components:
- Blending Tanks: Where the actual mixing of base oils and additives occurs.
- Mixing Devices: Such as agitators or stirrers to ensure thorough mixing.
- Heating Systems: To maintain optimal temperatures for blending.
- Additive Injection Systems: For precise dosing of additives.
- Metering Equipment: To ensure accurate measurement of base oils and additives.
- Pumps and Piping: For transporting the mixture through the system.
Advantages of Tank Blending Systems:
- Simplicity: Easy to operate and maintain.
- Cost-Effective: Lower initial investment compared to more advanced systems.
- Flexibility: Can be adapted for small or large batch production.
Disadvantages of Tank Blending Systems:
- Lower Efficiency: Batch processing can be time-consuming.
- Inconsistent Quality: Potential for human error in measuring and mixing.
- Energy-Intensive: Requires significant energy to maintain optimal blending conditions.
2. Inline Blending Systems
Inline blending systems represent a more advanced and continuous approach to the lube oil blending process. These systems use automated control instruments to manage the flow rates of various components, ensuring they mix in precise proportions as they pass through an inline mixer. Key components of inline blending systems include:
- Base Oil and Additive Pumps: For controlled delivery of components.
- Flow Meters: To monitor and adjust the flow rates of each component.
- Inline Mixers: Where the components are continuously blended.
- Control Systems: For real-time monitoring and adjustment.
Advantages of Inline Blending Systems:
- High Efficiency: Continuous blending reduces processing time.
- Precise Control: Automated systems ensure accurate blending ratios.
- Consistency: Produces uniform product quality.
- Energy Efficient: Lower energy consumption compared to batch processing.
Disadvantages of Inline Blending Systems:
- Complexity: More sophisticated and harder to maintain.
- High Initial Cost: Significant investment in advanced equipment and technology.
- Repair and Maintenance: Requires specialized knowledge for troubleshooting and repairs.
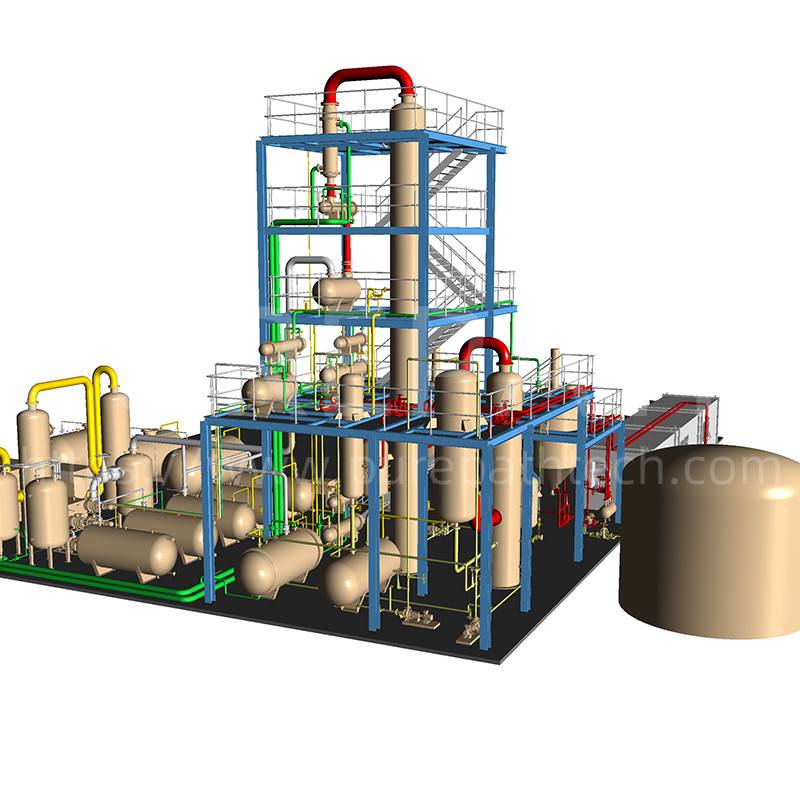
3. Automated Continuous Blending Systems
Automated continuous blending systems are designed for large-scale production with minimal human intervention. These systems integrate advanced electronic technologies, sensors, and control algorithms to automate the entire lube oil blending process from raw material input to final product output. Components of automated continuous blending systems include:
- Base Oil and Additive Storage Tanks: For large volumes of raw materials.
- Precision Dosing Pumps: For exact measurement of additives.
- Automated Mixers: Ensuring thorough and continuous blending.
- Advanced Control Systems: Utilizing real-time data to adjust blending parameters.
- Quality Monitoring Systems: To ensure the final product meets specified standards.
Advantages of Automated Continuous Blending Systems:
- High Production Capacity: Suitable for large-scale operations.
- Consistency and Quality: Maintains high product standards.
- Labor Efficiency: Reduces the need for manual labor.
- Data Integration: Facilitates comprehensive production monitoring and quality control.
Disadvantages of Automated Continuous Blending Systems:
- High Complexity: Requires sophisticated technology and expertise.
- Significant Initial Investment: High cost of setup and equipment.
- Maintenance: Ongoing need for technical support and maintenance.
4. Pulsed Air Mixing Systems
Pulsed air mixing systems use air pulses to create vigorous mixing within the blending tank. This method generates large air bubbles that help achieve rapid and uniform mixing of the lubricant components.
Advantages of Pulsed Air Mixing Systems:
- Efficient Mixing: Achieves quick and thorough blending.
- Energy Saving: Uses air pulses instead of mechanical agitation.
- Reduced Shear Stress: Gentle mixing preserves additive integrity.
Disadvantages of Pulsed Air Mixing Systems:
- Control Complexity: Requires precise control of air pulses.
- Initial Setup Cost: Investment in specialized equipment.
- Operational Challenges: Managing air pulse parameters for optimal performance.
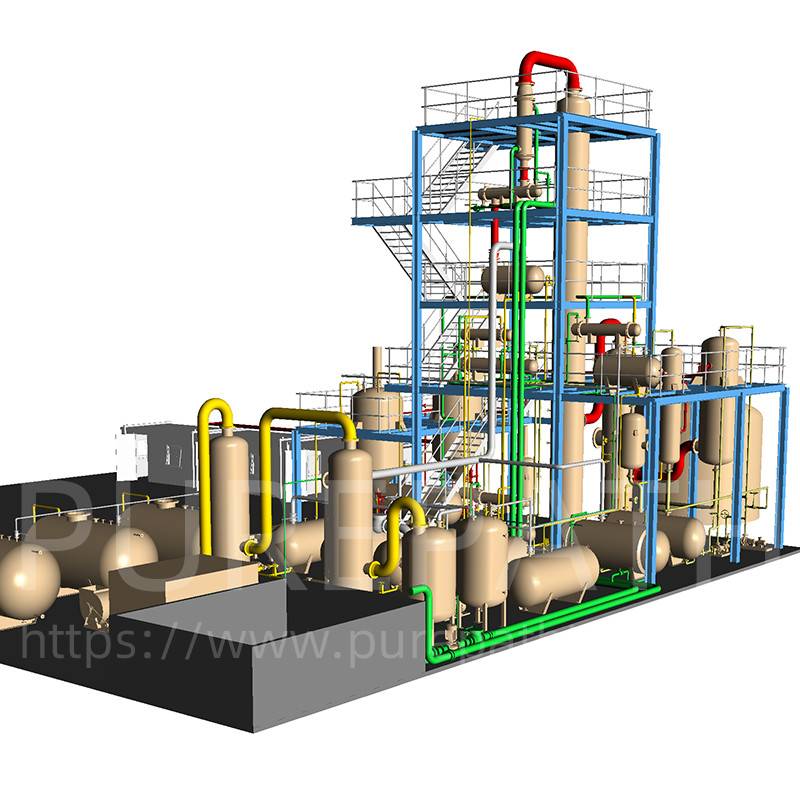
How Lube Oil Blending Plants Ensure the Product Quality
The quality of lubricants produced in a lube oil blending plant is paramount. Ensuring high product quality involves several critical measures:
1. Accurate Measurement and Dosing
Precise measurement and dosing of base oils and additives are fundamental to producing high-quality lubricants. Modern lube oil blending plants utilize advanced metering systems and automated dosing pumps to minimize human error and ensure exact proportions.
2. Advanced Blending Technologies
The adoption of advanced blending technologies, such as inline blending and automated continuous blending, enhances the consistency and quality of the final product. These technologies provide better control over the blending process, resulting in uniform products.
3. Real-Time Monitoring and Control
Digital management systems that offer real-time monitoring and control are essential for maintaining product quality. These systems track key parameters throughout the blending process, such as temperature, flow rates, and mixture homogeneity, allowing for immediate adjustments to maintain optimal conditions.
4. Quality Control Measures
Implementing stringent quality control measures at various stages of the production process ensures that the final product meets the desired standards. This includes:
- Raw Material Testing: Ensuring the quality of base oils and additives before blending.
- Process Monitoring: Continuous surveillance of the blending process to detect and correct deviations.
- Final Product Testing: Conducting comprehensive tests on the finished lubricant to confirm it meets all specifications.
5. Regular Maintenance and Calibration
Regular maintenance and calibration of blending equipment are crucial to sustain their accuracy and reliability. Scheduled maintenance prevents equipment malfunctions and ensures consistent performance, while calibration maintains the precision of measurement systems.
6. Operator Training
Proper training for operators is vital to the successful operation of a lubricant oil blending plant. Well-trained personnel understand the blending process, equipment operation, and troubleshooting, contributing to efficient production and high product quality.
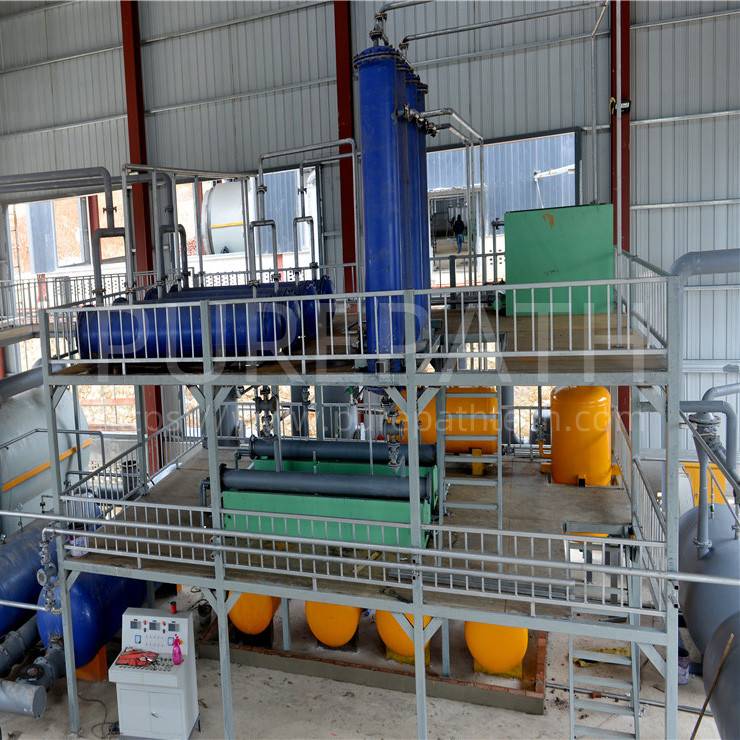
Conclusion
The selection and implementation of appropriate blending equipment and methods are critical to the success of a lubricant oil blending plant. Each type of equipment—whether tank blending, inline blending, automated continuous blending, or pulsed air mixing—has its unique advantages and challenges. Ensuring product quality in the lube oil blending process requires precise measurement, advanced technologies, real-time monitoring, strict quality control measures, regular maintenance, and skilled operators. By focusing on these aspects, lubricant oil blending plants can produce high-quality lubricants that meet market demands and maintain their competitive edge.