Waste Oil Distillation Machines: A Green Solution for a Growing Problem
Waste oil, a byproduct of various industrial and automotive processes, poses a significant environmental threat if not properly disposed of. It can contaminate water bodies, soil, and air, leading to severe ecological damage. Fortunately, waste oil distillation technology offers an effective and sustainable solution to this problem. By transforming waste oil into valuable products, this technology helps conserve natural resources and reduce pollution.
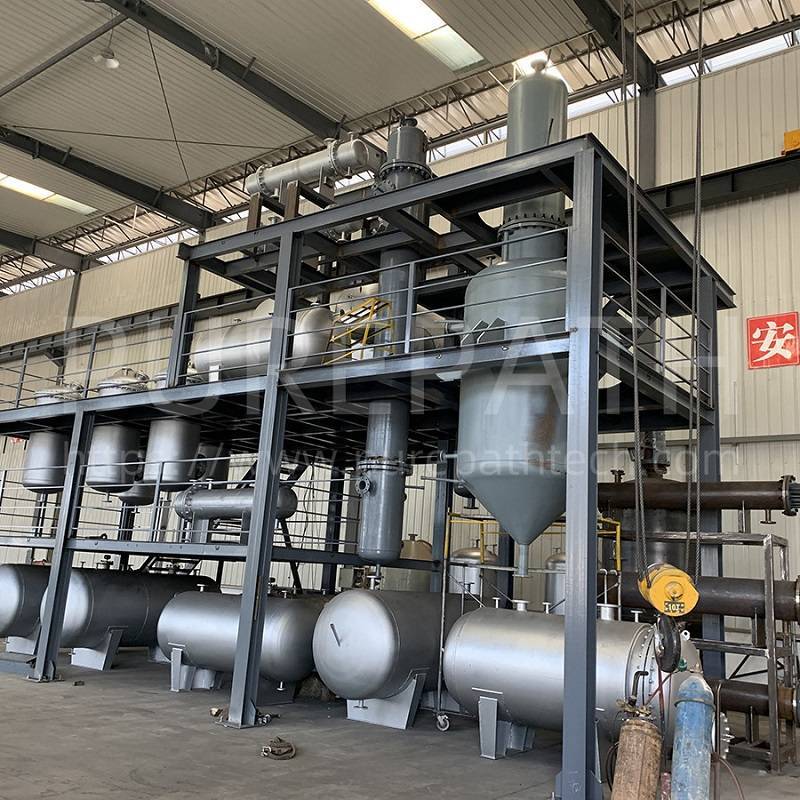
How Waste Oil Distillation Machine Works
Waste oil distillation is a complex process that involves several stages:
1. Preheating and Preparation
- Heat Transfer Oil Circulation: A heat transfer oil, typically a high-temperature resistant fluid, is circulated through a closed-loop system. This oil is heated to a high temperature, usually around 250°C, and then pumped into the distillation vessel.
- Vessel Preparation: The distillation vessel is a large, insulated tank designed to withstand high temperatures and pressures. Before the distillation process begins, the vessel is thoroughly cleaned and inspected to ensure optimal performance.
2. Distillation Process
- Heating and Vaporization: The heat transfer oil transfers its thermal energy to the waste oil, causing it to vaporize. As the temperature rises, different components of the waste oil vaporize at different rates.
- Separation: The vapors are then channeled into a condenser, where they are cooled and condensed back into liquid form. The condensed liquid is collected in separate tanks based on its boiling point range.
- Catalytic Cracking: In some cases, catalytic cracking may be employed to further refine the distillate. This process involves the use of catalysts to break down large hydrocarbon molecules into smaller, more valuable ones.
3. Purification
- Decolorization and Deodorization: The distillate is often dark in color and has an unpleasant odor. To improve its quality, it is subjected to a decolorization and deodorization process. This involves treating the distillate with adsorbents, such as clay or activated carbon, to remove impurities and improve its color and odor.
- Filtration: The purified distillate is then filtered to remove any remaining solid particles.
4. Residue Handling
- Residue Removal: The residue, or bottom product, is a heavy, viscous liquid that remains in the distillation vessel after the volatile components have been removed. This residue can be further processed or used as a fuel oil.
5. Emission Control
- Flue Gas Treatment: The flue gases generated during the distillation process are treated to remove pollutants, such as particulate matter, sulfur oxides, and nitrogen oxides. This is typically done using a combination of techniques, such as electrostatic precipitators, scrubbers, and catalytic converters.
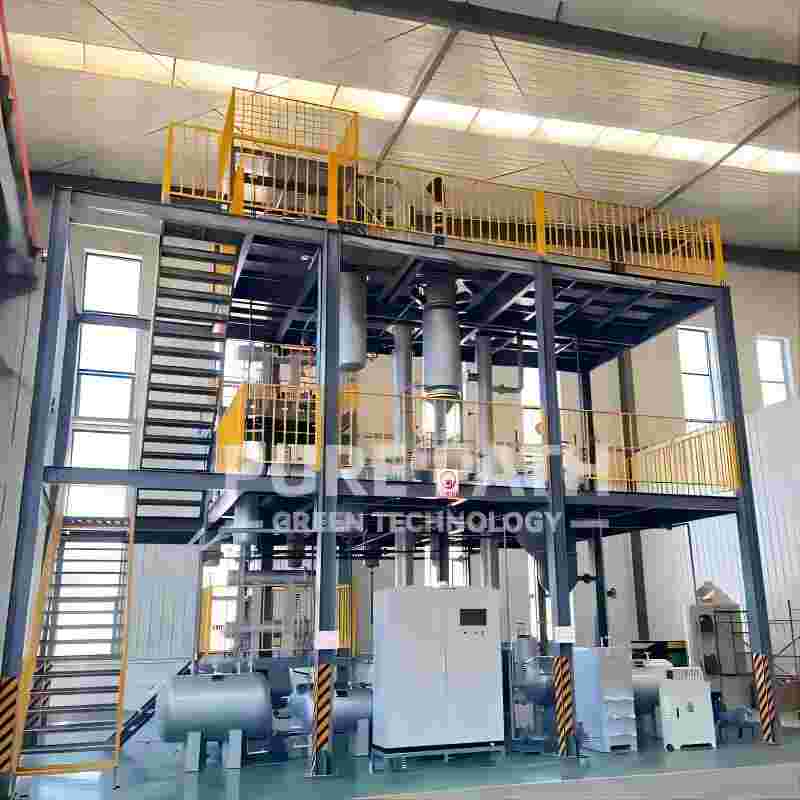
What Types of Waste Oil Can Be Processed by Waste Oil Distillation Machine?
Waste oil distillation machines are highly versatile and capable of processing various types of waste oils. The table below outlines common types of waste oils that can be processed, along with their characteristics and the specific treatments they require:
Waste Oil Type | Description | Common Contaminants | Treatment Required |
Used Engine Oil | Generated from vehicles and machinery, containing impurities like metal particles and additives. | Metal particles, degraded additives | Removal of metal particles and sludge; refining |
Lubricant Oil | Used in industrial and mechanical applications. | Sludge, dirt, and contaminants | Refining to remove sludge and contaminants |
Tire and Rubber Pyrolysis Oil | Extracted from the pyrolysis of waste tires and rubber, rich in hydrocarbons. | Heavy hydrocarbons | Cracking, temperature control, and purification |
Crude Oil and Sludge | Untreated crude oil and sludge from storage tanks or spills, often containing water and solids. | Water, solids, contaminants | Distillation, separation, and sludge removal |
Quenching and Heavy Oils | High-viscosity oils used in metal processing, often contaminated with nitrogen compounds. | Nitrogen compounds, heavy impurities | De-nitrogenation and de-sludging |
Diesel and Cutting Oils | Oils used in engines and metal cutting, requiring purification to remove impurities. | Odor, color, metal debris | Deodorization, decolorization, and filtration |
Comparison of Processing Different Waste Oils
The specific processing conditions and techniques used for different types of waste oil may vary. However, the general principles of distillation remain the same. Here’s a comparison of the key differences:
Waste Oil Type | Processing Method | Purpose and Techniques |
Engine and Lubricant Oils | Vacuum distillation | Prevents thermal degradation, minimizes cracking, separates lighter fractions efficiently. |
Pyrolysis Oils | Controlled temperature and time distillation, gas capture | Optimizes cracking efficiency, preserves product quality, and recycles gases (methane, hydrogen) as fuel. |
Crude Oil and Sludge | Conventional distillation for crude oil; thermal treatment followed by condensation for sludge | Separates fractions like gasoline, diesel, and lubricants; repurposes residual solids for fuel or construction material. |
Quenching and Heavy Oils | De-nitrogenation using chemical reagents like aluminum chloride | Removes nitrogen compounds and sludge, improves fuel quality. |
Diesel and Cutting Oils | Decolorization, deodorization, and filtration | Removes color, odor, and metallic impurities to restore oil usability. |
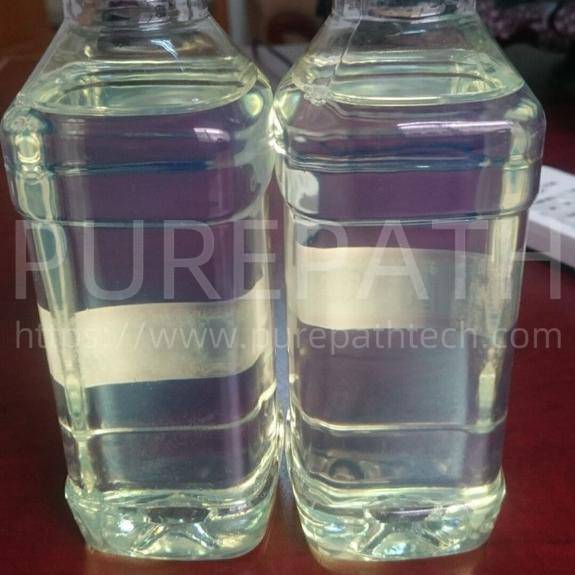
End Products and Applications of Waste Oil Distillation
The end products of waste oil distillation vary depending on the type of waste oil processed. Below is a table that outlines the typical products generated by different waste oils and their respective applications:
Waste Oil Type | End Products | Applications |
Engine and Lubricant Oils | Base oils, diesel, gasoline | Used in transportation, machinery, and manufacturing. |
Pyrolysis Oils | Fuel oil, carbon black, non-condensable gases | Used in power generation, as industrial fuel, and for material recovery. |
Crude Oil and Sludge | Refined petroleum products, residual solids | Used in construction materials, power generation, and as fuel. |
Quenching and Heavy Oils | Nitrogen-free fuel oils | Applied in energy generation and industrial heating. |
Diesel and Cutting Oils | Recycled diesel, high-quality lubricants | Utilized in automotive and industrial applications. |
Environmental Impact and Regulations of Waste Oil Distillation
Waste oil distillation offers numerous environmental benefits, including:
- Reduced Pollution: By recycling waste oil, we can prevent it from being dumped into landfills or water bodies, thereby reducing pollution and protecting the environment.
- Conservation of Natural Resources: Recycling waste oil reduces the demand for crude oil, a non-renewable resource.
- Energy Recovery: The recovered products from waste oil distillation can be used as fuels, reducing reliance on fossil fuels.
To ensure that waste oil distillation facilities operate in an environmentally responsible manner, strict regulations are in place. These regulations govern various aspects of the process, including:
- Emission Standards: Facilities must comply with air quality standards to minimize emissions of pollutants.
- Wastewater Treatment: Wastewater generated during the process must be treated to meet water quality standards.
- Waste Disposal: Solid waste and hazardous materials generated must be disposed of properly.
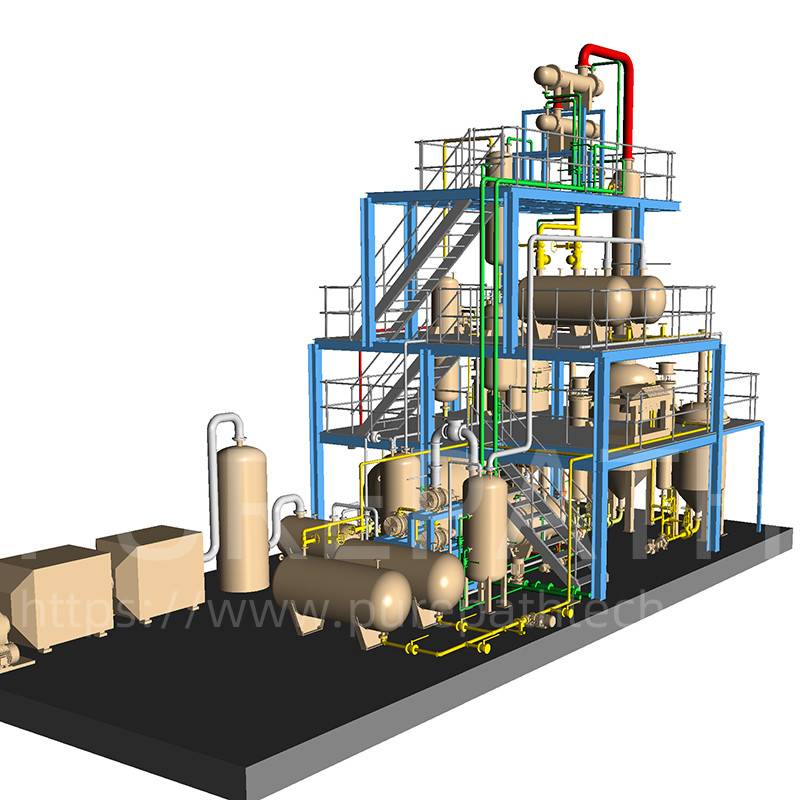
Waste oil distillation is a vital technology that plays a crucial role in promoting sustainable waste management. By transforming waste oil into valuable products, this technology helps to conserve natural resources, reduce pollution, and create a cleaner and healthier planet. As the demand for sustainable solutions continues to grow, waste oil distillation is poised to become an even more important part of the circular economy.