What Are the Process of Crude Oil Distillation?
Crude oil distillation is an integral step in refining petroleum into consumable products like gasoline, diesel, and jet fuel. This essential step transforms raw crude oil into valuable fuels and chemicals that can benefit society at large.
Why Distill Crude Oil?
Crude oil in its raw state is an inconvenient mix of hydrocarbons, impurities, and molecular weight variations that is inaccessible for direct use. Distillation is the cornerstone of refining as it segregates crude oil by boiling point into distinct components that can then be refined further into fuels and petrochemical products that power industries, transportation networks, and everyday life.
Without distillation, crude oil would remain a raw resource with limited applications. By refining, each hydrocarbon fraction is efficiently extracted to maximize utility while decreasing waste production.
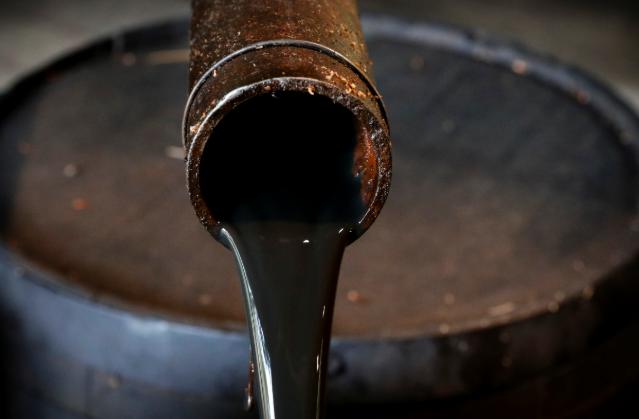
Benefits of Crude Oil Distillation
- Distillation Produces Essential Fuels – Distillation processes produce gasoline, diesel, kerosene, and jet fuel used to power vehicles, aircraft, and machinery worldwide.
- Petrochemical Production Made Possible – Separated fractions provide raw materials for plastics, synthetic rubber, solvents, and other industrial chemicals that enable production.
- Strengthen Refinery Efficiency – By breaking crude oil down into its various constituent parts, refineries can optimize processing and reduce energy waste.
- Reduces Environmental Waste – Most components of crude oil are utilized, from light gases to heavy residues such as asphalt, to ensure minimal waste.
- Distillation Provides Solutions to Multiple Industries – Distillation can support many different industries by producing fuels for transportation as well as lubricants for machinery, waxes for manufacturing processes, and feedstocks for pharmaceutical production.
Distillation is at the core of modern fuel production, allowing industries to meet energy demands efficiently while meeting global energy requirements.
Main Process of Crude Oil Distillation
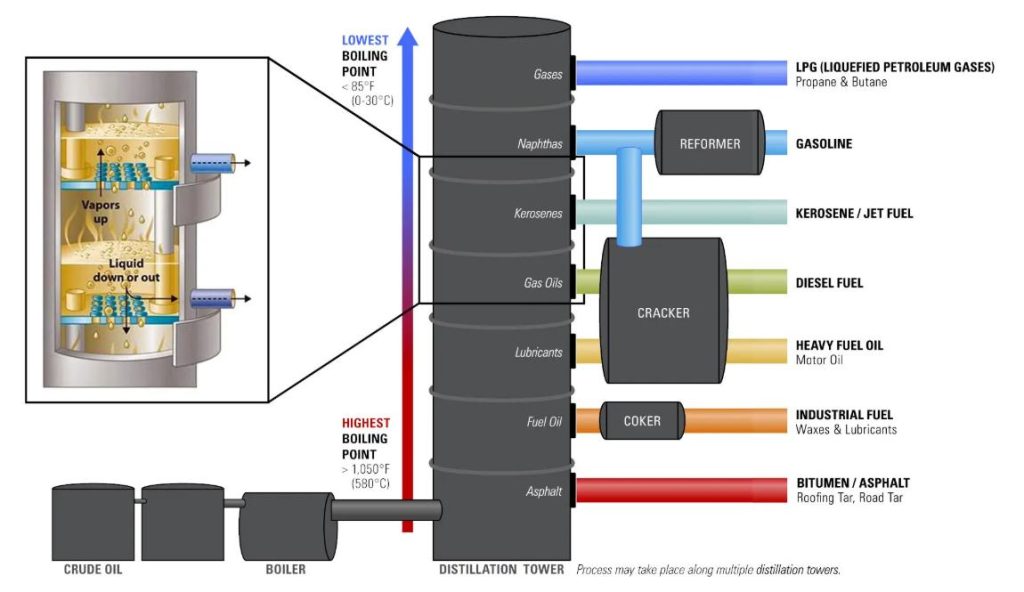
Crude oil distillation is a multi-stage separation process that divides petroleum into usable fractions based on boiling points. Below is a step-by-step explanation of the key stages:
Pre-Heating and Desalting
Before it can be refined into refined oil, crude oil must first undergo pre-treatment to eliminate impurities:
- Desalting: Water can help remove salts, sand, and other contaminants to protect the distillation unit against corrosion and fouling.
- Pre-Heating: For optimal flow and to maximize further heating, crude is initially heated between 110°C-150°C. This step improves flow while simultaneously prepping it for further processing.
Heating in a Furnace
Crude oil is fed into a furnace and heated to 350°C-400°C to transform it into a vapor-gas mixture. At such temperatures, most hydrocarbons vaporize prior to entering the distillation column for distillation.
Separation in the Fractionating Column
Heat-treated crude enters a tall distillation column (fractionating tower), where separation takes place in stages:
- Trays or Packing Material: Each column in the process consists of multiple trays or structured packing material to help separate components as vapors rise and condense, helping keep components separated as they rise to the top and condense back down to earth.
- Temperature Gradient: The column begins with temperatures at the bottom (350 °C) and gradually cools as you progress up it (20°C-100°C).
Fraction Collection at Different Levels:
Fraction | Boiling Range | Collection Point | Uses |
LPG & Light Naphtha | < 40°C | Top of Column | Bottled gas, gasoline blending |
Gasoline | 40°C–180°C | Upper Trays | Motor fuel, petrochemicals |
Kerosene / Jet Fuel | 180°C–250°C | Middle Section | Aviation fuel, lighting |
Diesel | 250°C–350°C | Lower Middle Section | Truck fuel, heating oil |
Lubricants & Waxes | 350°C–500°C | Near Bottom | Machinery oils, candles |
Residue (Bitumen) | > 500°C | Bottom of Column | Road asphalt, heavy fuel oil |
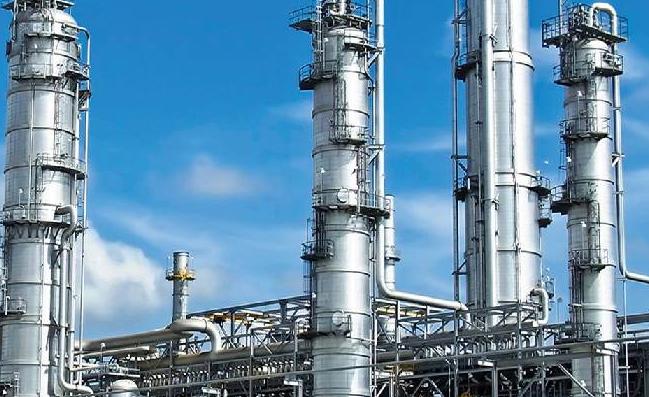
Condensation and Collection
As vapors rise, they cool and condense at different heights based on their boiling points.
Liquid fractions are drawn off through side outlets, while gases (like methane and propane) exit the top.
Reflux systems recycle some condensed liquid back into the column to improve separation efficiency.
Further Processing (Optional)
Some fractions undergo secondary refining for better quality:
Vacuum Distillation: Heavy residues are further separated under reduced pressure.
Cracking & Reforming: Converts heavier fractions into lighter, more valuable products like gasoline.
Cooling and Storage
Distilled products are stored before being transported for further refining or commercial use.
Why Use a Crude Oil Distillation Plant?
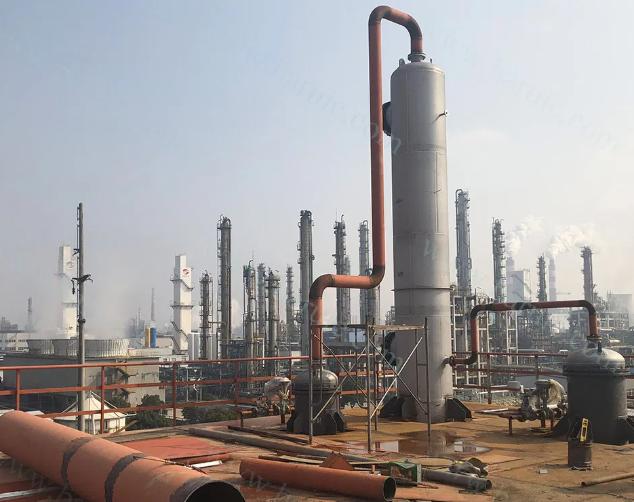
Crude oil distillation plants are essential for transforming raw petroleum into valuable fuels and petrochemical products. Here are the four key reasons why these plants are indispensable in the refining industry:
1. High Efficiency in Separation
Crude oil distillation plants are designed to ensure precision in hydrocarbon separation. Utilizing fractional distillation columns, these facilities efficiently separate crude oil into gasoline, diesel, kerosene, and lubricants according to their boiling points. Temperature and pressure controls help minimize energy waste while optimizing yields; without such facilities, refining crude oil would be far less effective, leading to increased costs and inferior product quality.
2. Producing Consistent, High-Quality Fuel
Quality control in fuel production is of the utmost importance, and distillation plants ensure consistent purity and performance of their refined products. Automated monitoring systems continuously adjust temperatures and pressures in real time to prevent contamination between fractions. Such precision is especially essential for meeting industry standards when producing gasoline or jet fuel, where impurities could damage engines or cause safety risks.
3. Scalability for Industrial Production
Distillation plants provide large refineries with an efficient solution for handling various volumes of crude oil per day, making them the ideal solution to meet growing fuel demands. Their modular design also makes for seamless expansion if more production capacity is necessary to keep pace with rising demands for fuel. Regardless of size or scope, distillation plants offer flexible infrastructure capable of efficiently processing vast volumes.
4. Environmental and Regulatory Compliance
Modern distillation plants utilize advanced emission control systems to minimize environmental impact. By streamlining their refining process, these facilities reduce waste, greenhouse gas emissions, and recover valuable byproducts like sulfur that would otherwise pollute the environment, as well as abide by stringent safety and environmental regulations that ensure legally compliant operations.
Wrapping Up
Crude oil distillation is the backbone of petroleum refining, enabling the production of essential fuels and chemicals. By understanding the distillation process, industries can optimize efficiency and reduce waste, making it a critical step in energy production.
Investing in a modern distillation plant ensures better fuel quality, higher yields, and sustainable refining practices.