Visbreaking in Petroleum Refining: Purpose, Process, Operation, and Environmental Impact
Visbreaking, a crucial process in petroleum refining, plays a significant role in upgrading heavy fuel oil (HFO) by reducing its viscosity and increasing the yield of lighter, more valuable products. This is achieved through moderate thermal cracking, which breaks down large hydrocarbon molecules into smaller ones, making the HFO more fluid and easier to process. This article provides an in-depth analysis of visbreaking, covering its objectives, comparison with other refining processes, established technologies, operational control, and environmental aspects.
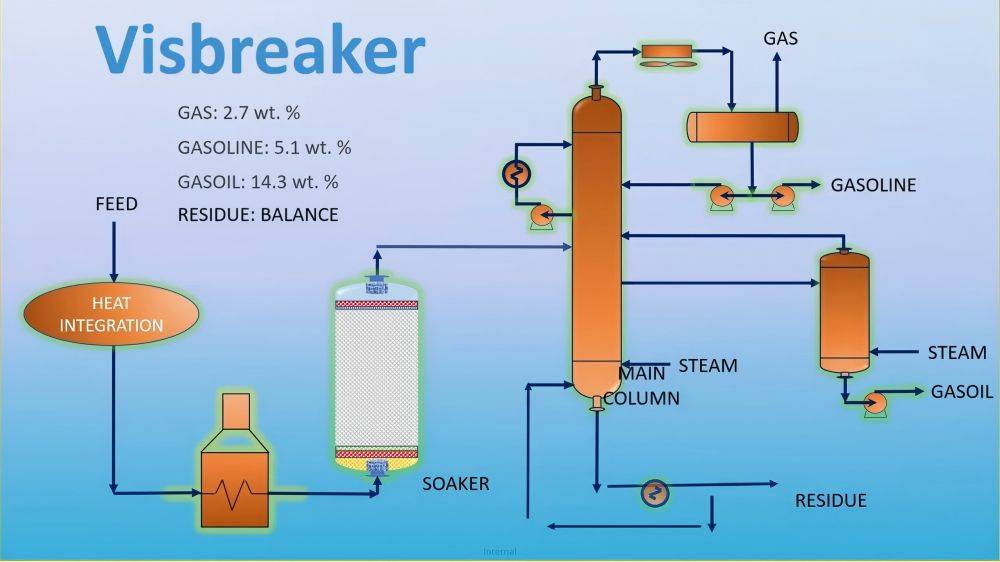
Objectives of Visbreaking and Comparison with Other Refining Processes
The primary objective of visbreaking is to reduce the viscosity of heavy fuel oils such as vacuum residue and bitumen, making them easier to handle and process. These heavy oils are characterized by high viscosity, high density, and high sulfur content, making them difficult to utilize directly. By breaking down the large hydrocarbon molecules into smaller ones, visbreaking achieves the “viscosity reduction” effect, enhancing the utilization value of heavy oil.
Specifically, the objectives of visbreaking include:
- Viscosity Reduction: This is the most important objective. Reducing the viscosity of heavy oil makes it easier to transport, store, and further process.
- Increased Light Oil Yield: Visbreaking generates some lighter oil products, such as gasoline and diesel, thereby increasing the refinery’s overall light oil yield.
- Improved Product Properties: The residual oil from visbreaking can be used as feedstock for fuel oil or asphalt, with improved properties such as reduced sulfur content and increased stability.
Compared to other refining processes, visbreaking has its unique characteristics:
- Catalytic Cracking: Catalytic cracking uses catalysts to facilitate the reaction at lower temperatures, producing light oil products like gasoline and diesel. Visbreaking relies on high-temperature thermal cracking, with relatively harsh reaction conditions. Catalytic cracking focuses more on generating high-value-added light oil products, while visbreaking emphasizes viscosity reduction and enhancing the utilization value of heavy oil.
- Delayed Coking: Delayed coking is mainly used to process heavy feedstocks like vacuum residue, producing coke and a small amount of light oil. Visbreaking focuses on reducing viscosity and increasing the utilization value of heavy oil and does not aim to produce coke. Delayed coking is a deep cracking process that produces coke as a fuel or industrial raw material, while visbreaking is a mild cracking process mainly aimed at reducing viscosity.
- Hydrocracking: Hydrocracking uses catalysts in the presence of hydrogen to crack heavy oil into lighter products. Hydrocracking has milder reaction conditions but requires high-pressure hydrogen and expensive catalysts. Visbreaking does not require hydrogen and has relatively simple reaction conditions.
Are There Any Established Visbreaking Technologies?
Currently, the most widely used visbreaking technologies in the industry include:
- Furnace Visbreaking: This is the most traditional visbreaking process. The feedstock oil undergoes thermal cracking in a furnace, producing lighter oil and reduced-viscosity residual oil. Furnace visbreaking is simple, but the furnace efficiency is low and energy consumption is high.
- Soaker Visbreaking: The reaction takes place in a soaker drum with a longer residence time, suitable for processing high-viscosity feedstocks. Soaker visbreaking is simple to operate, but the reaction rate is slow and production efficiency is low.
- Coil Visbreaking: This process uses rapid heating and rapid cooling to control the degree of reaction and reduce the occurrence of side reactions. Coil visbreaking can increase the yield of light oil, but it has high equipment requirements.
In addition, some new visbreaking technologies are being researched and developed, such as fluidized bed visbreaking and catalytic visbreaking. These new technologies aim to improve reaction efficiency, reduce energy consumption, and reduce pollutant emissions and are the future direction of visbreaking technology development.
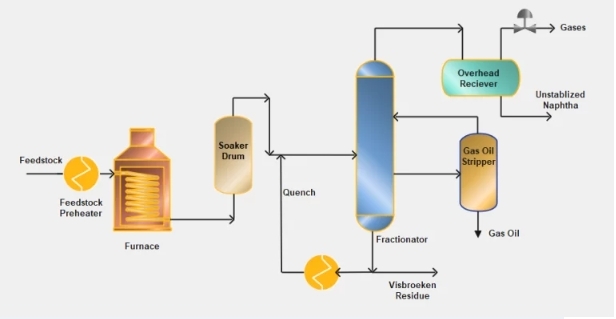
How to Control the Parameters of Visbreaking Unit During Operation?
The operation control of the visbreaking unit is crucial, mainly including:
- Reaction Temperature: Reaction temperature is a key factor affecting the degree of cracking. Too high or too low will affect product quality and yield. The reaction temperature needs to be precisely controlled according to the nature of the feedstock and process requirements to achieve the best viscosity reduction effect.
- Reaction Pressure: Reaction pressure has a certain impact on the cracking reaction. Generally, lower pressure is used. Reducing the reaction pressure can reduce the occurrence of side reactions and increase the yield of light oil.
- Residence Time: Residence time determines the degree of reaction and needs to be adjusted according to the nature of the feedstock and process requirements. Too long a residence time will lead to over-cracking and generate too much gas and coke; too short a residence time will lead to poor viscosity reduction effect.
- Feedstock Flow Rate: The feedstock flow rate needs to be matched with the reaction temperature, pressure, and residence time to ensure the stable operation of the unit and product quality.
- Recycle Ratio: The recycle ratio refers to the ratio of recycled oil to fresh feedstock. Adjusting the recycle ratio can control the reaction depth and product properties.
In addition to the above parameters, it is also necessary to control the combustion efficiency of the furnace, the fluid flow state of the reactor, etc., to ensure the stable operation of the unit and product quality.
Pollutants and Treatment in Visbreaking Process
The visbreaking process will generate certain pollutants, mainly including:
- Waste Gas: Mainly contains hydrocarbon gases, sulfides, nitrogen oxides, etc., which need to be purified. Hydrocarbon gases can be burned or recovered; sulfides can be removed by desulfurization devices; nitrogen oxides can be treated by selective catalytic reduction (SCR) or selective non-catalytic reduction (SNCR) and other technologies.
- Waste Water: Mainly contains pollutants such as oil and phenols, which need to be degreased and biologically treated. Oil can be removed by oil separators or air flotation devices; phenols can be treated by biodegradation or adsorption.
- Solid Waste: Mainly includes coke, residue, etc., which need to be utilized or safely disposed of. Coke can be used as fuel or for the production of electrode materials; residue can be incinerated or landfilled.
Corresponding treatment measures need to be taken for different pollutants, such as waste gas purification, waste water treatment, and comprehensive utilization of solid waste to meet environmental protection requirements.
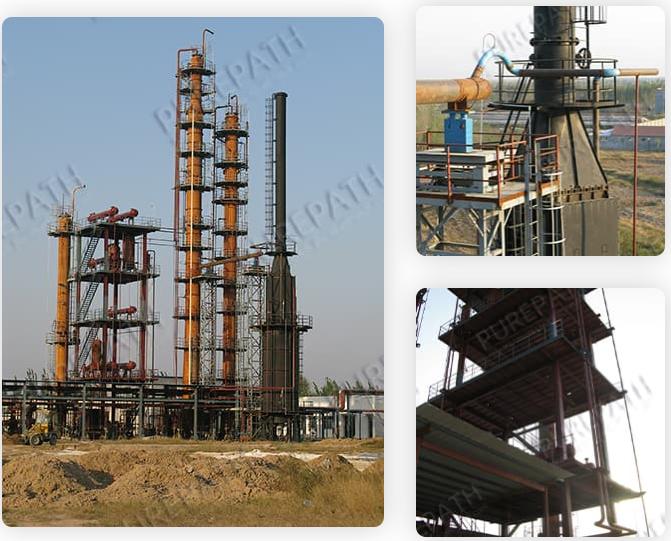
Wrap Up
Visbreaking, as an important means of processing heavy fuel oil, plays a significant role in increasing the yield of light oil and improving product performance. By continuously optimizing process technology, strengthening operation control and environmental management, visbreaking will play a more important role in the future refining industry. With the increasing stringent environmental protection requirements and the transformation of the energy structure, visbreaking technology will develop in the direction of high efficiency, energy saving, and environmental protection, and contribute to the sustainable development of the refining industry.