Visbreaking vs.Coking: A Comparative Analysis for Heavy Oil Upgrading
Fundamentals of Heavy Oil Upgrading
Heavy oil, often characterized by its high viscosity and dense composition, poses significant challenges for refineries due to its difficulty in processing. Heavy crude oil has a higher sulfur content and a greater concentration of impurities compared to lighter crudes, requiring specialized treatment to meet refining standards. One of the main objectives in heavy oil upgrading is to reduce the viscosity, making it more flowable and easier to refine into valuable products like gasoline, diesel, and jet fuel.
Thermal cracking processes, including coking and visbreaking, are commonly employed to break down these larger, more complex hydrocarbons into lighter fractions. These processes enhance product yield and quality while improving the overall efficiency of refinery operations. Both coking and visbreaking serve as crucial steps in the upgrading of heavy oil, each offering distinct methods and advantages.
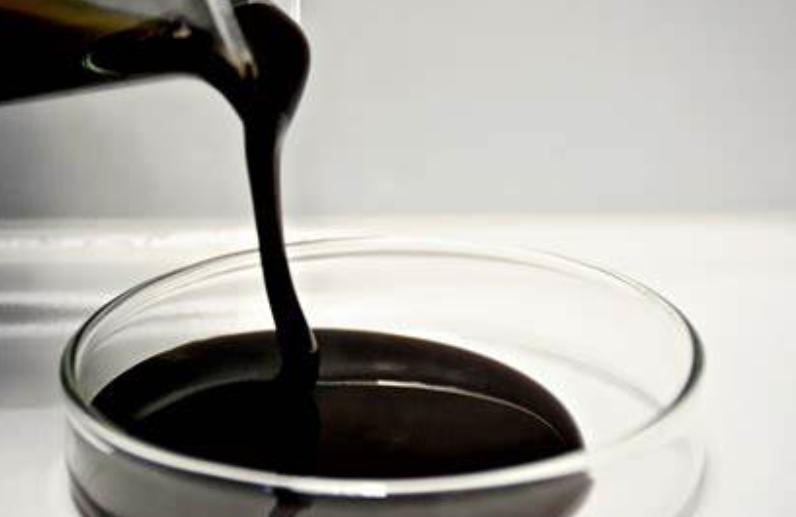
What is Visbreaking and Coking?
Visbreaking and coking are both thermal cracking processes used in refineries to upgrade heavy crude oil by breaking down large hydrocarbon molecules into lighter, more valuable products. While both involve high temperatures to induce molecular cracking, they differ in severity, objectives, and end products.
Visbreaking
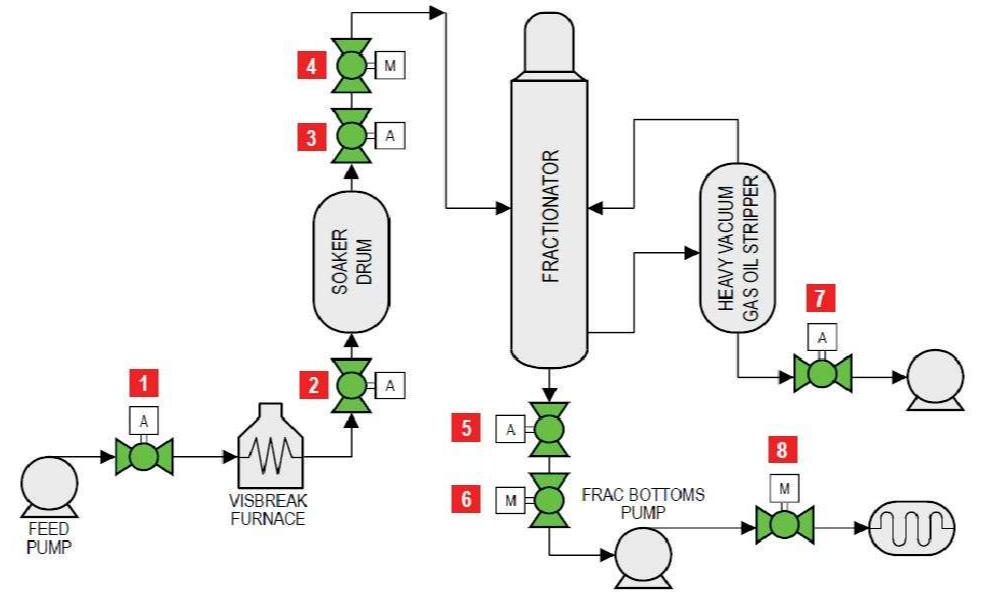
Visbreaking, or viscosity breaking, is a thermal cracking process designed to reduce the viscosity of heavy oil and residual feedstocks. It achieves this by breaking down large, complex hydrocarbon molecules into smaller, lighter fractions. The process operates at relatively moderate temperatures (450–500°C) and pressures, making it less severe compared to other upgrading methods. There are two primary types of visbreaking:
- Soaker Visbreaking: The heated feedstock is held in a reaction chamber (soaker drum) for a specific period to allow cracking to occur.
- Coil Visbreaking: The feedstock is rapidly heated in a furnace coil, and cracking takes place as it flows through the coil.
Visbreaking primarily produces lighter products such as naphtha and gas oil while reducing the yield of heavy residual fuel oil. It is a cost-effective and straightforward process, making it a popular choice for refineries looking to improve the handling and processing of heavy feedstocks without extensive residue conversion.
Coking
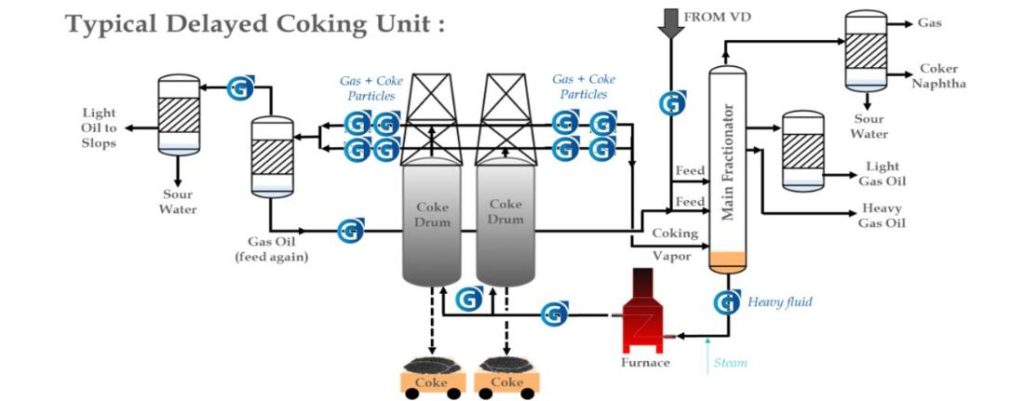
Coking is a thermal cracking process that is more intensive, designed to transform heavy oil residues into lighter, more valuable products along with solid coke. Operating at elevated temperatures (480–550°C), it leads to the complete thermal breakdown of heavy hydrocarbons. This method is especially suitable for treating heavy crude oils with high sulfur content and their residues.
There are three primary types of coking:
- Delayed Coking: The feedstock is first heated in a furnace before being sent to large coke drums, where it undergoes thermal cracking over several hours, ultimately forming solid coke.
- Fluid Coking: In this process, the feedstock is dispersed into a fluidized bed of hot coke particles, allowing for continuous cracking and coke generation.
- Flexicoking: A more advanced form of fluid coking, this process incorporates a gasifier that converts solid coke into syngas, enhancing flexibility and maximizing residue utilization.
Through coking, lighter hydrocarbon fractions such as gas oils and naphtha are obtained, alongside solid coke, which can serve as a fuel source or be utilized in industrial applications, including anode production for the aluminum industry. This process is particularly advantageous for refineries seeking to optimize residue conversion while reducing waste.
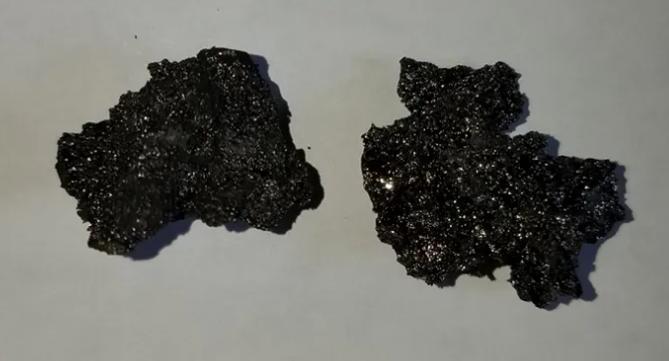
Differences Between Visbreaking and Coking for Heavy Oil Upgrading
Visbreaking and coking are both thermal processes employed to upgrade heavy oil; however, they differ considerably in process severity, outputs, and operational requirements. The following provides a detailed comparison of these two methods.
Aspect | Visbreaking | Coking |
Process Severity | Mild thermal cracking | Severe thermal cracking |
Pressure | Moderate pressures | Lower pressures |
Primary Outputs | Produces lighter fractions like naphtha and gas oil, with reduced viscosity | Produces lighter fractions (naphtha, gas oil) and solid coke |
Residue Conversion | Partially reduces residue, leaving some heavy fractions | Converts nearly all residue into lighter products and coke |
Energy Consumption | Lower energy requirements due to milder conditions | Higher energy consumption due to severe cracking conditions |
Operational Complexity | Simpler process with fewer operational challenges | More complex process, especially in handling coke and managing high temperatures |
Environmental Impact | Lower emissions and less environmental footprint | Higher emissions due to coke production and more intensive energy use |
Economic Considerations | Lower capital and operating costs | Higher capital and operating costs due to complex equipment and coke handling |
Feedstock Flexibility | Suitable for a wide range of heavy oils | Best suited for very heavy residues and high-sulfur crude oils |
Byproducts | Minimal byproducts, primarily lighter hydrocarbons | Generates solid coke as a significant byproduct |
This side-by-side comparison helps highlight the key differences between visbreaking and coking in terms of process, product outcomes, costs, and environmental considerations.
Industrial Applications of Visbreaking and Coking
Both visbreaking and coking play significant roles in refining heavy oils, but their industrial applications vary based on the type of crude being processed and the specific goals of the refinery. Each process serves a distinct function and is tailored to different feedstock types and desired product outcomes.
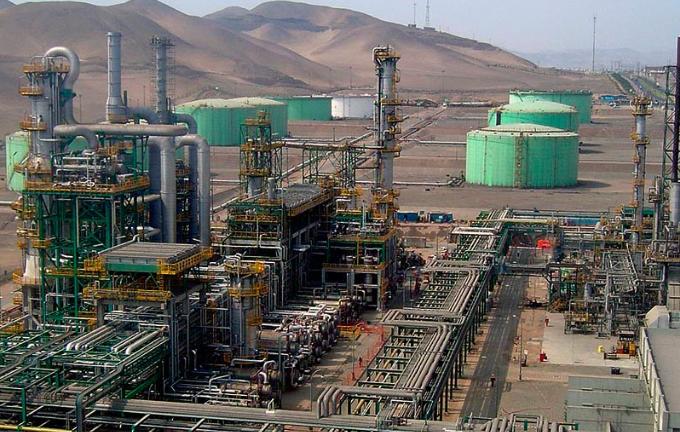
Visbreaking
Visbreaking is primarily employed in refineries handling heavy crude oils with moderate viscosity. This process is ideal for reducing viscosity in crude oils, making transportation and further refining more efficient. Refineries that manufacture industrial fuels, such as bunker fuels and fuel oils, frequently utilize visbreaking, as it produces suitable products for these applications. Additionally, it is implemented when refineries seek to enhance the quality of intermediate products without relying on more complex, energy-intensive methods. Refineries favor visbreaking as a cost-effective option for processing heavy oils without requiring substantial capital investment or operational complexity.
Coking
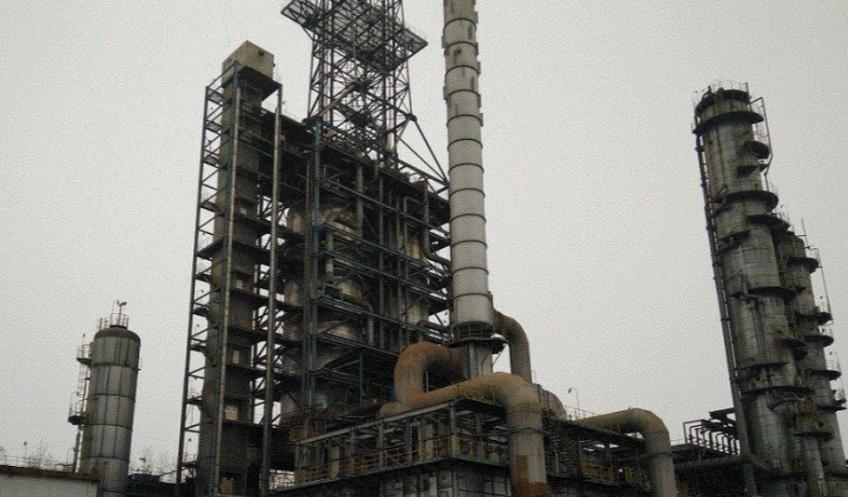
When refineries process extremely heavy crudes like bitumen or oil sands, they often rely on coking, as it facilitates the extensive upgrading required. Designed to accommodate high-viscosity feedstocks, coking units enhance the production of lighter and more valuable distillates, including gasoline, diesel, and jet fuel. Furthermore, the process generates solid coke, which serves as a fuel source, contributing to energy savings for refineries or other industrial uses. Particularly beneficial for refineries prioritizing the maximization of high-quality product output, coking is commonly integrated into facilities with complex configurations that incorporate both coking and hydroprocessing units. This method is well-suited for refineries processing extremely heavy crudes while efficiently managing the byproduct coke.
Overall, visbreaking and coking serve distinct but complementary roles in refining. While visbreaking offers a cost-effective way to reduce viscosity and improve fuel oil quality, coking provides a higher conversion rate and generates valuable light hydrocarbons at the expense of producing solid coke. The choice between these processes depends on refinery economics, feedstock availability, and market demands.
Summary
Visbreaking and coking are both essential in heavy oil upgrading, each serving distinct purposes and operating under different conditions. While visbreaking presents a straightforward and economical method to lower viscosity and yield lighter fractions, coking offers a more extensive solution for converting residues and generating coke. The selection of either process is influenced by factors like feedstock properties, refinery goals, and economic feasibility.