Waste Oil to Diesel Machines vs. Traditional Oil Refining
As the global demand for sustainable energy sources continues to grow, various technologies have emerged to recycle waste materials into usable fuel. Among these innovations is the waste oil to diesel technology, a process that converts used oil into biodiesel.
What is Waste Oil to Diesel Technology?
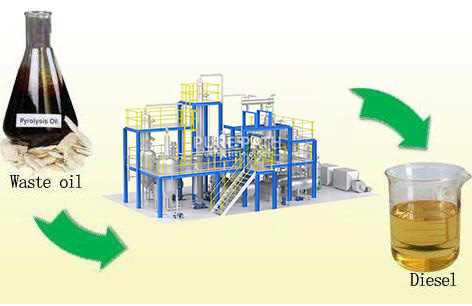
Waste oil to diesel technology refers to a set of innovative processes and machinery designed to convert various types of waste oils—such as used motor oil, cooking oil, and industrial lubricants—into diesel fuel. This technology focuses on recycling waste materials that would otherwise contribute to environmental pollution. The process generally involves several key steps:
- Collection and Pre-treatment: Waste oils are collected from diverse sources, including automotive workshops, restaurants, and manufacturing facilities. Before conversion, the oils undergo pre-treatment, which includes filtering out impurities like water, dirt, and food residues to ensure a clean feedstock.
- Transesterification: This is the core chemical process that transforms the waste oil into biodiesel. During transesterification, the waste oil is combined with an alcohol (commonly methanol) and a catalyst (usually sodium hydroxide or potassium hydroxide). This reaction yields biodiesel (fatty acid methyl esters) and glycerol, separating them into distinct products.
- Separation and Purification: After transesterification, the biodiesel and glycerol are separated. The biodiesel undergoes further purification processes, which may include washing, drying, and filtration, to eliminate any remaining contaminants and meet fuel quality standards.
- Storage and Distribution: Once purified, the biodiesel is stored and can be distributed for various applications, including use in diesel engines or blending with conventional diesel fuel.
This technology not only provides a renewable source of energy but also plays a significant role in reducing environmental waste by repurposing used oils, contributing to a more sustainable energy landscape.
What is the Traditional Oil Refining Process
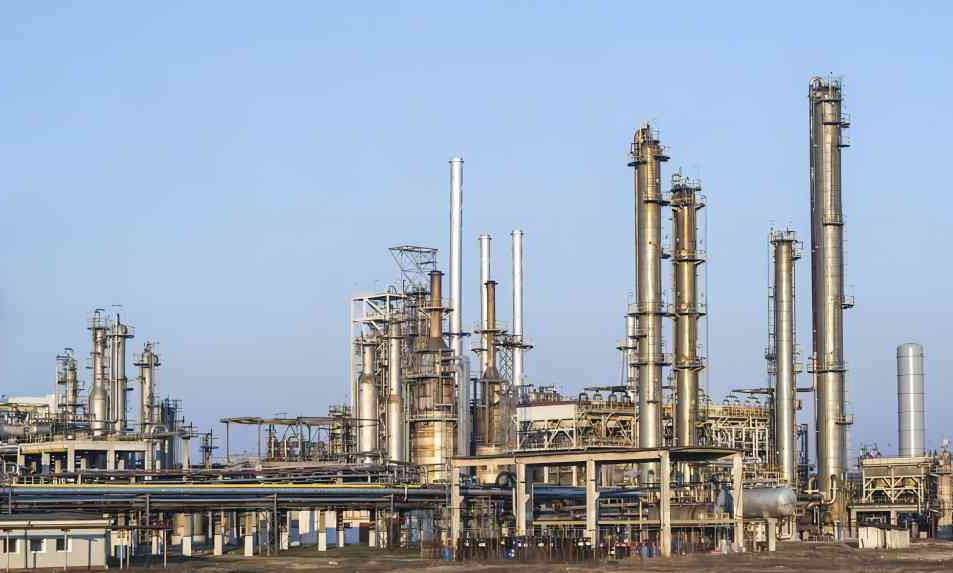
Traditional oil refining is a complex industrial process that transforms crude oil into various useful petroleum products, such as gasoline, diesel, jet fuel, and lubricants. The refining process typically consists of several stages:
- Crude Oil Extraction: The process begins with the extraction of crude oil from underground reservoirs through drilling. This raw material, often found in large quantities, is then transported to refineries for processing.
- Fractional Distillation: Once at the refinery, crude oil undergoes fractional distillation. The crude oil is heated in a large distillation column, where it separates into different hydrocarbon fractions based on their boiling points. Lighter hydrocarbons vaporize at lower temperatures and rise to the top of the column, while heavier fractions remain at the bottom.
- Conversion Processes: The separated fractions may undergo conversion processes to optimize the yield of desirable products. Techniques such as catalytic cracking, hydrocracking, and thermal cracking break down larger, heavier molecules into lighter, more valuable products, such as gasoline and diesel.
- Treatment and Refinement: After conversion, the products undergo treatment to remove impurities, such as sulfur and nitrogen compounds. This is achieved through processes like hydrotreating and desulfurization. The treated products are then blended to meet specific market specifications and performance requirements.
- Storage and Distribution: Finally, the refined petroleum products are stored in large tanks before being distributed to various markets, including gas stations and industrial users. This distribution network ensures that refined fuels reach consumers efficiently.
Traditional oil refining has been a cornerstone of the energy industry for over a century, providing essential fuels for transportation and industry. However, it is a resource-intensive process that has significant environmental impacts, including greenhouse gas emissions and the production of waste byproducts.
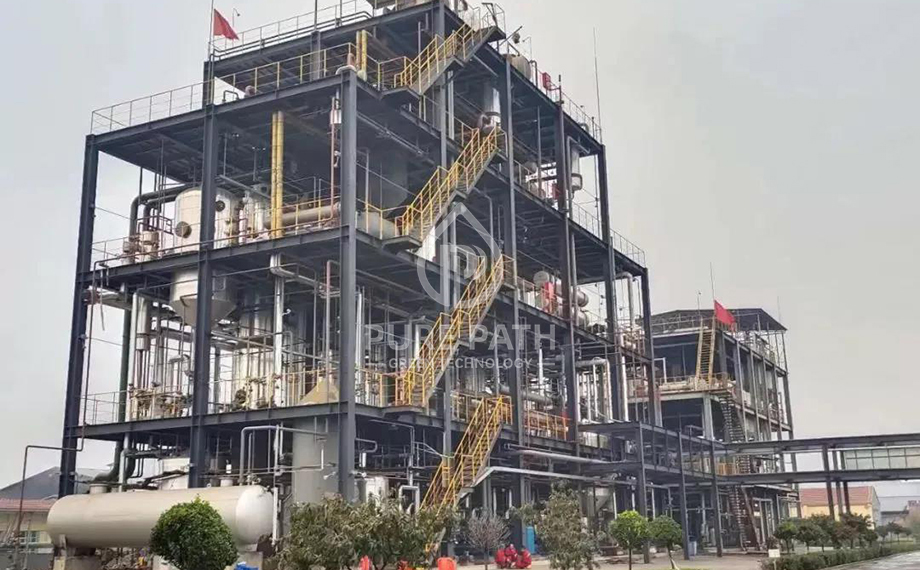
Waste Oil to Diesel Machines vs. Traditional Oil Refining
Environmental Impact
- Waste Oil to Diesel Machines: These machines are an environmentally friendly solution, as they focus on recycling waste oils that would otherwise be disposed of improperly. By converting used oil into diesel fuel, they help reduce pollution and lower the volume of hazardous waste entering landfills or water systems. This process significantly cuts down on greenhouse gas emissions when compared to extracting and refining crude oil.
- Traditional Oil Refining: Refining crude oil has a much larger environmental footprint. The process involves extracting crude oil from the earth, which can lead to spills, habitat destruction, and significant air pollution. In addition, traditional oil refining consumes vast amounts of energy and generates harmful byproducts, contributing to global warming and environmental degradation.
Economic Factors
- Waste Oil to Diesel Machines: The cost of implementing waste oil to diesel machines is often lower, particularly for small or medium-scale operations that produce or have access to waste oil. The process also offers a cost-effective way to turn what would be a waste product into a valuable fuel. Businesses that generate waste oil—such as automotive, industrial, or food production companies—can save on waste disposal fees while producing usable diesel for their own operations or for sale.
- Traditional Oil Refining: The traditional oil refining industry requires immense capital investment to build refineries, pipelines, and storage facilities. While it does produce a wide array of petroleum products, the process is sensitive to crude oil price fluctuations and geopolitical factors. Refining large amounts of crude oil comes with high operational and maintenance costs, making it a less flexible option for smaller-scale ventures.
Energy Consumption and Efficiency
- Waste Oil to Diesel Machines: Converting waste oil into diesel is generally more energy-efficient because it repurposes an existing resource—used oil. These machines consume less energy in the conversion process compared to the extraction and refining of crude oil, making them a cost-effective solution. Companies that adopt this technology can reduce energy consumption and operating expenses while still producing fuel.
- Traditional Oil Refining: Refining crude oil is an energy-intensive process, involving the extraction, heating, distillation, and cracking of crude oil to produce usable fuels. These stages demand significant energy, leading to higher operational costs and a larger carbon footprint. As a result, traditional refining is less sustainable in the long run.
Scalability and Flexibility
- Waste Oil to Diesel Machines: One major advantage of waste oil to diesel technology is its scalability. These machines are available in various sizes, making them suitable for both small- and large-scale operations. They can be deployed in decentralized locations, enabling localized fuel production without the need for extensive infrastructure. This flexibility allows municipalities, businesses, or even individual operators to customize the technology according to their specific needs.
- Traditional Oil Refining: In contrast, traditional oil refineries are large industrial complexes requiring substantial infrastructure and are typically situated in specific regions due to zoning regulations, proximity to crude oil sources, and logistical considerations. Scaling down traditional refining processes is challenging, and refineries cannot be easily relocated or adjusted to serve small-scale or local needs. This rigidity makes them less adaptable than the more flexible waste oil to diesel systems.
In summary, while both waste oil to diesel machines and traditional oil refining serve important roles in the energy sector, they differ significantly in terms of environmental impact, economic viability, energy efficiency, and scalability. Waste oil to diesel technology emerges as a more sustainable and adaptable solution, especially in the context of growing environmental concerns and the need for renewable energy sources.
Want to Find Reliable Waste Oil to Diesel Machines?
If you’re in the market for a dependable waste oil to diesel machine, choosing the right manufacturer is crucial for ensuring efficiency, sustainability, and long-term success. One company that stands out in this field is PurePath, a leading manufacturer known for its high-quality waste oil to diesel conversion systems.
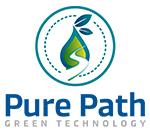
- PurePath specializes in advanced waste oil to diesel technology, offering innovative machines that convert waste oils into high-grade diesel fuel.
- With a reputation for delivering environmentally friendly and cost-effective solutions, PurePath provides systems that are easy to operate, energy-efficient, and designed to meet strict environmental standards.
- Whether you’re a small business or a large-scale operation, PurePath’s equipment is scalable to meet various production needs.
- Our machines ensure high fuel yield with minimal waste, making them a top choice for businesses looking to reduce their carbon footprint and recycle waste oils efficiently.