Used Lubricant Oil Recycling Plant vs. Lubricant Oil Blending Plant: Sustainable Lubricant Solutions
In the modern world, lubricating oils play a crucial role in the smooth operation of machinery and equipment across diverse industries. However, the widespread use of these lubricants generates a significant amount of used oil, posing environmental challenges if not properly managed. Used lubricant oil, if not recycled responsibly, can contaminate soil and water sources, posing a threat to ecosystems and human health. To address this environmental concern, lubricant oil recycling and blending plants have emerged as essential pillars of sustainable lubricant production.
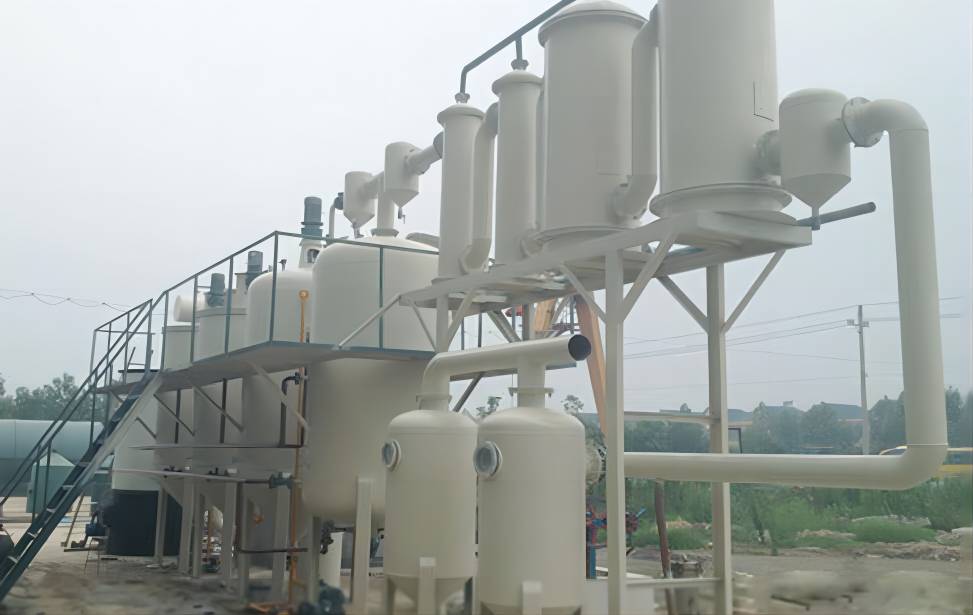
The Significance of Lubricant Oil Recycling and Blending
Lubricant oil recycling and blending offer a multitude of environmental and economic benefits. By diverting used lubricant oil from landfills and incineration, recycling reduces the risk of soil and water contamination. Additionally, it conserves virgin crude oil resources, contributing to energy security and reducing the environmental footprint of lubricant production.
Lubricant oil blending, in turn, plays a crucial role in meeting the diverse lubrication needs of various industries and applications. By blending base oils with specific additives, lubricating oils are tailored to provide optimal performance and protection for different types of machinery and equipment.
Key Differences between Used Lubricant Oil Recycling Plants and Lubricant Oil Blending Plants
While both types of facilities contribute to the sustainable production of lubricants, they serve distinct purposes and employ different processes.
Used Lubricant Oil Recycling Plants
Purpose: Used lubricant oil recycling plants primarily focus on collecting, processing, and re-refining used lubricating oil to produce base oil, which is a crucial component in lubricant manufacturing. By extracting valuable base oil from used oil, recycling plants not only reduce the environmental impact of waste oil disposal but also conserve the resources required to produce new base oil from crude oil.
Process
- Collection: The first step involves gathering used oil from various sources, including automotive workshops, industrial facilities, and oil collection centers. This collection network ensures a steady supply of used oil for the recycling process.
- Pre-treatment: Once collected, the used oil undergoes a pre-treatment stage to remove impurities and contaminants that can hinder the re-refining process. This pre-treatment typically involves filtration, centrifugation, and water removal to clean the used oil effectively.
- Re-refining: The heart of the recycling process lies in re-refining, where various techniques are employed to restore the properties of the used oil and produce base oil. These techniques include distillation, solvent extraction, and hydrotreating, which remove impurities, improve viscosity, and enhance the lubricating properties of the base oil.
Products
- Base oil: The primary product of used lubricant oil recycling plants is base oil, which serves as a key ingredient in lubricant blending. This base oil is carefully refined and purified to meet industry specifications.
- Other recovered materials: Apart from base oil, the recycling process may also yield other valuable materials, such as asphalt and fuel oil. These recovered materials can be further processed and utilized in various applications.
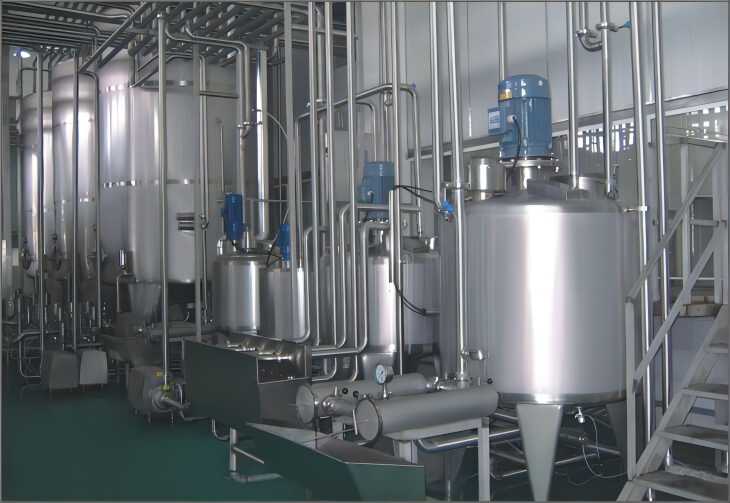
Lubricant Oil Blending Plants
Purpose: Lubricant oil blending plants specialize in blending base oil with carefully selected additives to produce a wide range of finished lubricants tailored for specific applications. The blending process ensures that the resulting lubricants meet the performance and viscosity requirements of various industrial and automotive applications.
Process
- Blending: The blending process involves meticulously mixing base oil with a precise blend of additives. Each additive serves a specific purpose, such as enhancing viscosity, improving oxidation resistance, or providing anti-wear protection. The blending ratios are carefully controlled to achieve the desired performance characteristics for each lubricant grade.
- Quality Control: To ensure the quality and consistency of the blended lubricants, rigorous quality control measures are implemented throughout the blending process. This includes testing the viscosity, flash point, oxidation stability, and wear protection properties of the blended lubricants to ensure they meet industry standards and customer specifications.
Products
- Finished lubricants: The final products of lubricant oil blending plants are finished lubricants, such as engine oil, transmission fluid, hydraulic oil, and industrial lubricants. These lubricants are designed to meet the specific performance requirements of various applications, ensuring optimal performance and protection for machinery and equipment.
In essence, used lubricant oil recycling plants focus on extracting valuable base oil from used oil, while lubricant oil blending plants transform base oil into a variety of finished lubricants with tailored performance characteristics. Both types of plants play a crucial role in the sustainable production and utilization of lubricants, promoting environmental protection and resource conservation.
Comparison of Used Lubricant Oil Recycling Plants and Lubricant Oil Blending Plants
Used lubricant oil recycling plants and lubricant oil blending plants play distinct yet complementary roles in the sustainable production of lubricants. The table below summarizes the key differences between the two types of plants:
Feature | Used Lubricant Oil Recycling Plants | Lubricant Oil Blending Plants |
Primary Function | Re-refining used lubricating oil into base oil | Blending base oil with additives to produce finished lubricants |
Input Materials | Used lubricating oil | Base oil and additives |
Output Products | Base oil, recovered materials (asphalt, fuel oil) | Finished lubricants (engine oil, transmission fluid, hydraulic oil) |
Environmental Impact | Reduces environmental contamination from improper disposal of used lubricant oil | Conserves virgin crude oil resources |
Economic Benefits | Diverts used lubricant oil from waste streams into valuable resources | Produces a variety of lubricants for various applications |
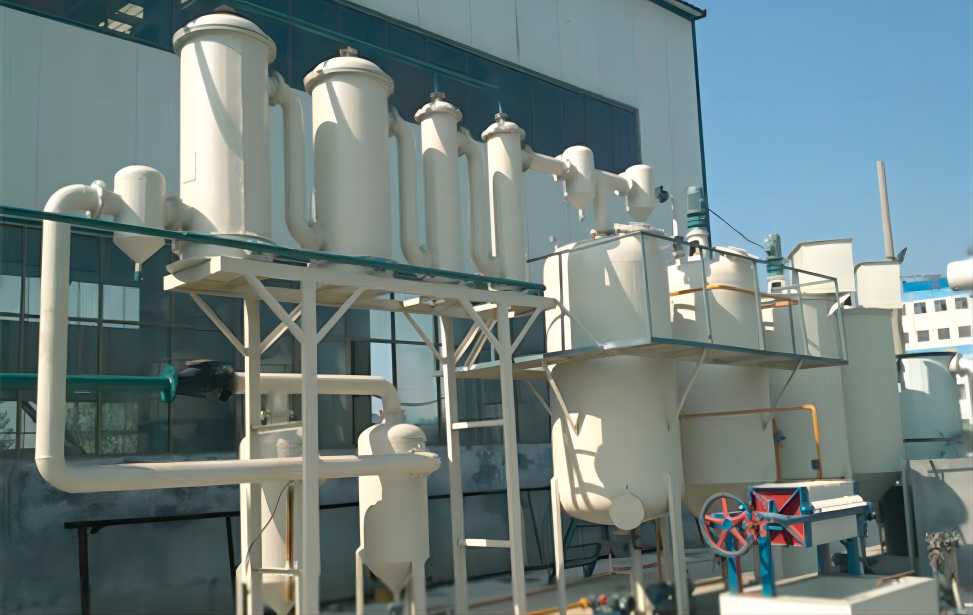
Conclusion
Lubricant oil recycling and blending are essential practices for sustainable lubricant production. By diverting used lubricant oil from waste streams into valuable resources and producing a variety of lubricants for diverse applications, these processes minimize environmental impact and promote resource conservation. As the lubricant industry continues to evolve, lubricant oil recycling and blending will play an increasingly crucial role in ensuring a sustainable and environmentally responsible future for lubrication.